Information injection-pump assembly
BOSCH
9 400 614 845
9400614845
ZEXEL
101602-4620
1016024620
ISUZU
1156021040
1156021040
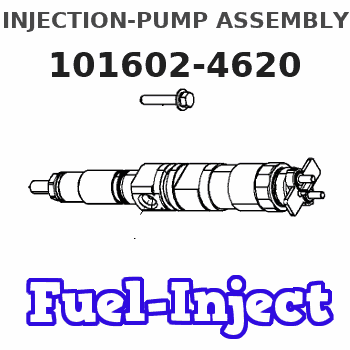
Rating:
Service parts 101602-4620 INJECTION-PUMP ASSEMBLY:
1.
_
5.
AUTOM. ADVANCE MECHANIS
8.
_
9.
_
11.
Nozzle and Holder
5-15300-089-1
12.
Open Pre:MPa(Kqf/cm2)
18.1(185)
15.
NOZZLE SET
Include in #1:
101602-4620
as INJECTION-PUMP ASSEMBLY
Include in #2:
104749-1370
as _
Cross reference number
BOSCH
9 400 614 845
9400614845
ZEXEL
101602-4620
1016024620
ISUZU
1156021040
1156021040
Zexel num
Bosch num
Firm num
Name
101602-4620
9 400 614 845
1156021040 ISUZU
INJECTION-PUMP ASSEMBLY
6BD1 * K 14BE PE6A PE
6BD1 * K 14BE PE6A PE
Calibration Data:
Adjustment conditions
Test oil
1404 Test oil ISO4113 or {SAEJ967d}
1404 Test oil ISO4113 or {SAEJ967d}
Test oil temperature
degC
40
40
45
Nozzle and nozzle holder
105780-8140
Bosch type code
EF8511/9A
Nozzle
105780-0000
Bosch type code
DN12SD12T
Nozzle holder
105780-2080
Bosch type code
EF8511/9
Opening pressure
MPa
17.2
Opening pressure
kgf/cm2
175
Injection pipe
Outer diameter - inner diameter - length (mm) mm 6-2-600
Outer diameter - inner diameter - length (mm) mm 6-2-600
Overflow valve opening pressure
kPa
157
123
191
Overflow valve opening pressure
kgf/cm2
1.6
1.25
1.95
Tester oil delivery pressure
kPa
157
157
157
Tester oil delivery pressure
kgf/cm2
1.6
1.6
1.6
Direction of rotation (viewed from drive side)
Right R
Right R
Injection timing adjustment
Direction of rotation (viewed from drive side)
Right R
Right R
Injection order
1-5-3-6-
2-4
Pre-stroke
mm
3.6
3.55
3.65
Beginning of injection position
Drive side NO.1
Drive side NO.1
Difference between angles 1
Cal 1-5 deg. 60 59.5 60.5
Cal 1-5 deg. 60 59.5 60.5
Difference between angles 2
Cal 1-3 deg. 120 119.5 120.5
Cal 1-3 deg. 120 119.5 120.5
Difference between angles 3
Cal 1-6 deg. 180 179.5 180.5
Cal 1-6 deg. 180 179.5 180.5
Difference between angles 4
Cyl.1-2 deg. 240 239.5 240.5
Cyl.1-2 deg. 240 239.5 240.5
Difference between angles 5
Cal 1-4 deg. 300 299.5 300.5
Cal 1-4 deg. 300 299.5 300.5
Injection quantity adjustment
Adjusting point
A
Rack position
8.9
Pump speed
r/min
800
800
800
Average injection quantity
mm3/st.
56.5
55
58
Max. variation between cylinders
%
0
-2
2
Basic
*
Fixing the lever
*
Injection quantity adjustment_02
Adjusting point
B
Rack position
8.6
Pump speed
r/min
1400
1400
1400
Average injection quantity
mm3/st.
58.8
56.8
60.8
Max. variation between cylinders
%
0
-4
4
Fixing the lever
*
Injection quantity adjustment_03
Adjusting point
-
Rack position
6.5+-0.5
Pump speed
r/min
325
325
325
Average injection quantity
mm3/st.
