Information injection-pump assembly
ZEXEL
101602-7270
1016027270
ISUZU
1156025880
1156025880
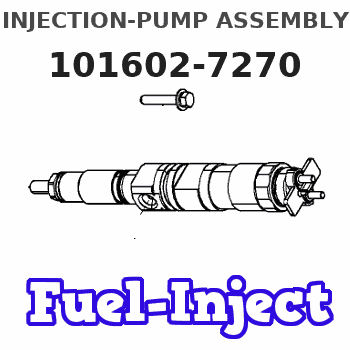
Rating:
Service parts 101602-7270 INJECTION-PUMP ASSEMBLY:
1.
_
5.
AUTOM. ADVANCE MECHANIS
6.
COUPLING PLATE
8.
_
9.
_
11.
Nozzle and Holder
5-15300-103-2
12.
Open Pre:MPa(Kqf/cm2)
14.7{150}
15.
NOZZLE SET
Include in #1:
101602-7270
as INJECTION-PUMP ASSEMBLY
Include in #2:
104741-1142
as _
Cross reference number
ZEXEL
101602-7270
1016027270
ISUZU
1156025880
1156025880
Zexel num
Bosch num
Firm num
Name
Calibration Data:
Adjustment conditions
Test oil
1404 Test oil ISO4113 or {SAEJ967d}
1404 Test oil ISO4113 or {SAEJ967d}
Test oil temperature
degC
40
40
45
Nozzle and nozzle holder
105780-8140
Bosch type code
EF8511/9A
Nozzle
105780-0000
Bosch type code
DN12SD12T
Nozzle holder
105780-2080
Bosch type code
EF8511/9
Opening pressure
MPa
17.2
Opening pressure
kgf/cm2
175
Injection pipe
Outer diameter - inner diameter - length (mm) mm 6-2-600
Outer diameter - inner diameter - length (mm) mm 6-2-600
Tester oil delivery pressure
kPa
157
157
157
Tester oil delivery pressure
kgf/cm2
1.6
1.6
1.6
Direction of rotation (viewed from drive side)
Right R
Right R
Injection timing adjustment
Direction of rotation (viewed from drive side)
Right R
Right R
Injection order
1-5-3-6-
2-4
Pre-stroke
mm
3.6
3.55
3.65
Beginning of injection position
Drive side NO.1
Drive side NO.1
Difference between angles 1
Cal 1-5 deg. 60 59.5 60.5
Cal 1-5 deg. 60 59.5 60.5
Difference between angles 2
Cal 1-3 deg. 120 119.5 120.5
Cal 1-3 deg. 120 119.5 120.5
Difference between angles 3
Cal 1-6 deg. 180 179.5 180.5
Cal 1-6 deg. 180 179.5 180.5
Difference between angles 4
Cyl.1-2 deg. 240 239.5 240.5
Cyl.1-2 deg. 240 239.5 240.5
Difference between angles 5
Cal 1-4 deg. 300 299.5 300.5
Cal 1-4 deg. 300 299.5 300.5
Injection quantity adjustment
Adjusting point
A
Rack position
8.7
Pump speed
r/min
1050
1050
1050
Average injection quantity
mm3/st.
50.6
49.6
51.6
Max. variation between cylinders
%
0
-2
2
Basic
*
Fixing the lever
*
Injection quantity adjustment_02
Adjusting point
-
Rack position
6.9+-0.5
Pump speed
r/min
360
360
360
Average injection quantity
mm3/st.
7.5
6.2
8.8
Max. variation between cylinders
%
0
-14
14
Fixing the rack
*
Remarks
Adjust only variation between cylinders; adjust governor according to governor specifications.
Adjust only variation between cylinders; adjust governor according to governor specifications.
Test data Ex:
Governor adjustment
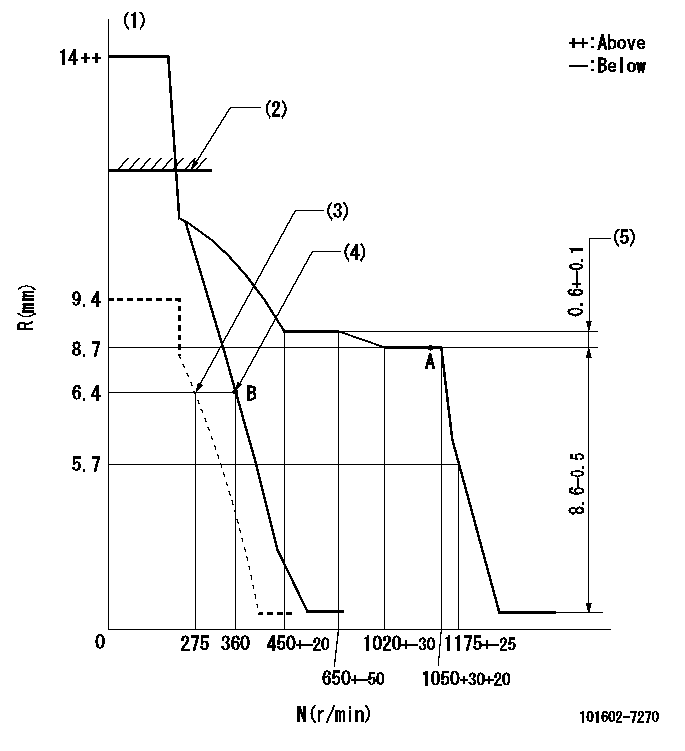
N:Pump speed
R:Rack position (mm)
(1)Target notch: K
(2)RACK LIMIT: RAL
(3)Set idle sub-spring
(4)Main spring setting
(5)Rack difference between N = N1 and N = N2
----------
K=13 RAL=13.5+-0.2mm N1=1050r/min N2=600r/min
----------
----------
K=13 RAL=13.5+-0.2mm N1=1050r/min N2=600r/min
----------
Speed control lever angle
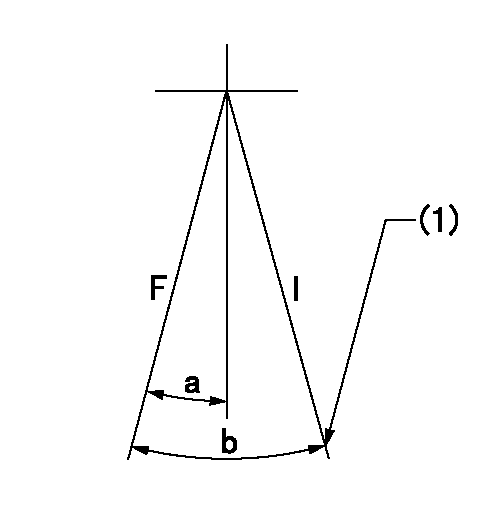
F:Full speed
I:Idle
(1)Stopper bolt setting
----------
----------
a=9deg+-5deg b=18deg+-5deg
----------
----------
a=9deg+-5deg b=18deg+-5deg
Stop lever angle
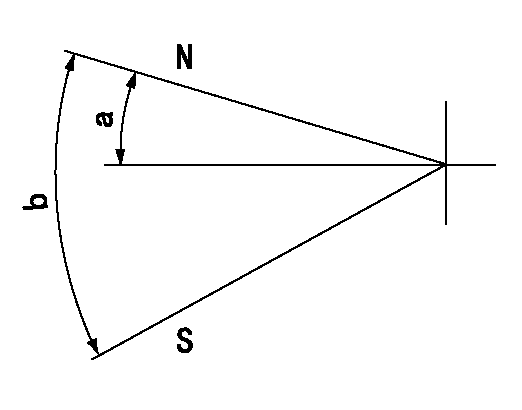
N:Pump normal
S:Stop the pump.
----------
----------
a=12deg+-5deg b=46deg+-5deg
----------
