Information injection-pump assembly
BOSCH
9 400 610 581
9400610581
ZEXEL
101602-2880
1016022880
HINO
220205060A
220205060a
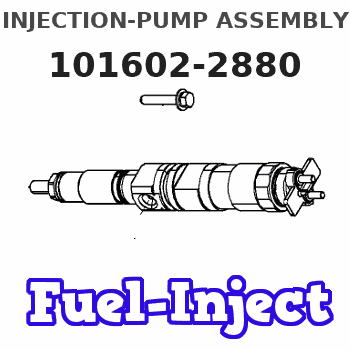
Rating:
Service parts 101602-2880 INJECTION-PUMP ASSEMBLY:
1.
_
5.
AUTOM. ADVANCE MECHANIS
6.
COUPLING PLATE
8.
_
9.
_
11.
Nozzle and Holder
23600-2850A
12.
Open Pre:MPa(Kqf/cm2)
17.7{180}
15.
NOZZLE SET
Cross reference number
BOSCH
9 400 610 581
9400610581
ZEXEL
101602-2880
1016022880
HINO
220205060A
220205060a
Zexel num
Bosch num
Firm num
Name
9 400 610 581
220205060A HINO
INJECTION-PUMP ASSEMBLY
W06D-TC * K 14BF PE6AD PE
W06D-TC * K 14BF PE6AD PE
Calibration Data:
Adjustment conditions
Test oil
1404 Test oil ISO4113 or {SAEJ967d}
1404 Test oil ISO4113 or {SAEJ967d}
Test oil temperature
degC
40
40
45
Nozzle and nozzle holder
105780-8140
Bosch type code
EF8511/9A
Nozzle
105780-0000
Bosch type code
DN12SD12T
Nozzle holder
105780-2080
Bosch type code
EF8511/9
Opening pressure
MPa
17.2
Opening pressure
kgf/cm2
175
Injection pipe
Outer diameter - inner diameter - length (mm) mm 6-2-600
Outer diameter - inner diameter - length (mm) mm 6-2-600
Overflow valve
134424-0920
Overflow valve opening pressure
kPa
162
147
177
Overflow valve opening pressure
kgf/cm2
1.65
1.5
1.8
Tester oil delivery pressure
kPa
157
157
157
Tester oil delivery pressure
kgf/cm2
1.6
1.6
1.6
Direction of rotation (viewed from drive side)
Right R
Right R
Injection timing adjustment
Direction of rotation (viewed from drive side)
Right R
Right R
Injection order
1-4-2-6-
3-5
Pre-stroke
mm
4.4
4.35
4.45
Beginning of injection position
Drive side NO.1
Drive side NO.1
Difference between angles 1
Cal 1-4 deg. 60 59.5 60.5
Cal 1-4 deg. 60 59.5 60.5
Difference between angles 2
Cyl.1-2 deg. 120 119.5 120.5
Cyl.1-2 deg. 120 119.5 120.5
Difference between angles 3
Cal 1-6 deg. 180 179.5 180.5
Cal 1-6 deg. 180 179.5 180.5
Difference between angles 4
Cal 1-3 deg. 240 239.5 240.5
Cal 1-3 deg. 240 239.5 240.5
Difference between angles 5
Cal 1-5 deg. 300 299.5 300.5
Cal 1-5 deg. 300 299.5 300.5
Injection quantity adjustment
Adjusting point
A
Rack position
11
Pump speed
r/min
900
900
900
Average injection quantity
mm3/st.
93.5
92
95
Max. variation between cylinders
%
0
-3.5
3.5
Basic
*
Fixing the lever
*
Boost pressure
kPa
25.3
25.3
Boost pressure
mmHg
190
190
Injection quantity adjustment_02
Adjusting point
C
Rack position
6.6+-0.5
Pump speed
r/min
475
475
475
Average injection quantity
mm3/st.
9
7.5
10.5
Max. variation between cylinders
%
0
-10
10
Fixing the rack
*
Boost pressure
kPa
0
0
0
Boost pressure
mmHg
0
0
0
Injection quantity adjustment_03
Adjusting point
D
Rack position
-
Pump speed
r/min
100
100
100
Average injection quantity
mm3/st.