9.4
8
10.8
Max. variation between cylinders
%
0
-14
14
Fixing the rack
*
Remarks
Adjust only variation between cylinders; adjust governor according to governor specifications.
Adjust only variation between cylinders; adjust governor according to governor specifications.
Test data Ex:
Governor adjustment
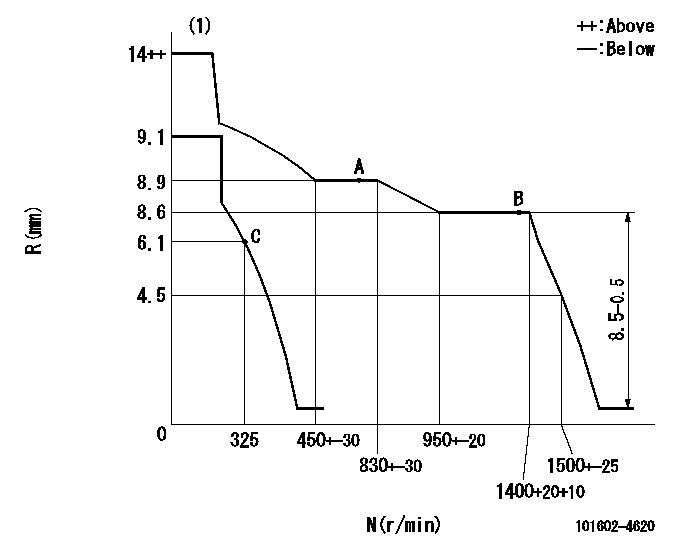
N:Pump speed
R:Rack position (mm)
(1)Target notch: K
----------
K=5
----------
----------
K=5
----------
Speed control lever angle

F:Full speed
I:Idle
(1)Stopper bolt setting
----------
----------
a=8deg+-5deg b=33deg+-5deg
----------
----------
a=8deg+-5deg b=33deg+-5deg
Stop lever angle
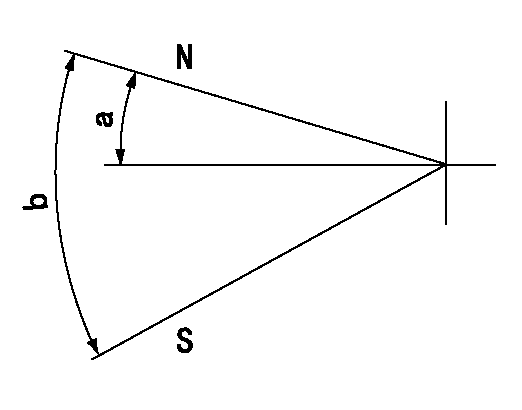
N:Pump normal
S:Stop the pump.
----------
----------
a=12deg+-5deg b=46deg+-5deg
----------
----------
a=12deg+-5deg b=46deg+-5deg
Timing setting
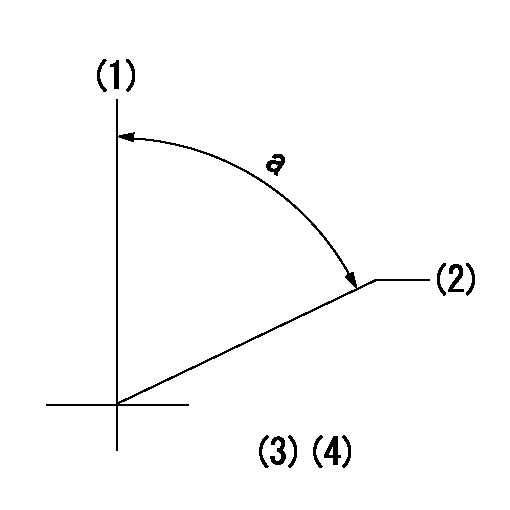
(1)Pump vertical direction
(2)Position of flywheel's threaded hole at No 1 cylinder's beginning of injection
(3)-
(4)-
----------
----------
a=(60deg)
----------
----------
a=(60deg)
Information:
Removing And Fitting A Starter Gear Ring
It is assumed that the flywheel is dismantled.Removing:
6-1Cut through the starter gear ring with a hard chisel and remove.Fig. 6-1Refitting:
1. Heat the starter gear ring to a temperature of 120 deg. C. Place the starter gear ring with the bevelled side of the teeth facing away from flywheel.
