Information injection-pump assembly
BOSCH
9 400 611 209
9400611209
ZEXEL
101602-2942
1016022942
HINO
220205233A
220205233a
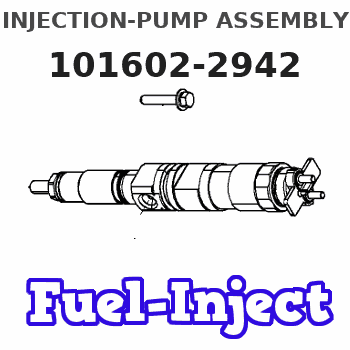
Rating:
Service parts 101602-2942 INJECTION-PUMP ASSEMBLY:
1.
_
5.
AUTOM. ADVANCE MECHANIS
8.
_
9.
_
11.
Nozzle and Holder
23600-3170A
12.
Open Pre:MPa(Kqf/cm2)
19.6{200}
15.
NOZZLE SET
Cross reference number
BOSCH
9 400 611 209
9400611209
ZEXEL
101602-2942
1016022942
HINO
220205233A
220205233a
Zexel num
Bosch num
Firm num
Name
Calibration Data:
Adjustment conditions
Test oil
1404 Test oil ISO4113 or {SAEJ967d}
1404 Test oil ISO4113 or {SAEJ967d}
Test oil temperature
degC
40
40
45
Nozzle and nozzle holder
105780-8140
Bosch type code
EF8511/9A
Nozzle
105780-0000
Bosch type code
DN12SD12T
Nozzle holder
105780-2080
Bosch type code
EF8511/9
Opening pressure
MPa
17.2
Opening pressure
kgf/cm2
175
Injection pipe
Outer diameter - inner diameter - length (mm) mm 6-2-600
Outer diameter - inner diameter - length (mm) mm 6-2-600
Overflow valve
131425-0620
Overflow valve opening pressure
kPa
255
221
289
Overflow valve opening pressure
kgf/cm2
2.6
2.25
2.95
Tester oil delivery pressure
kPa
157
157
157
Tester oil delivery pressure
kgf/cm2
1.6
1.6
1.6
Direction of rotation (viewed from drive side)
Left L
Left L
Injection timing adjustment
Direction of rotation (viewed from drive side)
Left L
Left L
Injection order
1-4-2-6-
3-5
Pre-stroke
mm
3.8
3.77
3.83
Beginning of injection position
Governor side NO.1
Governor side NO.1
Difference between angles 1
Cal 1-4 deg. 60 59.75 60.25
Cal 1-4 deg. 60 59.75 60.25
Difference between angles 2
Cyl.1-2 deg. 120 119.75 120.25
Cyl.1-2 deg. 120 119.75 120.25
Difference between angles 3
Cal 1-6 deg. 180 179.75 180.25
Cal 1-6 deg. 180 179.75 180.25
Difference between angles 4
Cal 1-3 deg. 240 239.75 240.25
Cal 1-3 deg. 240 239.75 240.25
Difference between angles 5
Cal 1-5 deg. 300 299.75 300.25
Cal 1-5 deg. 300 299.75 300.25
Injection quantity adjustment
Adjusting point
A
Rack position
8.8
Pump speed
r/min
900
900
900
Average injection quantity
mm3/st.
87
85
89
Max. variation between cylinders
%
0
-3.5
3.5
Basic
*
Fixing the lever
*
Boost pressure
kPa
42.7
42.7
Boost pressure
mmHg
320
320
Injection quantity adjustment_02
Adjusting point
C
Rack position
6.3+-0.5
Pump speed
r/min
365
365
365
Average injection quantity
mm3/st.
8.5
7.5
9.5
Max. variation between cylinders
%
0
-10
10
Fixing the rack
*
Boost pressure
kPa
0
0
0
Boost pressure
mmHg
0
0
0
Injection quantity adjustment_03
Adjusting point
E
Rack position
-
Pump speed
r/min
100
100
100
Average injection quantity
mm3/st.
