Information injection-pump assembly
ZEXEL
101603-0090
1016030090
ISUZU
1156015022
1156015022
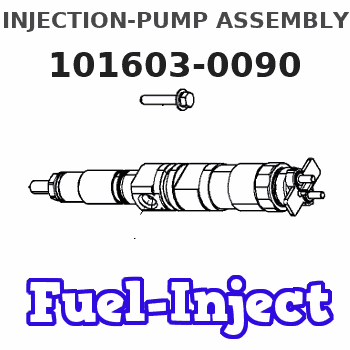
Rating:
Service parts 101603-0090 INJECTION-PUMP ASSEMBLY:
1.
_
7.
COUPLING PLATE
8.
_
9.
_
11.
Nozzle and Holder
12.
Open Pre:MPa(Kqf/cm2)
18.1(185)
15.
NOZZLE SET
Cross reference number
ZEXEL
101603-0090
1016030090
ISUZU
1156015022
1156015022
Zexel num
Bosch num
Firm num
Name
101603-0090
1156015022 ISUZU
INJECTION-PUMP ASSEMBLY
6BB1 * K
6BB1 * K
Calibration Data:
Adjustment conditions
Test oil
1404 Test oil ISO4113 or {SAEJ967d}
1404 Test oil ISO4113 or {SAEJ967d}
Test oil temperature
degC
40
40
45
Nozzle and nozzle holder
105780-8140
Bosch type code
EF8511/9A
Nozzle
105780-0000
Bosch type code
DN12SD12T
Nozzle holder
105780-2080
Bosch type code
EF8511/9
Opening pressure
MPa
17.2
Opening pressure
kgf/cm2
175
Injection pipe
Outer diameter - inner diameter - length (mm) mm 6-2-600
Outer diameter - inner diameter - length (mm) mm 6-2-600
Overflow valve
132424-0620
Overflow valve opening pressure
kPa
157
123
191
Overflow valve opening pressure
kgf/cm2
1.6
1.25
1.95
Tester oil delivery pressure
kPa
157
157
157
Tester oil delivery pressure
kgf/cm2
1.6
1.6
1.6
Direction of rotation (viewed from drive side)
Right R
Right R
Injection timing adjustment
Direction of rotation (viewed from drive side)
Right R
Right R
Injection order
1-5-3-6-
2-4
Pre-stroke
mm
3.6
3.55
3.65
Beginning of injection position
Drive side NO.1
Drive side NO.1
Difference between angles 1
Cal 1-5 deg. 60 59.5 60.5
Cal 1-5 deg. 60 59.5 60.5
Difference between angles 2
Cal 1-3 deg. 120 119.5 120.5
Cal 1-3 deg. 120 119.5 120.5
Difference between angles 3
Cal 1-6 deg. 180 179.5 180.5
Cal 1-6 deg. 180 179.5 180.5
Difference between angles 4
Cyl.1-2 deg. 240 239.5 240.5
Cyl.1-2 deg. 240 239.5 240.5
Difference between angles 5
Cal 1-4 deg. 300 299.5 300.5
Cal 1-4 deg. 300 299.5 300.5
Injection quantity adjustment
Adjusting point
-
Rack position
10.8
Pump speed
r/min
950
950
950
Average injection quantity
mm3/st.
61.4
59.8
63
Max. variation between cylinders
%
0
-2.5
2.5
Basic
*
Fixing the rack
*
Standard for adjustment of the maximum variation between cylinders
*
Injection quantity adjustment_02
Adjusting point
H
Rack position
9.5+-0.5
Pump speed
r/min
275
275
275
Average injection quantity
mm3/st.
7.4
6.1
8.7
Max. variation between cylinders
%
0
-14
14
Fixing the rack
*
Standard for adjustment of the maximum variation between cylinders
*
Injection quantity adjustment_03
Adjusting point
A
Rack position
R1(10.8)
Pump speed
r/min
950
950
950
Average injection quantity
mm3/st.
61.4
60.4
62.4
Basic
*
Fixing the lever
*
Injection quantity adjustment_04
Adjusting point
B
Rack position
R1+0.2
Pump speed
r/min
1600
1600
1600
Average injection quantity
mm3/st.
71
69.4
72.6
Fixing the lever
*
Injection quantity adjustment_05
Adjusting point
C
Rack position
R1-0.05
Pump speed
r/min
1300
1300
1300
Average injection quantity
mm3/st.
66
64.4
67.6
Fixing the lever
*
Injection quantity adjustment_06
Adjusting point
D
Rack position
R1-0.2
Pump speed
r/min
650
650
650
Average injection quantity
mm3/st.
