Information injection-pump assembly
ZEXEL
101603-2300
1016032300
HINO
220009240A
220009240a
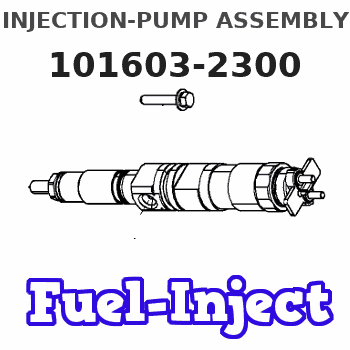
Rating:
Service parts 101603-2300 INJECTION-PUMP ASSEMBLY:
1.
_
7.
COUPLING PLATE
8.
_
9.
_
11.
Nozzle and Holder
23600-2663C
12.
Open Pre:MPa(Kqf/cm2)
16.7{170}/21.6{220}
14.
NOZZLE
Cross reference number
ZEXEL
101603-2300
1016032300
HINO
220009240A
220009240a
Zexel num
Bosch num
Firm num
Name
Calibration Data:
Adjustment conditions
Test oil
1404 Test oil ISO4113 or {SAEJ967d}
1404 Test oil ISO4113 or {SAEJ967d}
Test oil temperature
degC
40
40
45
Nozzle and nozzle holder
105780-8250
Bosch type code
1 688 901 101
Nozzle
105780-0120
Bosch type code
1 688 901 990
Nozzle holder
105780-2190
Opening pressure
MPa
20.7
Opening pressure
kgf/cm2
211
Injection pipe
Outer diameter - inner diameter - length (mm) mm 6-2-600
Outer diameter - inner diameter - length (mm) mm 6-2-600
Overflow valve
131425-0620
Overflow valve opening pressure
kPa
255
221
289
Overflow valve opening pressure
kgf/cm2
2.6
2.25
2.95
Tester oil delivery pressure
kPa
255
255
255
Tester oil delivery pressure
kgf/cm2
2.6
2.6
2.6
Direction of rotation (viewed from drive side)
Left L
Left L
Injection timing adjustment
Direction of rotation (viewed from drive side)
Left L
Left L
Injection order
1-4-2-6-
3-5
Pre-stroke
mm
3.8
3.77
3.83
Beginning of injection position
Governor side NO.1
Governor side NO.1
Difference between angles 1
Cal 1-4 deg. 60 59.75 60.25
Cal 1-4 deg. 60 59.75 60.25
Difference between angles 2
Cyl.1-2 deg. 120 119.75 120.25
Cyl.1-2 deg. 120 119.75 120.25
Difference between angles 3
Cal 1-6 deg. 180 179.75 180.25
Cal 1-6 deg. 180 179.75 180.25
Difference between angles 4
Cal 1-3 deg. 240 239.75 240.25
Cal 1-3 deg. 240 239.75 240.25
Difference between angles 5
Cal 1-5 deg. 300 299.75 300.25
Cal 1-5 deg. 300 299.75 300.25
Injection quantity adjustment
Adjusting point
-
Rack position
12.4
Pump speed
r/min
850
850
850
Average injection quantity
mm3/st.
104.5
102.5
106.5
Max. variation between cylinders
%
0
-3.5
3.5
Basic
*
Fixing the rack
*
Standard for adjustment of the maximum variation between cylinders
*
Injection quantity adjustment_02
Adjusting point
Z
Rack position
9.5+-0.5
Pump speed
r/min
375
375
375
Each cylinder's injection qty
mm3/st.
13
12
14
Fixing the rack
*
Standard for adjustment of the maximum variation between cylinders
*
Injection quantity adjustment_03
Adjusting point
A
Rack position
R1(12.4)
Pump speed
r/min
850
850
850
Average injection quantity
mm3/st.
104.5
103.5
105.5
Basic
*
Fixing the lever
*
Injection quantity adjustment_04
Adjusting point
B
Rack position
R1+0.9
Pump speed
r/min
1450
1450
1450
Average injection quantity
mm3/st.
109.5
105.5
113.5
Fixing the lever
*
Injection quantity adjustment_05
Adjusting point
C
Rack position
R1+0.55
Pump speed
r/min
1160
1160
1160
Average injection quantity
mm3/st.
109
105
113
Fixing the lever
*
Injection quantity adjustment_06
Adjusting point
I
Rack position
-
Pump speed
r/min
100
100
100
Average injection quantity
mm3/st.
140
140
150
Fixing the lever
*
Rack limit
*
Timer adjustment
Pump speed
r/min
950--
Advance angle
deg.
