Information injection-pump assembly
BOSCH
9 400 614 771
9400614771
ZEXEL
101602-2411
1016022411
HINO
220203361A
220203361a
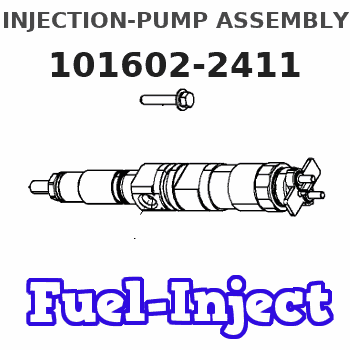
Rating:
Service parts 101602-2411 INJECTION-PUMP ASSEMBLY:
1.
_
5.
AUTOM. ADVANCE MECHANIS
6.
COUPLING PLATE
8.
_
9.
_
11.
Nozzle and Holder
23600-1593A
12.
Open Pre:MPa(Kqf/cm2)
21.6{220}
15.
NOZZLE SET
Cross reference number
BOSCH
9 400 614 771
9400614771
ZEXEL
101602-2411
1016022411
HINO
220203361A
220203361a
Zexel num
Bosch num
Firm num
Name
101602-2411
9 400 614 771
220203361A HINO
INJECTION-PUMP ASSEMBLY
W06D K
W06D K
Calibration Data:
Adjustment conditions
Test oil
1404 Test oil ISO4113 or {SAEJ967d}
1404 Test oil ISO4113 or {SAEJ967d}
Test oil temperature
degC
40
40
45
Nozzle and nozzle holder
105780-8140
Bosch type code
EF8511/9A
Nozzle
105780-0000
Bosch type code
DN12SD12T
Nozzle holder
105780-2080
Bosch type code
EF8511/9
Opening pressure
MPa
17.2
Opening pressure
kgf/cm2
175
Injection pipe
Outer diameter - inner diameter - length (mm) mm 6-2-600
Outer diameter - inner diameter - length (mm) mm 6-2-600
Overflow valve
131424-5720
Overflow valve opening pressure
kPa
255
221
289
Overflow valve opening pressure
kgf/cm2
2.6
2.25
2.95
Tester oil delivery pressure
kPa
157
157
157
Tester oil delivery pressure
kgf/cm2
1.6
1.6
1.6
Direction of rotation (viewed from drive side)
Right R
Right R
Injection timing adjustment
Direction of rotation (viewed from drive side)
Right R
Right R
Injection order
1-4-2-6-
3-5
Pre-stroke
mm
3.1
3.05
3.15
Beginning of injection position
Drive side NO.1
Drive side NO.1
Difference between angles 1
Cal 1-4 deg. 60 59.5 60.5
Cal 1-4 deg. 60 59.5 60.5
Difference between angles 2
Cyl.1-2 deg. 120 119.5 120.5
Cyl.1-2 deg. 120 119.5 120.5
Difference between angles 3
Cal 1-6 deg. 180 179.5 180.5
Cal 1-6 deg. 180 179.5 180.5
Difference between angles 4
Cal 1-3 deg. 240 239.5 240.5
Cal 1-3 deg. 240 239.5 240.5
Difference between angles 5
Cal 1-5 deg. 300 299.5 300.5
Cal 1-5 deg. 300 299.5 300.5
Injection quantity adjustment
Adjusting point
A
Rack position
9.2
Pump speed
r/min
800
800
800
Average injection quantity
mm3/st.
40.6
39.1
42.1
Max. variation between cylinders
%
0
-3
3
Basic
*
Fixing the lever
*
Injection quantity adjustment_02
Adjusting point
B
Rack position
8.5
Pump speed
r/min
1100
1100
1100
Average injection quantity
mm3/st.
35
33.5
36.5
Fixing the rack
*
Injection quantity adjustment_03
Adjusting point
C
Rack position
8.5+-0.5
Pump speed
r/min
330
330
330
Average injection quantity
mm3/st.
11.6
10.1
13.1
Max. variation between cylinders
%
0
-15
15
Fixing the rack
*
Injection quantity adjustment_04
Adjusting point
D
Rack position
-
Pump speed
r/min
100
100
100
Average injection quantity
mm3/st.
