Information injection-pump assembly
ZEXEL
101602-9551
1016029551
NISSAN-DIESEL
16790Z5565
16790z5565
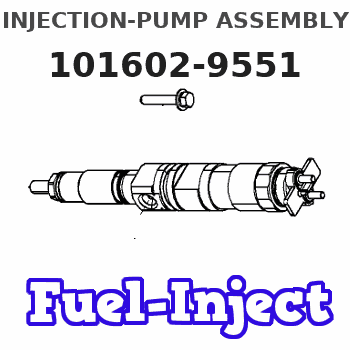
Rating:
Service parts 101602-9551 INJECTION-PUMP ASSEMBLY:
1.
_
5.
AUTOM. ADVANCE MECHANIS
7.
COUPLING PLATE
8.
_
9.
_
11.
Nozzle and Holder
16600-Z5515
12.
Open Pre:MPa(Kqf/cm2)
19.6{200}
15.
NOZZLE SET
Include in #1:
101602-9551
as INJECTION-PUMP ASSEMBLY
Include in #2:
104741-6591
as _
Cross reference number
ZEXEL
101602-9551
1016029551
NISSAN-DIESEL
16790Z5565
16790z5565
Zexel num
Bosch num
Firm num
Name
101602-9551
16790Z5565 NISSAN-DIESEL
INJECTION-PUMP ASSEMBLY
FD6T * K 14BE PE6A PE
FD6T * K 14BE PE6A PE
Calibration Data:
Adjustment conditions
Test oil
1404 Test oil ISO4113 or {SAEJ967d}
1404 Test oil ISO4113 or {SAEJ967d}
Test oil temperature
degC
40
40
45
Nozzle and nozzle holder
105780-8140
Bosch type code
EF8511/9A
Nozzle
105780-0000
Bosch type code
DN12SD12T
Nozzle holder
105780-2080
Bosch type code
EF8511/9
Opening pressure
MPa
17.2
Opening pressure
kgf/cm2
175
Injection pipe
Outer diameter - inner diameter - length (mm) mm 6-2-600
Outer diameter - inner diameter - length (mm) mm 6-2-600
Overflow valve opening pressure
kPa
157
123
191
Overflow valve opening pressure
kgf/cm2
1.6
1.25
1.95
Tester oil delivery pressure
kPa
157
157
157
Tester oil delivery pressure
kgf/cm2
1.6
1.6
1.6
Direction of rotation (viewed from drive side)
Right R
Right R
Injection timing adjustment
Direction of rotation (viewed from drive side)
Right R
Right R
Injection order
1-4-2-6-
3-5
Pre-stroke
mm
3
2.95
3.05
Beginning of injection position
Drive side NO.1
Drive side NO.1
Difference between angles 1
Cal 1-4 deg. 60 59.5 60.5
Cal 1-4 deg. 60 59.5 60.5
Difference between angles 2
Cyl.1-2 deg. 120 119.5 120.5
Cyl.1-2 deg. 120 119.5 120.5
Difference between angles 3
Cal 1-6 deg. 180 179.5 180.5
Cal 1-6 deg. 180 179.5 180.5
Difference between angles 4
Cal 1-3 deg. 240 239.5 240.5
Cal 1-3 deg. 240 239.5 240.5
Difference between angles 5
Cal 1-5 deg. 300 299.5 300.5
Cal 1-5 deg. 300 299.5 300.5
Injection quantity adjustment
Adjusting point
A
Rack position
9.8
Pump speed
r/min
750
750
750
Average injection quantity
mm3/st.
63.9
62.3
65.5
Max. variation between cylinders
%
0
-2
2
Basic
*
Fixing the lever
*
Boost pressure
kPa
50
50
Boost pressure
mmHg
375
375
Injection quantity adjustment_02
Adjusting point
B
Rack position
9.4
Pump speed
r/min
500
500
500
Average injection quantity
mm3/st.