45.7
44.1
47.3
Fixing the lever
*
Injection quantity adjustment_07
Adjusting point
I
Rack position
13.6+-0.
5
Pump speed
r/min
150
150
150
Average injection quantity
mm3/st.
87
87
95
Fixing the lever
*
Rack limit
*
Timer adjustment
Pump speed
r/min
1400--
Advance angle
deg.
0
0
0
Remarks
Start
Start
Timer adjustment_02
Pump speed
r/min
1350
Advance angle
deg.
0.5
Timer adjustment_03
Pump speed
r/min
1400
Advance angle
deg.
1.3
Timer adjustment_04
Pump speed
r/min
1500
Advance angle
deg.
2.3
1.8
2.8
Timer adjustment_05
Pump speed
r/min
1600
Advance angle
deg.
4
3.5
4.5
Remarks
Finish
Finish
Test data Ex:
Governor adjustment
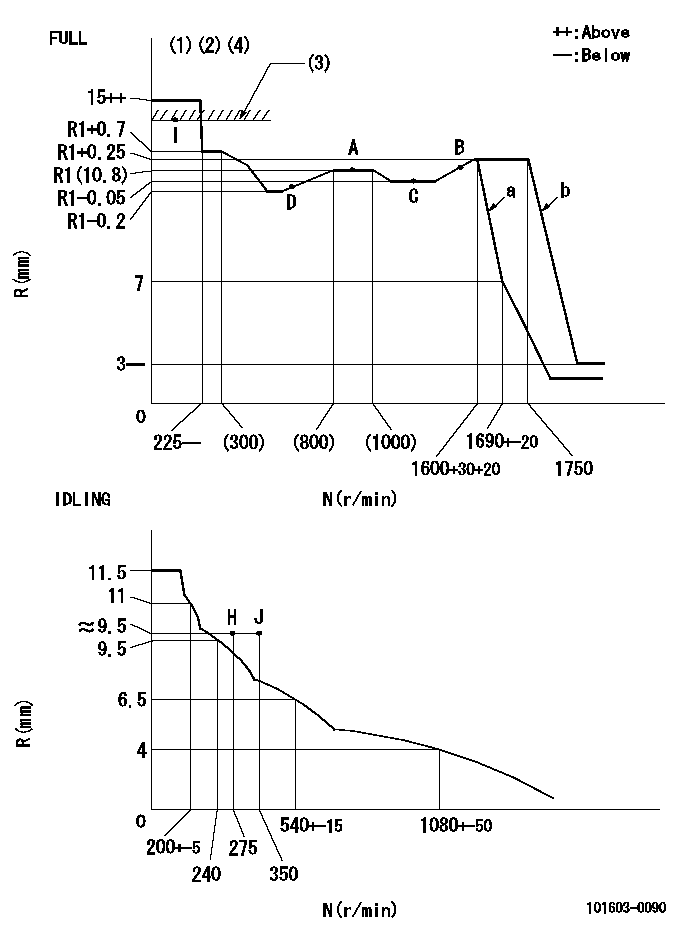
N:Pump speed
R:Rack position (mm)
(1)Torque cam stamping: T1
(2)Torque control stroke: L2
(3)RACK LIMIT
(4)Perform speed droop adjustment using the torque control spring in accordance with specification 'a' and confirm specification 'b.' Set the final full speed position lever in accordance with specification 'a.'
----------
T1=27 L2=(1.1)+-0.05mm
----------
----------
T1=27 L2=(1.1)+-0.05mm
----------
Speed control lever angle

F:Full speed
I:Idle
(1)Stopper bolt set position 'H'
----------
----------
a=42deg+-5deg b=37deg+-3deg
----------
----------
a=42deg+-5deg b=37deg+-3deg
Stop lever angle

N:Pump normal
S:Stop the pump.
----------
----------
a=25deg+-5deg b=40deg+-5deg
----------
----------
a=25deg+-5deg b=40deg+-5deg
0000001501 ACS
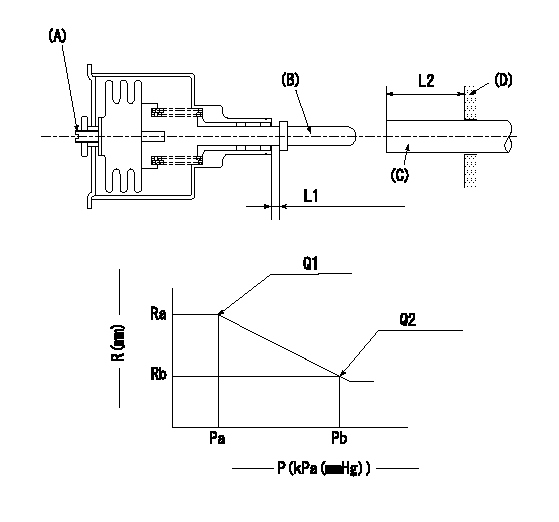
(A) Set screw
(B) Push rod 1
(C) Push rod 2
(D) Cover
1. Aneroid compensator unit adjustment
(1)Select the push rod 2 to obtain L2.
