Information injection-pump assembly
ZEXEL
101603-2260
1016032260
HINO
220009070A
220009070a
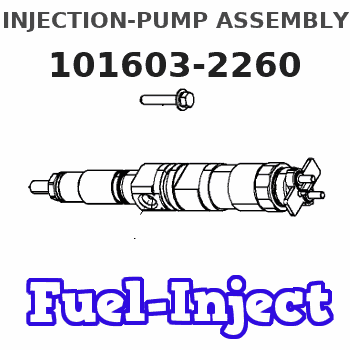
Rating:
Service parts 101603-2260 INJECTION-PUMP ASSEMBLY:
1.
_
7.
COUPLING PLATE
8.
_
9.
_
11.
Nozzle and Holder
23600-2830A
12.
Open Pre:MPa(Kqf/cm2)
17.7{180}
15.
NOZZLE SET
Cross reference number
ZEXEL
101603-2260
1016032260
HINO
220009070A
220009070a
Zexel num
Bosch num
Firm num
Name
Calibration Data:
Adjustment conditions
Test oil
1404 Test oil ISO4113 or {SAEJ967d}
1404 Test oil ISO4113 or {SAEJ967d}
Test oil temperature
degC
40
40
45
Nozzle and nozzle holder
105780-8260
Bosch type code
9 430 610 133
Nozzle
105780-0120
Bosch type code
1 688 901 990
Nozzle holder
105780-2190
Opening pressure
MPa
18
Opening pressure
kgf/cm2
184
Injection pipe
Outer diameter - inner diameter - length (mm) mm 6-2-600
Outer diameter - inner diameter - length (mm) mm 6-2-600
Overflow valve
131425-0620
Overflow valve opening pressure
kPa
255
221
289
Overflow valve opening pressure
kgf/cm2
2.6
2.25
2.95
Tester oil delivery pressure
kPa
255
255
255
Tester oil delivery pressure
kgf/cm2
2.6
2.6
2.6
Direction of rotation (viewed from drive side)
Right R
Right R
Injection timing adjustment
Direction of rotation (viewed from drive side)
Right R
Right R
Injection order
1-4-2-6-
3-5
Pre-stroke
mm
4
3.97
4.03
Beginning of injection position
Drive side NO.1
Drive side NO.1
Difference between angles 1
Cal 1-4 deg. 60 59.75 60.25
Cal 1-4 deg. 60 59.75 60.25
Difference between angles 2
Cyl.1-2 deg. 120 119.75 120.25
Cyl.1-2 deg. 120 119.75 120.25
Difference between angles 3
Cal 1-6 deg. 180 179.75 180.25
Cal 1-6 deg. 180 179.75 180.25
Difference between angles 4
Cal 1-3 deg. 240 239.75 240.25
Cal 1-3 deg. 240 239.75 240.25
Difference between angles 5
Cal 1-5 deg. 300 299.75 300.25
Cal 1-5 deg. 300 299.75 300.25
Injection quantity adjustment
Adjusting point
-
Rack position
11.3
Pump speed
r/min
850
850
850
Average injection quantity
mm3/st.
93
91
95
Max. variation between cylinders
%
0
-3.5
3.5
Basic
*
Fixing the rack
*
Standard for adjustment of the maximum variation between cylinders
*
Injection quantity adjustment_02
Adjusting point
Z
Rack position
9+-0.5
Pump speed
r/min
265
265
265
Each cylinder's injection qty
mm3/st.
15
14
16
Fixing the rack
*
Standard for adjustment of the maximum variation between cylinders
*
Injection quantity adjustment_03
Adjusting point
A
Rack position
R1(11.3)
Pump speed
r/min
850
850
850
Average injection quantity
mm3/st.
93
92
94
Basic
*
Fixing the lever
*
Injection quantity adjustment_04
Adjusting point
B
Rack position
R1+0.8
Pump speed
r/min
1450
1450
1450
Average injection quantity
mm3/st.
