Information injection-pump assembly
BOSCH
9 400 610 578
9400610578
ZEXEL
101602-2861
1016022861
HINO
220204841A
220204841a
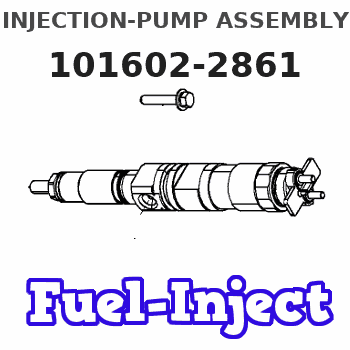
Rating:
Service parts 101602-2861 INJECTION-PUMP ASSEMBLY:
1.
_
5.
AUTOM. ADVANCE MECHANIS
7.
COUPLING PLATE
8.
_
9.
_
11.
Nozzle and Holder
23600-2133A
12.
Open Pre:MPa(Kqf/cm2)
19.6{200}
15.
NOZZLE SET
Cross reference number
BOSCH
9 400 610 578
9400610578
ZEXEL
101602-2861
1016022861
HINO
220204841A
220204841a
Zexel num
Bosch num
Firm num
Name
Calibration Data:
Adjustment conditions
Test oil
1404 Test oil ISO4113 or {SAEJ967d}
1404 Test oil ISO4113 or {SAEJ967d}
Test oil temperature
degC
40
40
45
Nozzle and nozzle holder
105780-8140
Bosch type code
EF8511/9A
Nozzle
105780-0000
Bosch type code
DN12SD12T
Nozzle holder
105780-2080
Bosch type code
EF8511/9
Opening pressure
MPa
17.2
Opening pressure
kgf/cm2
175
Injection pipe
Outer diameter - inner diameter - length (mm) mm 6-2-600
Outer diameter - inner diameter - length (mm) mm 6-2-600
Overflow valve
134424-0920
Overflow valve opening pressure
kPa
162
147
177
Overflow valve opening pressure
kgf/cm2
1.65
1.5
1.8
Tester oil delivery pressure
kPa
157
157
157
Tester oil delivery pressure
kgf/cm2
1.6
1.6
1.6
Direction of rotation (viewed from drive side)
Right R
Right R
Injection timing adjustment
Direction of rotation (viewed from drive side)
Right R
Right R
Injection order
1-4-2-6-
3-5
Pre-stroke
mm
4.8
4.77
4.83
Beginning of injection position
Drive side NO.1
Drive side NO.1
Difference between angles 1
Cal 1-4 deg. 60 59.75 60.25
Cal 1-4 deg. 60 59.75 60.25
Difference between angles 2
Cyl.1-2 deg. 120 119.75 120.25
Cyl.1-2 deg. 120 119.75 120.25
Difference between angles 3
Cal 1-6 deg. 180 179.75 180.25
Cal 1-6 deg. 180 179.75 180.25
Difference between angles 4
Cal 1-3 deg. 240 239.75 240.25
Cal 1-3 deg. 240 239.75 240.25
Difference between angles 5
Cal 1-5 deg. 300 299.75 300.25
Cal 1-5 deg. 300 299.75 300.25
Injection quantity adjustment
Adjusting point
A
Rack position
10
Pump speed
r/min
900
900
900
Average injection quantity
mm3/st.
116.5
115
118
Max. variation between cylinders
%
0
-3.5
3.5
Basic
*
Fixing the rack
*
Boost pressure
kPa
137
137
Boost pressure
mmHg
1030
1030
Injection quantity adjustment_02
Adjusting point
-
Rack position
6.8+-0.5
Pump speed
r/min
480
480
480
Average injection quantity
mm3/st.
10.5
9.5
11.5
Max. variation between cylinders
%
0
-10
10
Fixing the rack
*
Boost pressure
kPa
0
0
0
Boost pressure
mmHg
0
0
0
Remarks
Adjust only variation between cylinders; adjust governor according to governor specifications.
Adjust only variation between cylinders; adjust governor according to governor specifications.
