Information injection-pump assembly
BOSCH
F 019 Z20 462
f019z20462
ZEXEL
101602-9820
1016029820
NISSAN-DIESEL
16790Z5572
16790z5572
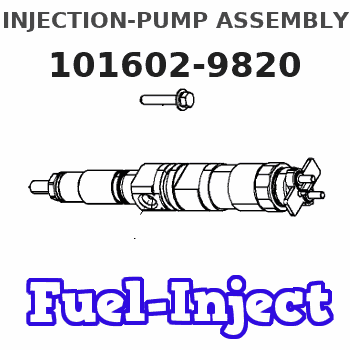
Rating:
Service parts 101602-9820 INJECTION-PUMP ASSEMBLY:
1.
_
5.
AUTOM. ADVANCE MECHANIS
6.
COUPLING PLATE
8.
_
9.
_
11.
Nozzle and Holder
16600-Z5574
12.
Open Pre:MPa(Kqf/cm2)
19.6{200}
15.
NOZZLE SET
Cross reference number
BOSCH
F 019 Z20 462
f019z20462
ZEXEL
101602-9820
1016029820
NISSAN-DIESEL
16790Z5572
16790z5572
Zexel num
Bosch num
Firm num
Name
F 019 Z20 462
16790Z5572 NISSAN-DIESEL
INJECTION-PUMP ASSEMBLY
FM6TA06 * K 14BF PE6AD PE
FM6TA06 * K 14BF PE6AD PE
Calibration Data:
Adjustment conditions
Test oil
1404 Test oil ISO4113 or {SAEJ967d}
1404 Test oil ISO4113 or {SAEJ967d}
Test oil temperature
degC
40
40
45
Nozzle and nozzle holder
105780-8140
Bosch type code
EF8511/9A
Nozzle
105780-0000
Bosch type code
DN12SD12T
Nozzle holder
105780-2080
Bosch type code
EF8511/9
Opening pressure
MPa
17.2
Opening pressure
kgf/cm2
175
Injection pipe
Outer diameter - inner diameter - length (mm) mm 6-2-600
Outer diameter - inner diameter - length (mm) mm 6-2-600
Overflow valve opening pressure
kPa
157
123
191
Overflow valve opening pressure
kgf/cm2
1.6
1.25
1.95
Tester oil delivery pressure
kPa
157
157
157
Tester oil delivery pressure
kgf/cm2
1.6
1.6
1.6
Direction of rotation (viewed from drive side)
Right R
Right R
Injection timing adjustment
Direction of rotation (viewed from drive side)
Right R
Right R
Injection order
1-4-2-6-
3-5
Pre-stroke
mm
3.6
3.55
3.65
Beginning of injection position
Drive side NO.1
Drive side NO.1
Difference between angles 1
Cal 1-4 deg. 60 59.5 60.5
Cal 1-4 deg. 60 59.5 60.5
Difference between angles 2
Cyl.1-2 deg. 120 119.5 120.5
Cyl.1-2 deg. 120 119.5 120.5
Difference between angles 3
Cal 1-6 deg. 180 179.5 180.5
Cal 1-6 deg. 180 179.5 180.5
Difference between angles 4
Cal 1-3 deg. 240 239.5 240.5
Cal 1-3 deg. 240 239.5 240.5
Difference between angles 5
Cal 1-5 deg. 300 299.5 300.5
Cal 1-5 deg. 300 299.5 300.5
Injection quantity adjustment
Adjusting point
A
Rack position
10.8
Pump speed
r/min
1350
1350
1350
Average injection quantity
mm3/st.
130.2
129.2
131.2
Max. variation between cylinders
%
0
-4
4
Basic
*
Fixing the lever
*
Injection quantity adjustment_02
Adjusting point
B
Rack position
5.8+-0.5
Pump speed
r/min
300
300
300
Average injection quantity
mm3/st.
