Information injection-pump assembly
BOSCH
9 400 615 047
9400615047
ZEXEL
101603-2324
1016032324
HINO
220204722B
220204722b
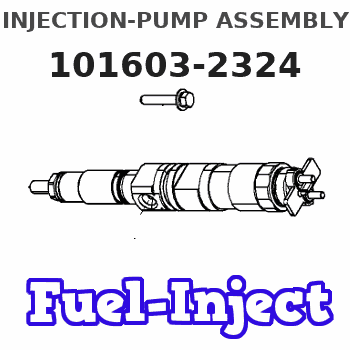
Rating:
Include in #1:
101603-7542
as _
Cross reference number
BOSCH
9 400 615 047
9400615047
ZEXEL
101603-2324
1016032324
HINO
220204722B
220204722b
Zexel num
Bosch num
Firm num
Name
101603-2324
9 400 615 047
220204722B HINO
INJECTION-PUMP ASSEMBLY
H07C-TD K 14BF INJECTION PUMP ASSY PE6AD PE
H07C-TD K 14BF INJECTION PUMP ASSY PE6AD PE
Calibration Data:
Adjustment conditions
Test oil
1404 Test oil ISO4113 or {SAEJ967d}
1404 Test oil ISO4113 or {SAEJ967d}
Test oil temperature
degC
40
40
45
Nozzle and nozzle holder
105780-8140
Bosch type code
EF8511/9A
Nozzle
105780-0000
Bosch type code
DN12SD12T
Nozzle holder
105780-2080
Bosch type code
EF8511/9
Opening pressure
MPa
17.2
Opening pressure
kgf/cm2
175
Injection pipe
Outer diameter - inner diameter - length (mm) mm 6-2-600
Outer diameter - inner diameter - length (mm) mm 6-2-600
Overflow valve
134424-0920
Overflow valve opening pressure
kPa
162
147
177
Overflow valve opening pressure
kgf/cm2
1.65
1.5
1.8
Tester oil delivery pressure
kPa
157
157
157
Tester oil delivery pressure
kgf/cm2
1.6
1.6
1.6
Direction of rotation (viewed from drive side)
Right R
Right R
Injection timing adjustment
Direction of rotation (viewed from drive side)
Right R
Right R
Injection order
1-4-2-6-
3-5
Pre-stroke
mm
4.8
4.77
4.83
Beginning of injection position
Drive side NO.1
Drive side NO.1
Difference between angles 1
Cal 1-4 deg. 60 59.75 60.25
Cal 1-4 deg. 60 59.75 60.25
Difference between angles 2
Cyl.1-2 deg. 120 119.75 120.25
Cyl.1-2 deg. 120 119.75 120.25
Difference between angles 3
Cal 1-6 deg. 180 179.75 180.25
Cal 1-6 deg. 180 179.75 180.25
Difference between angles 4
Cal 1-3 deg. 240 239.75 240.25
Cal 1-3 deg. 240 239.75 240.25
Difference between angles 5
Cal 1-5 deg. 300 299.75 300.25
Cal 1-5 deg. 300 299.75 300.25
Injection quantity adjustment
Adjusting point
A
Rack position
10
Pump speed
r/min
1050
1050
1050
Average injection quantity
mm3/st.
114.5
113
116
Max. variation between cylinders
%
0
-3.5
3.5
Basic
*
Fixing the lever
*
Boost pressure
kPa
28.7
28.7
Boost pressure
mmHg
215
215
Injection quantity adjustment_02
Adjusting point
C
Rack position
6.4+-0.5
Pump speed
r/min
410
410
410
Average injection quantity
mm3/st.
9
8
10
Max. variation between cylinders
%
0
-10
10
Fixing the rack
*
Boost pressure
kPa
0
0
0
Boost pressure
mmHg
0
0
0
Injection quantity adjustment_03
Adjusting point
D
Rack position
-
Pump speed
r/min
100
100
100
Average injection quantity
mm3/st.
