Information injection-pump assembly
ZEXEL
101603-0161
1016030161
ISUZU
1156015953
1156015953
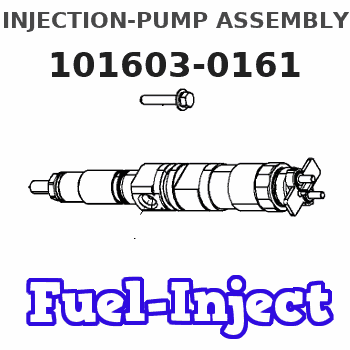
Rating:
Service parts 101603-0161 INJECTION-PUMP ASSEMBLY:
1.
_
7.
COUPLING PLATE
8.
_
9.
_
11.
Nozzle and Holder
5-15300-089-1
12.
Open Pre:MPa(Kqf/cm2)
18.1{185}
15.
NOZZLE SET
Cross reference number
ZEXEL
101603-0161
1016030161
ISUZU
1156015953
1156015953
Zexel num
Bosch num
Firm num
Name
Calibration Data:
Adjustment conditions
Test oil
1404 Test oil ISO4113 or {SAEJ967d}
1404 Test oil ISO4113 or {SAEJ967d}
Test oil temperature
degC
40
40
45
Nozzle and nozzle holder
105780-8140
Bosch type code
EF8511/9A
Nozzle
105780-0000
Bosch type code
DN12SD12T
Nozzle holder
105780-2080
Bosch type code
EF8511/9
Opening pressure
MPa
17.2
Opening pressure
kgf/cm2
175
Injection pipe
Outer diameter - inner diameter - length (mm) mm 6-2-600
Outer diameter - inner diameter - length (mm) mm 6-2-600
Overflow valve opening pressure
kPa
157
123
191
Overflow valve opening pressure
kgf/cm2
1.6
1.25
1.95
Tester oil delivery pressure
kPa
157
157
157
Tester oil delivery pressure
kgf/cm2
1.6
1.6
1.6
Direction of rotation (viewed from drive side)
Right R
Right R
Injection timing adjustment
Direction of rotation (viewed from drive side)
Right R
Right R
Injection order
1-5-3-6-
2-4
Pre-stroke
mm
3.6
3.55
3.65
Beginning of injection position
Drive side NO.1
Drive side NO.1
Difference between angles 1
Cal 1-5 deg. 60 59.5 60.5
Cal 1-5 deg. 60 59.5 60.5
Difference between angles 2
Cal 1-3 deg. 120 119.5 120.5
Cal 1-3 deg. 120 119.5 120.5
Difference between angles 3
Cal 1-6 deg. 180 179.5 180.5
Cal 1-6 deg. 180 179.5 180.5
Difference between angles 4
Cyl.1-2 deg. 240 239.5 240.5
Cyl.1-2 deg. 240 239.5 240.5
Difference between angles 5
Cal 1-4 deg. 300 299.5 300.5
Cal 1-4 deg. 300 299.5 300.5
Injection quantity adjustment
Adjusting point
-
Rack position
11.6
Pump speed
r/min
1000
1000
1000
Average injection quantity
mm3/st.
60
58.4
61.6
Max. variation between cylinders
%
0
-2.5
2.5
Basic
*
Fixing the rack
*
Standard for adjustment of the maximum variation between cylinders
*
Injection quantity adjustment_02
Adjusting point
H
Rack position
9.5+-0.5
Pump speed
r/min
325
325
325
Average injection quantity
mm3/st.
9.3
8
10.6
Max. variation between cylinders
%
0
-14
14
Fixing the rack
*
Standard for adjustment of the maximum variation between cylinders
*
Injection quantity adjustment_03
Adjusting point
A
Rack position
R1(11.6)
Pump speed
r/min
1000
1000
1000
Average injection quantity
mm3/st.
60
59
61
Basic
*
Fixing the lever
*
Injection quantity adjustment_04
Adjusting point
B
Rack position
R1+0.15
Pump speed
r/min
1600
1600
1600
Average injection quantity
mm3/st.
