Information injection-pump assembly
BOSCH
9 400 612 203
9400612203
ZEXEL
101602-5060
1016025060
HINO
220206080A
220206080a

Rating:
Service parts 101602-5060 INJECTION-PUMP ASSEMBLY:
1.
_
5.
AUTOM. ADVANCE MECHANIS
6.
COUPLING PLATE
8.
_
9.
_
11.
Nozzle and Holder
23600-3410A
12.
Open Pre:MPa(Kqf/cm2)
16.7{170}/21.6{220}
14.
NOZZLE
Include in #1:
101602-5060
as INJECTION-PUMP ASSEMBLY
Include in #2:
104749-1880
as _
Cross reference number
BOSCH
9 400 612 203
9400612203
ZEXEL
101602-5060
1016025060
HINO
220206080A
220206080a
Zexel num
Bosch num
Firm num
Name
Calibration Data:
Adjustment conditions
Test oil
1404 Test oil ISO4113 or {SAEJ967d}
1404 Test oil ISO4113 or {SAEJ967d}
Test oil temperature
degC
40
40
45
Nozzle and nozzle holder
105780-8140
Bosch type code
EF8511/9A
Nozzle
105780-0000
Bosch type code
DN12SD12T
Nozzle holder
105780-2080
Bosch type code
EF8511/9
Opening pressure
MPa
17.2
Opening pressure
kgf/cm2
175
Injection pipe
Outer diameter - inner diameter - length (mm) mm 6-2-600
Outer diameter - inner diameter - length (mm) mm 6-2-600
Overflow valve
131425-0620
Overflow valve opening pressure
kPa
255
221
289
Overflow valve opening pressure
kgf/cm2
2.6
2.25
2.95
Tester oil delivery pressure
kPa
255
255
255
Tester oil delivery pressure
kgf/cm2
2.6
2.6
2.6
Direction of rotation (viewed from drive side)
Left L
Left L
Injection timing adjustment
Direction of rotation (viewed from drive side)
Left L
Left L
Injection order
1-4-2-6-
3-5
Pre-stroke
mm
3.8
3.77
3.83
Beginning of injection position
Governor side NO.1
Governor side NO.1
Difference between angles 1
Cal 1-4 deg. 60 59.75 60.25
Cal 1-4 deg. 60 59.75 60.25
Difference between angles 2
Cyl.1-2 deg. 120 119.75 120.25
Cyl.1-2 deg. 120 119.75 120.25
Difference between angles 3
Cal 1-6 deg. 180 179.75 180.25
Cal 1-6 deg. 180 179.75 180.25
Difference between angles 4
Cal 1-3 deg. 240 239.75 240.25
Cal 1-3 deg. 240 239.75 240.25
Difference between angles 5
Cal 1-5 deg. 300 299.75 300.25
Cal 1-5 deg. 300 299.75 300.25
Injection quantity adjustment
Adjusting point
A
Rack position
9.1
Pump speed
r/min
750
750
750
Average injection quantity
mm3/st.
107.5
105.5
109.5
Max. variation between cylinders
%
0
-3.5
3.5
Basic
*
Fixing the rack
*
Boost pressure
kPa
133
133
Boost pressure
mmHg
1000
1000
Injection quantity adjustment_02
Adjusting point
B
Rack position
8.9
Pump speed
r/min
900
900
900
Average injection quantity
mm3/st.
103
100
106
Fixing the rack
*
Boost pressure
kPa
133
133
Boost pressure
mmHg
1000
1000
Injection quantity adjustment_03
Adjusting point
D
Rack position
6.5+-0.5
Pump speed
r/min
360
360
360
Average injection quantity
mm3/st.