135
135
145
Fixing the lever
*
Boost pressure
kPa
0
0
0
Boost pressure
mmHg
0
0
0
Rack limit
*
Boost compensator adjustment
Pump speed
r/min
800
800
800
Rack position
R1-0.85
Boost pressure
kPa
9.3
8
10.6
Boost pressure
mmHg
70
60
80
Boost compensator adjustment_02
Pump speed
r/min
800
800
800
Rack position
R1(10)
Boost pressure
kPa
18
14
22
Boost pressure
mmHg
135
105
165
Timer adjustment
Pump speed
r/min
900--
Advance angle
deg.
0
0
0
Remarks
Start
Start
Timer adjustment_02
Pump speed
r/min
850
Advance angle
deg.
0.3
Timer adjustment_03
Pump speed
r/min
1050
Advance angle
deg.
1.5
1.2
1.8
Remarks
Finish
Finish
Test data Ex:
Governor adjustment
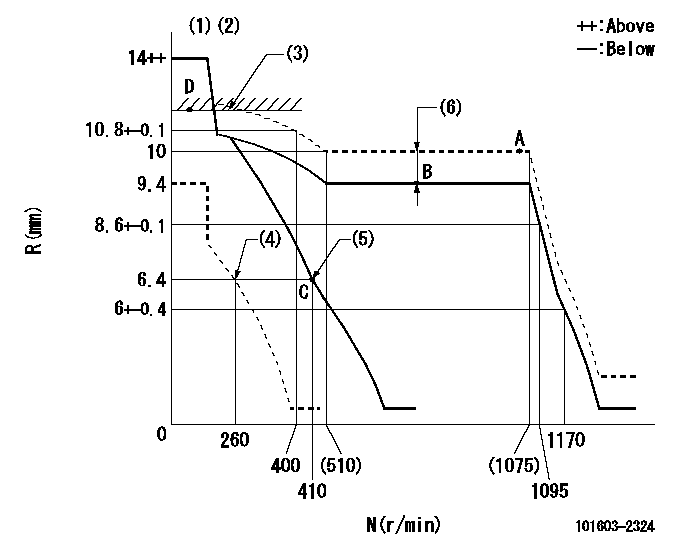
N:Pump speed
R:Rack position (mm)
(1)Target notch: K
(2)Tolerance for racks not indicated: +-0.05mm.
(3)RACK LIMIT
(4)Set idle sub-spring
(5)Main spring setting
(6)Boost compensator stroke: BCL
----------
K=13 BCL=0.85+-0.1mm
----------
----------
K=13 BCL=0.85+-0.1mm
----------
Speed control lever angle
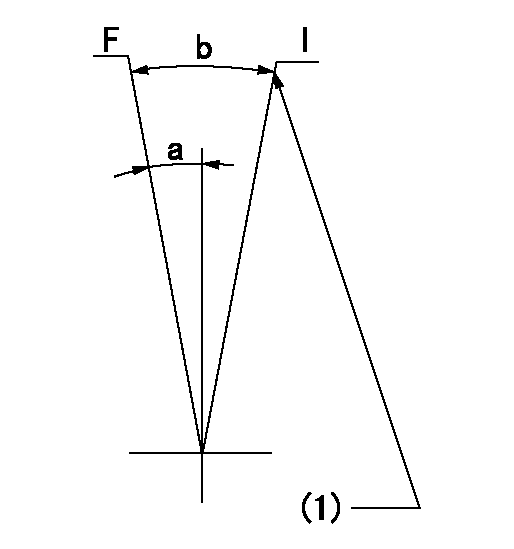
F:Full speed
I:Idle
(1)Stopper bolt setting
----------
----------
a=(6deg)+-5deg b=(20deg)+-5deg
----------
----------
a=(6deg)+-5deg b=(20deg)+-5deg
Stop lever angle

N:Pump normal
S:Stop the pump.