45.3
43.7
46.9
Max. variation between cylinders
%
0
-3
3
Fixing the lever
*
Boost pressure
kPa
0
0
0
Boost pressure
mmHg
0
0
0
Injection quantity adjustment_03
Adjusting point
C
Rack position
7.2+-0.5
Pump speed
r/min
300
300
300
Average injection quantity
mm3/st.
8.1
6.3
9.9
Max. variation between cylinders
%
0
-12
12
Fixing the rack
*
Boost pressure
kPa
0
0
0
Boost pressure
mmHg
0
0
0
Boost compensator adjustment
Pump speed
r/min
600
600
600
Rack position
9.4
Boost pressure
kPa
16
14.7
17.3
Boost pressure
mmHg
120
110
130
Boost compensator adjustment_02
Pump speed
r/min
600
600
600
Rack position
9.8
Boost pressure
kPa
36.7
30
43.4
Boost pressure
mmHg
275
225
325
Test data Ex:
Governor adjustment
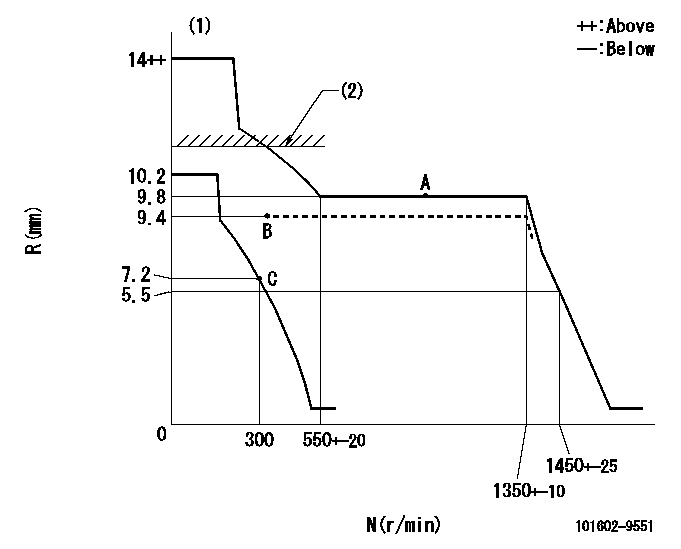
N:Pump speed
R:Rack position (mm)
(1)Target notch: K
(2)Rack limit using excess fuel lever: L1
----------
K=12 L1=10.3+0.2mm
----------
----------
K=12 L1=10.3+0.2mm
----------
Speed control lever angle
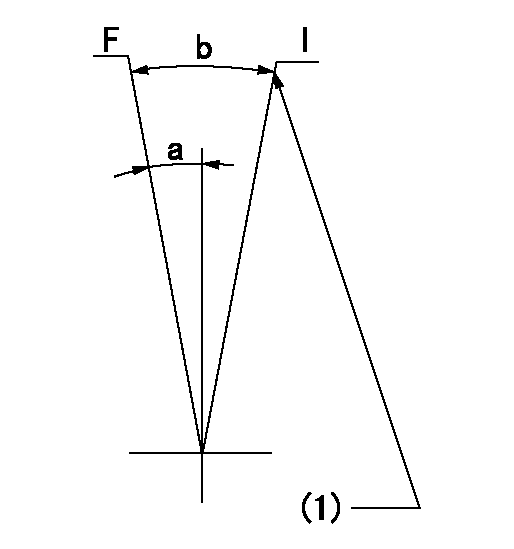
F:Full speed
I:Idle
(1)Stopper bolt setting
----------
----------
a=10deg+-5deg b=26deg+-5deg
----------
----------
a=10deg+-5deg b=26deg+-5deg
Stop lever angle

N:Pump normal
S:Stop the pump.
