Information injection-pump assembly
ZEXEL
101602-3350
1016023350
KOMATSU
6137711510
6137711510
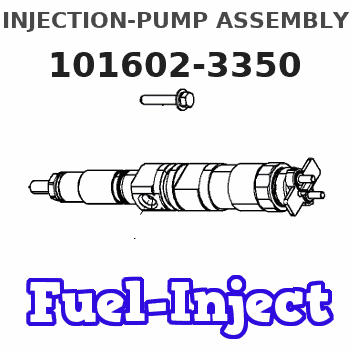
Rating:
Cross reference number
ZEXEL
101602-3350
1016023350
KOMATSU
6137711510
6137711510
Zexel num
Bosch num
Firm num
Name
101602-3350
6137711510 KOMATSU
INJECTION-PUMP ASSEMBLY
SL6D105 * K
SL6D105 * K
Calibration Data:
Adjustment conditions
Test oil
1404 Test oil ISO4113 or {SAEJ967d}
1404 Test oil ISO4113 or {SAEJ967d}
Test oil temperature
degC
40
40
45
Nozzle and nozzle holder
105780-8140
Bosch type code
EF8511/9A
Nozzle
105780-0000
Bosch type code
DN12SD12T
Nozzle holder
105780-2080
Bosch type code
EF8511/9
Opening pressure
MPa
17.2
Opening pressure
kgf/cm2
175
Injection pipe
Outer diameter - inner diameter - length (mm) mm 6-2-600
Outer diameter - inner diameter - length (mm) mm 6-2-600
Tester oil delivery pressure
kPa
157
157
157
Tester oil delivery pressure
kgf/cm2
1.6
1.6
1.6
Direction of rotation (viewed from drive side)
Right R
Right R
Injection timing adjustment
Direction of rotation (viewed from drive side)
Right R
Right R
Injection order
1-5-3-6-
2-4
Pre-stroke
mm
3.5
3.45
3.55
Beginning of injection position
Drive side NO.1
Drive side NO.1
Difference between angles 1
Cal 1-5 deg. 60 59.5 60.5
Cal 1-5 deg. 60 59.5 60.5
Difference between angles 2
Cal 1-3 deg. 120 119.5 120.5
Cal 1-3 deg. 120 119.5 120.5
Difference between angles 3
Cal 1-6 deg. 180 179.5 180.5
Cal 1-6 deg. 180 179.5 180.5
Difference between angles 4
Cyl.1-2 deg. 240 239.5 240.5
Cyl.1-2 deg. 240 239.5 240.5
Difference between angles 5
Cal 1-4 deg. 300 299.5 300.5
Cal 1-4 deg. 300 299.5 300.5
Injection quantity adjustment
Adjusting point
A
Rack position
9.4
Pump speed
r/min
900
900
900
Average injection quantity
mm3/st.
51.5
50.5
52.5
Max. variation between cylinders
%
0
-2
2
Basic
*
Fixing the lever
*
Injection quantity adjustment_02
Adjusting point
B
Rack position
8+-0.5
Pump speed
r/min
325
325
325
Average injection quantity
mm3/st.
10.5
9
12
Max. variation between cylinders
%
0
-10
10
Fixing the rack
*
Test data Ex:
Governor adjustment
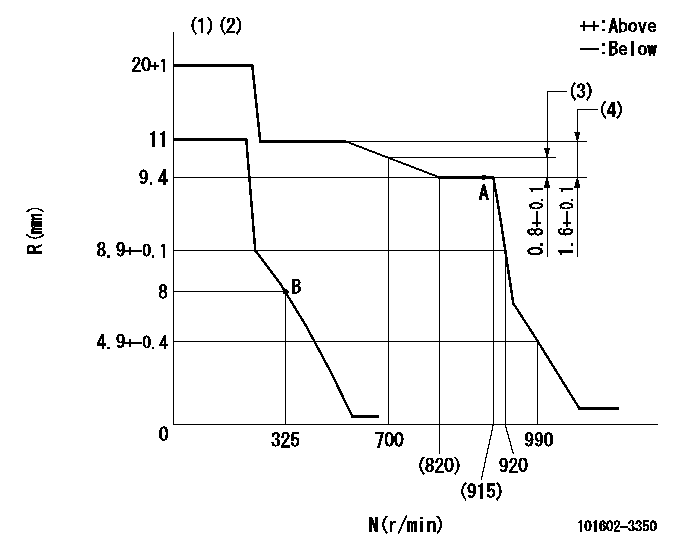
N:Pump speed
R:Rack position (mm)
(1)Target notch: K
(2)Tolerance for racks not indicated: +-0.05mm.