6-22. Locate the starter gear ring on the flywheel and tap it into position so that it seats against the shoulder.Fig. 6-2Removing And Fitting A Radial Sealing Ring On The Flywheel Side
It is assumed that the flywheel has been dismantled. Removing:
6-3Apply puller No. 142700 and draw off radial sealing ring.Fig. 6-3Refitting:
6-41. Mount guide-piece of device onto crankshaft.Fig. 6-4
6-52. Lightly grease the sealing lip of the new radial seal. Place seal on guide-piece with lip facing towards crankcase and press in with device No. 142530.Fig. 6-5 Inspect crankshaft in the zone of radial seal contact. If a friction groove has been formed by the radial seal, displace the complete cover by adding gaskets accordingly.Dismantling, Installing And Sealing The Cover On The Flywheel Side (As from 3-cylinder engine)
The flywheel has already been removed.Dismantling:
1. Remove the bolts in the oil sump securing the cover on the flywheel side and the bolts securing the cover to the crankcase. Remove cover and gasket. Renew radial sealing ring. Inspect crankshaft in the zone of radial seal contact. If a friction groove has been formed by the radial seal, displace the latter in the cover.Installing:
6-112. Adhere new gasket to crankcase. Trim off the portion of gasket projecting beyond the joint surface of the sump. Fig. 6-113. Apply coat of Deutz DW 48 jointing compound to the oil sump gasket in the region of the cover.
6-124. Press new radial seal into the rear cover so that the outside surface is flush (arrow).Fig. 6-12 Prior to fitting, heat cover "hand-warm" and coat radial seal with jointing compound.
6-135. Place cover in position. Lightly pretighten cover bolts in crankcase. Fully tighten sump bolts in cover, then fully tighten bolts in crankcase.Fig. 6-13Exploded Views
It is assumed that the flywheel is dismantled.Removing:
6-1Cut through the starter gear ring with a hard chisel and remove.Fig. 6-1Refitting:
1. Heat the starter gear ring to a temperature of 120 deg. C. Place the starter gear ring with the bevelled side of the teeth facing away from flywheel.
6-22. Locate the starter gear ring on the flywheel and tap it into position so that it seats against the shoulder.Fig. 6-2Removing And Fitting A Radial Sealing Ring On The Flywheel Side
It is assumed that the flywheel has been dismantled. Removing:
6-3Apply puller No. 142700 and draw off radial sealing ring.Fig. 6-3Refitting:
6-41. Mount guide-piece of device onto crankshaft.Fig. 6-4
6-52. Lightly grease the sealing lip of the new radial seal. Place seal on guide-piece with lip facing towards crankcase and press in with device No. 142530.Fig. 6-5 Inspect crankshaft in the zone of radial seal contact. If a friction groove has been formed by the radial seal, displace the complete cover by adding gaskets accordingly.Dismantling, Installing And Sealing The Cover On The Flywheel Side (As from 3-cylinder engine)
The flywheel has already been removed.Dismantling:
1. Remove the bolts in the oil sump securing the cover on the flywheel side and the bolts securing the cover to the crankcase. Remove cover and gasket. Renew radial sealing ring. Inspect crankshaft in the zone of radial seal contact. If a friction groove has been formed by the radial seal, displace the latter in the cover.Installing:
6-112. Adhere new gasket to crankcase. Trim off the portion of gasket projecting beyond the joint surface of the sump. Fig. 6-113. Apply coat of Deutz DW 48 jointing compound to the oil sump gasket in the region of the cover.
6-124. Press new radial seal into the rear cover so that the outside surface is flush (arrow).Fig. 6-12 Prior to fitting, heat cover "hand-warm" and coat radial seal with jointing compound.
6-135. Place cover in position. Lightly pretighten cover bolts in crankcase. Fully tighten sump bolts in cover, then fully tighten bolts in crankcase.Fig. 6-13Exploded Views
Have questions with 101602-4620?
Group cross 101602-4620 ZEXEL
Isuzu
101602-4620
9 400 614 845
1156021040
INJECTION-PUMP ASSEMBLY
6BD1
6BD1