Information injection-pump assembly
ZEXEL
101603-0830
1016030830
ISUZU
1156018710
1156018710
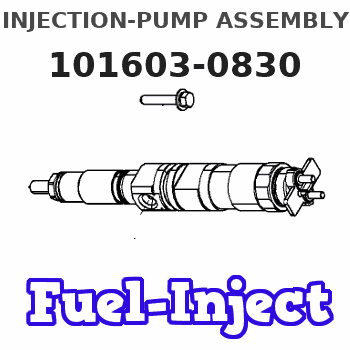
Rating:
Service parts 101603-0830 INJECTION-PUMP ASSEMBLY:
1.
_
7.
COUPLING PLATE
8.
_
9.
_
11.
Nozzle and Holder
12.
Open Pre:MPa(Kqf/cm2)
18.1(185)
15.
NOZZLE SET
Cross reference number
ZEXEL
101603-0830
1016030830
ISUZU
1156018710
1156018710
Zexel num
Bosch num
Firm num
Name
101603-0830
1156018710 ISUZU
INJECTION-PUMP ASSEMBLY
6BD1T * K 14BE PE6A PE
6BD1T * K 14BE PE6A PE
Calibration Data:
Adjustment conditions
Test oil
1404 Test oil ISO4113 or {SAEJ967d}
1404 Test oil ISO4113 or {SAEJ967d}
Test oil temperature
degC
40
40
45
Nozzle and nozzle holder
105780-8140
Bosch type code
EF8511/9A
Nozzle
105780-0000
Bosch type code
DN12SD12T
Nozzle holder
105780-2080
Bosch type code
EF8511/9
Opening pressure
MPa
17.2
Opening pressure
kgf/cm2
175
Injection pipe
Outer diameter - inner diameter - length (mm) mm 6-2-600
Outer diameter - inner diameter - length (mm) mm 6-2-600
Overflow valve opening pressure
kPa
157
123
191
Overflow valve opening pressure
kgf/cm2
1.6
1.25
1.95
Tester oil delivery pressure
kPa
157
157
157
Tester oil delivery pressure
kgf/cm2
1.6
1.6
1.6
Direction of rotation (viewed from drive side)
Right R
Right R
Injection timing adjustment
Direction of rotation (viewed from drive side)
Right R
Right R
Injection order
1-5-3-6-
2-4
Pre-stroke
mm
3.4
3.35
3.45
Rack position
After adjusting injection quantity. R=A
After adjusting injection quantity. R=A
Beginning of injection position
Drive side NO.1
Drive side NO.1
Difference between angles 1
Cal 1-5 deg. 60 59.5 60.5
Cal 1-5 deg. 60 59.5 60.5
Difference between angles 2
Cal 1-3 deg. 120 119.5 120.5
Cal 1-3 deg. 120 119.5 120.5
Difference between angles 3
Cal 1-6 deg. 180 179.5 180.5
Cal 1-6 deg. 180 179.5 180.5
Difference between angles 4
Cyl.1-2 deg. 240 239.5 240.5
Cyl.1-2 deg. 240 239.5 240.5
Difference between angles 5
Cal 1-4 deg. 300 299.5 300.5
Cal 1-4 deg. 300 299.5 300.5
Injection quantity adjustment
Adjusting point
-
Rack position
13.8
Pump speed
r/min
950
950
950
Average injection quantity
mm3/st.
71.4
69.8
73
Max. variation between cylinders
%
0
-2.5
2.5
Basic
*
Fixing the rack
*
Standard for adjustment of the maximum variation between cylinders
*
Injection quantity adjustment_02
Adjusting point
H
Rack position
9.5+-0.5
Pump speed
r/min
275
275
275
Average injection quantity
mm3/st.
10
8.7
11.3
Max. variation between cylinders
%
0
-14
14
Fixing the rack
*
Standard for adjustment of the maximum variation between cylinders
*
Injection quantity adjustment_03
Adjusting point
A
Rack position
R1(13.8)
Pump speed
r/min
950
950
950
Average injection quantity
mm3/st.
71.4
70.4
72.4
Basic
*
Fixing the lever
*
Injection quantity adjustment_04
Adjusting point
B
Rack position
R1-0.2
Pump speed
r/min
1500
1500
1500
Average injection quantity
mm3/st.
