Information injection-pump assembly
ZEXEL
101603-1820
1016031820
MITSUBISHI
ME035694
me035694

Rating:
Service parts 101603-1820 INJECTION-PUMP ASSEMBLY:
1.
_
6.
COUPLING PLATE
7.
COUPLING PLATE
8.
_
9.
_
11.
Nozzle and Holder
12.
Open Pre:MPa(Kqf/cm2)
21.6(220)
15.
NOZZLE SET
Cross reference number
ZEXEL
101603-1820
1016031820
MITSUBISHI
ME035694
me035694
Zexel num
Bosch num
Firm num
Name
Calibration Data:
Adjustment conditions
Test oil
1404 Test oil ISO4113 or {SAEJ967d}
1404 Test oil ISO4113 or {SAEJ967d}
Test oil temperature
degC
40
40
45
Nozzle and nozzle holder
105780-8140
Bosch type code
EF8511/9A
Nozzle
105780-0000
Bosch type code
DN12SD12T
Nozzle holder
105780-2080
Bosch type code
EF8511/9
Opening pressure
MPa
17.2
Opening pressure
kgf/cm2
175
Injection pipe
Outer diameter - inner diameter - length (mm) mm 6-2-600
Outer diameter - inner diameter - length (mm) mm 6-2-600
Overflow valve
131424-5520
Overflow valve opening pressure
kPa
255
221
289
Overflow valve opening pressure
kgf/cm2
2.6
2.25
2.95
Tester oil delivery pressure
kPa
157
157
157
Tester oil delivery pressure
kgf/cm2
1.6
1.6
1.6
Direction of rotation (viewed from drive side)
Left L
Left L
Injection timing adjustment
Direction of rotation (viewed from drive side)
Left L
Left L
Injection order
1-5-3-6-
2-4
Pre-stroke
mm
3.3
3.25
3.35
Beginning of injection position
Governor side NO.1
Governor side NO.1
Difference between angles 1
Cal 1-5 deg. 60 59.5 60.5
Cal 1-5 deg. 60 59.5 60.5
Difference between angles 2
Cal 1-3 deg. 120 119.5 120.5
Cal 1-3 deg. 120 119.5 120.5
Difference between angles 3
Cal 1-6 deg. 180 179.5 180.5
Cal 1-6 deg. 180 179.5 180.5
Difference between angles 4
Cyl.1-2 deg. 240 239.5 240.5
Cyl.1-2 deg. 240 239.5 240.5
Difference between angles 5
Cal 1-4 deg. 300 299.5 300.5
Cal 1-4 deg. 300 299.5 300.5
Injection quantity adjustment
Adjusting point
-
Rack position
11
Pump speed
r/min
850
850
850
Each cylinder's injection qty
mm3/st.
65
63
67
Basic
*
Fixing the rack
*
Standard for adjustment of the maximum variation between cylinders
*
Injection quantity adjustment_02
Adjusting point
H
Rack position
9.5+-0.5
Pump speed
r/min
275
275
275
Each cylinder's injection qty
mm3/st.
10.5
9
12
Fixing the rack
*
Standard for adjustment of the maximum variation between cylinders
*
Injection quantity adjustment_03
Adjusting point
A
Rack position
R1(11)
Pump speed
r/min
850
850
850
Average injection quantity
mm3/st.
65
64
66
Basic
*
Fixing the lever
*
Injection quantity adjustment_04
Adjusting point
B
Rack position
R1(11)
Pump speed
r/min
1450
1450
1450
Average injection quantity
mm3/st.
77.5
75.5
79.5
Fixing the lever
*
Injection quantity adjustment_05
Adjusting point
I
Rack position
14.1+-0.
5
Pump speed
r/min
100
100
100
Average injection quantity
mm3/st.
90
70
110
Fixing the lever
*
Rack limit
*
Timer adjustment
Pump speed
r/min
1250--
Advance angle
deg.
