Information injection-pump assembly
BOSCH
9 400 614 998
9400614998
ZEXEL
101603-0306
1016030306
ISUZU
1156017949
1156017949
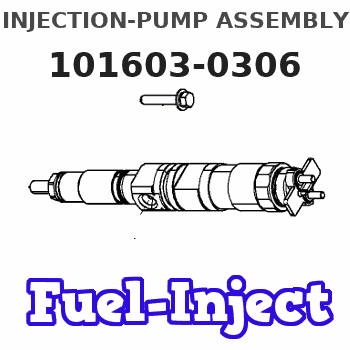
Rating:
Service parts 101603-0306 INJECTION-PUMP ASSEMBLY:
1.
_
7.
COUPLING PLATE
8.
_
9.
_
11.
Nozzle and Holder
1-15300-106-2
12.
Open Pre:MPa(Kqf/cm2)
18.1{185}
15.
NOZZLE SET
Cross reference number
BOSCH
9 400 614 998
9400614998
ZEXEL
101603-0306
1016030306
ISUZU
1156017949
1156017949
Zexel num
Bosch num
Firm num
Name
101603-0306
9 400 614 998
1156017949 ISUZU
INJECTION-PUMP ASSEMBLY
6BG1-TC K 14BF INJECTION PUMP ASSY PE6AD PE
6BG1-TC K 14BF INJECTION PUMP ASSY PE6AD PE
Calibration Data:
Adjustment conditions
Test oil
1404 Test oil ISO4113 or {SAEJ967d}
1404 Test oil ISO4113 or {SAEJ967d}
Test oil temperature
degC
40
40
45
Nozzle and nozzle holder
105780-8140
Bosch type code
EF8511/9A
Nozzle
105780-0000
Bosch type code
DN12SD12T
Nozzle holder
105780-2080
Bosch type code
EF8511/9
Opening pressure
MPa
17.2
Opening pressure
kgf/cm2
175
Injection pipe
Outer diameter - inner diameter - length (mm) mm 6-2-600
Outer diameter - inner diameter - length (mm) mm 6-2-600
Overflow valve opening pressure
kPa
157
123
191
Overflow valve opening pressure
kgf/cm2
1.6
1.25
1.95
Tester oil delivery pressure
kPa
157
157
157
Tester oil delivery pressure
kgf/cm2
1.6
1.6
1.6
Direction of rotation (viewed from drive side)
Right R
Right R
Injection timing adjustment
Direction of rotation (viewed from drive side)
Right R
Right R
Injection order
1-5-3-6-
2-4
Pre-stroke
mm
3.6
3.55
3.65
Beginning of injection position
Drive side NO.1
Drive side NO.1
Difference between angles 1
Cal 1-5 deg. 60 59.5 60.5
Cal 1-5 deg. 60 59.5 60.5
Difference between angles 2
Cal 1-3 deg. 120 119.5 120.5
Cal 1-3 deg. 120 119.5 120.5
Difference between angles 3
Cal 1-6 deg. 180 179.5 180.5
Cal 1-6 deg. 180 179.5 180.5
Difference between angles 4
Cyl.1-2 deg. 240 239.5 240.5
Cyl.1-2 deg. 240 239.5 240.5
Difference between angles 5
Cal 1-4 deg. 300 299.5 300.5
Cal 1-4 deg. 300 299.5 300.5
Injection quantity adjustment
Adjusting point
-
Rack position
14
Pump speed
r/min
850
850
850
Average injection quantity
mm3/st.
100.8
99.2
102.4
Max. variation between cylinders
%
0
-2.5
2.5
Basic
*
Fixing the rack
*
Standard for adjustment of the maximum variation between cylinders
*
Injection quantity adjustment_02
Adjusting point
-
Rack position
9.7+-0.5
Pump speed
r/min
275
275
275
Average injection quantity
mm3/st.
9.4
8.1
10.7
Max. variation between cylinders
%
0
-14
14
Fixing the rack
*
Standard for adjustment of the maximum variation between cylinders
*
Remarks
Adjust only variation between cylinders; adjust governor according to governor specifications.
Adjust only variation between cylinders; adjust governor according to governor specifications.
Injection quantity adjustment_03
Adjusting point
A
Rack position
R1(14)
Pump speed
r/min
850
850
850
Average injection quantity
mm3/st.
