Information injection-pump assembly
BOSCH
9 400 610 268
9400610268
ZEXEL
101602-3060
1016023060
KOMATSU
6137711102
6137711102
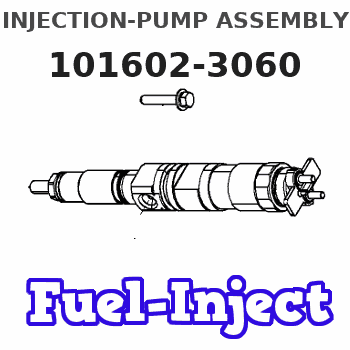
Rating:
Service parts 101602-3060 INJECTION-PUMP ASSEMBLY:
1.
_
5.
AUTOM. ADVANCE MECHANIS
7.
COUPLING PLATE
8.
_
9.
_
11.
Nozzle and Holder
6137-12-3100
12.
Open Pre:MPa(Kqf/cm2)
22.1{225}
15.
NOZZLE SET
Cross reference number
BOSCH
9 400 610 268
9400610268
ZEXEL
101602-3060
1016023060
KOMATSU
6137711102
6137711102
Zexel num
Bosch num
Firm num
Name
101602-3060
9 400 610 268
6137711102 KOMATSU
INJECTION-PUMP ASSEMBLY
S6D105 K 14BE INJECTION PUMP ASSY PE6A PE
S6D105 K 14BE INJECTION PUMP ASSY PE6A PE
Calibration Data:
Adjustment conditions
Test oil
1404 Test oil ISO4113 or {SAEJ967d}
1404 Test oil ISO4113 or {SAEJ967d}
Test oil temperature
degC
40
40
45
Nozzle and nozzle holder
105780-8140
Bosch type code
EF8511/9A
Nozzle
105780-0000
Bosch type code
DN12SD12T
Nozzle holder
105780-2080
Bosch type code
EF8511/9
Opening pressure
MPa
17.2
Opening pressure
kgf/cm2
175
Injection pipe
Outer diameter - inner diameter - length (mm) mm 6-2-600
Outer diameter - inner diameter - length (mm) mm 6-2-600
Tester oil delivery pressure
kPa
157
157
157
Tester oil delivery pressure
kgf/cm2
1.6
1.6
1.6
Direction of rotation (viewed from drive side)
Right R
Right R
Injection timing adjustment
Direction of rotation (viewed from drive side)
Right R
Right R
Injection order
1-5-3-6-
2-4
Pre-stroke
mm
3.3
3.25
3.35
Beginning of injection position
Drive side NO.1
Drive side NO.1
Difference between angles 1
Cal 1-5 deg. 60 59.5 60.5
Cal 1-5 deg. 60 59.5 60.5
Difference between angles 2
Cal 1-3 deg. 120 119.5 120.5
Cal 1-3 deg. 120 119.5 120.5
Difference between angles 3
Cal 1-6 deg. 180 179.5 180.5
Cal 1-6 deg. 180 179.5 180.5
Difference between angles 4
Cyl.1-2 deg. 240 239.5 240.5
Cyl.1-2 deg. 240 239.5 240.5
Difference between angles 5
Cal 1-4 deg. 300 299.5 300.5
Cal 1-4 deg. 300 299.5 300.5
Injection quantity adjustment
Adjusting point
A
Rack position
10.7
Pump speed
r/min
1250
1250
1250
Average injection quantity
mm3/st.
76.5
75.5
77.5
Max. variation between cylinders
%
0
-2
2
Basic
*
Fixing the lever
*
Boost pressure
kPa
40
40
Boost pressure
mmHg
300
300
Injection quantity adjustment_02
Adjusting point
B
Rack position
10.7+-0.
5
Pump speed
r/min
900
900
900
Average injection quantity
mm3/st.
74
72
76
Max. variation between cylinders
%
0
-4
4
Fixing the lever
*
Boost pressure
kPa
40
40
Boost pressure
mmHg
300
300
Injection quantity adjustment_03
Adjusting point
C
Rack position
8+-0.5
Pump speed
r/min
390
390
390
Average injection quantity
mm3/st.