80
80
90
Fixing the lever
*
Boost pressure
kPa
0
0
0
Boost pressure
mmHg
0
0
0
Rack limit
*
Boost compensator adjustment
Pump speed
r/min
600
600
600
Rack position
R1-1
Boost pressure
kPa
3.3
3.3
6
Boost pressure
mmHg
25
25
45
Boost compensator adjustment_02
Pump speed
r/min
600
600
600
Rack position
R1(11)
Boost pressure
kPa
14.7
10.7
18.7
Boost pressure
mmHg
110
80
140
Test data Ex:
Governor adjustment
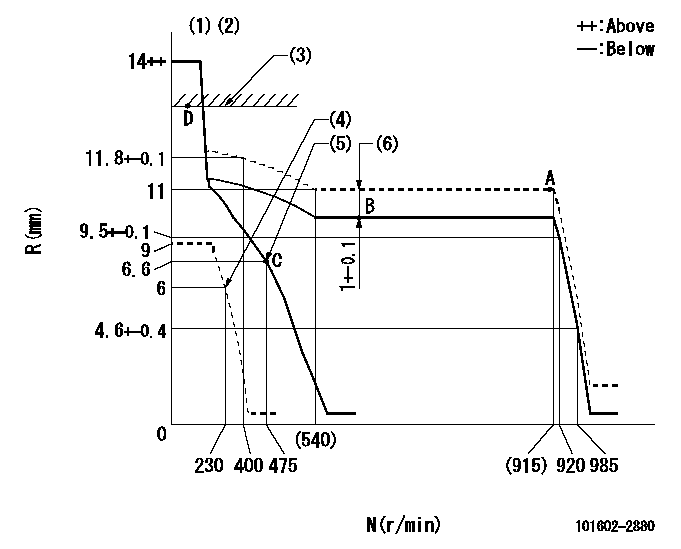
N:Pump speed
R:Rack position (mm)
(1)Target notch: K
(2)Tolerance for racks not indicated: +-0.05mm.
(3)RACK LIMIT
(4)Set idle sub-spring
(5)Main spring setting
(6)Boost compensator stroke
----------
K=5
----------
----------
K=5
----------
Speed control lever angle

F:Full speed
I:Idle
(1)Stopper bolt setting
----------
----------
a=0deg+-5deg b=18deg+-5deg
----------
----------
a=0deg+-5deg b=18deg+-5deg
Stop lever angle

N:Pump normal
S:Stop the pump.
(1)Pump speed aa and rack position bb (to be sealed at delivery)
----------
aa=0r/min bb=1-0.5mm
----------
a=21deg+-5deg b=(55deg)
----------
aa=0r/min bb=1-0.5mm
----------
a=21deg+-5deg b=(55deg)
Timing setting
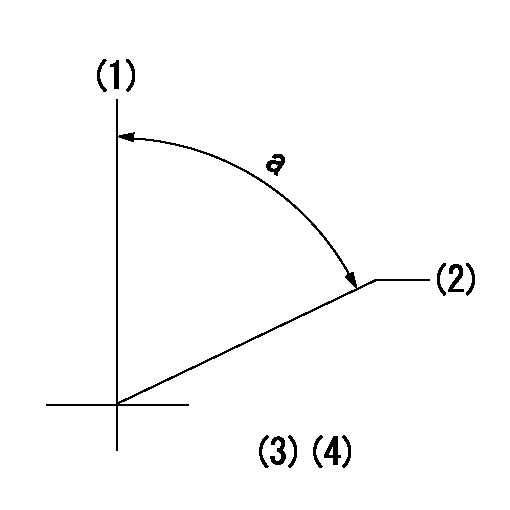
(1)Pump vertical direction
(2)Position of gear's standard threaded hole at No 1 cylinder's beginning of injection
(3)-
(4)-
----------
----------
a=(70deg)
----------
----------
a=(70deg)
Information:
Introduction
The problem that is identified below does not have a known permanent solution. Until a permanent solution is known, use the solution that is identified below.Problem
There have been some instances of the following active diagnostic codes:
651-6 Engine Injector Cylinder #01 : Current Above Normal
652-6 Engine Injector Cylinder #02 : Current Above Normal
653-6 Engine Injector Cylinder #03 : Current Above Normal
654-6 Engine Injector Cylinder #04 : Current Above NormalThe engine will be derated and will be difficult to start.Solution
Follow the correct troubleshooting procedure for the active diagnostic codes. Refer to Troubleshooting, Injector Solenoid - Test.