66.5
62.5
70.5
Fixing the lever
*
Injection quantity adjustment_05
Adjusting point
C
Rack position
R1(11.6)
Pump speed
r/min
1300
1300
1300
Average injection quantity
mm3/st.
62.1
58.9
65.3
Fixing the lever
*
Injection quantity adjustment_06
Adjusting point
D
Rack position
R1+0.1
Pump speed
r/min
650
650
650
Average injection quantity
mm3/st.
47.5
44.3
50.7
Fixing the lever
*
Injection quantity adjustment_07
Adjusting point
I
Rack position
(14.5)+0
.2
Pump speed
r/min
150
150
150
Average injection quantity
mm3/st.
80
80
85
Fixing the lever
*
Rack limit
*
Timer adjustment
Pump speed
r/min
1050--
Advance angle
deg.
0
0
0
Remarks
Start
Start
Timer adjustment_02
Pump speed
r/min
1000
Advance angle
deg.
0.5
Timer adjustment_03
Pump speed
r/min
1300
Advance angle
deg.
1.8
1.3
2.3
Timer adjustment_04
Pump speed
r/min
1600
Advance angle
deg.
4
3.5
4.5
Remarks
Finish
Finish
Test data Ex:
Governor adjustment
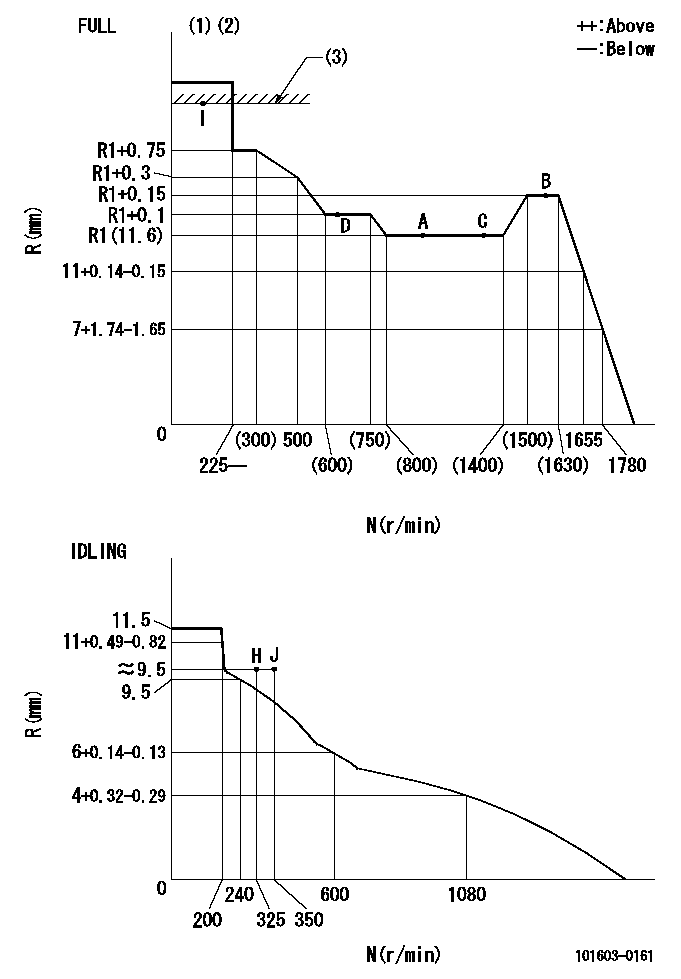
N:Pump speed
R:Rack position (mm)
(1)Torque cam stamping: T1
(2)Tolerance for racks not indicated: +-0.05mm.
(3)RACK LIMIT: RAL
----------
T1=D99 RAL=(14.5)+0.2mm
----------
----------
T1=D99 RAL=(14.5)+0.2mm
----------
Speed control lever angle

F:Full speed
I:Idle
(1)Use the hole at R = aa
(2)Stopper bolt setting
----------
aa=45mm
----------
a=19.5deg+-5deg b=40deg+-3deg
----------
aa=45mm
----------
a=19.5deg+-5deg b=40deg+-3deg
Stop lever angle

N:Pump normal
S:Stop the pump.