0
0
0
Load
1/5
Remarks
Start
Start
Timer adjustment_02
Pump speed
r/min
900
Advance angle
deg.
0.3
Load
1/5
Timer adjustment_03
Pump speed
r/min
-
Advance angle
deg.
1.25
0.95
1.55
Load
5/5
Remarks
Measure the actual speed.
Measure the actual speed.
Timer adjustment_04
Pump speed
r/min
(1190++)
Advance angle
deg.
1.25
0.95
1.55
Load
2/5
Remarks
Measure the actual speed.
Measure the actual speed.
Timer adjustment_05
Pump speed
r/min
1255-50
Advance angle
deg.
1.25
0.95
1.55
Load
5/5
Timer adjustment_06
Pump speed
r/min
1420-50
Advance angle
deg.
5.5
5.2
5.8
Load
5/5
Remarks
Finish
Finish
Test data Ex:
Governor adjustment

N:Pump speed
R:Rack position (mm)
(1)Torque cam stamping: T1
(2)Tolerance for racks not indicated: +-0.05mm.
(3)RACK LIMIT
----------
T1=K67
----------
----------
T1=K67
----------
Speed control lever angle

F:Full speed
I:Idle
(1)Use the hole at R = aa
(2)Stopper bolt set position 'H'
----------
aa=41mm
----------
a=6deg+-5deg b=(45.5deg)+-3deg
----------
aa=41mm
----------
a=6deg+-5deg b=(45.5deg)+-3deg
Stop lever angle
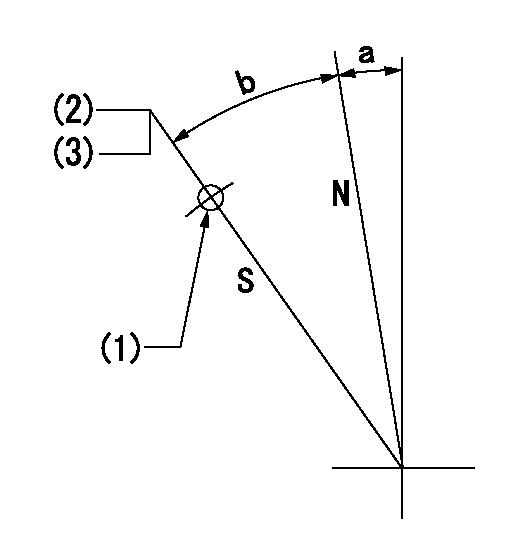
N:Pump normal
S:Stop the pump.
(1)Use the hole at R = aa
(2)Set the stopper bolt at speed = bb and rack position = cc (non-injection rack position). Confirm non-injection.
(3)After setting the stopper bolt, confirm non-injection at speed dd. Rack position = non-injection rack position (actual measurement)
----------
aa=50mm bb=1610r/min cc=6.5-0.5mm dd=275r/min
----------
a=0deg+-5deg b=(26deg)+-5deg
----------
aa=50mm bb=1610r/min cc=6.5-0.5mm dd=275r/min
----------
a=0deg+-5deg b=(26deg)+-5deg
Timing setting

(1)Pump vertical direction
(2)Coupling's key groove position at No 1 cylinder's beginning of injection
(3)-
(4)-
----------
----------
a=(20deg)
----------
----------
a=(20deg)
Information:
Solenoid Valve Replacement
Make reference to the at the beginning of the Testing And Adjusting section.
This procedure assumes that the ether cylinder mounted on the failed solenoid valve may still contain ether and is usable. If the ether cylinder is empty and needs replacement, complete this procedure and then follow the normal cylinder replacement procedure. See Ether Cylinder Replacement.
Solenoid Valve Assembly The solenoid valve itself is not serviceable. The complete solenoid valve assembly must be replaced. This includes the mounting bracket.1. Turn the disconnect switch to the OFF position. 2. Remove the ether cylinder from failed solenoid valve (1).3. Disconnect ether line (2) from the outlet of failed solenoid valve (1).4. Disconnect (unplug) solenoid valve harness connector (3). 5. Remove the reset switch bracket from the solenoid valve by removing two bolts (4). Leave the reset switch and wires intact on the bracket.6. Remove the solenoid valve assembly, which includes the mounting bracket, from the vehicle by removing two bolts (5).
Orifice Fitting And Filter7. Prepare the new solenoid valve for installation by installing a new orifice fitting and filter.
The orifice fitting has left-hand threads.
