Information injection-pump assembly
BOSCH
9 400 610 623
9400610623
ZEXEL
101602-8360
1016028360
ISUZU
1156031980
1156031980
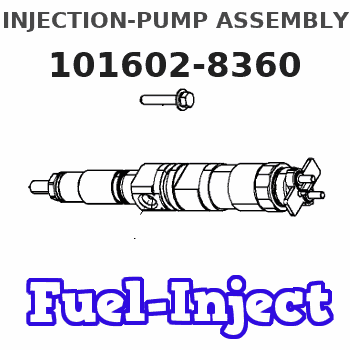
Rating:
Service parts 101602-8360 INJECTION-PUMP ASSEMBLY:
1.
_
5.
AUTOM. ADVANCE MECHANIS
6.
COUPLING PLATE
8.
_
9.
_
11.
Nozzle and Holder
1-15300-331-0
12.
Open Pre:MPa(Kqf/cm2)
18.1{185}
15.
NOZZLE SET
Include in #1:
101602-8360
as INJECTION-PUMP ASSEMBLY
Include in #2:
104749-5100
as _
Cross reference number
BOSCH
9 400 610 623
9400610623
ZEXEL
101602-8360
1016028360
ISUZU
1156031980
1156031980
Zexel num
Bosch num
Firm num
Name
9 400 610 623
1156031980 ISUZU
INJECTION-PUMP ASSEMBLY
6BG1-T * K 14BF PE6AD PE
6BG1-T * K 14BF PE6AD PE
Calibration Data:
Adjustment conditions
Test oil
1404 Test oil ISO4113 or {SAEJ967d}
1404 Test oil ISO4113 or {SAEJ967d}
Test oil temperature
degC
40
40
45
Nozzle and nozzle holder
105780-8140
Bosch type code
EF8511/9A
Nozzle
105780-0000
Bosch type code
DN12SD12T
Nozzle holder
105780-2080
Bosch type code
EF8511/9
Opening pressure
MPa
17.2
Opening pressure
kgf/cm2
175
Injection pipe
Outer diameter - inner diameter - length (mm) mm 6-2-600
Outer diameter - inner diameter - length (mm) mm 6-2-600
Overflow valve
131424-4920
Overflow valve opening pressure
kPa
127
107
147
Overflow valve opening pressure
kgf/cm2
1.3
1.1
1.5
Tester oil delivery pressure
kPa
157
157
157
Tester oil delivery pressure
kgf/cm2
1.6
1.6
1.6
Direction of rotation (viewed from drive side)
Right R
Right R
Injection timing adjustment
Direction of rotation (viewed from drive side)
Right R
Right R
Injection order
1-5-3-6-
2-4
Pre-stroke
mm
3.6
3.55
3.65
Beginning of injection position
Drive side NO.1
Drive side NO.1
Difference between angles 1
Cal 1-5 deg. 60 59.5 60.5
Cal 1-5 deg. 60 59.5 60.5
Difference between angles 2
Cal 1-3 deg. 120 119.5 120.5
Cal 1-3 deg. 120 119.5 120.5
Difference between angles 3
Cal 1-6 deg. 180 179.5 180.5
Cal 1-6 deg. 180 179.5 180.5
Difference between angles 4
Cyl.1-2 deg. 240 239.5 240.5
Cyl.1-2 deg. 240 239.5 240.5
Difference between angles 5
Cal 1-4 deg. 300 299.5 300.5
Cal 1-4 deg. 300 299.5 300.5
Injection quantity adjustment
Adjusting point
A
Rack position
9.2
Pump speed
r/min
900
900
900
Average injection quantity
mm3/st.
82.5
81
84
Max. variation between cylinders
%
0
-2
2
Basic
*
Fixing the rack
*
Injection quantity adjustment_02
Adjusting point
-
Rack position
7.5+-0.5
Pump speed
r/min
500
500
500
Average injection quantity
mm3/st.
12
10.7
13.3
Max. variation between cylinders
%
0
-14
14
Fixing the rack
*
Remarks
Adjust only variation between cylinders; adjust governor according to governor specifications.
Adjust only variation between cylinders; adjust governor according to governor specifications.
Injection quantity adjustment_03
Adjusting point
D
Rack position
-
Pump speed
r/min
100
100
100
Average injection quantity
mm3/st.
