Information injection-pump assembly
ZEXEL
101602-2660
1016022660
HINO
220203910A
220203910a

Rating:
Service parts 101602-2660 INJECTION-PUMP ASSEMBLY:
1.
_
5.
AUTOM. ADVANCE MECHANIS
7.
COUPLING PLATE
8.
_
9.
_
11.
Nozzle and Holder
23600-2133A
12.
Open Pre:MPa(Kqf/cm2)
19.6{200}
15.
NOZZLE SET
Cross reference number
ZEXEL
101602-2660
1016022660
HINO
220203910A
220203910a
Zexel num
Bosch num
Firm num
Name
Calibration Data:
Adjustment conditions
Test oil
1404 Test oil ISO4113 or {SAEJ967d}
1404 Test oil ISO4113 or {SAEJ967d}
Test oil temperature
degC
40
40
45
Nozzle and nozzle holder
105780-8140
Bosch type code
EF8511/9A
Nozzle
105780-0000
Bosch type code
DN12SD12T
Nozzle holder
105780-2080
Bosch type code
EF8511/9
Opening pressure
MPa
17.2
Opening pressure
kgf/cm2
175
Injection pipe
Outer diameter - inner diameter - length (mm) mm 6-2-600
Outer diameter - inner diameter - length (mm) mm 6-2-600
Overflow valve
134424-0920
Overflow valve opening pressure
kPa
162
147
177
Overflow valve opening pressure
kgf/cm2
1.65
1.5
1.8
Tester oil delivery pressure
kPa
157
157
157
Tester oil delivery pressure
kgf/cm2
1.6
1.6
1.6
Direction of rotation (viewed from drive side)
Right R
Right R
Injection timing adjustment
Direction of rotation (viewed from drive side)
Right R
Right R
Injection order
1-4-2-6-
3-5
Pre-stroke
mm
3.8
3.77
3.83
Beginning of injection position
Drive side NO.1
Drive side NO.1
Difference between angles 1
Cal 1-4 deg. 60 59.75 60.25
Cal 1-4 deg. 60 59.75 60.25
Difference between angles 2
Cyl.1-2 deg. 120 119.75 120.25
Cyl.1-2 deg. 120 119.75 120.25
Difference between angles 3
Cal 1-6 deg. 180 179.75 180.25
Cal 1-6 deg. 180 179.75 180.25
Difference between angles 4
Cal 1-3 deg. 240 239.75 240.25
Cal 1-3 deg. 240 239.75 240.25
Difference between angles 5
Cal 1-5 deg. 300 299.75 300.25
Cal 1-5 deg. 300 299.75 300.25
Injection quantity adjustment
Adjusting point
A
Rack position
9.5
Pump speed
r/min
1250
1250
1250
Average injection quantity
mm3/st.
98.4
96.4
100.4
Max. variation between cylinders
%
0
-3.5
3.5
Basic
*
Fixing the lever
*
Injection quantity adjustment_02
Adjusting point
-
Rack position
6.1+-0.5
Pump speed
r/min
650
650
650
Average injection quantity
mm3/st.
10
9
11
Max. variation between cylinders
%
0
-10
10
Fixing the rack
*
Remarks
Adjust only variation between cylinders; adjust governor according to governor specifications.
Adjust only variation between cylinders; adjust governor according to governor specifications.
Test data Ex:
Governor adjustment
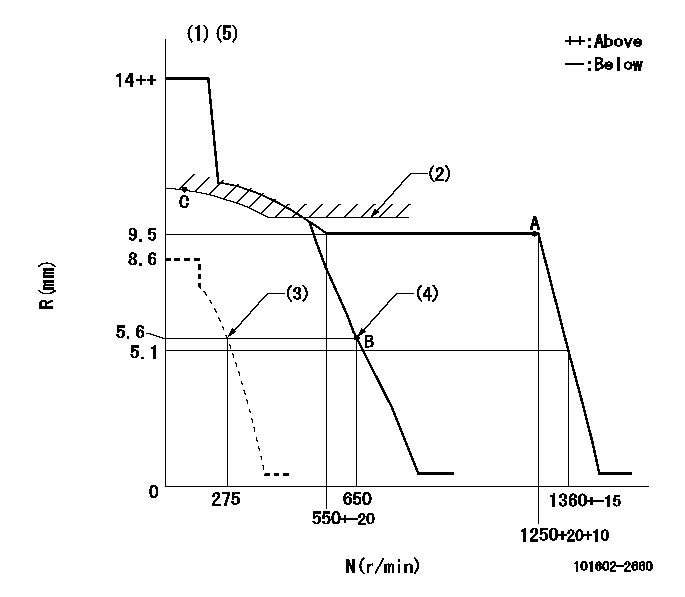
N:Pump speed
R:Rack position (mm)
(1)Target notch: K
(2)SMA RACK LIMIT; RAL
(3)Set idle sub-spring
(4)Main spring setting
(5)Perform governor adjustment at an ambient temperature of at least 15 deg C (rack limit spring is shape memory alloy).
