Information injection-pump assembly
ZEXEL
101603-0961
1016030961
ISUZU
1156018983
1156018983
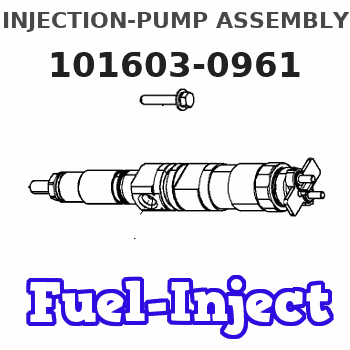
Rating:
Service parts 101603-0961 INJECTION-PUMP ASSEMBLY:
1.
_
7.
COUPLING PLATE
8.
_
9.
_
11.
Nozzle and Holder
5-15300-089-1
12.
Open Pre:MPa(Kqf/cm2)
18.1{185}
15.
NOZZLE SET
Cross reference number
ZEXEL
101603-0961
1016030961
ISUZU
1156018983
1156018983
Zexel num
Bosch num
Firm num
Name
Calibration Data:
Adjustment conditions
Test oil
1404 Test oil ISO4113 or {SAEJ967d}
1404 Test oil ISO4113 or {SAEJ967d}
Test oil temperature
degC
40
40
45
Nozzle and nozzle holder
105780-8140
Bosch type code
EF8511/9A
Nozzle
105780-0000
Bosch type code
DN12SD12T
Nozzle holder
105780-2080
Bosch type code
EF8511/9
Opening pressure
MPa
17.2
Opening pressure
kgf/cm2
175
Injection pipe
Outer diameter - inner diameter - length (mm) mm 6-2-600
Outer diameter - inner diameter - length (mm) mm 6-2-600
Overflow valve opening pressure
kPa
157
123
191
Overflow valve opening pressure
kgf/cm2
1.6
1.25
1.95
Tester oil delivery pressure
kPa
157
157
157
Tester oil delivery pressure
kgf/cm2
1.6
1.6
1.6
Direction of rotation (viewed from drive side)
Right R
Right R
Injection timing adjustment
Direction of rotation (viewed from drive side)
Right R
Right R
Injection order
1-5-3-6-
2-4
Pre-stroke
mm
3.6
3.55
3.65
Beginning of injection position
Drive side NO.1
Drive side NO.1
Difference between angles 1
Cal 1-5 deg. 60 59.5 60.5
Cal 1-5 deg. 60 59.5 60.5
Difference between angles 2
Cal 1-3 deg. 120 119.5 120.5
Cal 1-3 deg. 120 119.5 120.5
Difference between angles 3
Cal 1-6 deg. 180 179.5 180.5
Cal 1-6 deg. 180 179.5 180.5
Difference between angles 4
Cyl.1-2 deg. 240 239.5 240.5
Cyl.1-2 deg. 240 239.5 240.5
Difference between angles 5
Cal 1-4 deg. 300 299.5 300.5
Cal 1-4 deg. 300 299.5 300.5
Injection quantity adjustment
Adjusting point
-
Rack position
11.6
Pump speed
r/min
1000
1000
1000
Average injection quantity
mm3/st.
59.4
57.8
61
Max. variation between cylinders
%
0
-2.5
2.5
Basic
*
Fixing the rack
*
Standard for adjustment of the maximum variation between cylinders
*
Injection quantity adjustment_02
Adjusting point
H
Rack position
9.5+-0.5
Pump speed
r/min
325
325
325
Average injection quantity
mm3/st.
9.3
8
10.6
Max. variation between cylinders
%
0
-14
14
Fixing the rack
*
Standard for adjustment of the maximum variation between cylinders
*
Injection quantity adjustment_03
Adjusting point
A
Rack position
R1(11.6)
Pump speed
r/min
1000
1000
1000
Average injection quantity
mm3/st.
59.4
58.4
60.4
Basic
*
Fixing the lever
*
Injection quantity adjustment_04
Adjusting point
B
Rack position
R1(11.6)
Pump speed
r/min
1600
1600
1600
Average injection quantity
mm3/st.
63.1
59.1
67.1
Fixing the lever
*
Injection quantity adjustment_05
Adjusting point
C
Rack position
R1-0.05
Pump speed
r/min
1300
1300
1300
Average injection quantity
mm3/st.