80
80
90
Fixing the lever
*
Rack limit
*
Test data Ex:
Governor adjustment
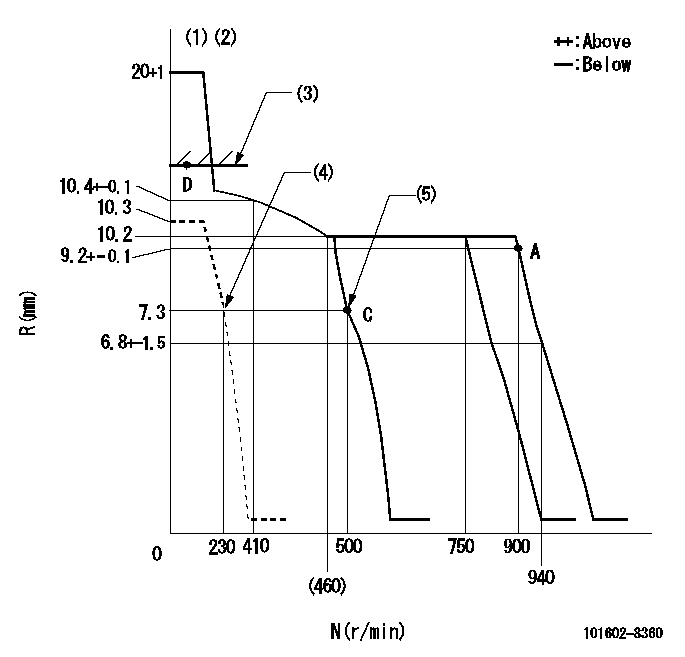
N:Pump speed
R:Rack position (mm)
(1)Notch fixed: K
(2)Tolerance for racks not indicated: +-0.05mm.
(3)RACK LIMIT
(4)Set idle sub-spring
(5)Main spring setting
----------
K=7
----------
----------
K=7
----------
Speed control lever angle
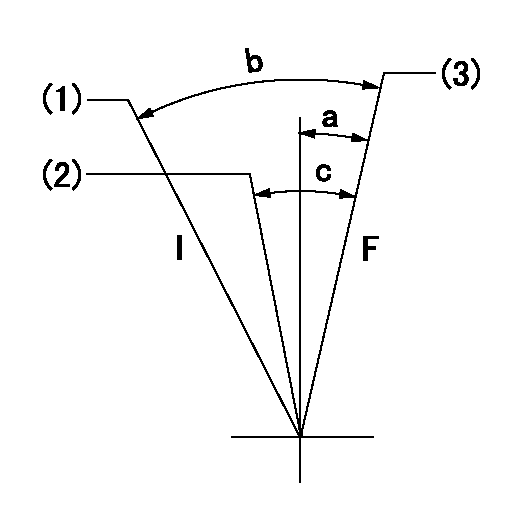
F:Full speed
I:Idle
(1)Stopper bolt setting
(2)Set the pump speed at aa
(3)Set speed at bb (setting at delivery).
----------
aa=750r/min bb=900r/min
----------
a=(0deg)+-5deg b=(16deg)+-5deg c=(5deg)+-5deg
----------
aa=750r/min bb=900r/min
----------
a=(0deg)+-5deg b=(16deg)+-5deg c=(5deg)+-5deg
Stop lever angle
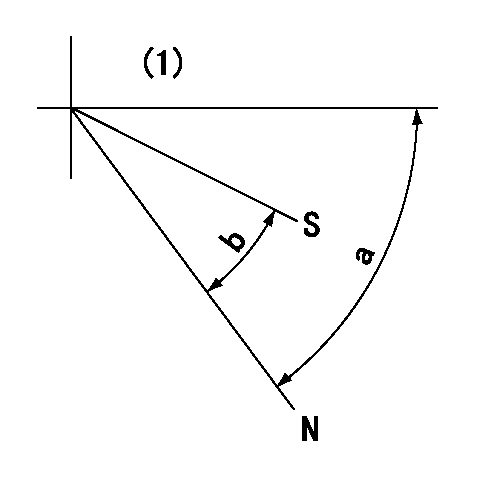
N:Pump normal
S:Stop the pump.
(1)No return spring
----------
----------
a=66.5deg+-5deg b=53deg+-5deg
----------
----------
a=66.5deg+-5deg b=53deg+-5deg
Timing setting

(1)Pump vertical direction
(2)Position of gear mark 'CC' at No 1 cylinder's beginning of injection
(3)B.T.D.C.: aa
(4)-
----------
aa=12deg
----------
a=(100deg)
----------
aa=12deg
----------
a=(100deg)
Information:
Changing Filter Element
A 1U-9578 Repair Kit (Nozzle Tester) is available to maintain the tester. The repair kit contains a new filter along with seals, gaskets, and instructions on how to use the kit. Do not reuse seals and gaskets when changing the filter. Always use new seals and gaskets.Calibration Fluid
The calibration fluid should be changed every three months or after testing 50 nozzles. The fluid should also be changed whenever inaccurate test results are suspected.Inaccurate test results can be caused by fluid with improper specific gravity, viscosity, visible contamination, fluid that foams, or discolored fluid.The fluid should also be checked for the correct viscosity. It is a good practice to test new calibration fluid for the correct viscosity and specific gravity. Use a 9U-7840 Test Kit to check calibration fluid.