----------
K=12 RAL=9.7+0.2mm
----------
----------
K=12 RAL=9.7+0.2mm
----------
Speed control lever angle
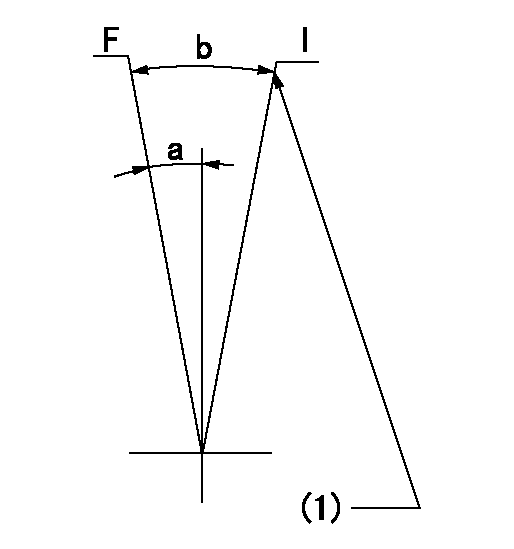
F:Full speed
I:Idle
(1)Stopper bolt setting
----------
----------
a=10deg+-5deg b=18deg+-5deg
----------
----------
a=10deg+-5deg b=18deg+-5deg
Stop lever angle
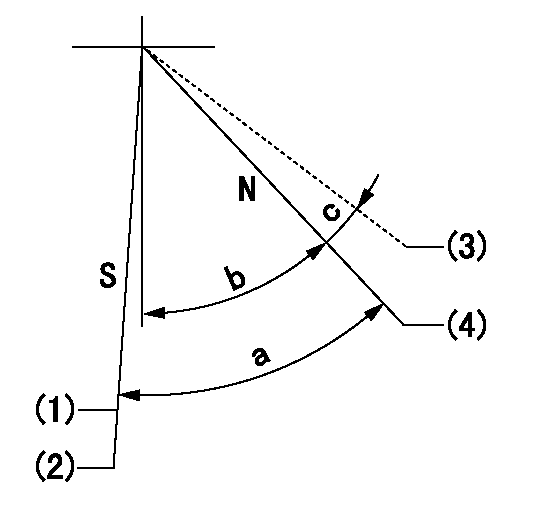
N:Pump normal
S:Stop the pump.
(1)Rack position aa or less, pump speed bb
(2)At delivery
(3)Contacts normal side pin
(4)Clearance from the pin on the normal side: cc
----------
aa=5.1mm bb=0r/min cc=2.5+-0.5mm
----------
a=53deg+-5deg b=51deg+-5deg c=(6deg)
----------
aa=5.1mm bb=0r/min cc=2.5+-0.5mm
----------
a=53deg+-5deg b=51deg+-5deg c=(6deg)
Timing setting
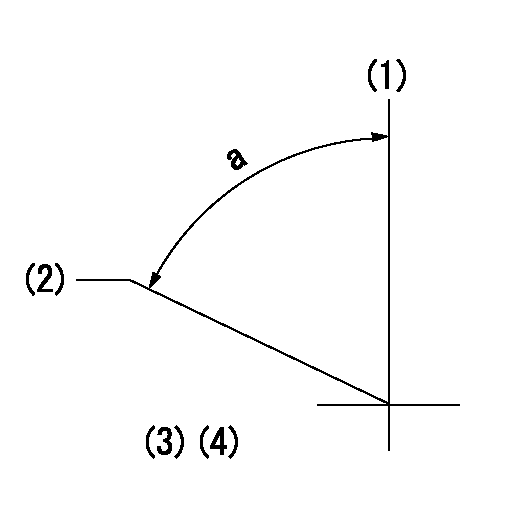
(1)Pump vertical direction
(2)Coupling's key groove position at No 1 cylinder's beginning of injection
(3)-
(4)-
----------
----------
a=(50deg)
----------
----------
a=(50deg)
Information:
Introduction
The problem that is identified below does not have a known permanent solution. Until a permanent solution is known, use the solution that is identified below.Problem
Elevated sodium in the oil samples.Solution
If the source of the sodium cannot be isolated via other normal testing of individual components (water pumps, oil coolers, and so on), then complete the following procedure:
Shut down the engine and allow system to cool.
Flip the ground level shutdown switch on the truck front bumper and leave the switch engaged. This action disables the fuel injection.
Verify that the engine will crank but the engine does NOT start.
Pull the last exhaust manifold from each bank of the engine.
Pressurize the truck cooling system, refer to Testing and Adjusting, KENR5397 for additional information.
Hold pressure on the cooling system for no more than 10 minutes for the first test. If the leak is bad, holding the pressure too long could risk hydraulic lock.
Illustration 1 g06059950
While cranking the engine, shine a light up into the exhaust manifolds and look for cylinders that are puffing steam and white smoke.
Verify any leaks by pulling the exhaust thermocouple port from the exhaust runner on that cylinder. Check for signs of moisture/steaming in that exhaust runner.
Repair any leaking injector sleeve by replacing the head.
The problem that is identified below does not have a known permanent solution. Until a permanent solution is known, use the solution that is identified below.Problem
Elevated sodium in the oil samples.Solution
If the source of the sodium cannot be isolated via other normal testing of individual components (water pumps, oil coolers, and so on), then complete the following procedure:
Shut down the engine and allow system to cool.
Flip the ground level shutdown switch on the truck front bumper and leave the switch engaged. This action disables the fuel injection.
Verify that the engine will crank but the engine does NOT start.
Pull the last exhaust manifold from each bank of the engine.
Pressurize the truck cooling system, refer to Testing and Adjusting, KENR5397 for additional information.
Hold pressure on the cooling system for no more than 10 minutes for the first test. If the leak is bad, holding the pressure too long could risk hydraulic lock.
Illustration 1 g06059950
While cranking the engine, shine a light up into the exhaust manifolds and look for cylinders that are puffing steam and white smoke.
Verify any leaks by pulling the exhaust thermocouple port from the exhaust runner on that cylinder. Check for signs of moisture/steaming in that exhaust runner.
Repair any leaking injector sleeve by replacing the head.