60.6
57.4
63.8
Fixing the lever
*
Injection quantity adjustment_06
Adjusting point
D
Rack position
R1+0.2
Pump speed
r/min
650
650
650
Average injection quantity
mm3/st.
48.8
45.6
52
Fixing the lever
*
Injection quantity adjustment_07
Adjusting point
I
Rack position
(13.5)+0
.2
Pump speed
r/min
150
150
150
Average injection quantity
mm3/st.
60.5
60.5
65.5
Fixing the lever
*
Rack limit
*
Timer adjustment
Pump speed
r/min
1050--
Advance angle
deg.
0
0
0
Remarks
Start
Start
Timer adjustment_02
Pump speed
r/min
1000
Advance angle
deg.
0.5
Timer adjustment_03
Pump speed
r/min
1300
Advance angle
deg.
1.8
1.3
2.3
Timer adjustment_04
Pump speed
r/min
1600
Advance angle
deg.
4
3.5
4.5
Remarks
Finish
Finish
Test data Ex:
Governor adjustment
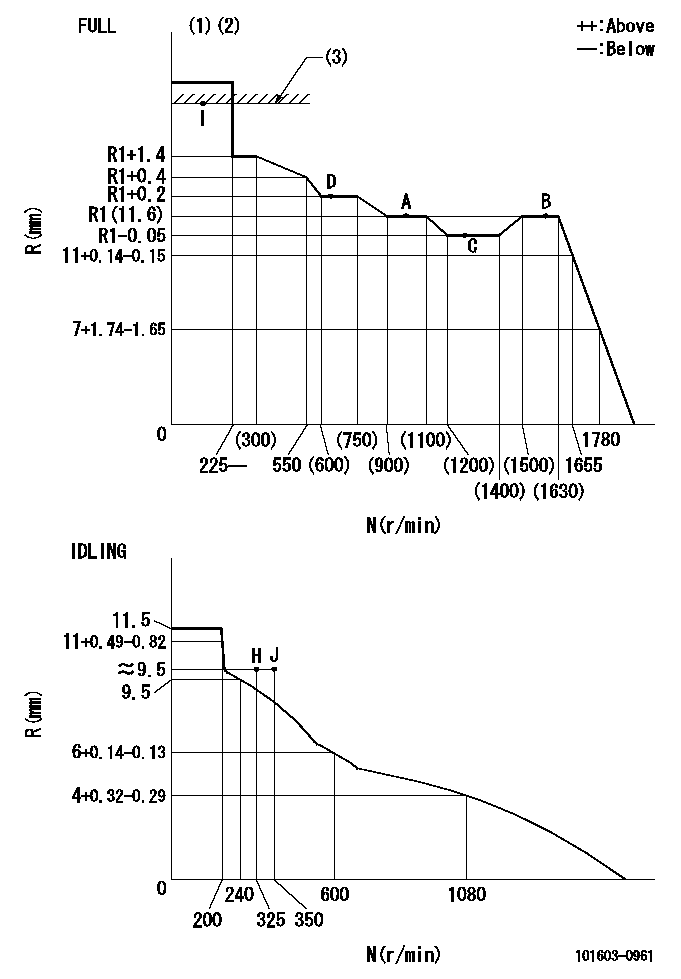
N:Pump speed
R:Rack position (mm)
(1)Torque cam stamping: T1
(2)Tolerance for racks not indicated: +-0.05mm.
(3)RACK LIMIT: RAL
----------
T1=E00 RAL=(13.5)+0.2mm
----------
----------
T1=E00 RAL=(13.5)+0.2mm
----------
Speed control lever angle

F:Full speed
I:Idle
(1)Use the hole at R = aa
(2)Stopper bolt setting
----------
aa=35mm
----------
a=39deg+-5deg b=40deg+-3deg
----------
aa=35mm
----------
a=39deg+-5deg b=40deg+-3deg
Stop lever angle

N:Pump normal
S:Stop the pump.