100.8
99.8
101.8
Basic
*
Fixing the lever
*
Boost pressure
kPa
24
24
Boost pressure
mmHg
180
180
Injection quantity adjustment_04
Adjusting point
B
Rack position
R1-0.65
Pump speed
r/min
1400
1400
1400
Average injection quantity
mm3/st.
93.5
90.3
96.7
Fixing the lever
*
Boost pressure
kPa
24
24
Boost pressure
mmHg
180
180
Injection quantity adjustment_05
Adjusting point
C
Rack position
R2(R1-0.
3)
Pump speed
r/min
550
550
550
Average injection quantity
mm3/st.
88.8
85.6
92
Fixing the lever
*
Boost pressure
kPa
24
24
Boost pressure
mmHg
180
180
Injection quantity adjustment_06
Adjusting point
D
Rack position
R2-1.4
Pump speed
r/min
550
550
550
Average injection quantity
mm3/st.
53.6
50.4
56.8
Fixing the lever
*
Boost pressure
kPa
0
0
0
Boost pressure
mmHg
0
0
0
Injection quantity adjustment_07
Adjusting point
I
Rack position
-
Pump speed
r/min
150
150
150
Average injection quantity
mm3/st.
92
92
100
Fixing the lever
*
Rack limit
*
Boost compensator adjustment
Pump speed
r/min
550
550
550
Rack position
R2-1.4
Boost pressure
kPa
2
2
4.7
Boost pressure
mmHg
15
15
35
Boost compensator adjustment_02
Pump speed
r/min
550
550
550
Rack position
R2-0.85
Boost pressure
kPa
4.7
4.7
7.4
Boost pressure
mmHg
35
35
55
Boost compensator adjustment_03
Pump speed
r/min
550
550
550
Rack position
R2(R1-0.
3)
Boost pressure
kPa
10.7
10.7
10.7
Boost pressure
mmHg
80
80
80
Timer adjustment
Pump speed
r/min
1325--
Advance angle
deg.
0
0
0
Remarks
Start
Start
Timer adjustment_02
Pump speed
r/min
1275
Advance angle
deg.
0.5
Timer adjustment_03
Pump speed
r/min
1400
Advance angle
deg.
1
0.5
1.5
Remarks
Finish
Finish
Test data Ex:
Governor adjustment
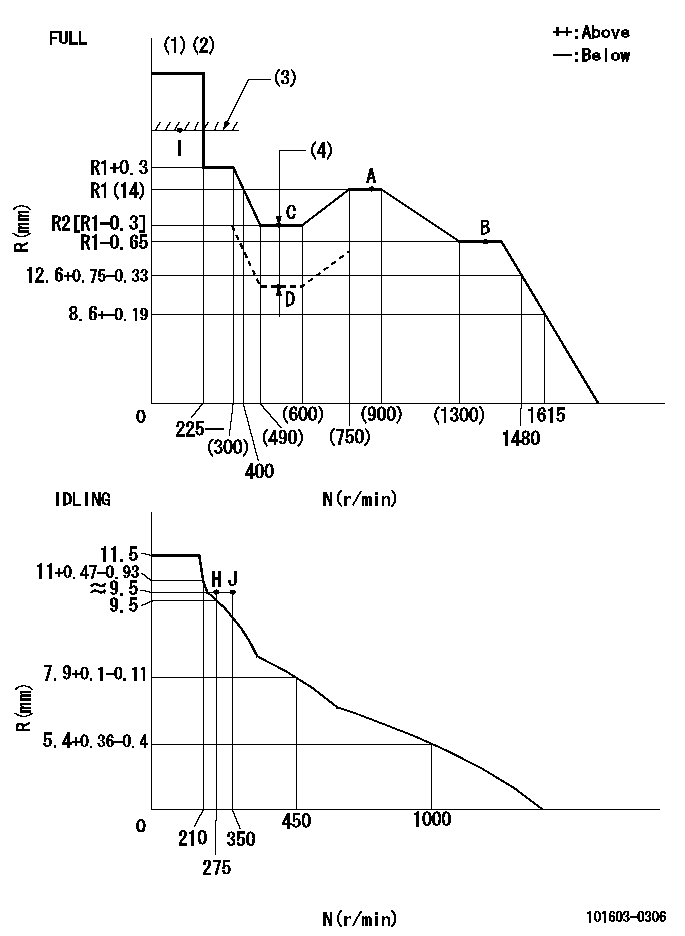
N:Pump speed
R:Rack position (mm)
(1)Torque cam stamping: T1
(2)Tolerance for racks not indicated: +-0.05mm.
