Information injection-pump assembly
BOSCH
9 400 610 582
9400610582
ZEXEL
101602-4670
1016024670
ISUZU
1156020740
1156020740
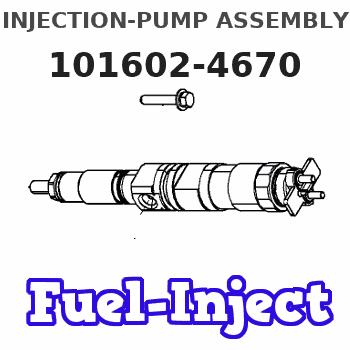
Rating:
Service parts 101602-4670 INJECTION-PUMP ASSEMBLY:
1.
_
5.
AUTOM. ADVANCE MECHANIS
7.
COUPLING PLATE
8.
_
9.
_
11.
Nozzle and Holder
1-15300-161-1
12.
Open Pre:MPa(Kqf/cm2)
22.1{225}
15.
NOZZLE SET
Include in #1:
101602-4670
as INJECTION-PUMP ASSEMBLY
Include in #2:
104740-1081
as _
Cross reference number
BOSCH
9 400 610 582
9400610582
ZEXEL
101602-4670
1016024670
ISUZU
1156020740
1156020740
Zexel num
Bosch num
Firm num
Name
101602-4670
9 400 610 582
1156020740 ISUZU
INJECTION-PUMP ASSEMBLY
6SA1T * K 14BF PE6AD PE
6SA1T * K 14BF PE6AD PE
Calibration Data:
Adjustment conditions
Test oil
1404 Test oil ISO4113 or {SAEJ967d}
1404 Test oil ISO4113 or {SAEJ967d}
Test oil temperature
degC
40
40
45
Nozzle and nozzle holder
105780-8140
Bosch type code
EF8511/9A
Nozzle
105780-0000
Bosch type code
DN12SD12T
Nozzle holder
105780-2080
Bosch type code
EF8511/9
Opening pressure
MPa
17.2
Opening pressure
kgf/cm2
175
Injection pipe
Outer diameter - inner diameter - length (mm) mm 6-2-600
Outer diameter - inner diameter - length (mm) mm 6-2-600
Overflow valve opening pressure
kPa
157
123
191
Overflow valve opening pressure
kgf/cm2
1.6
1.25
1.95
Tester oil delivery pressure
kPa
157
157
157
Tester oil delivery pressure
kgf/cm2
1.6
1.6
1.6
Direction of rotation (viewed from drive side)
Left L
Left L
Injection timing adjustment
Direction of rotation (viewed from drive side)
Left L
Left L
Injection order
1-5-3-6-
2-4
Pre-stroke
mm
4.7
4.65
4.75
Beginning of injection position
Governor side NO.1
Governor side NO.1
Difference between angles 1
Cal 1-5 deg. 60 59.5 60.5
Cal 1-5 deg. 60 59.5 60.5
Difference between angles 2
Cal 1-3 deg. 120 119.5 120.5
Cal 1-3 deg. 120 119.5 120.5
Difference between angles 3
Cal 1-6 deg. 180 179.5 180.5
Cal 1-6 deg. 180 179.5 180.5
Difference between angles 4
Cyl.1-2 deg. 240 239.5 240.5
Cyl.1-2 deg. 240 239.5 240.5
Difference between angles 5
Cal 1-4 deg. 300 299.5 300.5
Cal 1-4 deg. 300 299.5 300.5
Injection quantity adjustment
Adjusting point
A
Rack position
8.9
Pump speed
r/min
1050
1050
1050
Average injection quantity
mm3/st.
94.2
93.2
95.2
Max. variation between cylinders
%
0
-2.5
2.5
Basic
*
Fixing the lever
*
Injection quantity adjustment_02
Adjusting point
B
Rack position
5.6+-0.5
Pump speed
r/min
425
425
425
Average injection quantity
mm3/st.
