Information injection-pump assembly
ZEXEL
101602-3720
1016023720
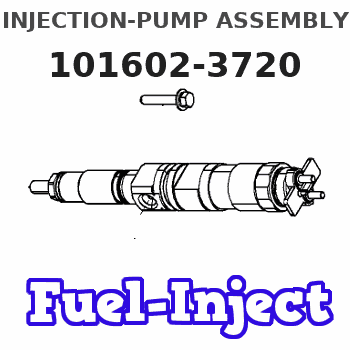
Rating:
Cross reference number
ZEXEL
101602-3720
1016023720
Zexel num
Bosch num
Firm num
Name
Calibration Data:
Adjustment conditions
Test oil
1404 Test oil ISO4113 or {SAEJ967d}
1404 Test oil ISO4113 or {SAEJ967d}
Test oil temperature
degC
40
40
45
Nozzle and nozzle holder
105780-8140
Bosch type code
EF8511/9A
Nozzle
105780-0000
Bosch type code
DN12SD12T
Nozzle holder
105780-2080
Bosch type code
EF8511/9
Opening pressure
MPa
17.2
Opening pressure
kgf/cm2
175
Injection pipe
Outer diameter - inner diameter - length (mm) mm 6-2-600
Outer diameter - inner diameter - length (mm) mm 6-2-600
Tester oil delivery pressure
kPa
157
157
157
Tester oil delivery pressure
kgf/cm2
1.6
1.6
1.6
Direction of rotation (viewed from drive side)
Right R
Right R
Injection timing adjustment
Direction of rotation (viewed from drive side)
Right R
Right R
Injection order
1-5-3-6-
2-4
Pre-stroke
mm
4
3.95
4.05
Beginning of injection position
Drive side NO.1
Drive side NO.1
Difference between angles 1
Cal 1-5 deg. 60 59.5 60.5
Cal 1-5 deg. 60 59.5 60.5
Difference between angles 2
Cal 1-3 deg. 120 119.5 120.5
Cal 1-3 deg. 120 119.5 120.5
Difference between angles 3
Cal 1-6 deg. 180 179.5 180.5
Cal 1-6 deg. 180 179.5 180.5
Difference between angles 4
Cyl.1-2 deg. 240 239.5 240.5
Cyl.1-2 deg. 240 239.5 240.5
Difference between angles 5
Cal 1-4 deg. 300 299.5 300.5
Cal 1-4 deg. 300 299.5 300.5
Injection quantity adjustment
Adjusting point
A
Rack position
10.2
Pump speed
r/min
900
900
900
Average injection quantity
mm3/st.
102.7
101.7
103.7
Max. variation between cylinders
%
0
-2
2
Basic
*
Fixing the rack
*
Injection quantity adjustment_02
Adjusting point
B
Rack position
7.7+-0.5
Pump speed
r/min
325
325
325
Average injection quantity
mm3/st.
13.9
12.7
15.1
Max. variation between cylinders
%
0
-10
10
Fixing the rack
*
Test data Ex:
Governor adjustment
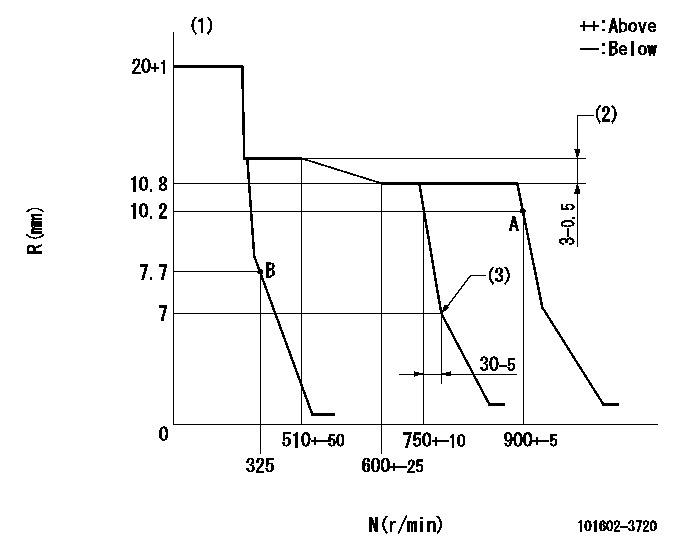
N:Pump speed
R:Rack position (mm)
(1)Target notch: K
(2)Rack difference between N = N1 and N = N2
(3)Idle sub spring setting: L1.