105
105
115
Fixing the lever
*
Boost pressure
kPa
0
0
0
Boost pressure
mmHg
0
0
0
Rack limit
*
Boost compensator adjustment
Pump speed
r/min
800
800
800
Rack position
R1-1.2
Boost pressure
kPa
4.7
3.4
6
Boost pressure
mmHg
35
25
45
Boost compensator adjustment_02
Pump speed
r/min
800
800
800
Rack position
R1(8.8)
Boost pressure
kPa
29.3
22.6
36
Boost pressure
mmHg
220
170
270
Test data Ex:
Governor adjustment
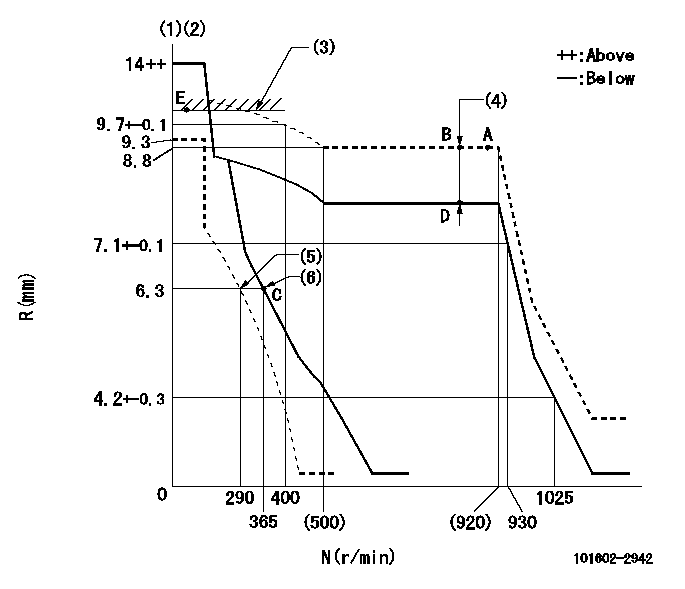
N:Pump speed
R:Rack position (mm)
(1)Target notch: K
(2)Tolerance for racks not indicated: +-0.05mm.
(3)RACK LIMIT
(4)Boost compensator stroke: BCL
(5)Set idle sub-spring
(6)Main spring setting
----------
K=8 BCL=1.2+-0.1mm
----------
----------
K=8 BCL=1.2+-0.1mm
----------
Speed control lever angle
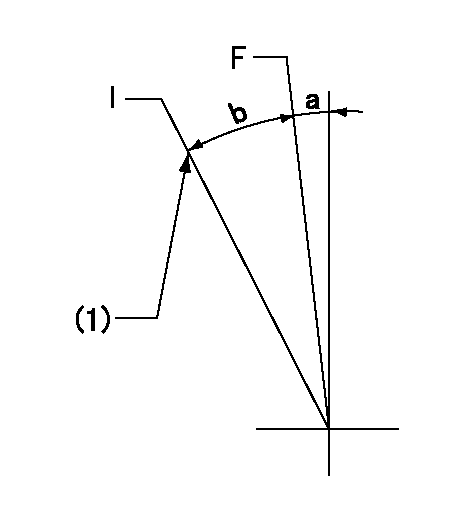
F:Full speed
I:Idle
(1)Stopper bolt setting
----------
----------
a=3deg+-5deg b=16deg+-5deg
----------
----------
a=3deg+-5deg b=16deg+-5deg
Stop lever angle
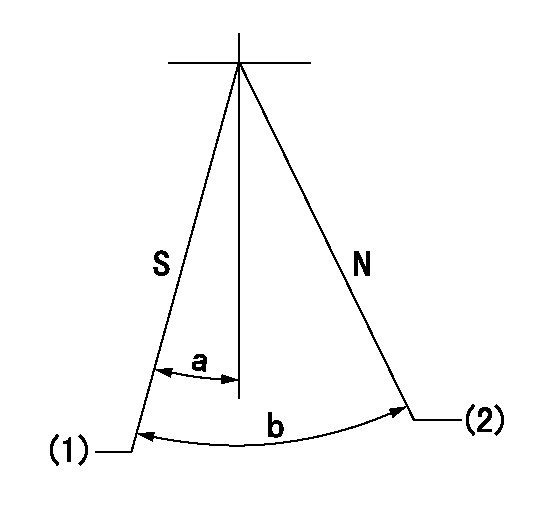
N:Pump normal
S:Stop the pump.
