Information injection-pump assembly
ZEXEL
101603-0042
1016030042
ISUZU
1156015304
1156015304
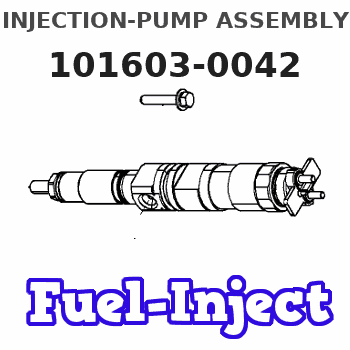
Rating:
Service parts 101603-0042 INJECTION-PUMP ASSEMBLY:
1.
_
7.
COUPLING PLATE
8.
_
9.
_
11.
Nozzle and Holder
5-15300-089-1
12.
Open Pre:MPa(Kqf/cm2)
18.1(185)
15.
NOZZLE SET
Cross reference number
ZEXEL
101603-0042
1016030042
ISUZU
1156015304
1156015304
Zexel num
Bosch num
Firm num
Name
Calibration Data:
Adjustment conditions
Test oil
1404 Test oil ISO4113 or {SAEJ967d}
1404 Test oil ISO4113 or {SAEJ967d}
Test oil temperature
degC
40
40
45
Nozzle and nozzle holder
105780-8140
Bosch type code
EF8511/9A
Nozzle
105780-0000
Bosch type code
DN12SD12T
Nozzle holder
105780-2080
Bosch type code
EF8511/9
Opening pressure
MPa
17.2
Opening pressure
kgf/cm2
175
Injection pipe
Outer diameter - inner diameter - length (mm) mm 6-2-600
Outer diameter - inner diameter - length (mm) mm 6-2-600
Overflow valve opening pressure
kPa
157
123
191
Overflow valve opening pressure
kgf/cm2
1.6
1.25
1.95
Tester oil delivery pressure
kPa
157
157
157
Tester oil delivery pressure
kgf/cm2
1.6
1.6
1.6
Direction of rotation (viewed from drive side)
Right R
Right R
Injection timing adjustment
Direction of rotation (viewed from drive side)
Right R
Right R
Injection order
1-5-3-6-
2-4
Pre-stroke
mm
3.6
3.55
3.65
Beginning of injection position
Drive side NO.1
Drive side NO.1
Difference between angles 1
Cal 1-5 deg. 60 59.5 60.5
Cal 1-5 deg. 60 59.5 60.5
Difference between angles 2
Cal 1-3 deg. 120 119.5 120.5
Cal 1-3 deg. 120 119.5 120.5
Difference between angles 3
Cal 1-6 deg. 180 179.5 180.5
Cal 1-6 deg. 180 179.5 180.5
Difference between angles 4
Cyl.1-2 deg. 240 239.5 240.5
Cyl.1-2 deg. 240 239.5 240.5
Difference between angles 5
Cal 1-4 deg. 300 299.5 300.5
Cal 1-4 deg. 300 299.5 300.5
Injection quantity adjustment
Adjusting point
-
Rack position
11.6
Pump speed
r/min
1000
1000
1000
Average injection quantity
mm3/st.
60
58.4
61.6
Max. variation between cylinders
%
0
-2.5
2.5
Basic
*
Fixing the rack
*
Standard for adjustment of the maximum variation between cylinders
*
Injection quantity adjustment_02
Adjusting point
H
Rack position
9.5+-0.5
Pump speed
r/min
325
325
325
Average injection quantity
mm3/st.
9.3
8
10.6
Max. variation between cylinders
%
0
-14
14
Fixing the rack
*
Standard for adjustment of the maximum variation between cylinders
*
Injection quantity adjustment_03
Adjusting point
A
Rack position
R1(11.6)
Pump speed
r/min
1000
1000
1000
Average injection quantity
mm3/st.
60
59
61
Basic
*
Fixing the lever
*
Injection quantity adjustment_04
Adjusting point
B
Rack position
R1+0.15
Pump speed
r/min
1600
1600
1600
Average injection quantity
mm3/st.
66.5
62.5
70.5
Fixing the lever
*
Injection quantity adjustment_05
Adjusting point
C
Rack position
R1(11.6)
Pump speed
r/min
1300
1300
1300
Average injection quantity
mm3/st.
62.1
58.9
65.3
Fixing the lever
*
Injection quantity adjustment_06
Adjusting point
D
Rack position
R1+0.1
Pump speed
r/min
650
650
650
Average injection quantity
mm3/st.