Boost compensator adjustment
Pump speed
r/min
500
500
500
Rack position
R1-2
Boost pressure
kPa
66.7
64
69.4
Boost pressure
mmHg
500
480
520
Boost compensator adjustment_02
Pump speed
r/min
500
500
500
Rack position
R1(11.3)
Boost pressure
kPa
124
117.3
130.7
Boost pressure
mmHg
930
880
980
Test data Ex:
Governor adjustment
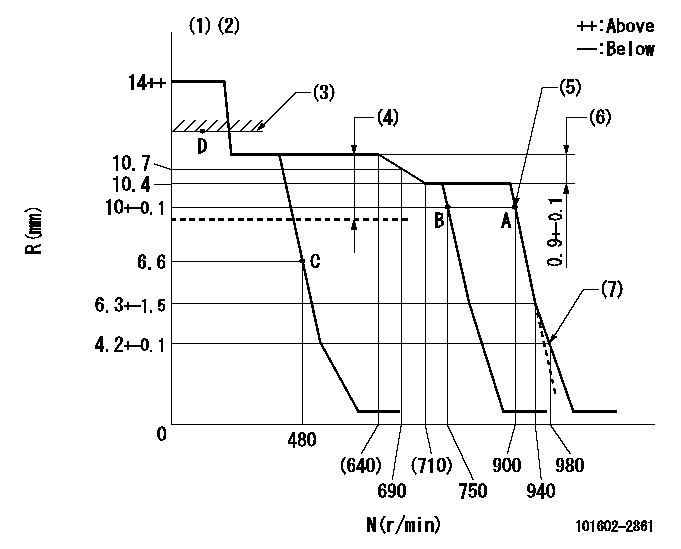
N:Pump speed
R:Rack position (mm)
(1)Notch fixed: K
(2)Tolerance for racks not indicated: +-0.05mm.
(3)Boost compensator excessive fuel lever at operation (at 0 boost pressure): L1
(4)Boost compensator stroke: BCL
(5)Main spring setting
(6)Rack difference between N = N1 and N = N2
(7)Set idle sub-spring
----------
K=9 L1=12.9+-0.1mm BCL=2+-0.1mm N1=850r/min N2=500r/min
----------
----------
K=9 L1=12.9+-0.1mm BCL=2+-0.1mm N1=850r/min N2=500r/min
----------
Speed control lever angle
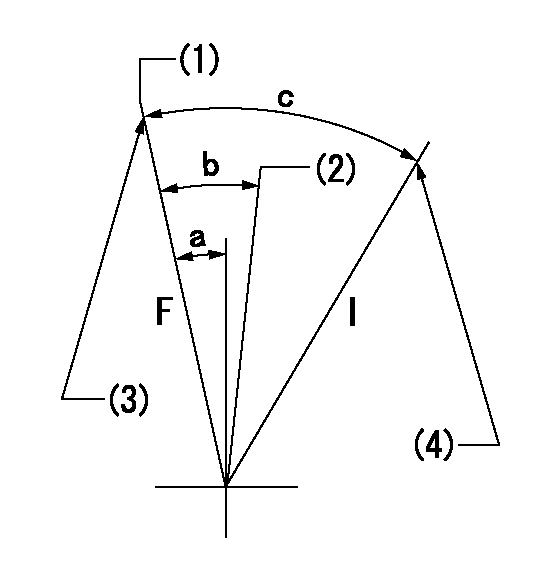
F:Full speed
I:Idle
(1)Set the pump speed at aa. ( At delivery )
(2)When pump speed set at bb
(3)Stopper bolt setting
(4)Stopper bolt setting
----------
aa=900r/min bb=750r/min
----------
a=(1deg)+-5deg b=(5deg)+-5deg c=(18deg)+-5deg
----------
aa=900r/min bb=750r/min
----------
a=(1deg)+-5deg b=(5deg)+-5deg c=(18deg)+-5deg
Stop lever angle

N:Pump normal
S:Stop the pump.