96
92
100
Fixing the lever
*
Injection quantity adjustment_05
Adjusting point
D
Rack position
R1-0.8
Pump speed
r/min
580
580
580
Average injection quantity
mm3/st.
74.5
70.5
78.5
Fixing the lever
*
Injection quantity adjustment_06
Adjusting point
I
Rack position
-
Pump speed
r/min
100
100
100
Average injection quantity
mm3/st.
140
140
150
Fixing the lever
*
Rack limit
*
Timer adjustment
Pump speed
r/min
1100+50
Advance angle
deg.
0
0
0
Remarks
Start
Start
Timer adjustment_02
Pump speed
r/min
1450-50
Advance angle
deg.
3.5
3.2
3.8
Remarks
Finish
Finish
Test data Ex:
Governor adjustment
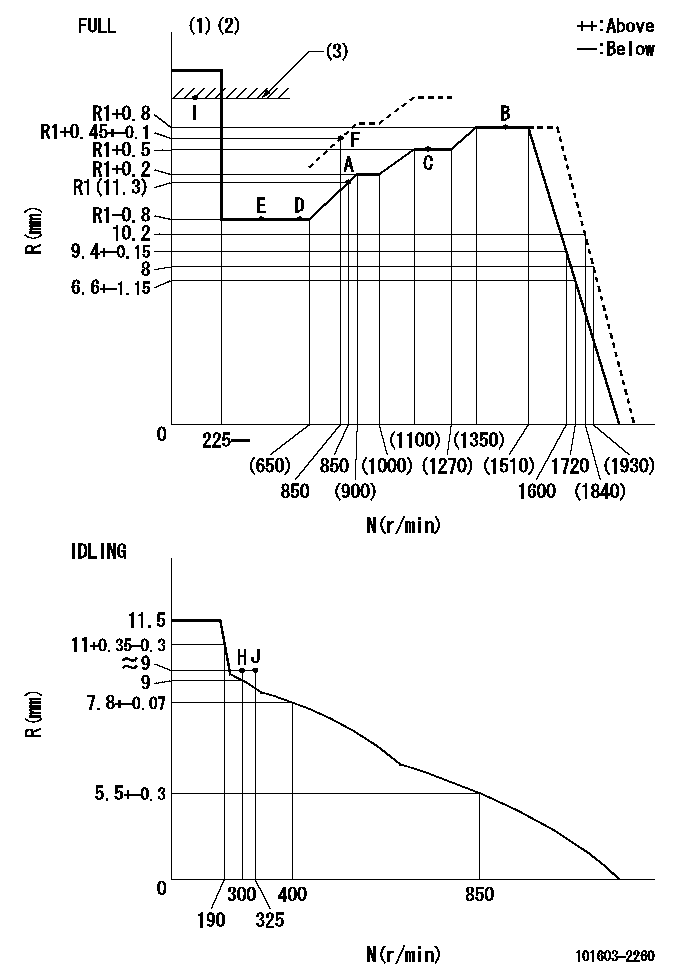
N:Pump speed
R:Rack position (mm)
(1)Torque cam stamping: T1
(2)Tolerance for racks not indicated: +-0.05mm.