47.5
44.3
50.7
Fixing the lever
*
Injection quantity adjustment_07
Adjusting point
I
Rack position
(14.5)+0
.2
Pump speed
r/min
150
150
150
Average injection quantity
mm3/st.
80
80
85
Fixing the lever
*
Rack limit
*
Timer adjustment
Pump speed
r/min
1050--
Advance angle
deg.
0
0
0
Remarks
Start
Start
Timer adjustment_02
Pump speed
r/min
1000
Advance angle
deg.
0.5
Timer adjustment_03
Pump speed
r/min
1300
Advance angle
deg.
1.8
1.3
2.3
Timer adjustment_04
Pump speed
r/min
1600
Advance angle
deg.
4
3.5
4.5
Remarks
Finish
Finish
Test data Ex:
Governor adjustment
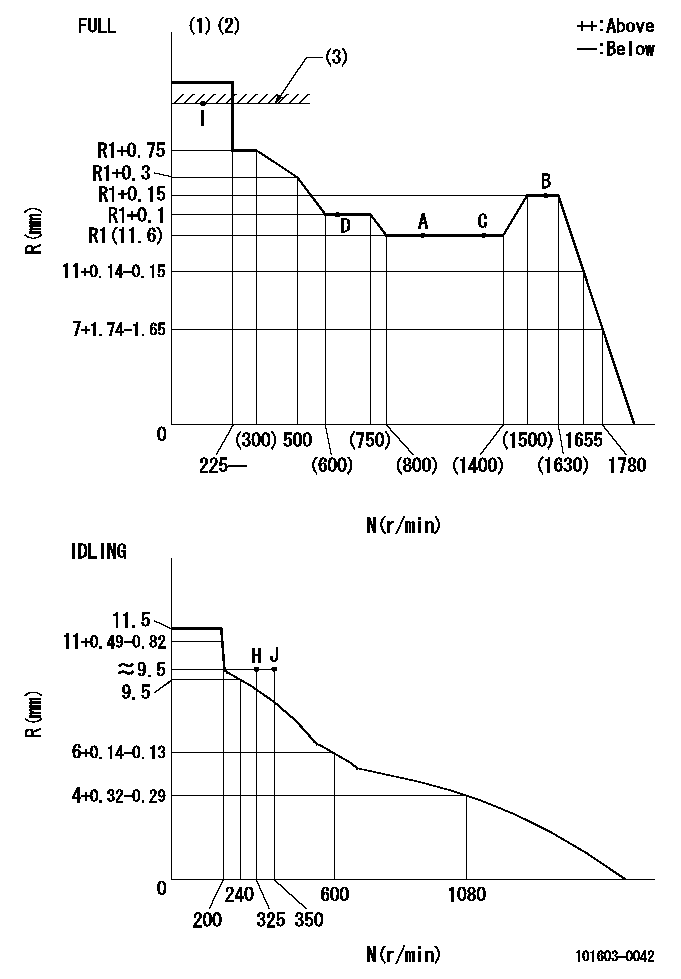
N:Pump speed
R:Rack position (mm)
(1)Torque cam stamping: T1
(2)Tolerance for racks not indicated: +-0.05mm.
(3)RACK LIMIT: RAL
----------
T1=D99 RAL=(14.5)+0.2mm
----------
----------
T1=D99 RAL=(14.5)+0.2mm
----------
Speed control lever angle
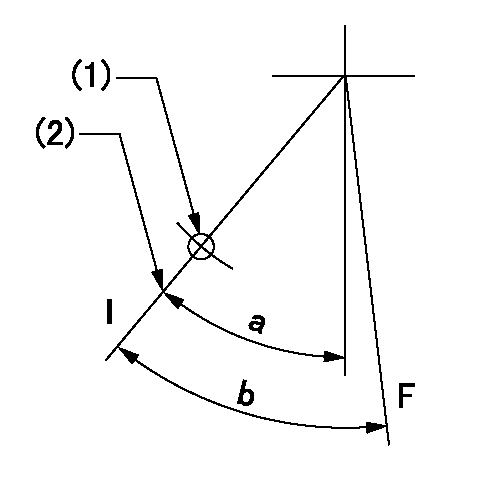
F:Full speed
I:Idle
(1)Use the hole at R = aa
(2)Stopper bolt setting
----------
aa=35mm
----------
a=39deg+-5deg b=40deg+-3deg
----------
aa=35mm
----------
a=39deg+-5deg b=40deg+-3deg
Stop lever angle

N:Pump normal
S:Stop the pump.
