Information injection-pump assembly
ZEXEL
101603-2032
1016032032
HINO
220204121A
220204121a
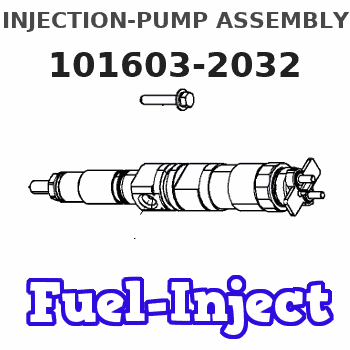
Rating:
Service parts 101603-2032 INJECTION-PUMP ASSEMBLY:
1.
_
7.
COUPLING PLATE
8.
_
9.
_
11.
Nozzle and Holder
23600-2490A
12.
Open Pre:MPa(Kqf/cm2)
19.6{200}
15.
NOZZLE SET
Cross reference number
ZEXEL
101603-2032
1016032032
HINO
220204121A
220204121a
Zexel num
Bosch num
Firm num
Name
Calibration Data:
Adjustment conditions
Test oil
1404 Test oil ISO4113 or {SAEJ967d}
1404 Test oil ISO4113 or {SAEJ967d}
Test oil temperature
degC
40
40
45
Nozzle and nozzle holder
105780-8140
Bosch type code
EF8511/9A
Nozzle
105780-0000
Bosch type code
DN12SD12T
Nozzle holder
105780-2080
Bosch type code
EF8511/9
Opening pressure
MPa
17.2
Opening pressure
kgf/cm2
175
Injection pipe
Outer diameter - inner diameter - length (mm) mm 6-2-600
Outer diameter - inner diameter - length (mm) mm 6-2-600
Overflow valve
134424-0920
Overflow valve opening pressure
kPa
162
147
177
Overflow valve opening pressure
kgf/cm2
1.65
1.5
1.8
Tester oil delivery pressure
kPa
157
157
157
Tester oil delivery pressure
kgf/cm2
1.6
1.6
1.6
Direction of rotation (viewed from drive side)
Right R
Right R
Injection timing adjustment
Direction of rotation (viewed from drive side)
Right R
Right R
Injection order
1-4-2-6-
3-5
Pre-stroke
mm
4.8
4.77
4.83
Beginning of injection position
Drive side NO.1
Drive side NO.1
Difference between angles 1
Cal 1-4 deg. 60 59.75 60.25
Cal 1-4 deg. 60 59.75 60.25
Difference between angles 2
Cyl.1-2 deg. 120 119.75 120.25
Cyl.1-2 deg. 120 119.75 120.25
Difference between angles 3
Cal 1-6 deg. 180 179.75 180.25
Cal 1-6 deg. 180 179.75 180.25
Difference between angles 4
Cal 1-3 deg. 240 239.75 240.25
Cal 1-3 deg. 240 239.75 240.25
Difference between angles 5
Cal 1-5 deg. 300 299.75 300.25
Cal 1-5 deg. 300 299.75 300.25
Injection quantity adjustment
Adjusting point
A
Rack position
11.6
Pump speed
r/min
1050
1050
1050
Average injection quantity
mm3/st.
117
115.5
118.5
Max. variation between cylinders
%
0
-3.5
3.5
Basic
*
Fixing the lever
*
Boost pressure
kPa
35.3
35.3
Boost pressure
mmHg
265
265
Injection quantity adjustment_02
Adjusting point
-
Rack position
6.2
Pump speed
r/min
430
430
430
Average injection quantity
mm3/st.
10
9
11
Max. variation between cylinders
%
0
-10
10
Fixing the rack
*
Boost pressure
kPa
0
0
0
Boost pressure
mmHg
0
0
0
Remarks
Adjust only variation between cylinders; adjust governor according to governor specifications.
Adjust only variation between cylinders; adjust governor according to governor specifications.
Injection quantity adjustment_03
Adjusting point
D
Rack position
-
Pump speed
r/min
100
100
100
Average injection quantity
mm3/st.
140
140
150
Fixing the lever
*
Boost pressure
kPa
0
0
0
Boost pressure
mmHg
0
0
0
Rack limit
*
Boost compensator adjustment
Pump speed
r/min
800
800
800
Rack position
R1-1.2
Boost pressure
kPa
8.7
6
11.4
Boost pressure
mmHg
65
45
85
Boost compensator adjustment_02
Pump speed
r/min
800
800
800
Rack position
R1(11.6)
Boost pressure
kPa
22
15.3
28.7
Boost pressure
mmHg
165
115
215
Timer adjustment
Pump speed
r/min
850--
Advance angle
deg.
0
0
0
Remarks
Start
Start
Timer adjustment_02
Pump speed
r/min
800
Advance angle
deg.
0.5
Timer adjustment_03
Pump speed
r/min
1050
Advance angle
deg.
