Information injection-pump assembly
BOSCH
9 400 614 777
9400614777
ZEXEL
101602-2500
1016022500
HINO
220203630A
220203630a
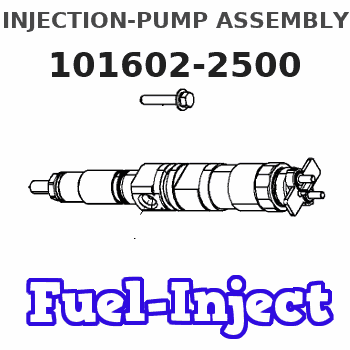
Rating:
Service parts 101602-2500 INJECTION-PUMP ASSEMBLY:
1.
_
5.
AUTOM. ADVANCE MECHANIS
6.
COUPLING PLATE
8.
_
9.
_
11.
Nozzle and Holder
23600-1593A
12.
Open Pre:MPa(Kqf/cm2)
21.6{220}
15.
NOZZLE SET
Include in #1:
101602-2500
as INJECTION-PUMP ASSEMBLY
Include in #2:
104234-2011
as _
Cross reference number
BOSCH
9 400 614 777
9400614777
ZEXEL
101602-2500
1016022500
HINO
220203630A
220203630a
Zexel num
Bosch num
Firm num
Name
101602-2500
9 400 614 777
220203630A HINO
INJECTION-PUMP ASSEMBLY
W06D K 14BE INJECTION PUMP ASSY PE6A PE
W06D K 14BE INJECTION PUMP ASSY PE6A PE
Calibration Data:
Adjustment conditions
Test oil
1404 Test oil ISO4113 or {SAEJ967d}
1404 Test oil ISO4113 or {SAEJ967d}
Test oil temperature
degC
40
40
45
Nozzle and nozzle holder
105780-8140
Bosch type code
EF8511/9A
Nozzle
105780-0000
Bosch type code
DN12SD12T
Nozzle holder
105780-2080
Bosch type code
EF8511/9
Opening pressure
MPa
17.2
Opening pressure
kgf/cm2
175
Injection pipe
Outer diameter - inner diameter - length (mm) mm 6-2-600
Outer diameter - inner diameter - length (mm) mm 6-2-600
Overflow valve
131424-5720
Overflow valve opening pressure
kPa
255
221
289
Overflow valve opening pressure
kgf/cm2
2.6
2.25
2.95
Tester oil delivery pressure
kPa
157
157
157
Tester oil delivery pressure
kgf/cm2
1.6
1.6
1.6
Direction of rotation (viewed from drive side)
Right R
Right R
Injection timing adjustment
Direction of rotation (viewed from drive side)
Right R
Right R
Injection order
1-4-2-6-
3-5
Pre-stroke
mm
3.1
3.05
3.15
Beginning of injection position
Drive side NO.1
Drive side NO.1
Difference between angles 1
Cal 1-4 deg. 60 59.5 60.5
Cal 1-4 deg. 60 59.5 60.5
Difference between angles 2
Cyl.1-2 deg. 120 119.5 120.5
Cyl.1-2 deg. 120 119.5 120.5
Difference between angles 3
Cal 1-6 deg. 180 179.5 180.5
Cal 1-6 deg. 180 179.5 180.5
Difference between angles 4
Cal 1-3 deg. 240 239.5 240.5
Cal 1-3 deg. 240 239.5 240.5
Difference between angles 5
Cal 1-5 deg. 300 299.5 300.5
Cal 1-5 deg. 300 299.5 300.5
Injection quantity adjustment
Adjusting point
A
Rack position
9.1
Pump speed
r/min
800
800
800
Average injection quantity
mm3/st.
38.7
36.7
40.7
Max. variation between cylinders
%
0
-3
3
Basic
*
Fixing the lever
*
Injection quantity adjustment_02
Adjusting point
C
Rack position
8.6+-0.5
Pump speed
r/min
360
360
360
Average injection quantity
mm3/st.
9.8
8.3
11.3
Max. variation between cylinders
%
0
-15
15
Fixing the rack
*
Injection quantity adjustment_03
Adjusting point
D
Rack position
-
Pump speed
r/min
100
100
100
Average injection quantity
mm3/st.