(2)Screw in (A) to obtain L1.
2. Adjustment when mounting the governor.
(1)Set the speed of the pump to N1 r/min and fix the control lever at the full set position.
(2)Screw in the aneroid compensator to obtain the performance shown in the graph above.
(3)As there is hysterisis, measure when the absolute pressure drops.
(4)Hysterisis must not exceed rack position = h1.
----------
N1=950r/min L1=(1.5) mm L2=11+-0.5mm h1=0.15
----------
Ra=R1(10.8)mm Rb=R1-0.7mm Pa=89.8+-2.7kPa(674+-20mmHg) Pb=70.1+-0.7kPa(526+-5 mmHg) Q1=61.4+-1cm3/1000st Q2=(48.8)+-1.6cm3/1000st
----------
N1=950r/min L1=(1.5) mm L2=11+-0.5mm h1=0.15
----------
Ra=R1(10.8)mm Rb=R1-0.7mm Pa=89.8+-2.7kPa(674+-20mmHg) Pb=70.1+-0.7kPa(526+-5 mmHg) Q1=61.4+-1cm3/1000st Q2=(48.8)+-1.6cm3/1000st
Timing setting
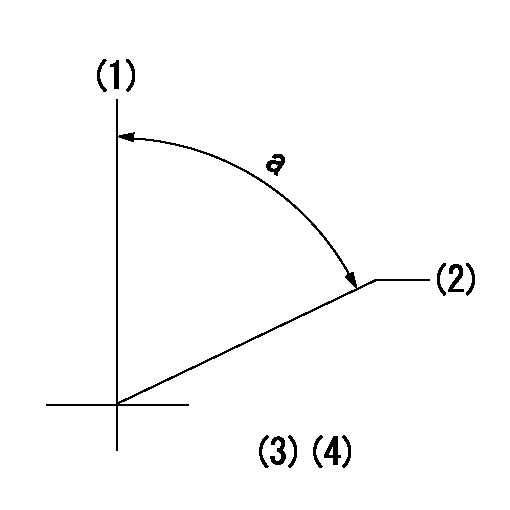
(1)Pump vertical direction
(2)Position of timer's threaded hole at No 1 cylinder's beginning of injection
(3)B.T.D.C.: aa
(4)-
----------
aa=14deg
----------
a=(60deg)
----------
aa=14deg
----------
a=(60deg)
Information:
Coolant Conditioner Elements
At operating temperature, the engine coolant is hot and under pressure.Steam can cause personal injury.Check the coolant level ONLY when the engine is stopped and the radiator fill cap is cool enough to touch with your hand.Remove the fill cap slowly to relieve pressure.Cooling System Conditioner contains alkali. Avoid contact with skin and eyes to prevent personal injury.
All water is corrosive at engine operating temperature. Use Caterpillar Coolant Conditioner Elements to treat either plain water or ethylene glycol solution.Do not use Caterpillar Coolant Conditioner Elements if Dowtherm 209 Full-Fill Coolant is used. Follow the recommendations with the Dowtherm 209 Full-Fill Coolant.