77.4
74.2
80.6
Fixing the lever
*
Injection quantity adjustment_05
Adjusting point
C
Rack position
R1-0.15
Pump speed
r/min
1300
1300
1300
Average injection quantity
mm3/st.
75.8
72.6
79
Fixing the lever
*
Injection quantity adjustment_06
Adjusting point
D
Rack position
R1-0.45
Pump speed
r/min
600
600
600
Average injection quantity
mm3/st.
45
41.8
48.2
Fixing the lever
*
Injection quantity adjustment_07
Adjusting point
I
Rack position
15.7+-0.
5
Pump speed
r/min
150
150
150
Average injection quantity
mm3/st.
74
74
79
Fixing the lever
*
Rack limit
*
Timer adjustment
Pump speed
r/min
1050--
Advance angle
deg.
0
0
0
Remarks
Start
Start
Timer adjustment_02
Pump speed
r/min
1000
Advance angle
deg.
0.5
Timer adjustment_03
Pump speed
r/min
1300
Advance angle
deg.
0.9
0.4
1.4
Timer adjustment_04
Pump speed
r/min
1600
Advance angle
deg.
2
1.5
2.5
Remarks
Finish
Finish
Test data Ex:
Governor adjustment
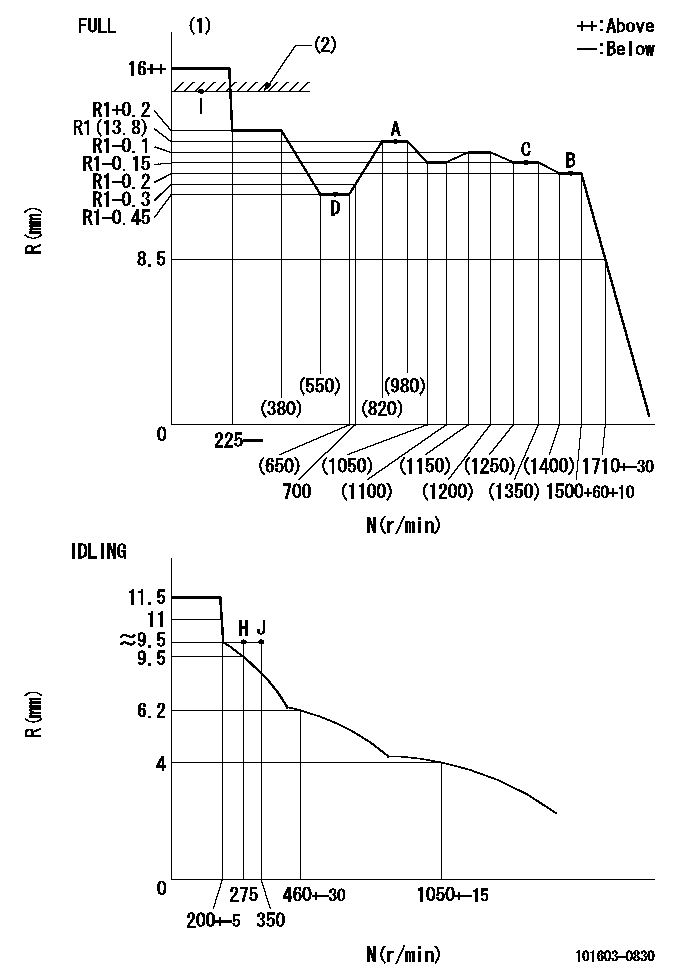
N:Pump speed
R:Rack position (mm)
(1)Torque cam stamping: T1
(2)RACK LIMIT
----------
T1=A31
----------
----------
T1=A31
----------
Speed control lever angle
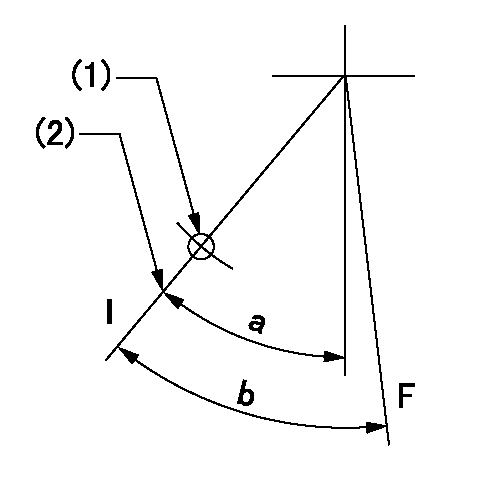
F:Full speed
I:Idle
(1)Use the hole at R = aa
(2)Stopper bolt set position 'H'
----------
aa=35mm
----------
a=34deg+-5deg b=41deg+-3deg
----------
aa=35mm
----------
a=34deg+-5deg b=41deg+-3deg
Stop lever angle

N:Pump normal
S:Stop the pump.