(3)RACK LIMIT
(4)Boost compensator stroke: BCL
----------
T1=E67 BCL=1.4+-0.1mm
----------
----------
T1=E67 BCL=1.4+-0.1mm
----------
Speed control lever angle

F:Full speed
I:Idle
(1)Use the hole at R = aa
(2)Stopper bolt set position 'H'
----------
aa=35mm
----------
a=43deg+-5deg b=41.5deg+-3deg
----------
aa=35mm
----------
a=43deg+-5deg b=41.5deg+-3deg
Stop lever angle

N:Pump normal
S:Stop the pump.
----------
----------
a=25deg+-5deg b=40deg+-5deg
----------
----------
a=25deg+-5deg b=40deg+-5deg
Timing setting
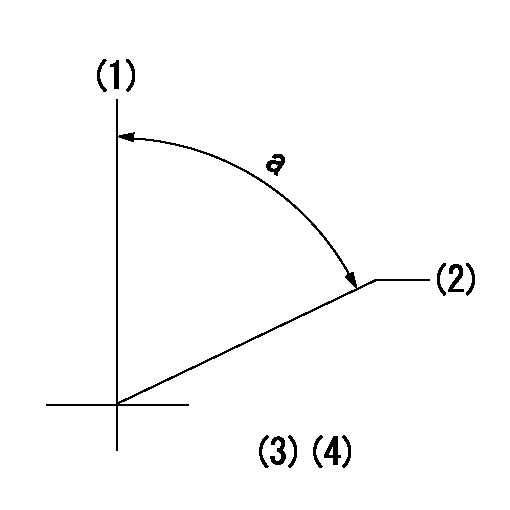
(1)Pump vertical direction
(2)Position of timer's threaded hole at No 1 cylinder's beginning of injection
(3)B.T.D.C.: aa
(4)-
----------
aa=13deg
----------
a=(60deg)
----------
aa=13deg
----------
a=(60deg)
Information:
The information supplied in this service letter may not be valid after the termination date of this program. Do not perform the work outlined in this Service Letter after the termination date without first contacting your Caterpillar product analyst.
This Program can only be administered after a failure occurs. The decision whether to apply the Program is made by the dealer. When reporting the repair, use "PS0904" as the Part Number and "7755" as the Group Number. Use "96" as the Warranty Claim Description Code and use "Z" as the SIMS Description Code.
This Revised Service Letter replaces the February 4, 1996 Service Letter. Changes have been made to the Problem, Affected Product, Parts Needed, Action Required, and Service Claim Allowances.
Termination Date
February 28, 1998Problem
Fuel injector tips may fail on certain 3176 and 3176B Truck Engines and Challenger 75 and 85 Tractors.
Affected Product
Model & Identification Number
3176 (7LG7500-Up)
3176B (9CK1-9353)
CH75C (4KK500-840)
CH85C (9TK1-1407)
Parts Needed
Reference the Rework Procedure to determine the quantity of parts to be replaced.
3176 (7LG) Parts
Up to 6 - 0R4523 Injector [7LG7500 - Up (325, 350 and 360 HP)]Up to 6 - 0R4525 Injector Gp [7LG7500 - Up (275 and 300 HP)]Up to 6 - 9X7317 Seal-O-Ring (injector tip o-ring)Up to 6 - 9X7557 Seal-O-Ring (injector upper o-ring)Up to 6 - 9X7722 Seal-O-Ring (injector lower o-ring) 3176B (9CK) Parts
Up to 6 - 0R4526 Injector Gp [9CK (275 HP)]Up to 6 - 0R4527 Injector Gp [9CK (300 and 325 HP)]Up to 6 - 0R4528 Injector Gp [9CK (342, 350, 365 and 335/365MT HP)]Up to 6 - 9X7317 Seal-O-Ring (injector tip o-ring)Up to 6 - 9X7557 Seal-O-Ring (injector upper o-ring)Up to 6 - 9X7722 Seal-O-Ring (injector lower o-ring) CH75C/85C (4KK and 9TK) Parts
Up to 6 - 0R4520 Injector GpUp to 6 - 9X7317 Seal-O-Ring (injector tip o-ring)Up to 6 - 9X7557 Seal-O-Ring (injector upper o-ring)Up to 6 - 9X7722 Seal-O-Ring (injector lower o-ring) Additional parts may be needed with contingent damage to engine such as cylinder head, cylinder pack, turbocharger, etc..