----------
a=12deg+-5deg b=46deg+-5deg
Timing setting

(1)Pump vertical direction
(2)Position of gear mark 'CC' at No 1 cylinder's beginning of injection
(3)B.T.D.C.: aa
(4)-
----------
aa=18deg
----------
a=(90deg)
----------
aa=18deg
----------
a=(90deg)
Information:
AFFECTED PRODUCT
Model Identification Number
D6R III GMT00101-00170
HCD00123-00155
TBC00100-00191
D6R III LGP DMK00130-00208
JWD00250
LGP00164-00166
WRG00158-00564
D6R III XL GJB00173-00622
JDL00113-00202
LAE00125
LFM00111-00180
D6R III XW DPS00120-00132
MRT00163-00387
D6R IIIP LGP DLM00161-00162
WCB00112-00184
D6R IIIP XL HKE00146-00221
RFC00140
D6R IIIP XW DJG00250-00251
HDC00133-00211
MTJ00151-00152
PARTS NEEDED
No parts needed for this program
ACTION REQUIRED
Please refer to the attached Rework Procedure.
OWNER NOTIFICATION
U.S. and Canadian owners will receive the attached Owner Notification.
SERVICE CLAIM ALLOWANCES
Caterpillar Dealer Suggested Customer Suggested
Parts % Labor Hrs% Parts % Labor Hrs% Parts % Labor Hrs%
100% 100% 0% 0% 0% 0%
This is a 1.0-hour job
PARTS DISPOSITION
Handle the parts in accordance with your Warranty Bulletin on warranty parts handling.
MAKE EVERY EFFORT TO COMPLETE THIS PROGRAM AS SOON AS POSSIBLE.
COPY OF OWNER NOTIFICATION FOR U.S. AND CANADIAN OWNERS
XYZ Corporation
3240 Arrow Drive
Anywhere, YZ 99999
PRIORITY - PRODUCT IMPROVEMENT PROGRAM FOR FLASHING INJECTOR ETRIM FILES
MODELS INVOLVED - CERTAIN D6R III, D6R IIIP XW, D6R IIIP LGP, D6R III LGP, D6R III XW, AND D6R III XL TRACK TYPE TRACTORS
Dear Caterpillar Product Owner:
New injector etrim files need to be installed on the products listed below. The upgraded files will help performance and stability of your D6R engine. You will not be charged for the service performed.
Contact your local Caterpillar dealer immediately to schedule this service. The dealer will advise you of the time required to complete this service.
Please refer the dealer to their Service Letter dated 31Aug2006 when scheduling this service.
We regret the inconvenience this may cause you, but urge you to have this service performed as soon as possible to prevent unscheduled downtime.
Caterpillar Inc.
Identification #(s)
Attached to 31Aug2006 Service Letter
Rework Procedure
Field Rework Procedure
1. Using the provided machine serial number of the D6R Series III tractor in your service area, go to TMI web and look up the engine serial number.
2. Look up your engine serial number on the Excell file emailed to all machine TCs in order to access the injector serial numbers. If you don't have a copy of this file go the the Knowledge Network to get the file from the following web address: https://kn.cat.com/message.cfm?id=4388&parent=153301&type=Broadcast
3. Copy the 6 injector serial numbers for each machine in your service area and go to SIS web.
4. At the main menu click on Service Software Files.
5. Follow the directions and down load the trim file for each injector, putting them on a disk or in a file that can be accessed from ET.
6. Down load the six trim files for the injectors and program into the ECM in the correct order, using ET.
7. Make sure the machine SN and /or engine SN are included in the service letter claim