(1)Pump speed aa and rack position bb (to be sealed at delivery)
(2)Normal
----------
aa=0r/min bb=1-0.5mm
----------
a=21deg+-5deg b=(55deg)
----------
aa=0r/min bb=1-0.5mm
----------
a=21deg+-5deg b=(55deg)
Timing setting

(1)Pump vertical direction
(2)Coupling's key groove position at No 1 cylinder's beginning of injection
(3)-
(4)-
----------
----------
a=(20deg)
----------
----------
a=(20deg)
Information:
Use of Cat Diesel Fuel System Cleaner or Cat Diesel Fuel System Conditioner does not lessen the responsibility of the engine owner and/or responsibility of the fuel supplier to follow all industry standard maintenance practices for fuel storage and for fuel handling. Refer to the “General Fuel Information” article in this Special Publication for additional information. Additionally, use of Cat Diesel Fuel System Cleaner or Cat Diesel Fuel System Conditioner does NOT lessen the responsibility of the owner of the engine to use appropriate diesel fuel. Refer to the “Fuel Specifications” section in this Special Publication (Maintenance Section) for guidance.
Caterpillar strongly recommends that Cat Diesel Fuel System Cleaner be used with biodiesel and biodiesel blends. Cat Diesel Fuel System Cleaner is suitable for use with biodiesel/biodiesel blends that meet Cat biodiesel recommendations and requirements. Note that not all fuel cleaners are suitable for use with biodiesel/biodiesel blends. Read and follow all applicable label usage instructions. Also, refer to this Special Publication, "Distillate Diesel Fuel", article and also refer to the “Biodiesel” article, which includes Cat biodiesel recommendations and requirements.When used as directed, Cat Diesel Fuel System Cleaner has proven to be compatible with non-road Tier 4 U.S. EPA certified engines that are equipped with aftertreatment devices.Note: When used as directed, Cat Diesel Fuel System Cleaner will not raise fuel sulfur levels measurably in the final fuel/additive blend. Follow all applicable national, regional, and local laws, mandates, and regulations concerning the use of diesel fuel conditioners/additives.
When used as directed Cat Diesel Fuel System Cleaner will not raise fuel sulfur levels measurably in the final fuel/additive blend. But, in the U.S., aftermarket fuel additives (retail consumer level versus bulk fuel additives used at the fuel supplier/distributor level) with more than 15 ppm sulfur are NOT allowed to be used in applications where ULSD usage is mandated (15 ppm or less fuel sulfur). Note that Cat Diesel Fuel System Cleaner contains less than 15 ppm of sulfur and is acceptable for use with ULSD fuel.
Renewable and Alternative Fuels
Renewable fuels are derived from renewable resources such as planted crops and crop residues (referred to as biomass), waste, algae, cellulosic material, yard and food waste, etc. Renewable fuels reduce the carbon footprint of the fuels compared to fossil fuels on a Life Cycle Analysis basis. Caterpillar, through sustainability initiatives, supports the development and use of renewable fuels.Renewable fuels (other than biodiesel) and alternative fuels (such as but not limited to Gas-to-Liquid fuel) are typically >99% hydrocarbons (composed of carbon and hydrogen). An exception is biodiesel, which is an oxygenated renewable fuel. Biodiesel is discussed in a separate article in this Fuel section. Significant research is on going to develop renewable fuels and produce the fuels economically.Caterpillar is not in a position to test all varieties of renewable and alternative fuels that are advertised in the market place. If a renewable or alternative fuel fulfills the performance requirements described in Cat Fuel Specification, the latest version of "ASTM D975", the latest version of "EN