(1)Pump speed aa and rack position bb (to be sealed at delivery)
(2)Normal
----------
aa=0r/min bb=1-0.5mm
----------
a=21deg+-5deg b=(55deg)
----------
aa=0r/min bb=1-0.5mm
----------
a=21deg+-5deg b=(55deg)
Timing setting
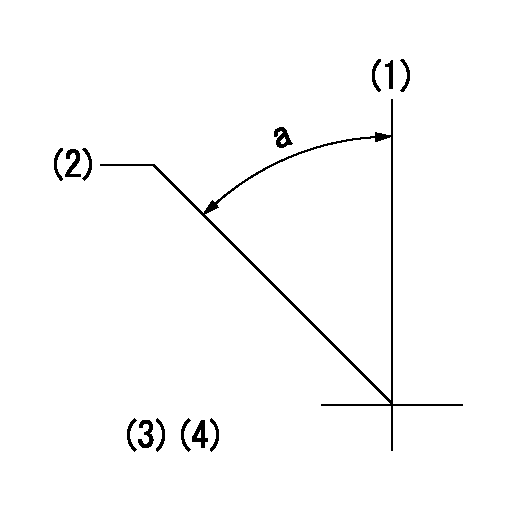
(1)Pump vertical direction
(2)Coupling's key groove position at No 1 cylinder's beginning of injection
(3)-
(4)-
----------
----------
a=(50deg)
----------
----------
a=(50deg)
Information:
If the crankshaft is not in the correct position when the magnetic pickup sensor is installed, the magnetic probe will be damaged when the engine is started.
F. Put a 2D6392 O-Ring Seal on the end of the Magnetic Pick-up Sensor (a small amount of clean engine oil will let the seal slide onto the sensor more easily).G. Push the sensor through the adapter until it comes in contact with the counterweight and move the O-Ring Seal down against the adapter.H. Withdraw the sensor 1 mm (.04 in.) and hand tighten the nut on the adapter sleeve to firmly hold the timing probe in position.I. Connect cable for magnetic pick-up to the magnetic pick-up sensor. Step 2. Install ECAP And Injector HarnessA. Connect an ECAP to the Engine Data Link Connector (J8).B. Install the Injection "T" Harness on the Fuel Injector Connector (J5/P5) in the valve cover base.C. Be certain all connections (probe, harness, ECAP) are made correctly. Use special care when connecting "T" Harness to J5. The plug can be mis-aligned. Also use care when reconnecting J5 and P5. Incorrect installation will result in a "No Start" condition. Step 3. Calibrate Speed/Timing SensorA. Start the engine and run at low idle until the engine has warmed up enough to change out of Cold Mode operation. The "Diagnostic Lamp" should go out after the engine has started and the 10 second lamp test is complete. The engine rpm will decrease from approximately 1000 rpm while in the cold mode to the programmed low idle rpm when out of Cold Mode.B. Check for ACTIVE Diagnostic Codes. Use the procedures in this manual to troubleshoot and repair any ACTIVE Diagnostic Codes before attempting a calibration check.C. After engine has shifted out of Cold Mode, select the 3176 Timing Calibrate Screen on the ECAP. To insure the most accurate timing calibration, the engine rpm should be held as steady as possible at approximately 1500 rpm. This can be performed using the hand throttle. Any major changes (greater than 100 rpm) will slow down the procedure and make it less accurate.D. Press on the "space" key on the ECAP and wait until the ECAP indicates timing is CALIBRATED (approximately 15 seconds).E. Verify that timing has been calibrated by observing the "Desired Timing" bar display on the ECAP. Run the engine at different rpm's, allowing a few seconds at each setting for the rpm to stabilize. * If the ECAP display reads that injection timing is CALIBRATED, but during verification, the actual timing bar display is not within the two vertical timing tolerance lines and/or the display is erratic, repeat the timing calibration procedure.* If the ECAP display reads UNABLE TO CALIBRATE TIMING, the electronic injection timing has NOT been set. OK: Timing is functional and calibrated if the right end of the bar graph display stays within the vertical bars at all steady speeds. NOT OK: Recheck the tool installation and tool operation. Verify that the engine speeds were kept stable ( 50
Have questions with 101603-2324?
Group cross 101603-2324 ZEXEL
Hino
Hino
101603-2324
9 400 615 047
220204722B
INJECTION-PUMP ASSEMBLY
H07C-TD
H07C-TD