(3)RACK LIMIT
----------
T1=L26
----------
----------
T1=L26
----------
Speed control lever angle
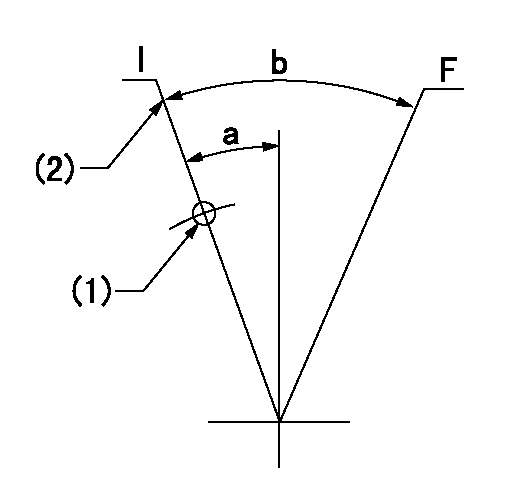
F:Full speed
I:Idle
(1)Use the hole at R = aa
(2)Stopper bolt set position 'H'
----------
aa=25.5mm
----------
a=20deg+-5deg b=38deg+-3deg
----------
aa=25.5mm
----------
a=20deg+-5deg b=38deg+-3deg
Stop lever angle
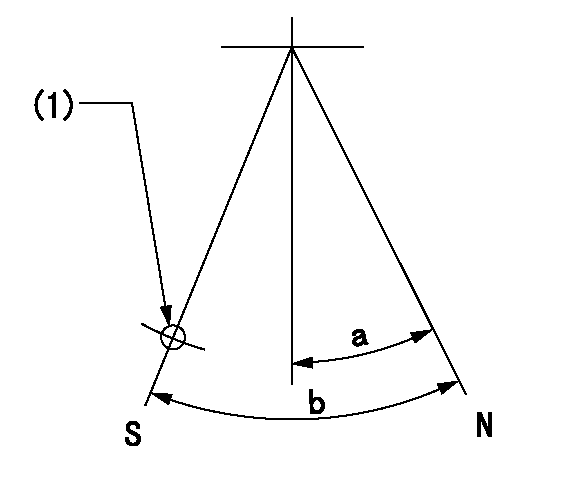
N:Pump normal
S:Stop the pump.
(1)Use the hole at R = aa
----------
aa=35mm
----------
a=14.5deg+-5deg b=40deg+-5deg
----------
aa=35mm
----------
a=14.5deg+-5deg b=40deg+-5deg
0000001501 TAMPER PROOF
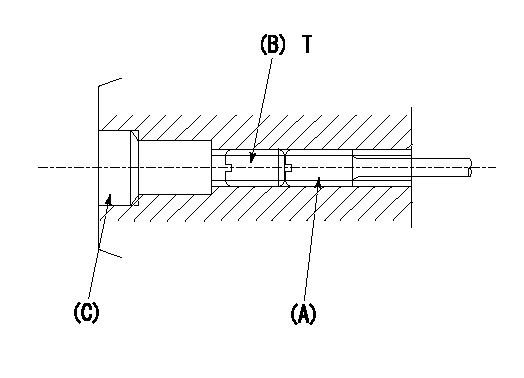
1. Method for setting tamperproof proofing
(1)Perform after governor adjustment (torque cam phase adjustment).
(2)Increase the full rack position to Ra using the load lever.
(3)Push in screw (A) to Rb.
(4)Temporarily caulk using the tip of a screwdriver
(5)Confirm that the rack at that time is at Rb .
(6)Lock using setscrew (B). (Tightening torque = T)
(7)Pressfit (C) after applying adhesive.
(8)Readjust the full rack using the load lever.
----------
Ra=R1(11.3)+0.45+-0.1mm Rb=R1(11.3)+0.45+-0.1mm
----------
T=3.4~4.9N-m(0.35~0.5Kgf-m)
----------
Ra=R1(11.3)+0.45+-0.1mm Rb=R1(11.3)+0.45+-0.1mm
----------
T=3.4~4.9N-m(0.35~0.5Kgf-m)