0
0
0
Remarks
Start
Start
Timer adjustment_02
Pump speed
r/min
1200
Advance angle
deg.
0.5
Timer adjustment_03
Pump speed
r/min
1350
Advance angle
deg.
2.4
1.9
2.9
Timer adjustment_04
Pump speed
r/min
1500
Advance angle
deg.
5
4.5
5.5
Remarks
Finish
Finish
Test data Ex:
Governor adjustment
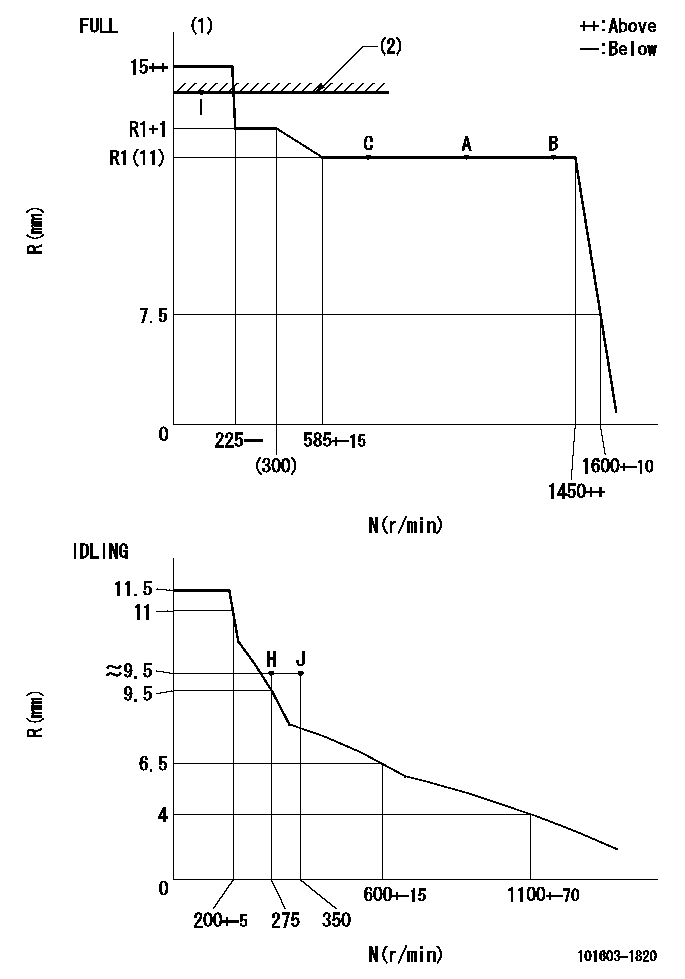
N:Pump speed
R:Rack position (mm)
(1)Torque cam stamping: T1
(2)RACK LIMIT
----------
T1=A10
----------
----------
T1=A10
----------
Speed control lever angle
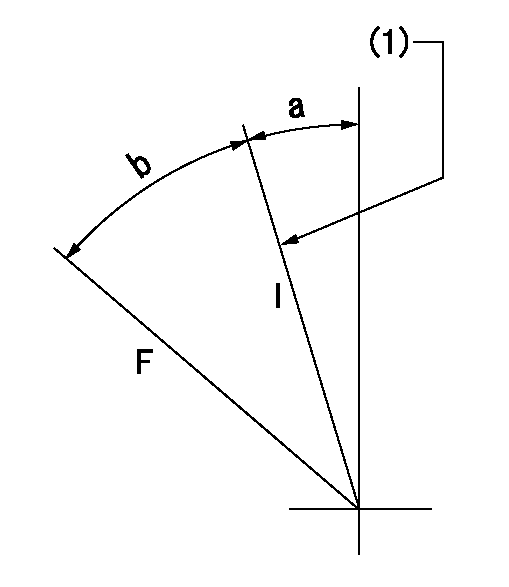
F:Full speed
I:Idle
(1)Stopper bolt set position 'H'
----------
----------
a=18.5deg+-5deg b=40.5deg+-3deg
----------
----------
a=18.5deg+-5deg b=40.5deg+-3deg
Stop lever angle
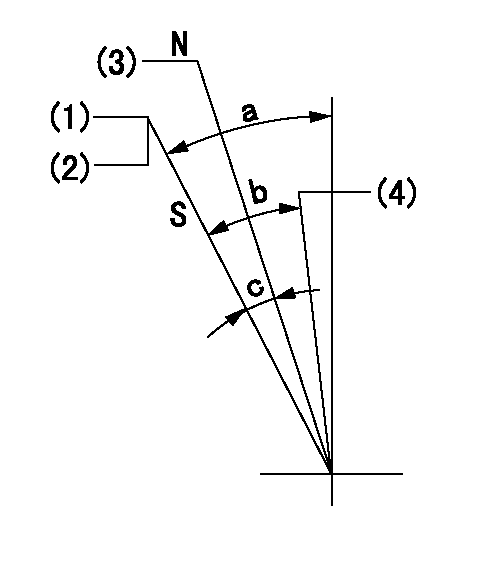
N:Pump normal
S:Stop the pump.
