Information injection-pump assembly
BOSCH
9 400 612 363
9400612363
ZEXEL
101602-2882
1016022882
HINO
220205061A
220205061a
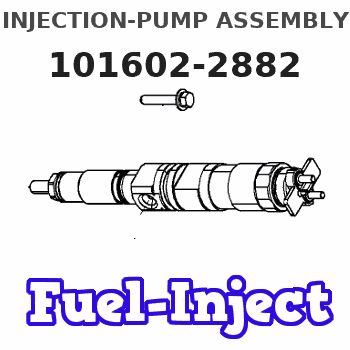
Rating:
Service parts 101602-2882 INJECTION-PUMP ASSEMBLY:
1.
_
5.
AUTOM. ADVANCE MECHANIS
6.
COUPLING PLATE
8.
_
9.
_
11.
Nozzle and Holder
23600-2850A
12.
Open Pre:MPa(Kqf/cm2)
17.7{180}
15.
NOZZLE SET
Cross reference number
Zexel num
Bosch num
Firm num
Name
101602-2882
9 400 612 363
220205061A HINO
INJECTION-PUMP ASSEMBLY
W06D-T K
W06D-T K
Information:
General Contamination Control Recommendations or Practices
Maintaining a low contamination level can reduce down time and can control the maintenance cost of the engine. The productive life as well as the reliability of components and fluid systems is often increased as a result of proper contamination control practices.The following are general guidelines for controlling contaminants.
Refer to the Recommendations for Fuel Systems in this chapter for recommended fuel cleanliness levels and guidelines.
Refer to the engine Operation and Maintenance Manual for the required maintenance for all engine fluids.
When you add oil to an engine, use engine oil filters of 12 microns absolute efficiency. Ensure that the oil temperature is 20° C (68° F) or higher.
Perform scheduled S O S Services Oil Analysis for contamination in order to maintain the recommended ISO cleanliness level of fill and machine fluids. Refer to the S O S Oil Analysis section in this Special Publication. The particle count analysis can be performed by your Cat dealer. Particle count can be conducted during the scheduled S O S Services Oil Analysis for the compartment. Extra oil samples are not required for the particle count sampling.
Use only coolants that are recommended by Cat for your machine. Follow the recommended maintenance procedure for the cooling system in the Operation and Maintenance Manual for your machine.
Maintain the engine air filters and air intake system to avoid unwanted contaminant ingression.
Follow contamination control practices for the shop area, component/machine disassembly areas, parts, shop tools, test setups, test areas, storage areas and waste collection areas. Keep components clean during inspection, assembly, testing, and filling engines with clean fluids. Good practices will enhance component life and reduce downtime associated with contaminants. Your Cat dealer can provide details on proper contamination processes and practices.
Follow contamination control practices for the workplace and for the worksite. Maintaining clean oil fill fluids saves time and effort and ensures that fill fluids are at the proper cleanliness levels.
Use properly designed and maintained bulk storage fluids tanks.
Protect the fluids storage tanks from dirt and water entry by using 4 µm or less absolute efficiency breathers with the ability to remove water.
Keep the areas around the tanks filler necks clean of debris and water.
Drain the storage tanks from water and sediments frequently. The draining schedule depends on use of proper inlet and outlet filters, the use of 4 µm breathers with the ability to remove water, and following recommended contamination control practices. Based on the contamination control program followed, and/or on the fuel supplier recommendations, the storage tank draining schedule may be as frequent as daily until no water is present, and then can be extended to longer periods.
Install and maintain a properly designed and grounded filtration system. Filtration should include at the entry and at the dispensing point. Continuous bulk filtration may be required to ensure that dispensed oils meet the cleanliness target.
Cover, protect, and ensure cleanliness of all connection hoses, fittings, and dispensing nozzles.Note: Bulk fuel filtration units are available through your Cat dealer. Proper maintenance practices of
Maintaining a low contamination level can reduce down time and can control the maintenance cost of the engine. The productive life as well as the reliability of components and fluid systems is often increased as a result of proper contamination control practices.The following are general guidelines for controlling contaminants.
Refer to the Recommendations for Fuel Systems in this chapter for recommended fuel cleanliness levels and guidelines.
Refer to the engine Operation and Maintenance Manual for the required maintenance for all engine fluids.
When you add oil to an engine, use engine oil filters of 12 microns absolute efficiency. Ensure that the oil temperature is 20° C (68° F) or higher.
Perform scheduled S O S Services Oil Analysis for contamination in order to maintain the recommended ISO cleanliness level of fill and machine fluids. Refer to the S O S Oil Analysis section in this Special Publication. The particle count analysis can be performed by your Cat dealer. Particle count can be conducted during the scheduled S O S Services Oil Analysis for the compartment. Extra oil samples are not required for the particle count sampling.
Use only coolants that are recommended by Cat for your machine. Follow the recommended maintenance procedure for the cooling system in the Operation and Maintenance Manual for your machine.
Maintain the engine air filters and air intake system to avoid unwanted contaminant ingression.
Follow contamination control practices for the shop area, component/machine disassembly areas, parts, shop tools, test setups, test areas, storage areas and waste collection areas. Keep components clean during inspection, assembly, testing, and filling engines with clean fluids. Good practices will enhance component life and reduce downtime associated with contaminants. Your Cat dealer can provide details on proper contamination processes and practices.
Follow contamination control practices for the workplace and for the worksite. Maintaining clean oil fill fluids saves time and effort and ensures that fill fluids are at the proper cleanliness levels.
Use properly designed and maintained bulk storage fluids tanks.
Protect the fluids storage tanks from dirt and water entry by using 4 µm or less absolute efficiency breathers with the ability to remove water.
Keep the areas around the tanks filler necks clean of debris and water.
Drain the storage tanks from water and sediments frequently. The draining schedule depends on use of proper inlet and outlet filters, the use of 4 µm breathers with the ability to remove water, and following recommended contamination control practices. Based on the contamination control program followed, and/or on the fuel supplier recommendations, the storage tank draining schedule may be as frequent as daily until no water is present, and then can be extended to longer periods.
Install and maintain a properly designed and grounded filtration system. Filtration should include at the entry and at the dispensing point. Continuous bulk filtration may be required to ensure that dispensed oils meet the cleanliness target.
Cover, protect, and ensure cleanliness of all connection hoses, fittings, and dispensing nozzles.Note: Bulk fuel filtration units are available through your Cat dealer. Proper maintenance practices of
Have questions with 101602-2882?
Group cross 101602-2882 ZEXEL
Hino
Hino
Hino
Hino
Hino
Hino
Hino
Hino
Hino
101602-2882
9 400 612 363
220205061A
INJECTION-PUMP ASSEMBLY
W06D-T
W06D-T