Information injection-pump assembly
BOSCH
9 400 613 290
9400613290
ZEXEL
101602-5061
1016025061
HINO
220206081A
220206081a
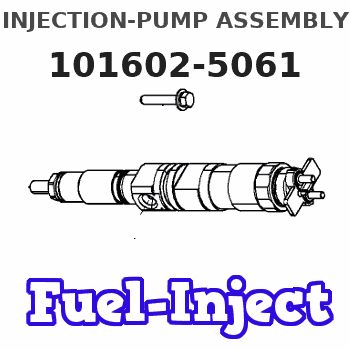
Rating:
Service parts 101602-5061 INJECTION-PUMP ASSEMBLY:
1.
_
5.
AUTOM. ADVANCE MECHANIS
8.
_
9.
_
11.
Nozzle and Holder
236003600A
12.
Open Pre:MPa(Kqf/cm2)
21.6{220}
15.
NOZZLE SET
Include in #1:
101602-5061
as INJECTION-PUMP ASSEMBLY
Include in #2:
104749-1900
as _
Cross reference number
BOSCH
9 400 613 290
9400613290
ZEXEL
101602-5061
1016025061
HINO
220206081A
220206081a
Zexel num
Bosch num
Firm num
Name
101602-5061
9 400 613 290
220206081A HINO
INJECTION-PUMP ASSEMBLY
J08C-T K 14BN INJECTION PUMP ASSY PE
J08C-T K 14BN INJECTION PUMP ASSY PE
Calibration Data:
Adjustment conditions
Test oil
1404 Test oil ISO4113 or {SAEJ967d}
1404 Test oil ISO4113 or {SAEJ967d}
Test oil temperature
degC
40
40
45
Nozzle and nozzle holder
105780-8140
Bosch type code
EF8511/9A
Nozzle
105780-0000
Bosch type code
DN12SD12T
Nozzle holder
105780-2080
Bosch type code
EF8511/9
Opening pressure
MPa
17.2
Opening pressure
kgf/cm2
175
Injection pipe
Outer diameter - inner diameter - length (mm) mm 6-2-600
Outer diameter - inner diameter - length (mm) mm 6-2-600
Overflow valve
131425-0620
Overflow valve opening pressure
kPa
255
221
289
Overflow valve opening pressure
kgf/cm2
2.6
2.25
2.95
Tester oil delivery pressure
kPa
255
255
255
Tester oil delivery pressure
kgf/cm2
2.6
2.6
2.6
Direction of rotation (viewed from drive side)
Left L
Left L
Injection timing adjustment
Direction of rotation (viewed from drive side)
Left L
Left L
Injection order
1-4-2-6-
3-5
Pre-stroke
mm
3.8
3.77
3.83
Beginning of injection position
Governor side NO.1
Governor side NO.1
Difference between angles 1
Cal 1-4 deg. 60 59.75 60.25
Cal 1-4 deg. 60 59.75 60.25
Difference between angles 2
Cyl.1-2 deg. 120 119.75 120.25
Cyl.1-2 deg. 120 119.75 120.25
Difference between angles 3
Cal 1-6 deg. 180 179.75 180.25
Cal 1-6 deg. 180 179.75 180.25
Difference between angles 4
Cal 1-3 deg. 240 239.75 240.25
Cal 1-3 deg. 240 239.75 240.25
Difference between angles 5
Cal 1-5 deg. 300 299.75 300.25
Cal 1-5 deg. 300 299.75 300.25
Injection quantity adjustment
Adjusting point
A
Rack position
8.7
Pump speed
r/min
750
750
750
Average injection quantity
mm3/st.
99
97
101
Max. variation between cylinders
%
0
-3.5
3.5
Basic
*
Fixing the rack
*
Boost pressure
kPa
28
28
Boost pressure
mmHg
210
210
Injection quantity adjustment_02
Adjusting point
B
Rack position
8.6
Pump speed
r/min
900
900
900
Average injection quantity
mm3/st.
96
93
99
Fixing the rack
*
Boost pressure
kPa
28
28
Boost pressure
mmHg
210
210
Injection quantity adjustment_03
Adjusting point
D
Rack position
6.5+-0.5
Pump speed
r/min
360
360
360
Average injection quantity
mm3/st.
