Information injection-pump assembly
BOSCH
9 400 614 782
9400614782
ZEXEL
101602-2550
1016022550
HINO
220203780A
220203780a

Rating:
Service parts 101602-2550 INJECTION-PUMP ASSEMBLY:
1.
_
5.
AUTOM. ADVANCE MECHANIS
6.
COUPLING PLATE
8.
_
9.
_
11.
Nozzle and Holder
23600-1710A
12.
Open Pre:MPa(Kqf/cm2)
21.6{220}
15.
NOZZLE SET
Include in #1:
101602-2550
as INJECTION-PUMP ASSEMBLY
Include in #2:
104257-3040
as _
Cross reference number
BOSCH
9 400 614 782
9400614782
ZEXEL
101602-2550
1016022550
HINO
220203780A
220203780a
Zexel num
Bosch num
Firm num
Name
101602-2550
9 400 614 782
220203780A HINO
INJECTION-PUMP ASSEMBLY
W06D-T * K
W06D-T * K
Calibration Data:
Adjustment conditions
Test oil
1404 Test oil ISO4113 or {SAEJ967d}
1404 Test oil ISO4113 or {SAEJ967d}
Test oil temperature
degC
40
40
45
Nozzle and nozzle holder
105780-8140
Bosch type code
EF8511/9A
Nozzle
105780-0000
Bosch type code
DN12SD12T
Nozzle holder
105780-2080
Bosch type code
EF8511/9
Opening pressure
MPa
17.2
Opening pressure
kgf/cm2
175
Injection pipe
Outer diameter - inner diameter - length (mm) mm 6-2-600
Outer diameter - inner diameter - length (mm) mm 6-2-600
Overflow valve
131424-5720
Overflow valve opening pressure
kPa
255
221
289
Overflow valve opening pressure
kgf/cm2
2.6
2.25
2.95
Tester oil delivery pressure
kPa
157
157
157
Tester oil delivery pressure
kgf/cm2
1.6
1.6
1.6
Direction of rotation (viewed from drive side)
Right R
Right R
Injection timing adjustment
Direction of rotation (viewed from drive side)
Right R
Right R
Injection order
1-4-2-6-
3-5
Pre-stroke
mm
3.1
3.05
3.15
Beginning of injection position
Drive side NO.1
Drive side NO.1
Difference between angles 1
Cal 1-4 deg. 60 59.5 60.5
Cal 1-4 deg. 60 59.5 60.5
Difference between angles 2
Cyl.1-2 deg. 120 119.5 120.5
Cyl.1-2 deg. 120 119.5 120.5
Difference between angles 3
Cal 1-6 deg. 180 179.5 180.5
Cal 1-6 deg. 180 179.5 180.5
Difference between angles 4
Cal 1-3 deg. 240 239.5 240.5
Cal 1-3 deg. 240 239.5 240.5
Difference between angles 5
Cal 1-5 deg. 300 299.5 300.5
Cal 1-5 deg. 300 299.5 300.5
Injection quantity adjustment
Adjusting point
A
Rack position
9.5
Pump speed
r/min
1250
1250
1250
Average injection quantity
mm3/st.
68.1
65.1
71.1
Max. variation between cylinders
%
0
-3
3
Basic
*
Fixing the lever
*
Injection quantity adjustment_02
Adjusting point
B
Rack position
7.6+-0.5
Pump speed
r/min
315
315
315
Average injection quantity
mm3/st.
9.5
8
11
Max. variation between cylinders
%
0
-15
15
Fixing the rack
*
Injection quantity adjustment_03
Adjusting point
C
Rack position
-
Pump speed
r/min
100
100
100
Average injection quantity
mm3/st.
100
100
110
Fixing the lever
*
Rack limit
*
Test data Ex:
Governor adjustment
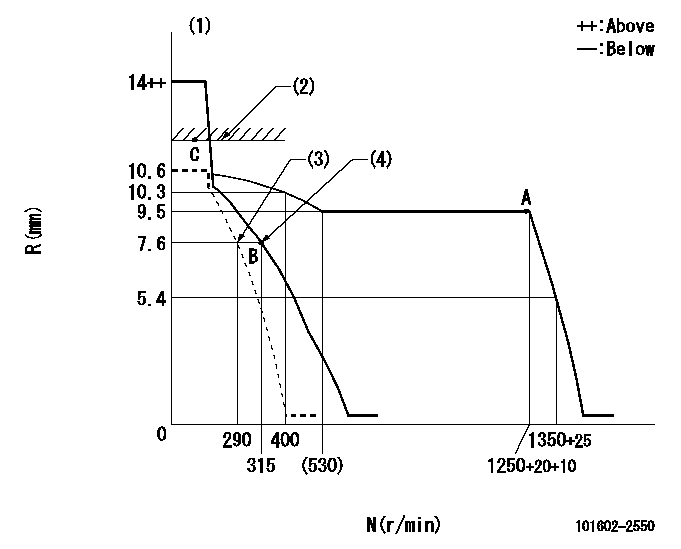
N:Pump speed
R:Rack position (mm)
(1)Target notch: K
(2)RACK LIMIT
(3)Set idle sub-spring
(4)Main spring setting
----------
K=8
----------
----------
K=8
----------
Speed control lever angle