----------
----------
a=25deg+-5deg b=40deg+-5deg
----------
----------
a=25deg+-5deg b=40deg+-5deg
Timing setting
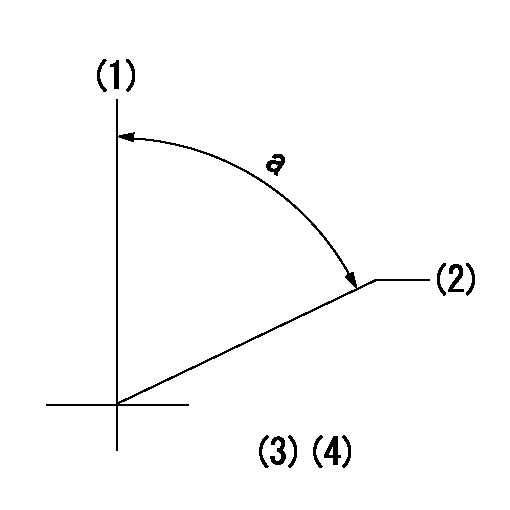
(1)Pump vertical direction
(2)Position of timer's threaded hole at No 1 cylinder's beginning of injection
(3)B.T.D.C.: aa
(4)-
----------
aa=14deg
----------
a=(60deg)
----------
aa=14deg
----------
a=(60deg)
Information:
Starting From External Electrical Source
Always wear protective glasses when working with batteries.Do not allow the free end of booster cables to make contact with each other or touch the engine. This will help prevent sparks near the batteries.Batteries give off flammable fumes that can explode.Do not smoke when observing the battery electrolyte levels.Electrolyte is an acid and can cause personal injury if it contacts skin or eyes.
Be sure the main power switch is in the OFF position before attaching the booster cables to the engine being started. When using booster cables, be sure to connect in parallel: POSITIVE (+) to POSITIVE (+) and NEGATIVE (-) to NEGATIVE (-).Use only equal voltage for boost starting. The use of a welder or higher voltage will damage the electrical system.
Engines without engine-to-frame ground straps can be damaged by electrical discharge.To prevent electrical discharge damage, check to make sure there is an engine-to-frame ground strap. For engines which have the alternator connected to an engine component, the ground strap must connect that component to the frame.Some engines have starter-to-frame ground straps. But, many of these starters are not electrically grounded to the engine. They have electrical insulation systems. For this reason, the starter-to-frame ground strap may not be an acceptable ground.Connect one end of cable to the POSITIVE (+) (ungrounded) terminal of the battery on the engine being started. Connect the other end to the POSITIVE (+) terminal of the power source.Connect one end of the second cable to the NEGATIVE (-) terminal of the power source. Connect the other end to the frame of the engine to be started.Turn the start switch on and start the engine.Disconnect the cable from the frame first. Disconnect the other end from the NEGATIVE (-) terminal of the power source. Disconnect the cable from the POSITIVE (+) terminal of the battery. Disconnect the other end from the POSITIVE (+) terminal of the power source.
Always wear protective glasses when working with batteries.Do not allow the free end of booster cables to make contact with each other or touch the engine. This will help prevent sparks near the batteries.Batteries give off flammable fumes that can explode.Do not smoke when observing the battery electrolyte levels.Electrolyte is an acid and can cause personal injury if it contacts skin or eyes.
Be sure the main power switch is in the OFF position before attaching the booster cables to the engine being started. When using booster cables, be sure to connect in parallel: POSITIVE (+) to POSITIVE (+) and NEGATIVE (-) to NEGATIVE (-).Use only equal voltage for boost starting. The use of a welder or higher voltage will damage the electrical system.
Engines without engine-to-frame ground straps can be damaged by electrical discharge.To prevent electrical discharge damage, check to make sure there is an engine-to-frame ground strap. For engines which have the alternator connected to an engine component, the ground strap must connect that component to the frame.Some engines have starter-to-frame ground straps. But, many of these starters are not electrically grounded to the engine. They have electrical insulation systems. For this reason, the starter-to-frame ground strap may not be an acceptable ground.Connect one end of cable to the POSITIVE (+) (ungrounded) terminal of the battery on the engine being started. Connect the other end to the POSITIVE (+) terminal of the power source.Connect one end of the second cable to the NEGATIVE (-) terminal of the power source. Connect the other end to the frame of the engine to be started.Turn the start switch on and start the engine.Disconnect the cable from the frame first. Disconnect the other end from the NEGATIVE (-) terminal of the power source. Disconnect the cable from the POSITIVE (+) terminal of the battery. Disconnect the other end from the POSITIVE (+) terminal of the power source.