(1)At the rated pump speed and rack position aa, set the stopper bolt. (Confirm that there is no injection.)
(2)After setting the stopper bolt, confirm non-injection at speed = bb. Rack position = cc (non-injection rack position).
(3)Rack position = approximately dd
(4)Free (at shipping)
----------
aa=(5.4)mm bb=275r/min cc=(7.4)mm dd=17.4mm
----------
a=38.5deg+-5deg b=(27deg) c=17deg+-5deg
----------
aa=(5.4)mm bb=275r/min cc=(7.4)mm dd=17.4mm
----------
a=38.5deg+-5deg b=(27deg) c=17deg+-5deg
0000001501 MICRO SWITCH
Adjustment of the micro-switch
Adjust the bolt to obtain the following lever position when the micro-switch is ON.
(1)Speed N1
(2)Rack position Ra
----------
N1=400+-5r/min Ra=9.2mm
----------
----------
N1=400+-5r/min Ra=9.2mm
----------
Timing setting

(1)Pump vertical direction
(2)Position of timer's tooth at No 1 cylinder's beginning of injection
(3)B.T.D.C.: aa
(4)-
----------
aa=13deg
----------
a=(0deg)
----------
aa=13deg
----------
a=(0deg)
Information:
Heavy Duty Air Cleaners
Generator set engines equipped with heavy duty air cleaners have a serviceable air cleaner element. The element may be cleaned up to six times, but must be replaced Every Year.Remove and Install Air Cleaner Elements
Heavy duty air cleaner:(1) service indicator(2) upper body (air filter element housing)(3) clamps(4) lower body (tube element)(5) dust collector cup1. Loosen clamps (3) between the lower body (4) and the dust collector cup (5). Remove the cup.2. Loosen the clamps between the lower body and the upper body (2). Remove the tube element.3. Clean the tubes from both sides with water or air.4. Remove the air filter element from the upper body (2). Wipe the inside of the upper body clean.5. Inspect and clean air filter element. Install a clean or new element.6. Inspect the gasket between the upper body and lower body. Inspect the seal between the lower body and the dust collector cup. Install a new gasket and seal if necessary.7. Install the cleaned, dry tube element. Tighten the retaining clamps attaching the lower body to the upper body.8. Wipe the dust collector cup clean. Install the cup and tighten the retaining clamps.9. Reset the service indicator (1).Cleaning Air Filter Elements
The primary element (Caterpillar air filters) can be cleaned several times before replacement. The element, when cleaned, should be thoroughly checked for rips or tears in the filter material.Replace the primary element at least EVERY YEAR regardless of operating hours it has accumulated.
Do not clean filter elements by bumping or tapping.Do not use filter elements with damaged pleats, gaskets or seals. Engine damage could result.