9
7.9
10.1
Max. variation between cylinders
%
0
-10
10
Fixing the rack
*
Test data Ex:
Governor adjustment
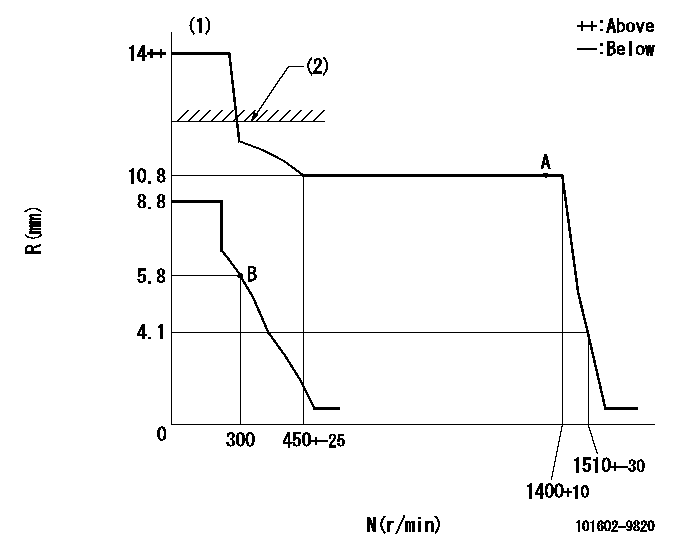
N:Pump speed
R:Rack position (mm)
(1)Target notch: K
(2)RACK LIMIT: RAL
----------
K=9 RAL=11.8+-0.1mm
----------
----------
K=9 RAL=11.8+-0.1mm
----------
Speed control lever angle
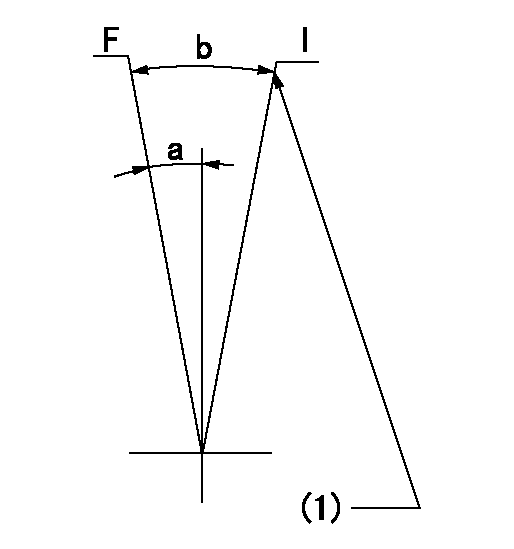
F:Full speed
I:Idle
(1)Stopper bolt setting
----------
----------
a=8deg+-5deg b=30deg+-5deg
----------
----------
a=8deg+-5deg b=30deg+-5deg
Stop lever angle
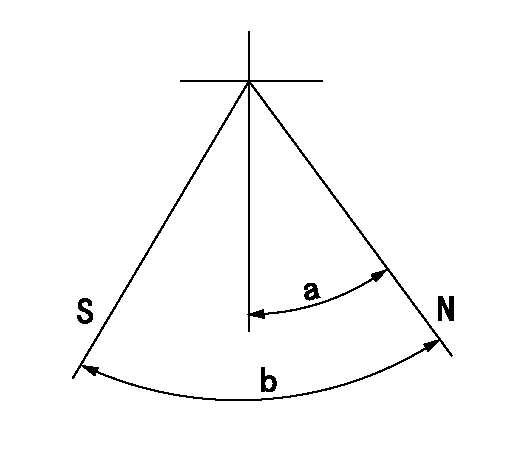
N:Pump normal
S:Stop the pump.
----------
----------
a=26.5deg+-5deg b=53deg+-5deg
----------
----------
a=26.5deg+-5deg b=53deg+-5deg
Timing setting
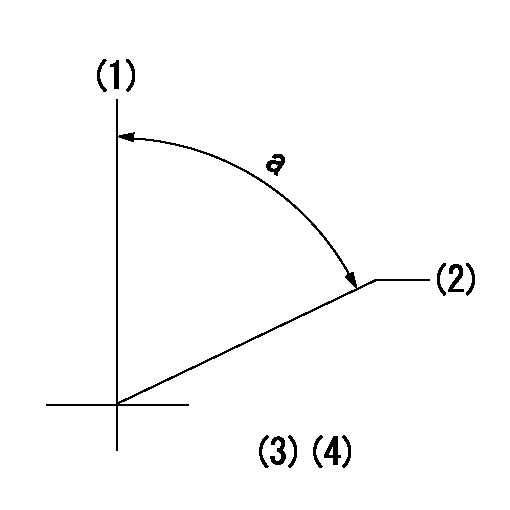
(1)Pump vertical direction
(2)Position of gear's standard threaded hole at No 1 cylinder's beginning of injection (position of gear's 'M' mark)
(3)B.T.D.C.: aa
(4)-
----------
aa=20deg
----------
a=(50deg)
----------
aa=20deg
----------
a=(50deg)
Information:
Start By:a. remove fuel injection nozzlesb. remove cylinder head assembly and spacer plate 1. Put compression on valve spring (2) with Tool (A). Remove locks (1).2. Remove Tool (A), rotocoil, spring, valve stem oil shield and valve. Put identification marks on valves with respect to their location in the cylinder head. 3. Check the spring force with Tool (B). The spring force is 257 25 N (57.8 5.6 lb). The length of spring under test force is 44.86 mm (1.766 in). The free length after test is 52.07 mm (2.050 in).4. Do Steps 1 through 3 again for the remainder of the valves.Install Valves
1. Put clean engine oil on the valve stems. Install valve (3), oil shield (4), spring (2) and rotocoil (1) in the cylinder head. 2. Put Tool (A) in position on the valve spring. Install the locks with Tool (B).
Locks can be thrown from valve when the compressor is released if they are not in their correct position on valve stem. Personal injury can be the result if not carefully removed.
3. Remove Tool (A), and hit the top of valve with a plastic hammer to be sure the locks are in their correct position on valve.4. Do Steps 1 through 3 again for the remainder of the valves.End By:a. install cylinder head assembly and spacer plateb. install fuel injection nozzles
1. Put clean engine oil on the valve stems. Install valve (3), oil shield (4), spring (2) and rotocoil (1) in the cylinder head. 2. Put Tool (A) in position on the valve spring. Install the locks with Tool (B).
Locks can be thrown from valve when the compressor is released if they are not in their correct position on valve stem. Personal injury can be the result if not carefully removed.
3. Remove Tool (A), and hit the top of valve with a plastic hammer to be sure the locks are in their correct position on valve.4. Do Steps 1 through 3 again for the remainder of the valves.End By:a. install cylinder head assembly and spacer plateb. install fuel injection nozzles