Do not refill the nozzle tester with test oil that has been pumped through a fuel injection nozzle. Nozzles contain residual amounts of diesel fuel that is pumped out when tested. The diesel fuel mixes with and contaminates the test oil. Using this diesel fuel test oil combination will damage the nozzle tester.
9U-7840 Test Kit For Checking Fluid Viscosity Calibration fluid will last longer if the nozzles are cleaned prior to testing. As the fluid in the tester becomes contaminated, the accuracy of the test results are decreased.Changing Calibration Fluid
1. Completely drain the reservoir and any fluid contained in the pump mechanism. Special care must be taken for the disposal of the calibration fluid. Recent regulations prohibit the dumping of oil; all oil must be properly disposed.2. Thoroughly clean the reservoir using an 8T-9011 Component Cleaner or equivalent and clean towels.3. Install a new 8T-5313 Filter Element (10 micron). A new filter element should be installed whenever the calibration fluid is changed (even if less than 3 months).4. Fill the reservoir with clean calibration fluid (refer to the chart for part numbers).Nozzle Tester Pressure Gauges
Pressure gauges in the nozzle tester should be checked for accuracy every 12 months or whenever inaccurate test results are suspected. Gauges should also be checked whenever a gauge is damaged or the needle does not return to zero. Record all data on the data sheets in the "Forms" section.1. Remove pressure gauge from the nozzle tester.2. Install gauge adapter from 5P-8558 Calibrating Group Pressure Gauge onto pressure gauge.3. Connect pressure to tester port.4. Use a 1U-5230 Hand Pump to apply pressure to the gauge. Increase the pressure to 25% of the pressure gauges capacity.5. Check the actual gauge pressure with the tester gauge reading. The two pressures should be within two percent of each other.6. Repeat Step 5 at 50, 75 and 100 percent increments. Each increment should be within two percent of the tester gauge reading.7. If the pressure is not within two percent, the pressure gauge should be replaced.Check Tester For Leakage
Before testing any nozzle, check the tester for obvious external leakage. Leakage in the tester will give inaccurate test results, causing good nozzles to be rejected.Always check the tester for leakage
A 1U-9578 Repair Kit (Nozzle Tester) is available to maintain the tester. The repair kit contains a new filter along with seals, gaskets, and instructions on how to use the kit. Do not reuse seals and gaskets when changing the filter. Always use new seals and gaskets.Calibration Fluid
The calibration fluid should be changed every three months or after testing 50 nozzles. The fluid should also be changed whenever inaccurate test results are suspected.Inaccurate test results can be caused by fluid with improper specific gravity, viscosity, visible contamination, fluid that foams, or discolored fluid.The fluid should also be checked for the correct viscosity. It is a good practice to test new calibration fluid for the correct viscosity and specific gravity. Use a 9U-7840 Test Kit to check calibration fluid.
Do not refill the nozzle tester with test oil that has been pumped through a fuel injection nozzle. Nozzles contain residual amounts of diesel fuel that is pumped out when tested. The diesel fuel mixes with and contaminates the test oil. Using this diesel fuel test oil combination will damage the nozzle tester.
9U-7840 Test Kit For Checking Fluid Viscosity Calibration fluid will last longer if the nozzles are cleaned prior to testing. As the fluid in the tester becomes contaminated, the accuracy of the test results are decreased.Changing Calibration Fluid
1. Completely drain the reservoir and any fluid contained in the pump mechanism. Special care must be taken for the disposal of the calibration fluid. Recent regulations prohibit the dumping of oil; all oil must be properly disposed.2. Thoroughly clean the reservoir using an 8T-9011 Component Cleaner or equivalent and clean towels.3. Install a new 8T-5313 Filter Element (10 micron). A new filter element should be installed whenever the calibration fluid is changed (even if less than 3 months).4. Fill the reservoir with clean calibration fluid (refer to the chart for part numbers).Nozzle Tester Pressure Gauges
Pressure gauges in the nozzle tester should be checked for accuracy every 12 months or whenever inaccurate test results are suspected. Gauges should also be checked whenever a gauge is damaged or the needle does not return to zero. Record all data on the data sheets in the "Forms" section.1. Remove pressure gauge from the nozzle tester.2. Install gauge adapter from 5P-8558 Calibrating Group Pressure Gauge onto pressure gauge.3. Connect pressure to tester port.4. Use a 1U-5230 Hand Pump to apply pressure to the gauge. Increase the pressure to 25% of the pressure gauges capacity.5. Check the actual gauge pressure with the tester gauge reading. The two pressures should be within two percent of each other.6. Repeat Step 5 at 50, 75 and 100 percent increments. Each increment should be within two percent of the tester gauge reading.7. If the pressure is not within two percent, the pressure gauge should be replaced.Check Tester For Leakage
Before testing any nozzle, check the tester for obvious external leakage. Leakage in the tester will give inaccurate test results, causing good nozzles to be rejected.Always check the tester for leakage