----------
----------
a=25deg+-5deg b=40deg+-5deg
----------
----------
a=25deg+-5deg b=40deg+-5deg
0000001501 ACS
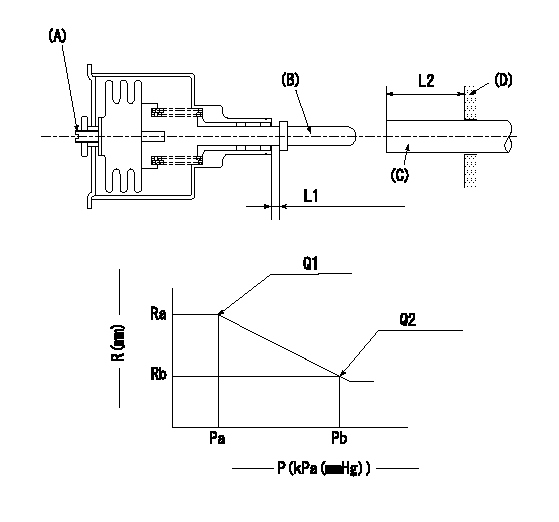
(A) Set screw
(B) Push rod 1
(C) Push rod 2
(D) Cover
1. Aneroid compensator unit adjustment
(1)Select the push rod 2 to obtain L2.
(2)Screw in (A) to obtain L1.
2. Adjustment when mounting the governor.
(1)Set the speed of the pump to N1 r/min and fix the control lever at the full set position.
(2)Screw in the aneroid compensator to obtain the performance shown in the graph above.
(3)As there is hysterisis, measure when the absolute pressure drops.
(4)Hysterisis must not exceed rack position = h1.
----------
N1=950r/min L1=(1.5)mm L2=11+-0.5mm h1=0.15mm
----------
Ra=R1(13.8)mm Rb=R1-0.2mm Pa=89.4+-2.7kPa(674+-20mmHg) Pb=70.1+-0.7kPa(526+-5mmHg) Q1=71.4+-1cm3/1000st Q2=(68)+-1.6cm3/1000st
----------
N1=950r/min L1=(1.5)mm L2=11+-0.5mm h1=0.15mm
----------
Ra=R1(13.8)mm Rb=R1-0.2mm Pa=89.4+-2.7kPa(674+-20mmHg) Pb=70.1+-0.7kPa(526+-5mmHg) Q1=71.4+-1cm3/1000st Q2=(68)+-1.6cm3/1000st
Timing setting
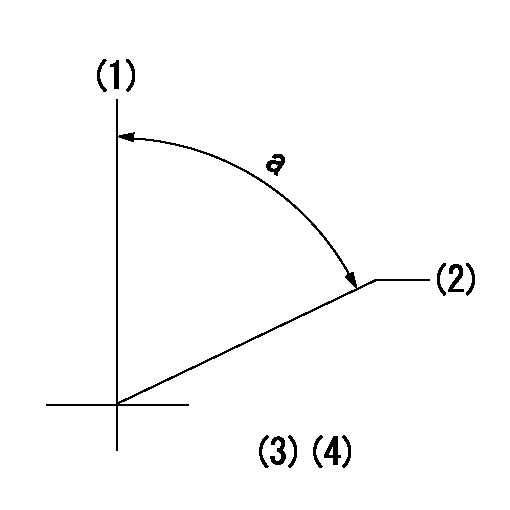
(1)Pump vertical direction
(2)Position of timer's threaded hole at No 1 cylinder's beginning of injection
(3)B.T.D.C.: aa
(4)-
----------
aa=10deg
----------
a=(60deg)
----------
aa=10deg
----------
a=(60deg)
Information:
Safety is everyone's business and is basically the use of good common sense. A general guide of safety precautions are given below, but each installation has its own peculiarities which cannot always be predicted and covered by established rules. Past experience and common sense are needed for the necessary safety measures. Attention to safety will help avoid serious accidents. Be alert. Watch for hazards. Use preventive measures. Correct deficiencies immediately.The following safety precautions are a general guide to safe operation:1. To prevent personal injury, install guards over all exposed rotating parts.2. To prevent hearing damage, wear ear protective devices if working inside an enclosed engine room with engine running.3. To prevent head injury, wear safety hat when working in the area of overhead equipment.4. Wear safety glasses and shoes as required. 5. Do not wear loose clothing whenever working around engines or machinery.6. Wipe up spilled oil, fuel or coolant.7. Keep batteries in a well ventilated area. Do not smoke around batteries. Hydrogen gas, which is present in the area of the batteries, is highly explosive.8. Provide adequate and safe waste oil disposal.9. Store oily rags in fireproof containers. Don't leave rags on engine.