----------
----------
a=25deg+-5deg b=40deg+-5deg
----------
----------
a=25deg+-5deg b=40deg+-5deg
0000001501 ACS
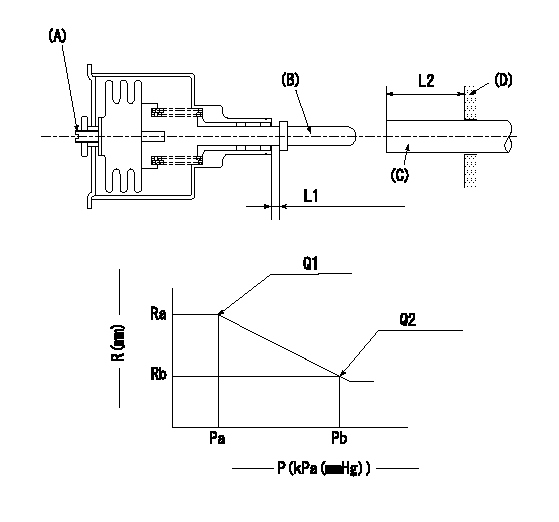
(A) Set screw
(B) Push rod 1
(C) Push rod 2
(D) Cover
1. Aneroid compensator unit adjustment
(1)Select the push rod 2 to obtain L2.
(2)Screw in (A) to obtain L1.
2. Adjustment when mounting the governor.
(1)Set the speed of the pump to N1 r/min and fix the control lever at the full set position.
(2)Screw in the aneroid compensator to obtain the performance shown in the graph above.
(3)As there is hysterisis, measure when the absolute pressure drops.
(4)Hysterisis must not exceed rack position = h1.
----------
N1=1000r/min L1=(1.5)mm L2=11+-0.5mm h1=0.15mm
----------
Ra=R1(11.6)mm Rb=R3(10.7)mm Pa=89.8+-2.7kPa(674+-20mmHg) Pb=70.1+-0.7kPa(526+-5mmHg) Q1=60+-1cm3/1000st Q2=40.6+-1.6cm3/1000st
----------
N1=1000r/min L1=(1.5)mm L2=11+-0.5mm h1=0.15mm
----------
Ra=R1(11.6)mm Rb=R3(10.7)mm Pa=89.8+-2.7kPa(674+-20mmHg) Pb=70.1+-0.7kPa(526+-5mmHg) Q1=60+-1cm3/1000st Q2=40.6+-1.6cm3/1000st
Timing setting
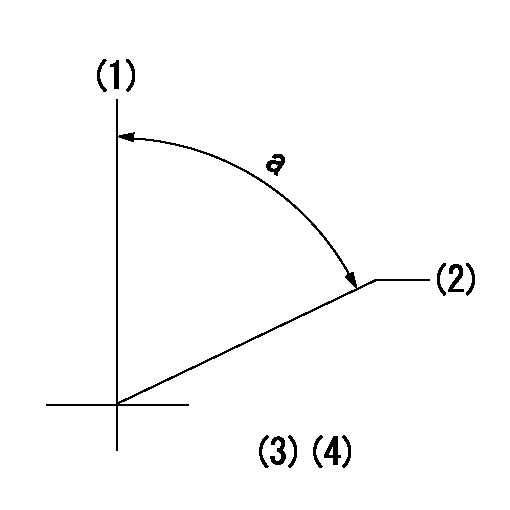
(1)Pump vertical direction
(2)Position of timer's threaded hole at No 1 cylinder's beginning of injection
(3)B.T.D.C.: aa
(4)-
----------
aa=14deg
----------
a=(60deg)
----------
aa=14deg
----------
a=(60deg)
Information:
Caterpillar: Confidential Yellow
PSP FOR ADDING HOLDDOWN BRACKET AND PLATE TO FUEL INJECTION LINES ON CERTAIN CHALLENGER 65 TRACTORS - MAILED US AND CANADA, LI MITED CACO, LIMITED COFA
  The information supplied in this service letter may not be valid after the termination date of this program.   Do not perform the work outlined in this Service Letter after the termination date without first contacting your Caterpillar product analyst.