12.5
11.5
13.5
Max. variation between cylinders
%
0
-10
10
Fixing the rack
*
Boost pressure
kPa
0
0
0
Boost pressure
mmHg
0
0
0
Boost compensator adjustment
Pump speed
r/min
600
600
600
Rack position
R1-0.4
Boost pressure
kPa
6.7
6.7
10
Boost pressure
mmHg
50
50
75
Boost compensator adjustment_02
Pump speed
r/min
600
600
600
Rack position
R1(9.1)
Boost pressure
kPa
14.7
14.7
14.7
Boost pressure
mmHg
110
110
110
Test data Ex:
Governor adjustment
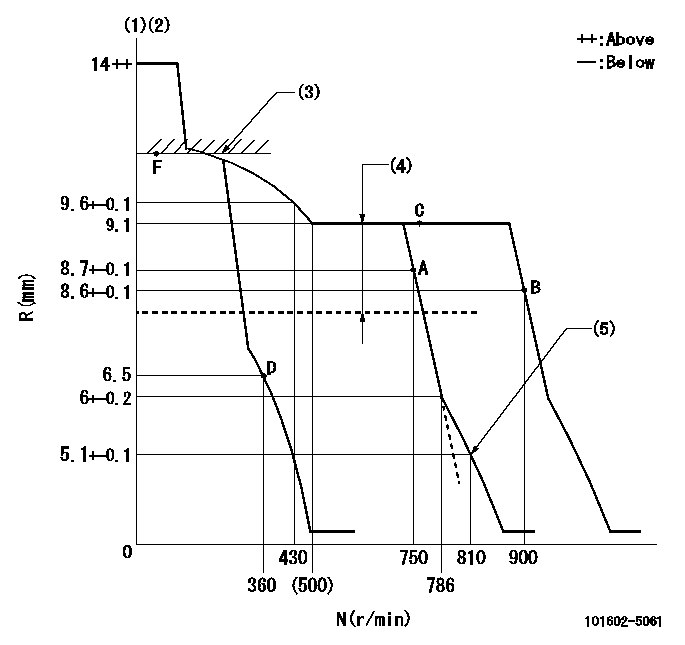
N:Pump speed
R:Rack position (mm)
(1)Target notch: K
(2)Tolerance for racks not indicated: +-0.05mm.
(3)Boost compensator excessive fuel lever at operation: L1 (at 0 boost pressure)
(4)Boost compensator stroke: BCL
(5)Set idle sub-spring
----------
K=12 L1=10.6+-0.1mm BCL=0.4+-0.1mm
----------
----------
K=12 L1=10.6+-0.1mm BCL=0.4+-0.1mm
----------
Speed control lever angle
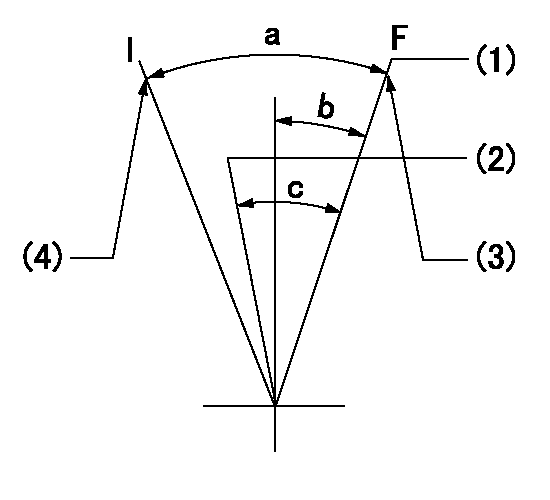
F:Full speed
I:Idle
(1)Set the pump speed at aa
(2)When pump speed set at bb
(3)Stopper bolt setting
(4)Stopper bolt setting
----------
aa=900r/min bb=750r/min
----------
a=22deg+-5deg b=0deg+-5deg c=6deg+-5deg
----------
aa=900r/min bb=750r/min
----------
a=22deg+-5deg b=0deg+-5deg c=6deg+-5deg
Stop lever angle
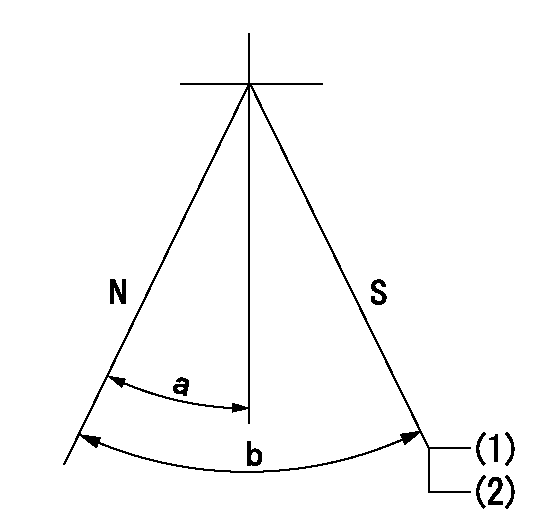
N:Pump normal
S:Stop the pump.