When using pressure air, wear safety glasses and protective clothing. Maximum air pressure, used for cleaning, must be below 30 PSI (2 kg/cm2).
10. Remove all tools, electrical cords and other loose items from the engine before starting.11. Disconnect and tape the battery ground lead before working on an engine to prevent accidental starting. Be sure an automatic start-stop system cannot operate and start the engine while working on it.12. Do not attempt repairs you do not understand. Follow instructions.13. Stop engine before adjusting or repairing engine or driven equipment.14. Remove radiator cap slowly. Cooling systems can be pressurized and hot fluid will flash to steam as pressure is removed.15. Never start an engine with the governor linkage disconnected.16. Replace or repair broken or damaged equipment. Use proper tools.17. Do not smoke while refueling. Observe NO SMOKING signs.18. Never store flammable liquids near the engine.19. All electrical equipment must be grounded according to local building codes.20. Check all connections periodically for tightness and insulation.21. Insulate all connections and disconnected wires.22. Do not use carbon tetrachloride fire extinguishers. Fumes are toxic and the liquid has a deteriorating effect on insulation. 23. Do not touch the heat sink on the generator regulator when the generator is running. It is electrically "hot".24. Do not work on electrically "hot" equipment.25. Always disconnect the engine starter circuit when working on the generator.26. Hot engine oil can cause burns when drained. Allow the oil to cool below 140°F or provide protection when draining the hot oil.27. Never remove a plug to check pressure with the engine running. Shut down the engine and assure there is no pressure before removing plug.28. When starting an engine after repair, make provisions for shutting off air supply in case there is an overspeed on start up.29. Never look into an open cylinder port and turn over
When using pressure air, wear safety glasses and protective clothing. Maximum air pressure, used for cleaning, must be below 30 PSI (2 kg/cm2).
10. Remove all tools, electrical cords and other loose items from the engine before starting.11. Disconnect and tape the battery ground lead before working on an engine to prevent accidental starting. Be sure an automatic start-stop system cannot operate and start the engine while working on it.12. Do not attempt repairs you do not understand. Follow instructions.13. Stop engine before adjusting or repairing engine or driven equipment.14. Remove radiator cap slowly. Cooling systems can be pressurized and hot fluid will flash to steam as pressure is removed.15. Never start an engine with the governor linkage disconnected.16. Replace or repair broken or damaged equipment. Use proper tools.17. Do not smoke while refueling. Observe NO SMOKING signs.18. Never store flammable liquids near the engine.19. All electrical equipment must be grounded according to local building codes.20. Check all connections periodically for tightness and insulation.21. Insulate all connections and disconnected wires.22. Do not use carbon tetrachloride fire extinguishers. Fumes are toxic and the liquid has a deteriorating effect on insulation. 23. Do not touch the heat sink on the generator regulator when the generator is running. It is electrically "hot".24. Do not work on electrically "hot" equipment.25. Always disconnect the engine starter circuit when working on the generator.26. Hot engine oil can cause burns when drained. Allow the oil to cool below 140°F or provide protection when draining the hot oil.27. Never remove a plug to check pressure with the engine running. Shut down the engine and assure there is no pressure before removing plug.28. When starting an engine after repair, make provisions for shutting off air supply in case there is an overspeed on start up.29. Never look into an open cylinder port and turn over
Have questions with 101603-0830?
Group cross 101603-0830 ZEXEL
Isuzu
101603-0830
1156018710
INJECTION-PUMP ASSEMBLY
6BD1T
6BD1T