U-159 A-73.1 AU-98.1 1252 PS4250 This Program can be administered either before or after a failure. In either case the decision whether to apply the Program is made by the dealer. When reporting the repair, use "PS4250" as Part Number and "7755" as Group Number. Termination Date
October 31, 1989
Problem
The No. 1, No. 2, and No. 3 fuel injection lines may crack at the injector end of the lines due to vibration from injection pulses or engine combustion. A clamping plate and a hold-down bracket can be installed to the lines to reduce vibration.
Affected Product
Model Identification Number CH65 7YC1 - 824, 828-831, 835, 836, 841, 849, 851
Parts Needed
3 - 4B4274 Washer 3 - 1W9169 Clamp 3 - 9N3388 Screw 1 - 9Y7523 Bracket 3 - 1W9167 Clamp As. 1 - 9Y7524 Plate
Action Required
Install the parts needed as shown in Illustrations 1 and 2.
Service Claim Allowances
Product Caterpillar Dealer Suggested Customer Suggested smu/age Parts Labor Hrs. Parts Labor Hrs. Parts Labor Hrs. whichever (D/N) (Cost) (C/L) (Sell) comes first 0-2000 100% 1 0 0 0 0 0-24 mo 2001-4000 33 1/3% .5 0 .5 0 0 25-36 mo This is a 1-hour job.
Parts Disposition
Not applicable ****** IMAGE: SEBE3893.00001.001 CAPTION: Illustration 1. Top View Of Installation ****** IMAGE: SEBE3893.00001.002 CAPTION: Illustration 2. Side View Of Installation
PSP FOR ADDING HOLDDOWN BRACKET AND PLATE TO FUEL INJECTION LINES ON CERTAIN CHALLENGER 65 TRACTORS - MAILED US AND CANADA, LI MITED CACO, LIMITED COFA
  The information supplied in this service letter may not be valid after the termination date of this program.   Do not perform the work outlined in this Service Letter after the termination date without first contacting your Caterpillar product analyst.
U-159 A-73.1 AU-98.1 1252 PS4250 This Program can be administered either before or after a failure. In either case the decision whether to apply the Program is made by the dealer. When reporting the repair, use "PS4250" as Part Number and "7755" as Group Number. Termination Date
October 31, 1989
Problem
The No. 1, No. 2, and No. 3 fuel injection lines may crack at the injector end of the lines due to vibration from injection pulses or engine combustion. A clamping plate and a hold-down bracket can be installed to the lines to reduce vibration.
Affected Product
Model Identification Number CH65 7YC1 - 824, 828-831, 835, 836, 841, 849, 851
Parts Needed
3 - 4B4274 Washer 3 - 1W9169 Clamp 3 - 9N3388 Screw 1 - 9Y7523 Bracket 3 - 1W9167 Clamp As. 1 - 9Y7524 Plate
Action Required
Install the parts needed as shown in Illustrations 1 and 2.
Service Claim Allowances
Product Caterpillar Dealer Suggested Customer Suggested smu/age Parts Labor Hrs. Parts Labor Hrs. Parts Labor Hrs. whichever (D/N) (Cost) (C/L) (Sell) comes first 0-2000 100% 1 0 0 0 0 0-24 mo 2001-4000 33 1/3% .5 0 .5 0 0 25-36 mo This is a 1-hour job.
Parts Disposition
Not applicable ****** IMAGE: SEBE3893.00001.001 CAPTION: Illustration 1. Top View Of Installation ****** IMAGE: SEBE3893.00001.002 CAPTION: Illustration 2. Side View Of Installation