(1)Normal stop
(2)Rack position aa or less, pump speed bb
----------
aa=6mm bb=0r/min
----------
a=19deg+-5deg b=53deg+-5deg
----------
aa=6mm bb=0r/min
----------
a=19deg+-5deg b=53deg+-5deg
0000001101
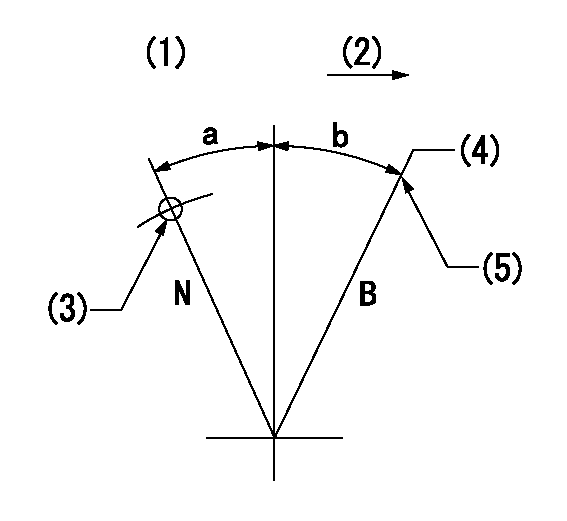
N:Normal
B:When boosted
(1)(at boost pressure = aa)
(2)Drive side
(3)Use the hole at R = bb
(4)Rack position = cc
(5)Stopper bolt setting
----------
aa=0kPa(0mmHg) bb=30mm cc=10.6+-0.1mm
----------
a=(11deg) b=(4deg)
----------
aa=0kPa(0mmHg) bb=30mm cc=10.6+-0.1mm
----------
a=(11deg) b=(4deg)
Timing setting

(1)Pump vertical direction
(2)Coupling's key groove position at No 1 cylinder's beginning of injection
(3)-
(4)-
----------
----------
a=(20deg)
----------
----------
a=(20deg)
Information:
ACTION REQUIRED
Take the following actions before or after a failure occurs on one or more injectors in any of the machines listed in this service letter.
- If one or more injectors fail it may be necessary to replace up to 6 injectors at the time of repair.
There will be situations when all 6 injectors do not have to be replaced. Refer to next paragraph to determine which injectors should be replaced.
- If an injector repair has previously been performed after approximately 01Oct07 on any of the listed machines, only the injectors that were not replaced at that time should be replaced. This should further be verified by comparing the injector serial numbers in the engine to a range of 3B115776403B to 3B11676551F9. Disregard the first and last two characters in the serial number (in this case "3B" and "3B" in the first serial number and "3B" and "F9" in the second serial number). The reason for verifying the serial number range is due to a batch change of the internal part that is failing. The change was made after serial number 3B11676551F9.
Only injectors falling within the range of 11577640-11676551 should be replaced.
- If the suspect injector can not be identified by using the automatic cylinder cutout test use the two methods below.
- First, run a manual cylinder cutout test at a high engine speed with some load on the engine. When the injector that has failed is cutout, the sound of the engine should be more normal as opposed to the loud knocking heard when the failed injector is active. The second method is to unplug the wiring harness at the valve cover base that sends current to the injector solenoids as well as the harness connection for the injection actuation pressure sensor. By making these disconnections, the fuel injectors will not fire and the HEUI pump will go to maximum actuation pressure. Then remove the valve cover and crank the engine. The injectors that have failed should expel more oil (from the HEUI System) than those that are not failed.
-Refer to RENR9579 for removal/install procedure of the unit injector.
-The serial number of all injectors replaced in a machine covered under this service letter must be documented in the claims story.
SERVICE CLAIM ALLOWANCES
Product smu/age
Have questions with 101602-5061?
Group cross 101602-5061 ZEXEL
Hino
101602-5061
9 400 613 290
220206081A
INJECTION-PUMP ASSEMBLY
J08C-T
J08C-T