11
9
13
Max. variation between cylinders
%
0
-14
14
Fixing the rack
*
Test data Ex:
Governor adjustment
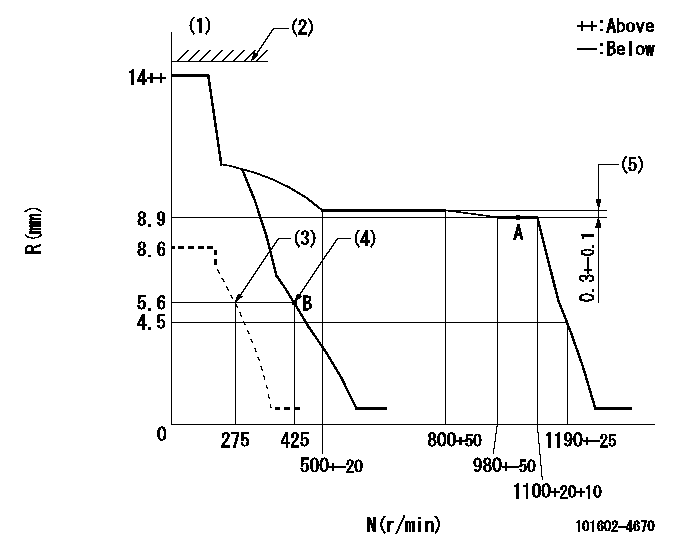
N:Pump speed
R:Rack position (mm)
(1)Target notch: K
(2)RACK LIMIT not operating.
(3)Set idle sub-spring
(4)Main spring setting
(5)Rack difference between N = N1 and N = N2
----------
K=11 N1=1050r/min N2=800r/min
----------
----------
K=11 N1=1050r/min N2=800r/min
----------
Speed control lever angle

F:Full speed
I:Idle
(1)Stopper bolt setting
----------
----------
a=8deg+-5deg b=24deg+-5deg
----------
----------
a=8deg+-5deg b=24deg+-5deg
Stop lever angle
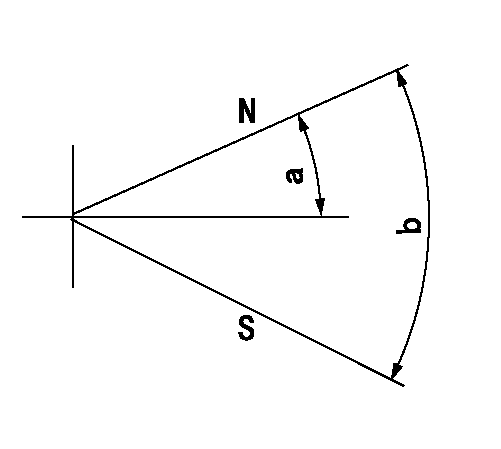
N:Pump normal
S:Stop the pump.
----------
----------
a=19deg+-5deg b=53deg+-5deg
----------
----------
a=19deg+-5deg b=53deg+-5deg
Timing setting

(1)Pump vertical direction
(2)Position of coupling's threaded hole at No 1 cylinder's beginning of injection
(3)B.T.D.C.: aa
(4)-
----------
aa=20deg
----------
a=(40deg)
----------
aa=20deg
----------
a=(40deg)
Information:
* Be sure to orient the oil grooves as indicated above, otherwise seizures may occur in the engine.
* Use oversize thrust plates when adjusting the crankshaft end play. The upper and lower thrust plates on the same side must be of the same size. The thrust plates on one side may differ in size from those on the other side. Installation: Main bearings
* The upper main bearing has an oil hole while the lower main bearing does not. Do not confuse the two, as incorrect installation can cause seizures in the engine.