Filter elements can be cleaned with air pressure, 205 kPa (30 psi) maximum, or water pressure, 280 kPa (40 psi) maximum, or detergent washing. Have spare elements on hand to use while cleaning used elements.* Direct air or water along the length of the plate inside and outside of air filter element.The element can be washed in warm water and nonsudsing household detergent, such as automatic dishwasher detergent. Rinse inside and outside the pleats. The filter should then be thoroughly air dried and inspected.* Inspect the filter elements after cleaning for any rips, tears or damage. Insert a light inside of the clean, dry element. Do not use a filter element with damaged pleats, gaskets or seals. Discard the element if damaged.* Wrap and store the clean filter elements in a clean, dry place.* Reset the service indicator by pushing the piston plunger in.For more information on air cleaner element cleaning, refer to Guideline for Reusable Parts-Cleaning and Inspection of Air Filters, SEBU8062.Air Starter & Air Tank (If Equipped)
Check Lubricator Level
Never allow the lubricator bowl (if equipped) to become empty. The starting motor will be damaged by lack of proper lubrication.
The vanes of the starting motor are lubricated with a fine mist of oil from the motor lubricator. Check the level of oil in the lubricator bowl. If the bowl is less than half full, add lubricant. Use non detergent 10W engine oil for temperatures
Generator set engines equipped with heavy duty air cleaners have a serviceable air cleaner element. The element may be cleaned up to six times, but must be replaced Every Year.Remove and Install Air Cleaner Elements
Heavy duty air cleaner:(1) service indicator(2) upper body (air filter element housing)(3) clamps(4) lower body (tube element)(5) dust collector cup1. Loosen clamps (3) between the lower body (4) and the dust collector cup (5). Remove the cup.2. Loosen the clamps between the lower body and the upper body (2). Remove the tube element.3. Clean the tubes from both sides with water or air.4. Remove the air filter element from the upper body (2). Wipe the inside of the upper body clean.5. Inspect and clean air filter element. Install a clean or new element.6. Inspect the gasket between the upper body and lower body. Inspect the seal between the lower body and the dust collector cup. Install a new gasket and seal if necessary.7. Install the cleaned, dry tube element. Tighten the retaining clamps attaching the lower body to the upper body.8. Wipe the dust collector cup clean. Install the cup and tighten the retaining clamps.9. Reset the service indicator (1).Cleaning Air Filter Elements
The primary element (Caterpillar air filters) can be cleaned several times before replacement. The element, when cleaned, should be thoroughly checked for rips or tears in the filter material.Replace the primary element at least EVERY YEAR regardless of operating hours it has accumulated.
Do not clean filter elements by bumping or tapping.Do not use filter elements with damaged pleats, gaskets or seals. Engine damage could result.
Filter elements can be cleaned with air pressure, 205 kPa (30 psi) maximum, or water pressure, 280 kPa (40 psi) maximum, or detergent washing. Have spare elements on hand to use while cleaning used elements.* Direct air or water along the length of the plate inside and outside of air filter element.The element can be washed in warm water and nonsudsing household detergent, such as automatic dishwasher detergent. Rinse inside and outside the pleats. The filter should then be thoroughly air dried and inspected.* Inspect the filter elements after cleaning for any rips, tears or damage. Insert a light inside of the clean, dry element. Do not use a filter element with damaged pleats, gaskets or seals. Discard the element if damaged.* Wrap and store the clean filter elements in a clean, dry place.* Reset the service indicator by pushing the piston plunger in.For more information on air cleaner element cleaning, refer to Guideline for Reusable Parts-Cleaning and Inspection of Air Filters, SEBU8062.Air Starter & Air Tank (If Equipped)
Check Lubricator Level
Never allow the lubricator bowl (if equipped) to become empty. The starting motor will be damaged by lack of proper lubrication.
The vanes of the starting motor are lubricated with a fine mist of oil from the motor lubricator. Check the level of oil in the lubricator bowl. If the bowl is less than half full, add lubricant. Use non detergent 10W engine oil for temperatures