95
95
105
Fixing the lever
*
Rack limit
*
Test data Ex:
Governor adjustment
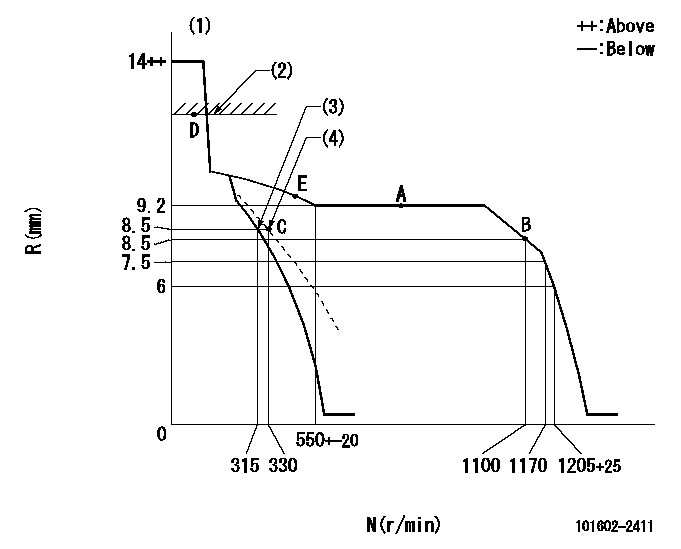
N:Pump speed
R:Rack position (mm)
(1)Target notch: K
(2)RACK LIMIT
(3)Main spring setting
(4)Set idle sub-spring
----------
K=9
----------
----------
K=9
----------
Speed control lever angle

F:Full speed
I:Idle
(1)Stopper bolt setting
----------
----------
a=(7deg)+-5deg b=(18deg)+-5deg
----------
----------
a=(7deg)+-5deg b=(18deg)+-5deg
Stop lever angle

N:Pump normal
S:Stop the pump.
----------
----------
a=27deg+-5deg b=53deg+-5deg
----------
----------
a=27deg+-5deg b=53deg+-5deg
Timing setting
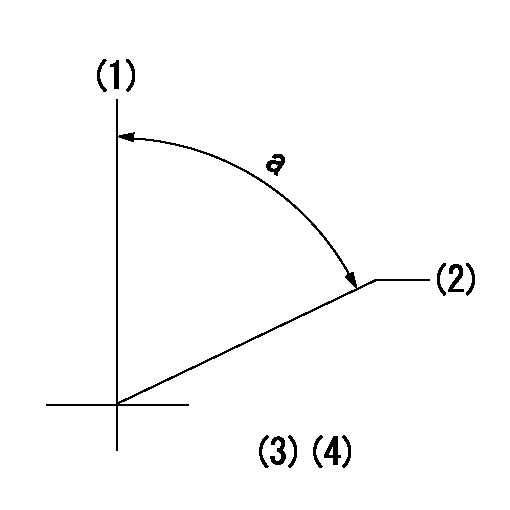
(1)Pump vertical direction
(2)Position of gear's standard threaded hole at No 1 cylinder's beginning of injection
(3)-
(4)-
----------
----------
a=(70deg)
----------
----------
a=(70deg)
Information:
Personal injury or death can result from machine articulation or movement. Machine frames can move and a person can be crushed. Connect the steering frame lock between the front and rear frames before working on the machine.Before operating the machine, place the steering frame lock in the stored position.Failure to place the steering frame lock into the stored position before operating can result in loss of steering.
Reference: Disassembly and Assembly, M0084637, "R1700 Load Haul Dump Machine Systems"Reference: Disassembly and Assembly, M0100022, "R2900 Load Haul Dump Machine Systems"Required Parts
Table 1
Required Parts
Qty Part Number Description
1 389-9442 Insulation
1 434-1304 Insulation
1 434-1305 Insulation
7 290-1993 Cable Strap Machine Preparation
Note: Cleanliness is an important factor. Before the removal procedure, clean the exterior of the component thoroughly. Cleaning the exterior will help to prevent dirt from entering the internal mechanism.
Move the machine to a hard level surface away from operating machines and away from personnel.
Engage the parking brake. Place wheel blocks in front of the wheels and behind the wheels.
Stop the engine.
Install the steering frame lock. Refer to Disassembly and Assembly, "Steering Frame Lock - Install".
Turn the key start switch and the battery disconnect switch to the OFF position. If there is no battery disconnect switch, remove the negative battery cable at the battery.
Release system pressure. Refer to Operation and Maintenance Manual, "System Pressure - Release".Procedure
Illustration 1 g06525155
Typical example
(1) Cover As
(2) Cover As
Remove cover assembly (1) and cover assembly (2).
Illustration 2 g06525163
Typical example
(3) Hose As
Locate DEF supply hose assembly (3).
Illustration 3 g06526653
DEF supply hose on the R1700 machine
(4) 290-1993 Cable Strap
(5) 389-9442 Insulation
(6) 434-1305 Insulation
(7) 434-1304 Insulation
Illustration 4 g06526655
DEF supply hose on the R2900 machine
(4) 290-1993 Cable Strap
(5) 389-9442 Insulation
(6) 434-1305 Insulation
(7) 434-1304 Insulation
Install Item (5) through Item (7), securing with 290-1993 Cable Straps as required.Note: On the R1700 machine, 434-1305 Insulation (6) is installed over the top of 389-9442 Insulation (5).Note: On the R2900 machine, 434-1305 Insulation (6) slightly overlaps 389-9442 Insulation (5).
Install cover assembly (1) and cover assembly (2). Refer to Illustration 1.
Have questions with 101602-2411?
Group cross 101602-2411 ZEXEL
Hino
Hino
101602-2411
9 400 614 771
220203361A
INJECTION-PUMP ASSEMBLY
W06D
W06D