Use a Caterpillar Part Number 1W5518 precharge element when the cooling system is drained and refilled. This will establish the proper initial conditioner concentration.Use a Caterpillar Part Number 9N6123 maintenance element every 250 service hours thereafter, to maintain the proper conditioner concentration.If the coolant conditioner elements have been regularly changed at 250 service hours, the change period for engine coolant can be extended to 4000 hours.Refer to the "Maintenance" (Lubrication and Maintenance) Guide for the procedures to change the antifreeze solution, or flush the cooling system.To Change Element
1. Remove the radiator cap slowly to relieve pressure in the cooling system. 2. Close the inlet valve and the outlet valve at the element base. Turn each handle clockwise to close each valve. 3. Remove the coolant conditioner element. Discard the element. 4. Clean the element mounting base. Make certain all of the old element gasket material is removed.5. Use the correct precharge or maintenance element for your cooling system. Elements are sized according to the cooling system capacity. 6. Coat the seal of the element with a thin film of clean engine oil or antifreeze. 7. Install the element. Tighten it until the seal contacts the base, then tighten it an additional 3/4 turn. 8. Open the inlet valve and the outlet valve. 9. Maintain the coolant level above the low level plate.10. Clean and install the radiator cap.11. Start the engine and check for leaks.Fuel Specifications for Direct Injection Engines
Caterpillar Diesel Engines have the ability to burn a wide variety of fuels. These fuels are divided into two general groups, preferred and permissible.Types of Fuel
The preferred fuels provide maximum engine service life and performance. They are distillate fuels. They are commonly called fuel oil, furnace oil, diesel fuel, gas oil, or kerosene.The permissible fuels are crude oils or blended fuels. Use of these fuels can result in higher maintenance costs and reduced engine service life.See Caterpillar Form Number SEHS7067, "Fuels for Caterpillar Diesel Engines," for a detailed summary of preferred and permissible fuels and their specifications.Cetane Requirement
The minimum cetane number recommended for the engine is 40.Fuel Cloud Point
Fuel waxing can plug the fuel filters in cold weather. The fuel cloud point must be below the temperature of the surrounding air to prevent filter waxing and power loss. Fuel heating attachments are available from your Caterpillar dealer to minimize fuel filter waxing.Fuel Sulfur Content
The percent of sulfur
At operating temperature, the engine coolant is hot and under pressure.Steam can cause personal injury.Check the coolant level ONLY when the engine is stopped and the radiator fill cap is cool enough to touch with your hand.Remove the fill cap slowly to relieve pressure.Cooling System Conditioner contains alkali. Avoid contact with skin and eyes to prevent personal injury.
All water is corrosive at engine operating temperature. Use Caterpillar Coolant Conditioner Elements to treat either plain water or ethylene glycol solution.Do not use Caterpillar Coolant Conditioner Elements if Dowtherm 209 Full-Fill Coolant is used. Follow the recommendations with the Dowtherm 209 Full-Fill Coolant.
Use a Caterpillar Part Number 1W5518 precharge element when the cooling system is drained and refilled. This will establish the proper initial conditioner concentration.Use a Caterpillar Part Number 9N6123 maintenance element every 250 service hours thereafter, to maintain the proper conditioner concentration.If the coolant conditioner elements have been regularly changed at 250 service hours, the change period for engine coolant can be extended to 4000 hours.Refer to the "Maintenance" (Lubrication and Maintenance) Guide for the procedures to change the antifreeze solution, or flush the cooling system.To Change Element
1. Remove the radiator cap slowly to relieve pressure in the cooling system. 2. Close the inlet valve and the outlet valve at the element base. Turn each handle clockwise to close each valve. 3. Remove the coolant conditioner element. Discard the element. 4. Clean the element mounting base. Make certain all of the old element gasket material is removed.5. Use the correct precharge or maintenance element for your cooling system. Elements are sized according to the cooling system capacity. 6. Coat the seal of the element with a thin film of clean engine oil or antifreeze. 7. Install the element. Tighten it until the seal contacts the base, then tighten it an additional 3/4 turn. 8. Open the inlet valve and the outlet valve. 9. Maintain the coolant level above the low level plate.10. Clean and install the radiator cap.11. Start the engine and check for leaks.Fuel Specifications for Direct Injection Engines
Caterpillar Diesel Engines have the ability to burn a wide variety of fuels. These fuels are divided into two general groups, preferred and permissible.Types of Fuel
The preferred fuels provide maximum engine service life and performance. They are distillate fuels. They are commonly called fuel oil, furnace oil, diesel fuel, gas oil, or kerosene.The permissible fuels are crude oils or blended fuels. Use of these fuels can result in higher maintenance costs and reduced engine service life.See Caterpillar Form Number SEHS7067, "Fuels for Caterpillar Diesel Engines," for a detailed summary of preferred and permissible fuels and their specifications.Cetane Requirement
The minimum cetane number recommended for the engine is 40.Fuel Cloud Point
Fuel waxing can plug the fuel filters in cold weather. The fuel cloud point must be below the temperature of the surrounding air to prevent filter waxing and power loss. Fuel heating attachments are available from your Caterpillar dealer to minimize fuel filter waxing.Fuel Sulfur Content
The percent of sulfur
Have questions with 101603-0090?
Group cross 101603-0090 ZEXEL
Isuzu
101603-0090
1156015022
INJECTION-PUMP ASSEMBLY
6BB1
6BB1