Action Required
1. Inspect the failed injector for a cracked or broken tip. If the tip is not cracked or broken, this program does not apply. Refer to the attached rework procedure.2. Replace the fuel injectors according to the attached rework procedure and repair any additional damage caused by the cracked tip.Service Claim Allowances (Truck Engines)
Service Claim Allowances (Tractors)
Parts Disposition
Handle the parts in accordance with your Warranty Bulletin on warranty parts handling.
Attach.(1-Rework Procedure)Rework Procedure
1. Remove the necessary air piping, air cleaners, valve covers, Jake Brakes, and rocker arm assemblies. Remove the lower plug at the rear of the fuel manifold and drain the fuel from the cylinder head and manifold. Reinstall the plug.2. Diagnose the problem to the specific injector. Inspect the failed injector for a cracked or broken tip. If the tip is not cracked or broken, this program does not apply.3. Determine if the other injectors should or should not be replaced. Remove the other injectors and check the date code stamped on the nozzle cone. 4. If a portion of the
This Program can only be administered after a failure occurs. The decision whether to apply the Program is made by the dealer. When reporting the repair, use "PS0904" as the Part Number and "7755" as the Group Number. Use "96" as the Warranty Claim Description Code and use "Z" as the SIMS Description Code.
This Revised Service Letter replaces the February 4, 1996 Service Letter. Changes have been made to the Problem, Affected Product, Parts Needed, Action Required, and Service Claim Allowances.
Termination Date
February 28, 1998Problem
Fuel injector tips may fail on certain 3176 and 3176B Truck Engines and Challenger 75 and 85 Tractors.
Affected Product
Model & Identification Number
3176 (7LG7500-Up)
3176B (9CK1-9353)
CH75C (4KK500-840)
CH85C (9TK1-1407)
Parts Needed
Reference the Rework Procedure to determine the quantity of parts to be replaced.
3176 (7LG) Parts
Up to 6 - 0R4523 Injector [7LG7500 - Up (325, 350 and 360 HP)]Up to 6 - 0R4525 Injector Gp [7LG7500 - Up (275 and 300 HP)]Up to 6 - 9X7317 Seal-O-Ring (injector tip o-ring)Up to 6 - 9X7557 Seal-O-Ring (injector upper o-ring)Up to 6 - 9X7722 Seal-O-Ring (injector lower o-ring) 3176B (9CK) Parts
Up to 6 - 0R4526 Injector Gp [9CK (275 HP)]Up to 6 - 0R4527 Injector Gp [9CK (300 and 325 HP)]Up to 6 - 0R4528 Injector Gp [9CK (342, 350, 365 and 335/365MT HP)]Up to 6 - 9X7317 Seal-O-Ring (injector tip o-ring)Up to 6 - 9X7557 Seal-O-Ring (injector upper o-ring)Up to 6 - 9X7722 Seal-O-Ring (injector lower o-ring) CH75C/85C (4KK and 9TK) Parts
Up to 6 - 0R4520 Injector GpUp to 6 - 9X7317 Seal-O-Ring (injector tip o-ring)Up to 6 - 9X7557 Seal-O-Ring (injector upper o-ring)Up to 6 - 9X7722 Seal-O-Ring (injector lower o-ring) Additional parts may be needed with contingent damage to engine such as cylinder head, cylinder pack, turbocharger, etc..
Action Required
1. Inspect the failed injector for a cracked or broken tip. If the tip is not cracked or broken, this program does not apply. Refer to the attached rework procedure.2. Replace the fuel injectors according to the attached rework procedure and repair any additional damage caused by the cracked tip.Service Claim Allowances (Truck Engines)
Service Claim Allowances (Tractors)
Parts Disposition
Handle the parts in accordance with your Warranty Bulletin on warranty parts handling.
Attach.(1-Rework Procedure)Rework Procedure
1. Remove the necessary air piping, air cleaners, valve covers, Jake Brakes, and rocker arm assemblies. Remove the lower plug at the rear of the fuel manifold and drain the fuel from the cylinder head and manifold. Reinstall the plug.2. Diagnose the problem to the specific injector. Inspect the failed injector for a cracked or broken tip. If the tip is not cracked or broken, this program does not apply.3. Determine if the other injectors should or should not be replaced. Remove the other injectors and check the date code stamped on the nozzle cone. 4. If a portion of the
Have questions with 101603-0306?
Group cross 101603-0306 ZEXEL
Isuzu
101603-0306
9 400 614 998
1156017949
INJECTION-PUMP ASSEMBLY
6BG1-TC
6BG1-TC