95
95
105
Fixing the lever
*
Rack limit
*
Test data Ex:
Governor adjustment
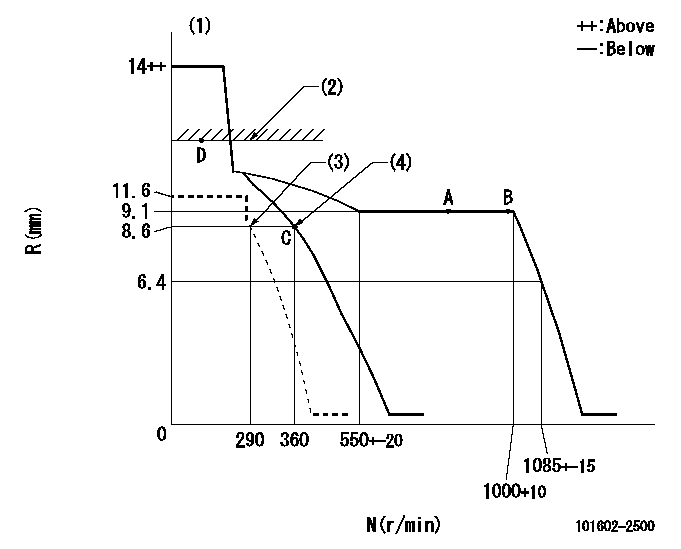
N:Pump speed
R:Rack position (mm)
(1)Target notch: K
(2)RACK LIMIT
(3)Set idle sub-spring
(4)Main spring setting
----------
K=9
----------
----------
K=9
----------
Speed control lever angle

F:Full speed
I:Idle
(1)Stopper bolt setting
----------
----------
a=0deg+-5deg b=20deg+-5deg
----------
----------
a=0deg+-5deg b=20deg+-5deg
Stop lever angle

N:Pump normal
S:Stop the pump.
(1)Rack position aa or less, pump speed bb
----------
aa=8.1mm bb=0r/min
----------
a=27deg+-5deg b=53deg+-5deg
----------
aa=8.1mm bb=0r/min
----------
a=27deg+-5deg b=53deg+-5deg
Timing setting
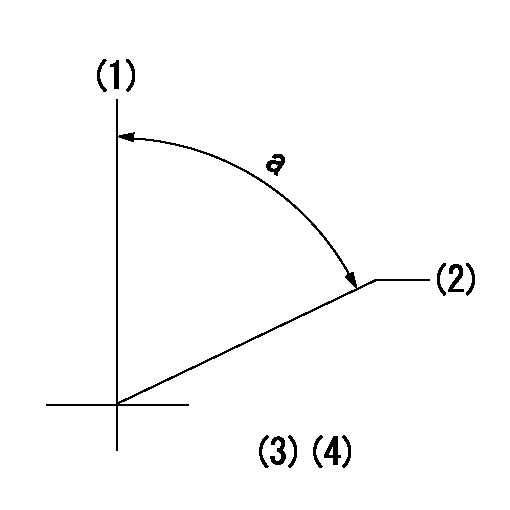
(1)Pump vertical direction
(2)Position of gear's standard threaded hole at No 1 cylinder's beginning of injection
(3)-
(4)-
----------
----------
a=(70deg)
----------
----------
a=(70deg)
Information:
Table 1
Required Parts
Qty Part Number Part Name Former Part Number
1 494-6233 Injector 307-3245(1)
(1) The former part number listed is for reference only and may differ.
Do not operate or work on this product unless you have read and understood the instruction and warnings in the relevant Operation and Maintenance Manuals and relevant service literature. Failure to follow the instructions or heed the warnings could result in injury or death. Proper care is your responsibility.
"The improved autolube injector requires a new adjustment sleeve. Follow the procedure below for the selection and adjustment of the sleeve.Changing the Metering Unit
Illustration 1 g06607746
(A) Adjustment Screw
(B) Locknut
(C) Adjustment Sleeve
Table 2
Adjustment Sleeves
Caterpillar Part Number Part Name Output cc Sleeve Color
494-6245 Sleeve 0.25 cc (0.015 cubic inch) Pink
494-6241 Sleeve 0.50 cc (0.030 cubic inch) Red
494-6242 Sleeve 0.750 cc (0.045 cubic inch) Silver
494-6243 Sleeve 1.00 cc (0.06 cubic inch) Gold
494-6244 Sleeve 1.25 cc (0.075 cubic inch) Green The automatic lubrication system offers the ability to change the amount of grease that is supplied per cycle to each grease point. Changing the grease supply amount is completed by adjusting locknut (B) or replacing adjustment sleeve (C) on the injector. See Table 2 for reference.There is a set of color-coded anodized aluminum adjustment sleeves (C) available for various lubrication dispensing amounts. Adjustment sleeves (C) provide an easy way to adjust the output of the injectors and provide a clear indication of the output setting. Adjustment sleeves (C) allow for easy system installation and preventative maintenance.Install adjustment sleeves (C) by doing the following Steps below:
Remove and discard locknut (B).
Place adjustment sleeve (C) on adjustment screw (A).
Tighten adjustment screw (A) to 6.7 N m (60 lb in).
Have questions with 101602-2500?
Group cross 101602-2500 ZEXEL
Hino
101602-2500
9 400 614 777
220203630A
INJECTION-PUMP ASSEMBLY
W06D
W06D