10
9
11
Max. variation between cylinders
%
0
-10
10
Fixing the rack
*
Boost pressure
kPa
0
0
0
Boost pressure
mmHg
0
0
0
Boost compensator adjustment
Pump speed
r/min
600
600
600
Rack position
R1-1.8
Boost pressure
kPa
66.7
64
69.4
Boost pressure
mmHg
500
480
520
Boost compensator adjustment_02
Pump speed
r/min
600
600
600
Rack position
R1(9.3)
Boost pressure
kPa
120
120
120
Boost pressure
mmHg
900
900
900
Test data Ex:
Governor adjustment
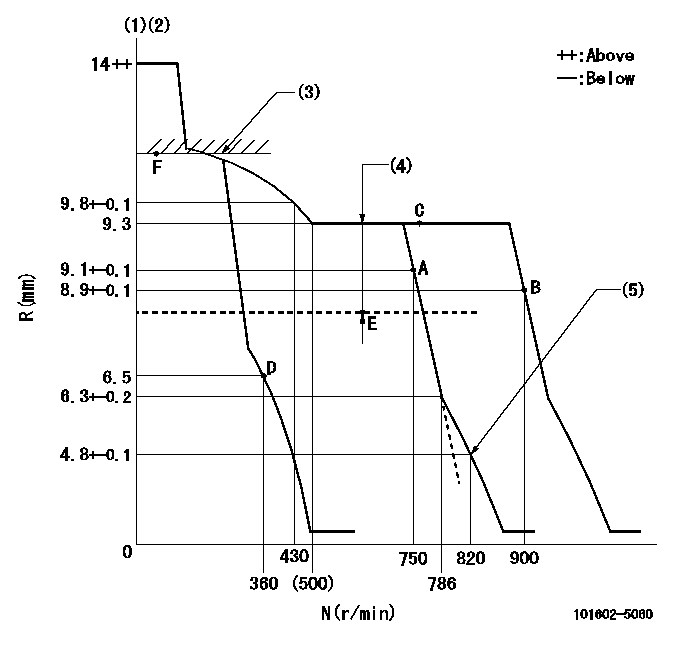
N:Pump speed
R:Rack position (mm)
(1)Target notch: K
(2)Tolerance for racks not indicated: +-0.05mm.
(3)Boost compensator excessive fuel lever at operation: L1 (at 0 boost pressure)
(4)Boost compensator stroke: BCL
(5)Set idle sub-spring
----------
K=11 L1=10.5+-0.1mm BCL=1.8+-0.1mm
----------
----------
K=11 L1=10.5+-0.1mm BCL=1.8+-0.1mm
----------
Speed control lever angle
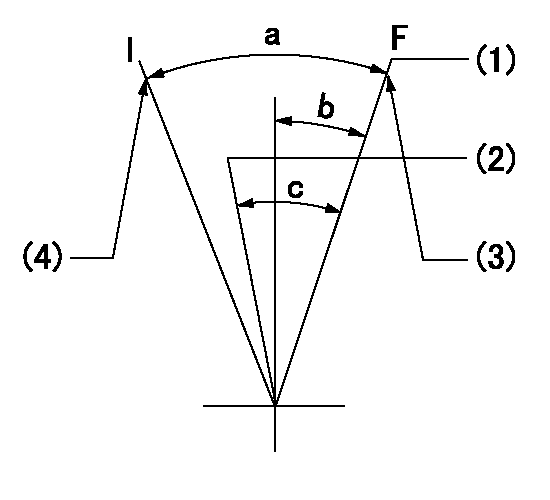
F:Full speed
I:Idle
(1)Set the pump speed at aa
(2)When pump speed set at bb
(3)Stopper bolt setting
(4)Stopper bolt setting
----------
aa=900r/min bb=750r/min
----------
a=22deg+-5deg b=1deg+-5deg c=6deg+-5deg
----------
aa=900r/min bb=750r/min
----------
a=22deg+-5deg b=1deg+-5deg c=6deg+-5deg
Stop lever angle
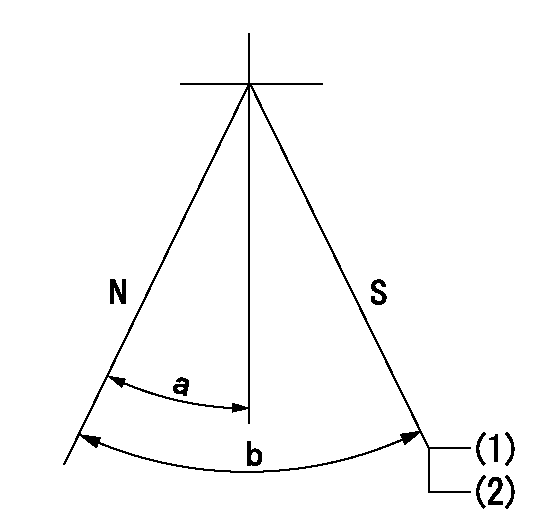
N:Pump normal
S:Stop the pump.