(1)Rack position aa or less, pump speed bb
----------
aa=6.1mm bb=0r/min
----------
a=27deg+-5deg b=53deg+-5deg
----------
aa=6.1mm bb=0r/min
----------
a=27deg+-5deg b=53deg+-5deg
0000001101
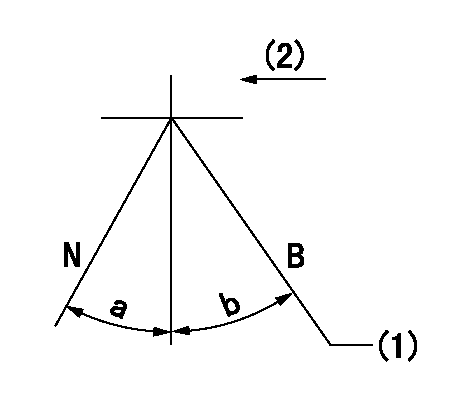
N:Normal
B:When boosted
(1)Rack position = aa (point D) at boost pressure 0.
(2)Drive side
----------
aa=12.9+-0.1mm
----------
a=(15deg) b=(11deg)
----------
aa=12.9+-0.1mm
----------
a=(15deg) b=(11deg)
Timing setting
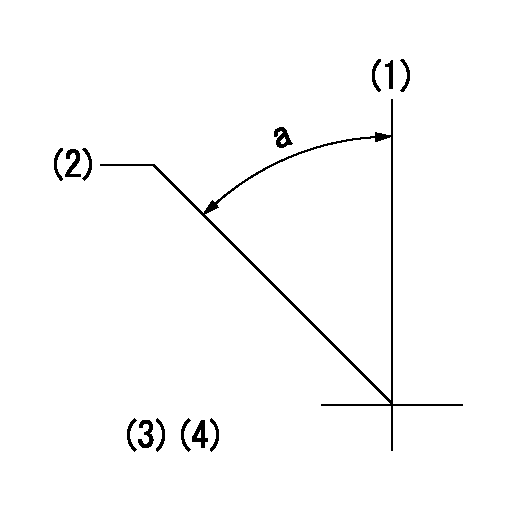
(1)Pump vertical direction
(2)Coupling's key groove position at No 1 cylinder's beginning of injection
(3)-
(4)-
----------
----------
a=(50deg)
----------
----------
a=(50deg)
Information:
Bulk storage
Follow all local regulations covering bulk storage tanks. Follow proper tank construction guidelines. Tank volume typically should be 110% of planned capacity. Appropriately vent indoor tanks. Plan for control of overflow of the tank. Heat tanks that dispense DEF in cold climates.Bulk tank breathers should be fitted with filtration to keep airborne debris from entering the tank. Desiccant breathers should not be used because water will be absorbed, which potentially can alter DEF concentration.Handling
Follow all local regulations covering transport and handling. DEF transport temperature is recommended to be −5° C (23° F) to 25° C (77° F). All transfer equipment and intermediate containers should be used exclusively for DEF. Containers should not be reused for any other fluids. Ensure that transfer equipment is made from DEF-compatible materials. Recommended material for hoses and other non-metallic transfer equipment include:
Nitrile Rubber (NBR)
Fluoroelastomer (FKM)
Ethylene Propylene Diane Ionomer (EPDM)The condition of hoses and other nonmetallic items that are used with DEF should be monitored for signs of degradation. DEF leaks are easily recognizable by white urea crystals that accumulate at the site of the leak. Solid urea can be corrosive to galvanized or unalloyed steel, aluminum, copper, and brass. Leaks should be repaired immediately to avoid damage to surrounding hardware.Cleanliness
Contaminants can degrade the quality and life of DEF. Filtering DEF is recommended when dispensed into the DEF tank. Filters should be compatible with DEF and should be used exclusively with DEF. Check with the filter supplier to confirm compatibility with DEF before using. Mesh-type filters using compatible metals, such as stainless steel, are recommended. Paper (cellulose) media and some synthetic filter media are not recommended because of degradation during use.Care should be taken when dispensing DEF. Spills should be cleaned immediately. Machine or engine surfaces should be wiped clean and rinsed with water. Caution should be used when dispensing DEF near an engine that has recently been running.Note: Spilling DEF onto hot components may cause the release of ammonia vapors. Do not breathe ammonia vapors. Do not clean up any spills with bleach.Stability
DEF fluid is stable when stored and handled properly. The quality of DEF rapidly degrades when stored at high temperatures. The ideal storage temperature for DEF is between −9° C (15.8° F) and 25° C (77° F). DEF that is stored above 35° C (95° F) for longer than 1 month must be tested before use. Testing should evaluate Urea Percentage, Alkalinity as NH3 and Biuret content.The length of storage of DEF is listed in the following table:
Table 3
Storage Temperature Expected DEF Life
Below 25° C (77° F) 18 months