2
1.5
2.5
Remarks
Finish
Finish
Test data Ex:
Governor adjustment
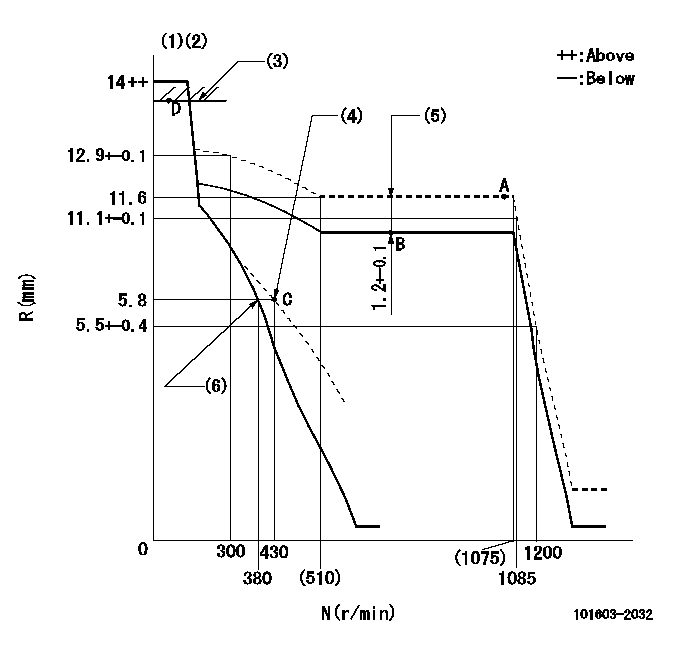
N:Pump speed
R:Rack position (mm)
(1)Target notch: K
(2)Tolerance for racks not indicated: +-0.05mm.
(3)RACK LIMIT
(4)Set idle sub-spring
(5)Boost compensator stroke
(6)Main spring setting
----------
K=16
----------
----------
K=16
----------
Speed control lever angle
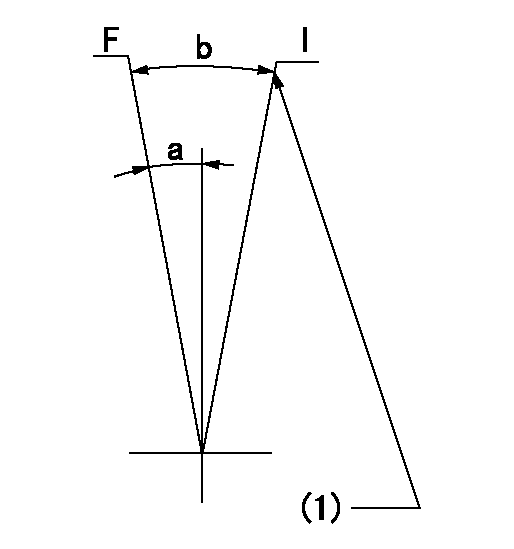
F:Full speed
I:Idle
(1)Stopper bolt setting
----------
----------
a=16deg+-5deg b=28deg+-5deg
----------
----------
a=16deg+-5deg b=28deg+-5deg
Stop lever angle

N:Pump normal
S:Stop the pump.
(1)Speed = aa, rack position = bb (sealed at shipping)
----------
aa=0r/min bb=1-0.5mm
----------
a=21deg+-5deg b=(55deg)
----------
aa=0r/min bb=1-0.5mm
----------
a=21deg+-5deg b=(55deg)
Timing setting
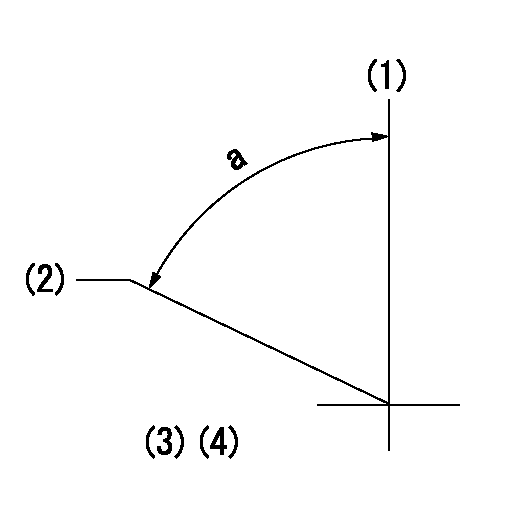
(1)Pump vertical direction
(2)Coupling's key groove position at No 1 cylinder's beginning of injection
(3)-
(4)-
----------
----------
a=(50deg)
----------
----------
a=(50deg)
Information:
2. Locate wire 405-GY on the main cab harness near the connector exiting the cab wall on the right hand side, as shown by arrow.Cut this wire close to the connector. Splice it and the wire just assembled using an 8S4626 Splice. Be sure to splice to the portion of the wire that goes into the cab harness.3. Connect the 7N9738 Housing to the two pin connector on the 8X9862 Harness Assembly (housing containing 405-GY). Clip with a 3T3048 Clip Assembly.Installation of 8X8384 Ether (Chassis) Wiring Harness
The 8X7433 Chassis Harness called out in the AEIS Special Instruction, is replaced with 8X8384 Chassis Harness.Follow the installation procedure outlined in the AEIS Special Instruction for the 8X7433 Harness Assembly. Be sure to use the new 8X8382 Wire Assembly for the harness code plug.Installation of 8X8385 Ether (Engine) Wiring Harness
The 8X7107 Engine Harness on the AEIS is replaced with 8X8385 Harness Assembly.Follow the installation procedure outlined in the AEIS Special Instruction for the 8X7107 Harness Assembly. In addition, the following steps need to be performed. 1. Route the end of the harness with the 8T8732 Receptacle to the 3E3530 Electronic Control Group [oil pressure sensor] (2), installed at the right rear of the engine as shown.2. Connect the three pin receptacle to the connector on the 3E3530 Electronic Control Group (2) and clip into the 9X3495 Clip Assembly (7) installed earlier. Use 3S2093 Straps to loosely secure the harness to the top rear of the engine as shown.3. Remove the 8W3048 Harness Assembly that is connected to the remaining 6T7663 Oil Pressure Switch (9) and was connected to the 6T7663 Oil Pressure Switch that was removed.4. Connect an 8X8337 Harness Assembly to the one remaining oil pressure switch and reconnect to the engine harness. Clip with the existing clip. DO NOT tighten the straps or clips until all new wiring harnesses have been installed so any repositioning or adjustments can be made as necessary.Checking the Automatic Ether Injection System
* The system check-out will be same as for the AEIS with the following change:"A4" harness code on the 777B (indicates 3508 application) for two seconds.Retrofit to an Existing AEIS System
Necessary Parts
Installation of 3E3778 Ether Control Group