If the troubleshooting procedure identifies suspect injectors, use the electronic service tool to generate a Product Status Report (PSR). Select the "Histogram" option when generating the PSR.
Install replacement 418-3229 Fuel Injector Gp, as required. Refer to Disassembly and Assembly, Electronic Unit Injector - Remove and Disassembly and Assembly, Electronic Unit Injector - Install.
Use 169-7372 Fluid Sampling Bottles to obtain a fuel sample from the following locations:
Machine fuel tank ( 355 mL (12 oz)
Bulk fuel supply tank ( 355 mL (12 oz)Analyze the fuel sample. The fuel samples will need to be analyzed for the following properties:
Lubricity Wear Scar - "ASTM D6079" or "ISO 12156"
Density at 15° C (59° F) - "ASTM D1298", "ASTM D4052", "ISO 3675", or "ISO 12185"
Kinematic Viscosity at 40° C (104° F) - "ASTM D445", "ISO 3448", or "ISO 3104"
Sulfur - "ASTM D4294", "ASTM D5185", "ASTM D5453", "ASTM D26222", "ISO 20846", or "ISO 20884"
Water by Distillation - "ASTM D95", "ASTM D6304", "ASTM D2709", "ASTM D1796", or "ISO3734"
Cloud Point - "ASTM D2500" or "ISO 3015"
FAME - "EN 14078", "ASTM D7806", or "ASTM D7371"
Oxidation Stability - "EN 14112"
Copper - "ASTM D7111"
Sodium - "ASTM D7111"
Zinc - "ASTM D7111"
Calcium - "ASTM D7111"
Potassium - "ASTM D7111"Provide the results of the fuel sample.
Retain any removed injectors. The injectors will be requested for return through the "Send It Back" (SIB) process.
Submit the PSR along with TIB Media number, M0085259, and CPI number 386169 through "CPI Feedback" within the Service Information Management System (SIMSi).
The problem that is identified below does not have a known permanent solution. Until a permanent solution is known, use the solution that is identified below.Problem
There have been some instances of the following active diagnostic codes:
651-6 Engine Injector Cylinder #01 : Current Above Normal
652-6 Engine Injector Cylinder #02 : Current Above Normal
653-6 Engine Injector Cylinder #03 : Current Above Normal
654-6 Engine Injector Cylinder #04 : Current Above NormalThe engine will be derated and will be difficult to start.Solution
Follow the correct troubleshooting procedure for the active diagnostic codes. Refer to Troubleshooting, Injector Solenoid - Test.
If the troubleshooting procedure identifies suspect injectors, use the electronic service tool to generate a Product Status Report (PSR). Select the "Histogram" option when generating the PSR.
Install replacement 418-3229 Fuel Injector Gp, as required. Refer to Disassembly and Assembly, Electronic Unit Injector - Remove and Disassembly and Assembly, Electronic Unit Injector - Install.
Use 169-7372 Fluid Sampling Bottles to obtain a fuel sample from the following locations:
Machine fuel tank ( 355 mL (12 oz)
Bulk fuel supply tank ( 355 mL (12 oz)Analyze the fuel sample. The fuel samples will need to be analyzed for the following properties:
Lubricity Wear Scar - "ASTM D6079" or "ISO 12156"
Density at 15° C (59° F) - "ASTM D1298", "ASTM D4052", "ISO 3675", or "ISO 12185"
Kinematic Viscosity at 40° C (104° F) - "ASTM D445", "ISO 3448", or "ISO 3104"
Sulfur - "ASTM D4294", "ASTM D5185", "ASTM D5453", "ASTM D26222", "ISO 20846", or "ISO 20884"
Water by Distillation - "ASTM D95", "ASTM D6304", "ASTM D2709", "ASTM D1796", or "ISO3734"
Cloud Point - "ASTM D2500" or "ISO 3015"
FAME - "EN 14078", "ASTM D7806", or "ASTM D7371"
Oxidation Stability - "EN 14112"
Copper - "ASTM D7111"
Sodium - "ASTM D7111"
Zinc - "ASTM D7111"
Calcium - "ASTM D7111"
Potassium - "ASTM D7111"Provide the results of the fuel sample.
Retain any removed injectors. The injectors will be requested for return through the "Send It Back" (SIB) process.
Submit the PSR along with TIB Media number, M0085259, and CPI number 386169 through "CPI Feedback" within the Service Information Management System (SIMSi).