8. Attach the new solenoid valve and reset switch bracket to the vehicle. Tighten top two bolts (5) and leave lower two bolts (4) loose.
Gasket Filter9. Install a new gasket filter into the inlet of the solenoid valve.10. Install the same ether cylinder. See within Ether Cylinder Replacement. Hand tighten the ether cylinder to the solenoid valve. 11. Adjust the reset switch bracket such that reset switch button (6) depresses as much as possible while contacting the ether cylinder. Tighten lower two bolts (4) which fasten the reset switch bracket and solenoid valve to the vehicle. The reset switch must be adjusted correctly in order for the ether injection system to operate properly. The function of the reset switch is: to be OPEN (depressed switch button) when an ether cylinder is installed, and to be CLOSED (extended switch button) when the ether cylinder is removed. Ether injection is disabled when an ether cylinder is removed (reset switch closed).12. Verify that the reset switch is OPEN by continuity checking between the pin and socket in harness plug (7) of the reset switch. There should be no continuity.13. Reconnect the harnesses to the solenoid valve and the reset switch. Turn the disconnect switch to the ON position.Ether Cylinder Removal
Non-Empty Cylinders
During maintenance or servicing, the ether cylinders may need to be removed when they are not empty (for example, the cylinders may have to be removed to gain access to some other item requiring service). Under these conditions, it is desirable to remove and reinstall the ether cylinders without disturbing the "ether cylinder timers" within the ether injection control. This procedure allows the same ether cylinder to be reinstalled after it has been removed. Normal ether cylinder replacement is performed when the ether cylinder is empty. Normal removal of an empty ether cylinder resets the "ether cylinder timers" within the ether injection control. See Ether Cylinder Replacement. Failure to
Make reference to the at the beginning of the Testing And Adjusting section.
This procedure assumes that the ether cylinder mounted on the failed solenoid valve may still contain ether and is usable. If the ether cylinder is empty and needs replacement, complete this procedure and then follow the normal cylinder replacement procedure. See Ether Cylinder Replacement.
Solenoid Valve Assembly The solenoid valve itself is not serviceable. The complete solenoid valve assembly must be replaced. This includes the mounting bracket.1. Turn the disconnect switch to the OFF position. 2. Remove the ether cylinder from failed solenoid valve (1).3. Disconnect ether line (2) from the outlet of failed solenoid valve (1).4. Disconnect (unplug) solenoid valve harness connector (3). 5. Remove the reset switch bracket from the solenoid valve by removing two bolts (4). Leave the reset switch and wires intact on the bracket.6. Remove the solenoid valve assembly, which includes the mounting bracket, from the vehicle by removing two bolts (5).
Orifice Fitting And Filter7. Prepare the new solenoid valve for installation by installing a new orifice fitting and filter.
The orifice fitting has left-hand threads.
8. Attach the new solenoid valve and reset switch bracket to the vehicle. Tighten top two bolts (5) and leave lower two bolts (4) loose.
Gasket Filter9. Install a new gasket filter into the inlet of the solenoid valve.10. Install the same ether cylinder. See within Ether Cylinder Replacement. Hand tighten the ether cylinder to the solenoid valve. 11. Adjust the reset switch bracket such that reset switch button (6) depresses as much as possible while contacting the ether cylinder. Tighten lower two bolts (4) which fasten the reset switch bracket and solenoid valve to the vehicle. The reset switch must be adjusted correctly in order for the ether injection system to operate properly. The function of the reset switch is: to be OPEN (depressed switch button) when an ether cylinder is installed, and to be CLOSED (extended switch button) when the ether cylinder is removed. Ether injection is disabled when an ether cylinder is removed (reset switch closed).12. Verify that the reset switch is OPEN by continuity checking between the pin and socket in harness plug (7) of the reset switch. There should be no continuity.13. Reconnect the harnesses to the solenoid valve and the reset switch. Turn the disconnect switch to the ON position.Ether Cylinder Removal
Non-Empty Cylinders
During maintenance or servicing, the ether cylinders may need to be removed when they are not empty (for example, the cylinders may have to be removed to gain access to some other item requiring service). Under these conditions, it is desirable to remove and reinstall the ether cylinders without disturbing the "ether cylinder timers" within the ether injection control. This procedure allows the same ether cylinder to be reinstalled after it has been removed. Normal ether cylinder replacement is performed when the ether cylinder is empty. Normal removal of an empty ether cylinder resets the "ether cylinder timers" within the ether injection control. See Ether Cylinder Replacement. Failure to