25° C (77° F) to 30° C (86° F) 12 months
30° C (86° F) to 35° C (95° F) 6 months
Above 35° C (95° F) test quality before use Refer to "ISO 22241" document series for more information about DEF quality control.Note: Dispose of all fluids according to applicable regulations and mandates.General Characteristics of DEF
For detailed information on the requirements and
Follow all local regulations covering bulk storage tanks. Follow proper tank construction guidelines. Tank volume typically should be 110% of planned capacity. Appropriately vent indoor tanks. Plan for control of overflow of the tank. Heat tanks that dispense DEF in cold climates.Bulk tank breathers should be fitted with filtration to keep airborne debris from entering the tank. Desiccant breathers should not be used because water will be absorbed, which potentially can alter DEF concentration.Handling
Follow all local regulations covering transport and handling. DEF transport temperature is recommended to be −5° C (23° F) to 25° C (77° F). All transfer equipment and intermediate containers should be used exclusively for DEF. Containers should not be reused for any other fluids. Ensure that transfer equipment is made from DEF-compatible materials. Recommended material for hoses and other non-metallic transfer equipment include:
Nitrile Rubber (NBR)
Fluoroelastomer (FKM)
Ethylene Propylene Diane Ionomer (EPDM)The condition of hoses and other nonmetallic items that are used with DEF should be monitored for signs of degradation. DEF leaks are easily recognizable by white urea crystals that accumulate at the site of the leak. Solid urea can be corrosive to galvanized or unalloyed steel, aluminum, copper, and brass. Leaks should be repaired immediately to avoid damage to surrounding hardware.Cleanliness
Contaminants can degrade the quality and life of DEF. Filtering DEF is recommended when dispensed into the DEF tank. Filters should be compatible with DEF and should be used exclusively with DEF. Check with the filter supplier to confirm compatibility with DEF before using. Mesh-type filters using compatible metals, such as stainless steel, are recommended. Paper (cellulose) media and some synthetic filter media are not recommended because of degradation during use.Care should be taken when dispensing DEF. Spills should be cleaned immediately. Machine or engine surfaces should be wiped clean and rinsed with water. Caution should be used when dispensing DEF near an engine that has recently been running.Note: Spilling DEF onto hot components may cause the release of ammonia vapors. Do not breathe ammonia vapors. Do not clean up any spills with bleach.Stability
DEF fluid is stable when stored and handled properly. The quality of DEF rapidly degrades when stored at high temperatures. The ideal storage temperature for DEF is between −9° C (15.8° F) and 25° C (77° F). DEF that is stored above 35° C (95° F) for longer than 1 month must be tested before use. Testing should evaluate Urea Percentage, Alkalinity as NH3 and Biuret content.The length of storage of DEF is listed in the following table:
Table 3
Storage Temperature Expected DEF Life
Below 25° C (77° F) 18 months
25° C (77° F) to 30° C (86° F) 12 months
30° C (86° F) to 35° C (95° F) 6 months
Above 35° C (95° F) test quality before use Refer to "ISO 22241" document series for more information about DEF quality control.Note: Dispose of all fluids according to applicable regulations and mandates.General Characteristics of DEF
For detailed information on the requirements and