----------
----------
a=26.5deg+-5deg b=53deg+-5deg
----------
----------
a=26.5deg+-5deg b=53deg+-5deg
0000001101

N:Normal
B:When boosted
----------
----------
a=(15deg) b=(2deg)
----------
----------
a=(15deg) b=(2deg)
0000001501 GOV FULL LOAD ADJUSTMENT

Title1:Full load stopper adjustment
Title2:Governor set speed
LABEL1:Distinguishing
LABEL2:Pump speed (r/min)
LABEL3:Ave. injection quantity (mm3/st)
LABEL4:Max. var. bet. cyl.
LABEL5:Remarks
LABEL6:Distinguishing
LABEL7:Governor set speed (r/min)
LABEL8:Maximum no-load speed (r/min)
LABEL9:Remarks
(1)Adjustment conditions are the same as those for measuring injection quantity.
(2)At high idle rack position L
----------
L=5.5mm
----------
a1=A a2=B a3=- a4=- a5=- a6=- r1=900r/min r2=750r/min r3=- r4=- r5=- r6=- Q1=71.8+-1.6mm3/st Q2=63.9+-1.6mm3/st Q3=- Q4=- Q5=- Q6=- c1=+-2% c2=+-2% c3=- c4=- c5=- c6=- a7=27 a8=26 a9=25 a10=24 a11=23 a12=22 a13=21 a14=20 a15=19 a16=18 a17=17 a18=16 a19=15 a20=- a21=- a22=- a23=- a24=- a25=- a26=- a27=- a28=- r7=1350r/min r8=1300r/min r9=1250r/min r10=1200r/min r11=1150r/min r12=1100r/min r13=1050r/min r14=1000r/min r15=950r/min r16=900r/min r17=850r/min r18=800r/min r19=750r/min r20=- r21=- r22=- r23=- r24=- r25=- r26=- r27=- r28=- R7=1450+-33r/min R8=1395+-32r/min R9=1340+-31r/min R10=1290+-30r/min R11=1235+-28r/min R12=1180+-27r/min R13=1130+-26r/min R14=1075+-25r/min R15=1020+-23r/min R16=965+-22r/min R17=915+-22r/min R18=860+-20r/min R19=805+-18r/min R20=- R21=- R22=- R23=- R24=- R25=- R26=- R27=- R28=-
----------
L=5.5mm
----------
a1=A a2=B a3=- a4=- a5=- a6=- r1=900r/min r2=750r/min r3=- r4=- r5=- r6=- Q1=71.8+-1.6mm3/st Q2=63.9+-1.6mm3/st Q3=- Q4=- Q5=- Q6=- c1=+-2% c2=+-2% c3=- c4=- c5=- c6=- a7=27 a8=26 a9=25 a10=24 a11=23 a12=22 a13=21 a14=20 a15=19 a16=18 a17=17 a18=16 a19=15 a20=- a21=- a22=- a23=- a24=- a25=- a26=- a27=- a28=- r7=1350r/min r8=1300r/min r9=1250r/min r10=1200r/min r11=1150r/min r12=1100r/min r13=1050r/min r14=1000r/min r15=950r/min r16=900r/min r17=850r/min r18=800r/min r19=750r/min r20=- r21=- r22=- r23=- r24=- r25=- r26=- r27=- r28=- R7=1450+-33r/min R8=1395+-32r/min R9=1340+-31r/min R10=1290+-30r/min R11=1235+-28r/min R12=1180+-27r/min R13=1130+-26r/min R14=1075+-25r/min R15=1020+-23r/min R16=965+-22r/min R17=915+-22r/min R18=860+-20r/min R19=805+-18r/min R20=- R21=- R22=- R23=- R24=- R25=- R26=- R27=- R28=-
Timing setting
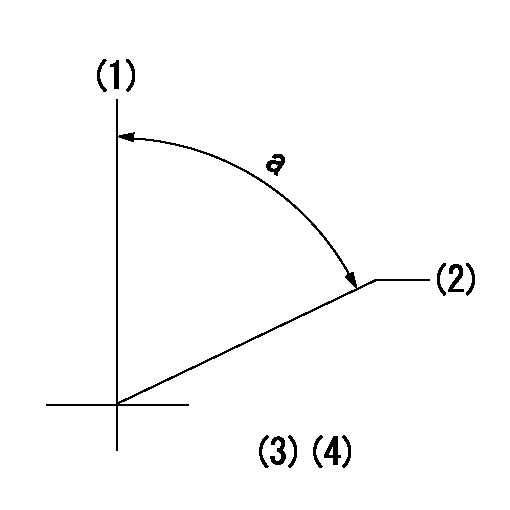
(1)Pump vertical direction
(2)Position of coupling's threaded hole at No 1 cylinder's beginning of injection
(3)-
(4)-
----------
----------
a=(60deg)
----------
----------
a=(60deg)
Information:
Cut apart used filters to see contaminants. Use a 6V790S FilterCutter
to cut the filter housing.