(3)Rack difference from N = N1
(4)Rack difference between N = N2 and N = N3
----------
K=15 N1=900r/min N2=900r/min N3=450r/min
----------
----------
K=15 N1=900r/min N2=900r/min N3=450r/min
----------
Speed control lever angle
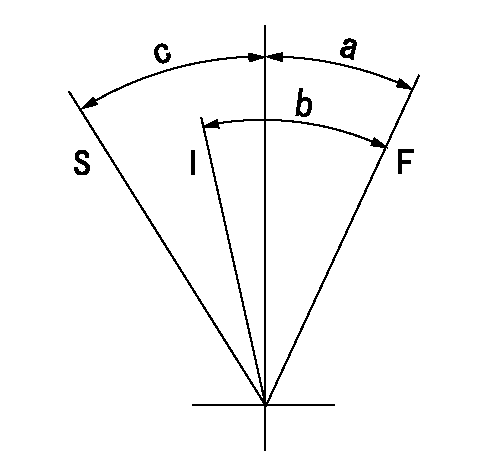
F:Full speed
I:Idle
S:Stop
----------
----------
a=6deg+-5deg b=30deg+-5deg c=32deg+-3deg
----------
----------
a=6deg+-5deg b=30deg+-5deg c=32deg+-3deg
0000001501 LEVER

(F) P/N: Part number of the shim
L1:Thickness (mm)
1. Adjustment of the control lever
(1)Perform idling with the control lever (A) contacting the pushrod (B). At this time, confirm that the spring (C) is not compressed by control lever (A)'s operating torque.
(2)To set the stop position, compress spring (C) using the control lever (A) and adjust the rack so that it contacts the guide screw (D) at position L2. Then, set and fix using the lock nut (E). Adjust the rack position L2 at this time using the shim (F).
(3)Confirm that the control lever (A) returns to the idling position when pulled in the stop direction and then released.
----------
L2=0.2~2mm
----------
----------
L2=0.2~2mm
----------
Information:
Table 3
Injector Resistance Measurement
Step Instruction Completed
(Yes/No) Results
Comments Units
1 Turn the keyswitch to the OFF position. Allow 2 minutes to elapse before proceeding.
2 Disconnect the DEF injector from the applicable harness.
3 Inspect the connector for damage or debris (if damaged take photo)
4 Measure the temperature of the injector (aluminum body) C
5 Connect two 398-4987 connectors to the DEF injector. The connectors must be used to prevent damage to the DEF injector connector.
6 Measure the resistance of the DEF injector. Ohms
Table 4
Dosing Accuracy Test
Step Instruction Completed
(Yes/No) Results
Comments Units
1 Follow the Testing and Adjusting, Aftertreatment SCR System Dosing - Test.
2 Remove the injector from the DPF outlet.
3 Take a photograph of the DEF injector mount on the DPF outlet and the tip of the DEF injector.
4 Install the injector on the beaker.
5 Run the DEF System Dosing Accuracy test through Cat ET.
6 Use the breaker to measure the amount of fluid from the dosing test. ml
7 Repeat the test to verify consistency. ml
8 Install the injector back onto the DPF outlet.
Illustration 2 g06068068
DEF Injector Resistance Measurement
Illustration 3 g06067706
Injector Mount on DPF (Outlet Sample Picture)
Illustration 4 g06067753
DEF Injector Tip (Sample Picture)
When troubleshooting requests the DEF quality check, DEF injector resistance measurement or Dosing Accuracy Test, please document results in the Tables shown above.
After completing troubleshooting and performing the Aftertreatment System Functional Test, download a new Product Status Report with all ECM's.
Table 5
Injector Failure Report
Step Instruction Completed
(Yes/No) Results
Comments Units
1 Download "Product Status Report" (PSR) from the engine ECM and send to the email address in the instructions.
2 Download "Warranty Report" (WR) from the engine ECM and send to the email address in the instructions.
3 Take a picture of the injector part number / serial number.
4 Follow the correct TSG based on Table 1 and complete tables 2 through 4 when they apply.
5 Perform an "Aftertreatment System Functional Test".
6 Download "Product Status Report" (PSR) from the engine ECM and send to the email address in the instructions.
7 Submit "TIB Check List", "Product Status Reports", DEF injector deposits photographs, CEM deposit photographs, and DEF injector part number and serial number photograph to the email address in the instructions.
Fill out the Injector Failure Report and send all information including product status reports, warranty reports, DEF injector and mount photos, DEF injector part number and serial number and test results to the email address provided above.
Have questions with 101602-3350?
Group cross 101602-3350 ZEXEL
Komatsu
101602-3350
6137711510
INJECTION-PUMP ASSEMBLY
SL6D105
SL6D105