* Select and use a main bearing set of a thickness that can accommodate the inside diameter of each main bearing fitting hole between the upper crankcase and lower crankcase and the diameter of the corresponding crankshaft journal. Select the appropriate main bearing set by one of the two following methods.(1) Measurement based selection* Mount the upper crankcase on the lower crankcase without fitting main bearings. * Tighten the main cap bolts to 20 N m {2.0 kgf m}.* Measure the inside diameter of the main bearing fitting hole between the upper crankcase and lower crankcase (vertically from one point), and the diameter of the crankshaft journal (vertically or horizontally from one point).* Select a main bearing set that matches the measurements from the table below. If the color identification mark is indiscernible, measure the thickness of the bearing walls and use the measurements in its place. (Unit: mm) (2) Color identification mark based method* The crankshaft, upper crankcase, and main bearing can be appropriately combined in the following ways according to their color identification marks: No. 1: Position of color identification mark on No. 1 journalNo. 2: Position of color identification mark on No. 2 journalNo. 3: Position of color identification mark on No. 3 journalNo. 4: Position of color identification mark on No. 4 journalNo. 5: Position of color identification mark on No. 5 journal Installation: Lower crankcase
* Before installing the main cap bolt, check the punch marks on each bolt's head. (Bolts with one or two punch marks can be reused.)* The punch marks indicate the number of times each main cap bolt has been tightened using the torque-turn tightening method. Any main cap bolt that already has three punch marks must be replaced.
* Clean the sealant application surfaces of each part. * Apply a bead of sealant to the upper crankcase evenly and without any breaks as shown in the illustration.* Install the lower crankcase within three minutes of applying the sealant to the upper crankcase, being careful not to dislodge the sealant.* Apply engine oil to the threads and seating surface under the head of each of the main cap bolts, and tighten the bolts to a torque of 20 N m {2.0 kgf m} in the order indicated in the illustration (1 to 10). * Then, tighten the main cap bolts further by 90 degrees in the same order.* Tighten them by another 90 degrees in the same order.* After completing
* Use oversize thrust plates when adjusting the crankshaft end play. The upper and lower thrust plates on the same side must be of the same size. The thrust plates on one side may differ in size from those on the other side. Installation: Main bearings
* The upper main bearing has an oil hole while the lower main bearing does not. Do not confuse the two, as incorrect installation can cause seizures in the engine.
* Select and use a main bearing set of a thickness that can accommodate the inside diameter of each main bearing fitting hole between the upper crankcase and lower crankcase and the diameter of the corresponding crankshaft journal. Select the appropriate main bearing set by one of the two following methods.(1) Measurement based selection* Mount the upper crankcase on the lower crankcase without fitting main bearings. * Tighten the main cap bolts to 20 N m {2.0 kgf m}.* Measure the inside diameter of the main bearing fitting hole between the upper crankcase and lower crankcase (vertically from one point), and the diameter of the crankshaft journal (vertically or horizontally from one point).* Select a main bearing set that matches the measurements from the table below. If the color identification mark is indiscernible, measure the thickness of the bearing walls and use the measurements in its place. (Unit: mm) (2) Color identification mark based method* The crankshaft, upper crankcase, and main bearing can be appropriately combined in the following ways according to their color identification marks: No. 1: Position of color identification mark on No. 1 journalNo. 2: Position of color identification mark on No. 2 journalNo. 3: Position of color identification mark on No. 3 journalNo. 4: Position of color identification mark on No. 4 journalNo. 5: Position of color identification mark on No. 5 journal Installation: Lower crankcase
* Before installing the main cap bolt, check the punch marks on each bolt's head. (Bolts with one or two punch marks can be reused.)* The punch marks indicate the number of times each main cap bolt has been tightened using the torque-turn tightening method. Any main cap bolt that already has three punch marks must be replaced.
* Clean the sealant application surfaces of each part. * Apply a bead of sealant to the upper crankcase evenly and without any breaks as shown in the illustration.* Install the lower crankcase within three minutes of applying the sealant to the upper crankcase, being careful not to dislodge the sealant.* Apply engine oil to the threads and seating surface under the head of each of the main cap bolts, and tighten the bolts to a torque of 20 N m {2.0 kgf m} in the order indicated in the illustration (1 to 10). * Then, tighten the main cap bolts further by 90 degrees in the same order.* Tighten them by another 90 degrees in the same order.* After completing
Have questions with 101602-4670?
Group cross 101602-4670 ZEXEL
Isuzu
101602-4670
9 400 610 582
1156020740
INJECTION-PUMP ASSEMBLY
6SA1T
6SA1T