Maintenance for Engines Using Heavy Fuel
Engines operating on heavy fuel must be carefully monitored and maintained.Service intervals must be strictly observed. Operators must be trained toperform a thorough service inspection.
"As Needed" Periodic Activities
Test fuel as it is delivered. Identify contaminant levels immediately and notify appropriate operations personnel.
Before storage, test for compatibility between fuel in the tanks and the fuel being purchased. Keep the fuel in separate tanks if possible.
Use regular S.O.S oil analysis to determine if there are wear particles in the oil, and maintain the proper TBN level.
Request infrared analysis on used oils to determine the effects of burning heavy fuel on the crankcase oil.
Daily Activities
Maintain and monitor fuel treatment equipment.
Record engine temperatures to assure adequate jacket water temperature, aftercooler temperature, and air intake temperature.
If equipped with a turbocharger water wash attachment, wash the turbocharger exhaust turbine. It is necessary to remove deposits from the turbine side of the turbocharger. (A washer attachment which does this is available on 3600 Family Engines.)
Check exhaust thermocouples and record exhaust temperatures. Be alert for worn exhaust valves.
Measure valve stem projection when new; use a stationary point such asthe valve cover gasket surface for a reference point. Record the measurementsfor each valve for later follow-up measurements. If valve stem projection movesmore than 1.25 mm (.050 in.) consider disassembly to find the reason. Anotherway to observe valve face wear is to measure and record changes on valve lashover a period of time.
Monitor fuel and oil filter differentials every shift. Check for filter plugging.
Drain settling and fuel tank bottoms daily. Take note if there is excessive water or sediment.
Every 1000 Hours
Check one cylinder head for exhaust valve seating and carbon build-up. Check the fuel injectors for adequate nozzle spray pattern. Make sure the valve rotators are operating.
Clean the turbocharger (exhaust turbine) (3500 and 3600 Family Engines without washers).
Operating the Engine at Low Load
If you're expecting to operate your engine at part load for extendedperiods, switch to No.2 diesel fuel or marine diesel oil. (Make sure the fuelinjectors are not run without fuel during the switch.)
The following chart shows the relationship between engine load and length oftime. It will guide you on what type of fuel to burn in light load applications.
Chart with time and numbers.
Other Heavy Fuel Tips
Here are some things to keep in mind when using heavy fuels.
Cut apart used filters to see contaminants. As contamination levels increase, the quality of diesel fuel is generally decreasing.
As fuel quality decreases, it becomes even more important to have good fuel treatment systems. The treatment system can sometimes compensate for poor fuel quality. ..but there is less margin for error with a system that is not working correctly.
Often, diesel engines cannot operate on fuel that is straight from the fuel tank (bunkered).
Viscosity does not relate to quality. Do not use fuel thickness
Have questions with 101602-9551?
Group cross 101602-9551 ZEXEL
Nissan-Diesel
101602-9551
16790Z5565
INJECTION-PUMP ASSEMBLY
FD6T
FD6T