9
8
10
Max. variation between cylinders
%
0
-10
10
Fixing the rack
*
Boost pressure
kPa
0
0
0
Boost pressure
mmHg
0
0
0
Boost compensator adjustment
Pump speed
r/min
750
750
750
Rack position
R1-1
Boost pressure
kPa
6.7
5.4
8
Boost pressure
mmHg
50
40
60
Boost compensator adjustment_02
Pump speed
r/min
750
750
750
Rack position
R1(10.7)
Boost pressure
kPa
26.7
26.7
26.7
Boost pressure
mmHg
200
200
200
Test data Ex:
Governor adjustment
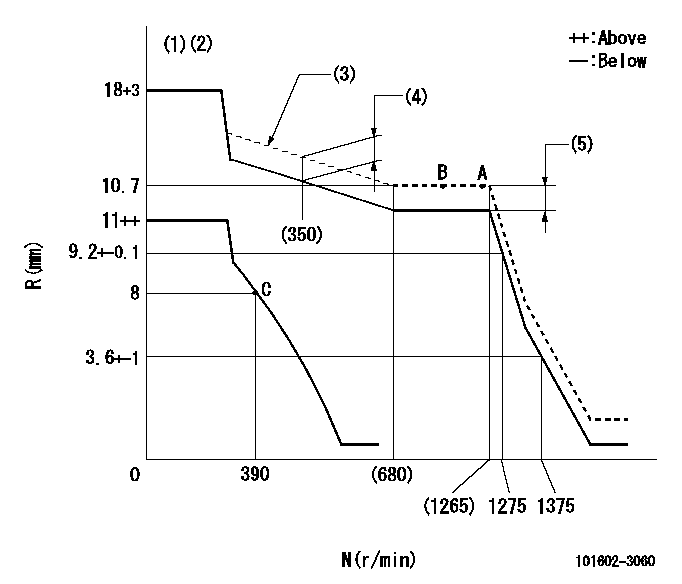
N:Pump speed
R:Rack position (mm)
(1)Target notch: K
(2)Tolerance for racks not indicated: +-0.05mm.
(3)The torque control spring must does not have a set force.
(4)Torque control stroke: L1
(5)Boost compensator stroke: BCL
----------
K=5 L1=1.9+0.2mm BCL=1+-0.1mm
----------
----------
K=5 L1=1.9+0.2mm BCL=1+-0.1mm
----------
Speed control lever angle
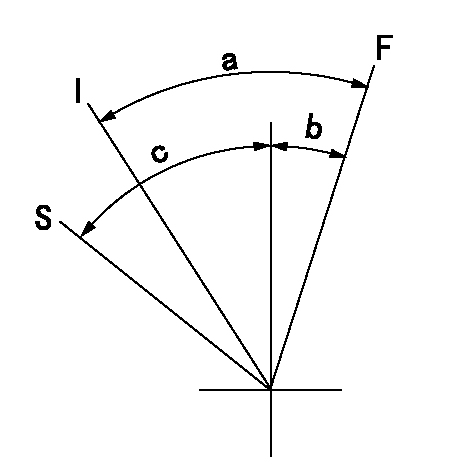
F:Full speed
I:Idle
S:Stop
----------
----------
a=21deg+-5deg b=4.5deg+-5deg c=32deg+-3deg
----------
----------
a=21deg+-5deg b=4.5deg+-5deg c=32deg+-3deg
0000001501 LEVER

(F) P/N: Part number of the shim
L1:Thickness (mm)
1. Adjustment of the control lever
(1)Perform idling with the control lever (A) contacting the pushrod (B). At this time, confirm that the spring (C) is not compressed by control lever (A)'s operating torque.
(2)To set the stop position, compress spring (C) using the control lever (A) and adjust the rack so that it contacts the guide screw (D) at position L2. Then, set and fix using the lock nut (E). Adjust the rack position L2 at this time using the shim (F).
(3)Confirm that the control lever (A) returns to the idling position when pulled in the stop direction and then released.
----------
L2=0.2~2mm
----------
----------
L2=0.2~2mm
----------
Timing setting

(1)Pump vertical direction
(2)Coupling's key groove position at No 1 cylinder's beginning of injection
(3)-
(4)-
----------
----------
a=(0deg)
----------
----------
a=(0deg)
Information:
Wear goggles, gloves, protective clothing, and a National Institute for Occupationsl Safety and Health (Niosh) approved P95 or N95 half-face respirator when handling a used Diesel Particulate Filter or Catalytic Converter Muffler. Failure to do so could result in personal injury.
Anyone working around or near the Cat Diesel Particulate Filter (DPF) system should be trained in the proper safety precautions and procedures including emergency shutdown, MSDS sheets detail for the necessary safety precautions and procedures required for the handling of materials. These precautions and procedures must be followed.
Service on the Cat DPF system is to be done only by trained and qualified individuals. The training includes all electrical and mechanical service.
If there is any concern about the safety of this system, clear the area immediately of all personnel. Contact the appropriate person for further instructions.
Have questions with 101602-3060?
Group cross 101602-3060 ZEXEL
Komatsu
101602-3060
9 400 610 268
6137711102
INJECTION-PUMP ASSEMBLY
S6D105
S6D105