----------
K=16 N1=850r/min N2=450r/min L1=7-0.5mm
----------
----------
K=16 N1=850r/min N2=450r/min L1=7-0.5mm
----------
Speed control lever angle
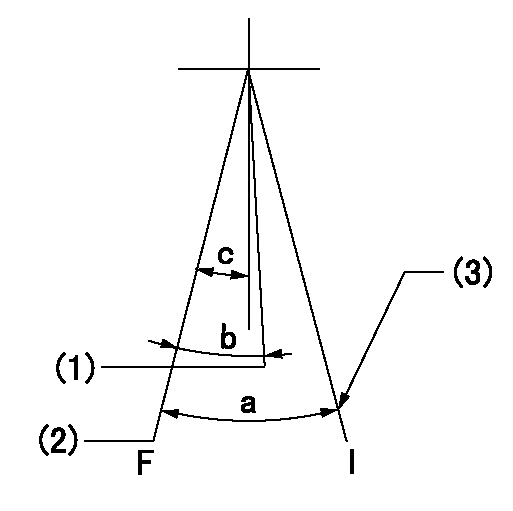
F:Full speed
I:Idle
(1)Set the pump speed at aa
(2)Set the pump speed at bb.
(3)Stopper bolt setting
----------
aa=750r/min bb=900r/min
----------
a=28.5deg+-5deg b=6.5deg+-5deg c=6.5deg+-5deg
----------
aa=750r/min bb=900r/min
----------
a=28.5deg+-5deg b=6.5deg+-5deg c=6.5deg+-5deg
Stop lever angle

N:Pump normal
S:Stop the pump.
(1)At shipping
----------
----------
a=11.5deg+-5deg b=53deg+-5deg
----------
----------
a=11.5deg+-5deg b=53deg+-5deg
Information:
Personal injury can result from improper handling of chemicals.Make sure you use all the necessary protective equipment required to do the job.Make sure that you read and understand all directions and hazards described on the labels and material safety data sheet of any chemical that is used.Observe all safety precautions recommended by the chemical manufacturer for handling, storage, and disposal of chemicals.
Before servicing/performing maintenance on the machine, electrical power must be physically disconnected; battery plugs must be disconnected from the batteries, or the trailing cable must be unplugged, and warning tags and padlocks shall be applied by a certified electrician. Certified electricians shall perform or direct any electrical work, including any energized testing, repair work in controllers, motors, or other approved compartments, and shall insure that all compartments are properly closed and inspected prior to re-energization. All applicable lock out and tag out procedures must be followed.
Observe the safe working load limits of all lifting and blocking devices and keep a safe distance from suspended/blocked loads. Personnel may be seriously injured or killed by falling loads.
Connector Pin Arcing
Injector solenoid diagnostic codes can be a result of poor electrical connections between the injector and injector harness. When troubleshooting a suspected injector failure, carefully inspect injector connector pins for signs of arcing. If arcing is observed, both injector and harness must be replaced due to damaged connector pins and sockets. Connector pin arcing can also be caused by improper removal the harness from the injector. When removing the harness use approved tool 458-3562 Tool As. Refer to Illustration 2.
Illustration 2 g06300012
Connector Pin Arcing
Illustration 3 g06399136
(1) Correct placement of tool
Illustration 4 g06399157
(2) Correct removal of connectorRefer to the following publications for more details and specifications:
Refer to Troubleshooting, RENR9343, "Injector Solenoid - Test".
Refer to Service Magazine, SEPD1840, "A New Improved Removal and Installation of the Injector Harness Procedure is Now Used on Certain C13, C15, and C18 Engines".
Refer to Engine News, SEBD9957, "A New Improved Removal and Installation of the Injector Harness Procedure is Now Used on Certain C13, C15, and C18 Engines".Fuel System Restrictions
Adequate fuel flow rate through the engine is required to cool fuel injectors and injector solenoids. Contaminated fuel combined with inadequate maintenance of the secondary fuel filter can reduce fuel flow rate. Fuel filter restrictions can cause fuel to bypass internally within the secondary filter base. This bypass will allow fuel flow to return to tank without cooling the fuel injectors. Refer to Illustration 5.
Illustration 5 g06399162
(3) Normal Solenoid
(4) Overheated SolenoidTroubleshooting of injector failures should include investigation of secondary filter internal bypass. Internal bypass can be indicated by measuring fuel pressure at the sample port that is on the secondary filter base. Fuel bypass will occur as pressure approaches 655 kPa (95 psi) at the sample port. High-pressure measurements with the engine operating at low idle are especially concerning.Pressure measurement at the sample port differs from the measurement of pressure near the engine cylinder head. Pressure measured at the sample port is immediately upstream of the fuel filter element and the