F:Full speed
I:Idle
(1)Stopper bolt setting
----------
----------
a=5deg+-5deg b=25deg+-5deg
----------
----------
a=5deg+-5deg b=25deg+-5deg
Stop lever angle

N:Pump normal
S:Stop the pump.
(1)Rack position aa or less, pump speed bb
----------
----------
a=27deg+-5deg b=53deg+-5deg
----------
----------
a=27deg+-5deg b=53deg+-5deg
Timing setting
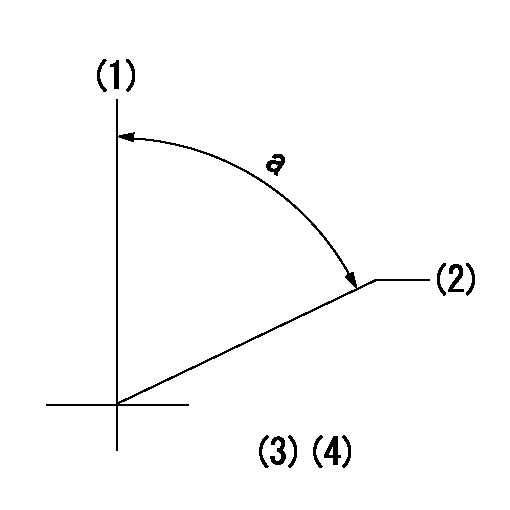
(1)Pump vertical direction
(2)Position of gear's standard threaded hole at No 1 cylinder's beginning of injection
(3)-
(4)-
----------
----------
a=(70deg)
----------
----------
a=(70deg)
Information:
Introduction
Do not perform any procedure that is outlined in the Special Instruction until the entire instruction has been read and understood.Check Valve Torque
Care must be taken to ensure that fluids are contained during performance of inspection, maintenance, testing, adjusting, and repair of the product. Be prepared to collect the fluid with suitable containers before opening any compartment or disassembling any component containing fluids.Refer to Special Publication, NENG2500, "Dealer Service Tool Catalog" for tools and supplies suitable to collect and contain fluids on Cat products.Dispose of all fluids according to local regulations and mandates.
The check valves that are located within the fuel pressure regulator group are sensitive to assembly torque. In order to eliminate the risk of valve distortion, torque the check valves to 28 3 N m (21 2 lb ft). Refer to Table 1 for the check valve part numbers that required the torque that is listed above.
Table 1
Part Number     Description    
327-0376     Check Valve Gp    
327-4448     Check Valve Gp    
281-2725     Check Valve Gp    
282-1915     Check Valve Gp    
228-7381     Check Valve Gp    
327-8044     Check Valve Gp    
Do not perform any procedure that is outlined in the Special Instruction until the entire instruction has been read and understood.Check Valve Torque
Care must be taken to ensure that fluids are contained during performance of inspection, maintenance, testing, adjusting, and repair of the product. Be prepared to collect the fluid with suitable containers before opening any compartment or disassembling any component containing fluids.Refer to Special Publication, NENG2500, "Dealer Service Tool Catalog" for tools and supplies suitable to collect and contain fluids on Cat products.Dispose of all fluids according to local regulations and mandates.
The check valves that are located within the fuel pressure regulator group are sensitive to assembly torque. In order to eliminate the risk of valve distortion, torque the check valves to 28 3 N m (21 2 lb ft). Refer to Table 1 for the check valve part numbers that required the torque that is listed above.
Table 1
Part Number     Description    
327-0376     Check Valve Gp    
327-4448     Check Valve Gp    
281-2725     Check Valve Gp    
282-1915     Check Valve Gp    
228-7381     Check Valve Gp    
327-8044     Check Valve Gp    
Have questions with 101602-2550?
Group cross 101602-2550 ZEXEL
Hino
101602-2550
9 400 614 782
220203780A
INJECTION-PUMP ASSEMBLY
W06D-T
W06D-T