0000001601 AIR CYLINDER
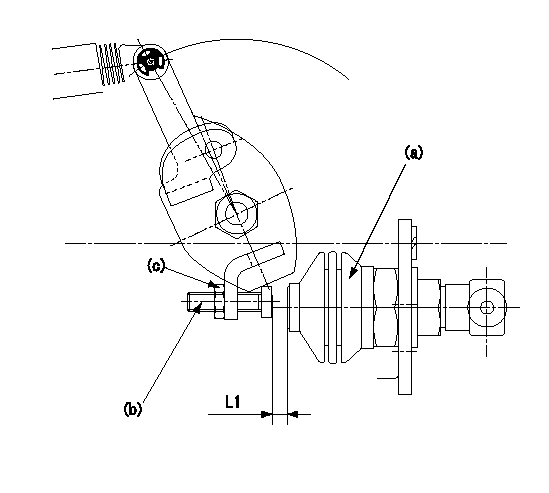
Adjustment of the air cylinder
1. Set the speed lever at the idling position.
2. Set the gap between the air cylinder (a) and the set bolt (b) to L1.
3. Set the speed at N1, apply positive pressure P1 to the air cylinder (a) and read the rack position.
4. Push set bolt (b) out and tighten nut (c) at N1 when the rack position is R1.
5. Apply positive pressure several times and confirm that the lever returns to the idle position at positive pressure P2.
6. Confirm that the rack position is R1 at positive pressure P1.
----------
L1=(8)mm R1=8.8+-0.1mm N1=475r/min P1=392+98kPa(4+1kgf/cm2) P2=0kPa(0kgf/cm2)
----------
----------
L1=(8)mm R1=8.8+-0.1mm N1=475r/min P1=392+98kPa(4+1kgf/cm2) P2=0kPa(0kgf/cm2)
----------
Timing setting
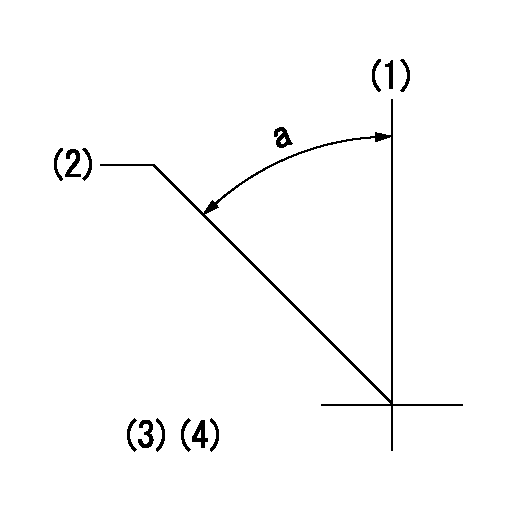
(1)Pump vertical direction
(2)Coupling's key groove position at No 1 cylinder's beginning of injection
(3)-
(4)-
----------
----------
a=(50deg)
----------
----------
a=(50deg)
Information:
Lubrication System
OIL LUBRICATION SCHEMATICThe lubrication system is the pressure type. The oil pump draws oil from the sump through a suction pipe and strainer to the pump. The oil pump is driven by the auxiliary drive group which is driven by the timing gears.Pressure oil flows to the oil cooler. The oil cooler is cooled by water from the cooling system. Coolers on T6.3544 Engines have a bypass valve that allows the oil to go around the cooler in case of a restriction or if the oil is too cold and thick. From the cooler, oil passes through the relief valve. On T6.3544 Engines, the relief valve is two stage. At 205 to 225 kPa (30 to 37 psi), oil is fed by a pipe to the piston cooling jet gallery which is a drilled passage the length of the crankcase, above the camshaft chamber. The piston cooling jets are bolted into the gallery and point into the bottom of each cylinder. Oil is sprayed onto the underneath side of each piston which takes heat from the combustion area. The oil then drains back to sump.At 345 to 415 kPa (50 to 60 psi), oil passes through a single oil filter on 6.3544 Engines or two filters on T6.3544 Engines. Oil then flows to the main oil gallery which is a drilled passage the length of the crankcase. Oil also flows from the filters to the turbocharger bearings on T6.3544 Engines. Passages in the crankcase webs feed oil from the main oil gallery to the main bearings. Passages in the crankshaft carry oil to the big end bearings. Through passages in No. 1, 3, 5 and 7 crankcase webs, oil passes from the main bearings to lubricate the camshaft bearings.The No. 2 camshaft bearing supplies a controlled amount of oil to the rocker shaft assembly, which then flows through a small bleed hole in each rocker lever to lubricate the valves and springs.Pistons, cylinder liners, connecting rod small end bushings, cam lobes and valve lifters are splash and oil mist lubricated.Oil flows from the main oil gallery to the two idler gear hubs. The oil passes through the hubs to radial passages in the idler gears to lubricate the teeth of the timing gears.The auxiliary drive group shaft bearings are lubricated by a passage from the main oil gallery to the front auxiliary drive shaft bearing. Oil then passes around a groove in the bearing journal and through another passage along the outer side of the auxiliary drive housing to the rear auxiliary drive shaft bearing. The upper fuel pump bearing is also lubricated from this passage. Also connected to this outer housing passage is a spray tube which directs oil on to the auxiliary drive shaft (worn gear) and gear assembly (worm wheel).Air Inlet And Exhaust System