The 3E3778 Control Group is required for the MPPS System.Check the electronic control box installed with the AEIS to see if it is a 3E3778 or a 9X5303 Control Group. If a 9X5303 Control Group is installed, replace it with 3E3778 Control Group and 3E3779 Film.Follow the control box installation instructions outlined in the AEIS installation Special Instruction, SEHS9329. Be sure to install the 8X8386 Wire Assembly between the control and mounting plate. If an MPPS identification film is needed for a language other than English, refer to the following chart for the part number of the film for a specific language. Installation of 3E3530 Electronic Control Group [(PWM) Oil Pressure Sensor]
1. Remove the 6T7663 Oil Pressure Switch and adapter from the turbo oil adapter on the right rear of the engine (switch on bottom port with
The 8X7433 Chassis Harness called out in the AEIS Special Instruction, is replaced with 8X8384 Chassis Harness.Follow the installation procedure outlined in the AEIS Special Instruction for the 8X7433 Harness Assembly. Be sure to use the new 8X8382 Wire Assembly for the harness code plug.Installation of 8X8385 Ether (Engine) Wiring Harness
The 8X7107 Engine Harness on the AEIS is replaced with 8X8385 Harness Assembly.Follow the installation procedure outlined in the AEIS Special Instruction for the 8X7107 Harness Assembly. In addition, the following steps need to be performed. 1. Route the end of the harness with the 8T8732 Receptacle to the 3E3530 Electronic Control Group [oil pressure sensor] (2), installed at the right rear of the engine as shown.2. Connect the three pin receptacle to the connector on the 3E3530 Electronic Control Group (2) and clip into the 9X3495 Clip Assembly (7) installed earlier. Use 3S2093 Straps to loosely secure the harness to the top rear of the engine as shown.3. Remove the 8W3048 Harness Assembly that is connected to the remaining 6T7663 Oil Pressure Switch (9) and was connected to the 6T7663 Oil Pressure Switch that was removed.4. Connect an 8X8337 Harness Assembly to the one remaining oil pressure switch and reconnect to the engine harness. Clip with the existing clip. DO NOT tighten the straps or clips until all new wiring harnesses have been installed so any repositioning or adjustments can be made as necessary.Checking the Automatic Ether Injection System
* The system check-out will be same as for the AEIS with the following change:"A4" harness code on the 777B (indicates 3508 application) for two seconds.Retrofit to an Existing AEIS System
Necessary Parts
Installation of 3E3778 Ether Control Group
The 3E3778 Control Group is required for the MPPS System.Check the electronic control box installed with the AEIS to see if it is a 3E3778 or a 9X5303 Control Group. If a 9X5303 Control Group is installed, replace it with 3E3778 Control Group and 3E3779 Film.Follow the control box installation instructions outlined in the AEIS installation Special Instruction, SEHS9329. Be sure to install the 8X8386 Wire Assembly between the control and mounting plate. If an MPPS identification film is needed for a language other than English, refer to the following chart for the part number of the film for a specific language. Installation of 3E3530 Electronic Control Group [(PWM) Oil Pressure Sensor]
1. Remove the 6T7663 Oil Pressure Switch and adapter from the turbo oil adapter on the right rear of the engine (switch on bottom port with