(1)Normal stop
(2)Rack position aa or less, pump speed bb
----------
aa=6mm bb=0r/min
----------
a=19deg+-5deg b=53deg+-5deg
----------
aa=6mm bb=0r/min
----------
a=19deg+-5deg b=53deg+-5deg
0000001101
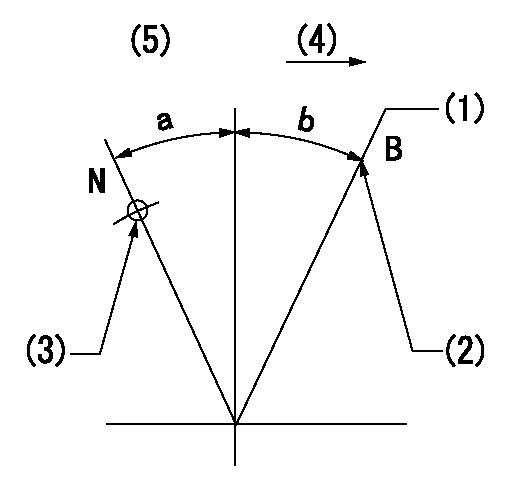
N:Normal
B:When boosted
(1)Rack position = aa
(2)Stopper bolt setting
(3)Use the hole at R = bb
(4)Drive side
(5)At boost pressure = cc
----------
aa=10.5+-0.1mm bb=30mm cc=0kPa(0mmHg)
----------
a=(11deg) b=(5deg)
----------
aa=10.5+-0.1mm bb=30mm cc=0kPa(0mmHg)
----------
a=(11deg) b=(5deg)
Timing setting

(1)Pump vertical direction
(2)Coupling's key groove position at No 1 cylinder's beginning of injection
(3)-
(4)-
----------
----------
a=(20deg)
----------
----------
a=(20deg)
Information:
This is a 1.5-hour job for Group 2
1) An additional allowance of 4.0 hours can be claimed if the pump needs to be replaced after failing inspection.
2) Should the Dealer not have access to a Bore Scope an allowance of $250 per Dealer is allowed for the purchase of this tool.
PARTS DISPOSITION
Handle the parts in accordance with your Warranty Bulletin on warranty parts handling.
For NACD
Caterpillar Inc.
Attn: Supplier Recovery
Service Claims Room
8201 N. University
Peoria, IL 61615
MAKE EVERY EFFORT TO COMPLETE THIS PROGRAM AS SOON AS POSSIBLE.
COPY OF OWNER NOTIFICATION FOR U.S. AND CANADIAN OWNERS
XYZ Corporation
3240 Arrow Drive
Anywhere, YZ 99999
SAFETY - PRODUCT IMPROVEMENT PROGRAM FOR THE INSPECTION AND POSSIBLE REPLACEMENT OF THE FUEL INJECTION PUMP ON CERTAIN TURBOCHARGED 414E, 416E, 420E, AND 430E BACKHOE LOADERS
MODELS INVOLVED - 414E, 416E, 420E, 430E
Dear Caterpillar Product Owner:
The Fuel Injection Pump needs to be inspected and possibly replaced on the products listed below. The existing Fuel Injection Pump can cause an unexpected increase in engine speed which may result in personal injury or death.
You will not be charged for the service performed.
Contact your local Caterpillar dealer immediately to schedule this service. The dealer will advise you of the time required to complete this service.
Please refer the dealer to their Service Letter dated 08May2008 when scheduling this service.
We regret the inconvenience this may cause you, but urge you to have this service performed for your added safety and satisfaction.
Caterpillar Inc.
Identification #(s)
Attached to 08May2008 Service Letter
Rework Procedure
Tools required for the inspection of the fuel injection pump are:
17 mm hexagonal socket 3/8" drive.
3/8" drive ratchet wrench with 300 mm extension
Bore Scope with flexible end and ninety degree viewing lens. The Bore Scope has to be capable of being inserted in a 10 mm diameter hole. A 6 mm Bore Scope is recommended for optimium viewing.
1) Before proceeding, first check the serial number shown on the pump identification plate. Image 1.1.1
Image1.1.1
If the machine is identified in the Affected Product and the fuel pump serial number ends with the letter "B" as indicated in image 1.1.1 then the fuel pump should be further inspected.
2) Remove engine compartment door by removing the three bolts holding the door in place using a 13 mm ratchet and socket. Pull the rear of the door away from the machine and then pull the door towards the rear of the machine to remove it from the radiator guard. Image 1.2.1
Image1.2.1
3) Record pump and engine serial number.
Only carry out the following procedure if the pump type number is identified with the "B". (The pumps without the "B" are not affected by this problem).
4) Ensure the area around the fuel return connection is clean. The connection is on the top of the fuel pump toward the front of the engine. Image 1.3.1
Image1.3.1
5) Use a 17 mm X 3/8" drive hexagonal socket, extension 3/8" x 3/8" x 300 mm length and ratchet wrench 3/8" drive to release and remove the return connection fitting.
Note: Be careful not to damage the fitting and o-rings (image 1.4.1), and ensure nothing is