6.3544 Engines
AIR INLET AND EXHAUST SYSTEM COMPONENTS
1. Exhaust manifold. 2. Inlet manifold. 3. Engine cylinderThe air inlet and exhaust system components on naturally aspirated engines are: the air cleaner, inlet manifold,
OIL LUBRICATION SCHEMATICThe lubrication system is the pressure type. The oil pump draws oil from the sump through a suction pipe and strainer to the pump. The oil pump is driven by the auxiliary drive group which is driven by the timing gears.Pressure oil flows to the oil cooler. The oil cooler is cooled by water from the cooling system. Coolers on T6.3544 Engines have a bypass valve that allows the oil to go around the cooler in case of a restriction or if the oil is too cold and thick. From the cooler, oil passes through the relief valve. On T6.3544 Engines, the relief valve is two stage. At 205 to 225 kPa (30 to 37 psi), oil is fed by a pipe to the piston cooling jet gallery which is a drilled passage the length of the crankcase, above the camshaft chamber. The piston cooling jets are bolted into the gallery and point into the bottom of each cylinder. Oil is sprayed onto the underneath side of each piston which takes heat from the combustion area. The oil then drains back to sump.At 345 to 415 kPa (50 to 60 psi), oil passes through a single oil filter on 6.3544 Engines or two filters on T6.3544 Engines. Oil then flows to the main oil gallery which is a drilled passage the length of the crankcase. Oil also flows from the filters to the turbocharger bearings on T6.3544 Engines. Passages in the crankcase webs feed oil from the main oil gallery to the main bearings. Passages in the crankshaft carry oil to the big end bearings. Through passages in No. 1, 3, 5 and 7 crankcase webs, oil passes from the main bearings to lubricate the camshaft bearings.The No. 2 camshaft bearing supplies a controlled amount of oil to the rocker shaft assembly, which then flows through a small bleed hole in each rocker lever to lubricate the valves and springs.Pistons, cylinder liners, connecting rod small end bushings, cam lobes and valve lifters are splash and oil mist lubricated.Oil flows from the main oil gallery to the two idler gear hubs. The oil passes through the hubs to radial passages in the idler gears to lubricate the teeth of the timing gears.The auxiliary drive group shaft bearings are lubricated by a passage from the main oil gallery to the front auxiliary drive shaft bearing. Oil then passes around a groove in the bearing journal and through another passage along the outer side of the auxiliary drive housing to the rear auxiliary drive shaft bearing. The upper fuel pump bearing is also lubricated from this passage. Also connected to this outer housing passage is a spray tube which directs oil on to the auxiliary drive shaft (worn gear) and gear assembly (worm wheel).Air Inlet And Exhaust System
6.3544 Engines
AIR INLET AND EXHAUST SYSTEM COMPONENTS
1. Exhaust manifold. 2. Inlet manifold. 3. Engine cylinderThe air inlet and exhaust system components on naturally aspirated engines are: the air cleaner, inlet manifold,