----------
----------
a=25deg+-5deg b=40deg+-5deg
----------
----------
a=25deg+-5deg b=40deg+-5deg
Timing setting
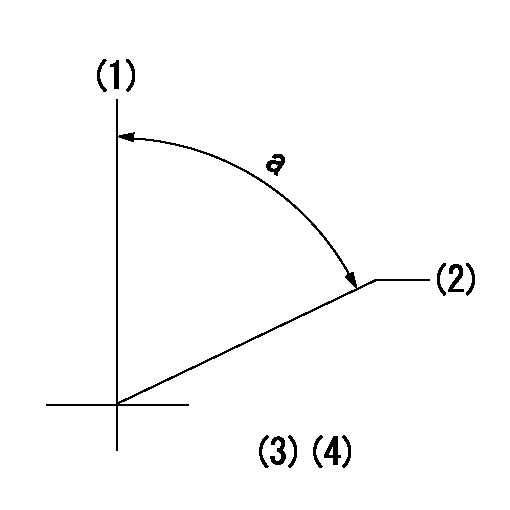
(1)Pump vertical direction
(2)Position of timer's threaded hole at No 1 cylinder's beginning of injection
(3)B.T.D.C.: aa
(4)-
----------
aa=14deg
----------
a=(60deg)
----------
aa=14deg
----------
a=(60deg)
Information:
Above 32°F (0°C)
Make sure no one is working on or close to the machine before starting the engine. Fasten seat belt.
1. Make certain TRANSMISSION NEUTRAL LOCK and PARKING BRAKE LOCKING lever is engaged. Move all implement controls to HOLD. 2. Insert the key in the disconnect switch and turn the switch ON.
Never turn the disconnect switch OFF with the engine running.
3. Move the governor control lever to the low idle position just past the detent. 4. Push in and turn the START switch to START. Release the switch when the engine starts.Below 32°F (0°C)
1. Follow steps 1-thru-4 for above 32°F (0°C). If engine does not start, push in the Starting Aid Button. A metered amount of starting fluid, sufficient to help start the engine, is released each time the Starting Aid Button is pushed in. 2. While cranking the engine use additional Starting Aid Fluid every 2 seconds, by pushing the button in and releasing it. 3. Release the START switch when the engine starts.4. If necessary continue the use of Starting Aid Fluid every 2 seconds after the engine starts, until it runs smoothly.
After every 30 seconds of cranking, allow 2 minutes for the starting motor to cool.
5. If extra battery capacity is needed, refer to the Operator's Guide SEBU5516 - 955L, 977L & 983B Track Type Loaders.6. Refer to the Operator's Guide for after starting checks, warm up procedure and engine shutdown. For starting below 0°F (-18°C) the use of optional cold weather starting aids is recommended. A coolant heater, jacket water heater or extra battery capacity may be required.
The Starting Aid Ether Bottle must be removed before transporting the machine. See the Lubrication and Maintenance Guide SEBU5515 for removal and replacing the bottle.
Make sure no one is working on or close to the machine before starting the engine. Fasten seat belt.
1. Make certain TRANSMISSION NEUTRAL LOCK and PARKING BRAKE LOCKING lever is engaged. Move all implement controls to HOLD. 2. Insert the key in the disconnect switch and turn the switch ON.
Never turn the disconnect switch OFF with the engine running.
3. Move the governor control lever to the low idle position just past the detent. 4. Push in and turn the START switch to START. Release the switch when the engine starts.Below 32°F (0°C)
1. Follow steps 1-thru-4 for above 32°F (0°C). If engine does not start, push in the Starting Aid Button. A metered amount of starting fluid, sufficient to help start the engine, is released each time the Starting Aid Button is pushed in. 2. While cranking the engine use additional Starting Aid Fluid every 2 seconds, by pushing the button in and releasing it. 3. Release the START switch when the engine starts.4. If necessary continue the use of Starting Aid Fluid every 2 seconds after the engine starts, until it runs smoothly.
After every 30 seconds of cranking, allow 2 minutes for the starting motor to cool.
5. If extra battery capacity is needed, refer to the Operator's Guide SEBU5516 - 955L, 977L & 983B Track Type Loaders.6. Refer to the Operator's Guide for after starting checks, warm up procedure and engine shutdown. For starting below 0°F (-18°C) the use of optional cold weather starting aids is recommended. A coolant heater, jacket water heater or extra battery capacity may be required.
The Starting Aid Ether Bottle must be removed before transporting the machine. See the Lubrication and Maintenance Guide SEBU5515 for removal and replacing the bottle.