Information injection-pump assembly
ZEXEL
101602-2370
1016022370
HINO
220203220A
220203220a
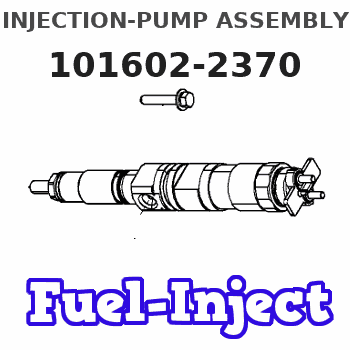
Rating:
Cross reference number
ZEXEL
101602-2370
1016022370
HINO
220203220A
220203220a
Zexel num
Bosch num
Firm num
Name
Calibration Data:
Adjustment conditions
Test oil
1404 Test oil ISO4113 or {SAEJ967d}
1404 Test oil ISO4113 or {SAEJ967d}
Test oil temperature
degC
40
40
45
Nozzle and nozzle holder
105780-8140
Bosch type code
EF8511/9A
Nozzle
105780-0000
Bosch type code
DN12SD12T
Nozzle holder
105780-2080
Bosch type code
EF8511/9
Opening pressure
MPa
17.2
Opening pressure
kgf/cm2
175
Injection pipe
Outer diameter - inner diameter - length (mm) mm 6-2-600
Outer diameter - inner diameter - length (mm) mm 6-2-600
Overflow valve
131424-5720
Overflow valve opening pressure
kPa
255
221
289
Overflow valve opening pressure
kgf/cm2
2.6
2.25
2.95
Tester oil delivery pressure
kPa
157
157
157
Tester oil delivery pressure
kgf/cm2
1.6
1.6
1.6
Direction of rotation (viewed from drive side)
Right R
Right R
Injection timing adjustment
Direction of rotation (viewed from drive side)
Right R
Right R
Injection order
1-4-2-6-
3-5
Pre-stroke
mm
3.1
3.05
3.15
Beginning of injection position
Drive side NO.1
Drive side NO.1
Difference between angles 1
Cal 1-4 deg. 60 59.5 60.5
Cal 1-4 deg. 60 59.5 60.5
Difference between angles 2
Cyl.1-2 deg. 120 119.5 120.5
Cyl.1-2 deg. 120 119.5 120.5
Difference between angles 3
Cal 1-6 deg. 180 179.5 180.5
Cal 1-6 deg. 180 179.5 180.5
Difference between angles 4
Cal 1-3 deg. 240 239.5 240.5
Cal 1-3 deg. 240 239.5 240.5
Difference between angles 5
Cal 1-5 deg. 300 299.5 300.5
Cal 1-5 deg. 300 299.5 300.5
Injection quantity adjustment
Adjusting point
A
Rack position
8.3
Pump speed
r/min
800
800
800
Average injection quantity
mm3/st.
32.2
31.2
33.2
Max. variation between cylinders
%
0
-3
3
Basic
*
Fixing the lever
*
Injection quantity adjustment_02
Adjusting point
C
Rack position
8.1+-0.5
Pump speed
r/min
325
325
325
Average injection quantity
mm3/st.
8.8
7.3
10.3
Max. variation between cylinders
%
0
-15
15
Fixing the rack
*
Injection quantity adjustment_03
Adjusting point
D
Rack position
-
Pump speed
r/min
100
100
100
Average injection quantity
mm3/st.
95
95
105
Fixing the lever
*
Rack limit
*
Test data Ex:
Governor adjustment
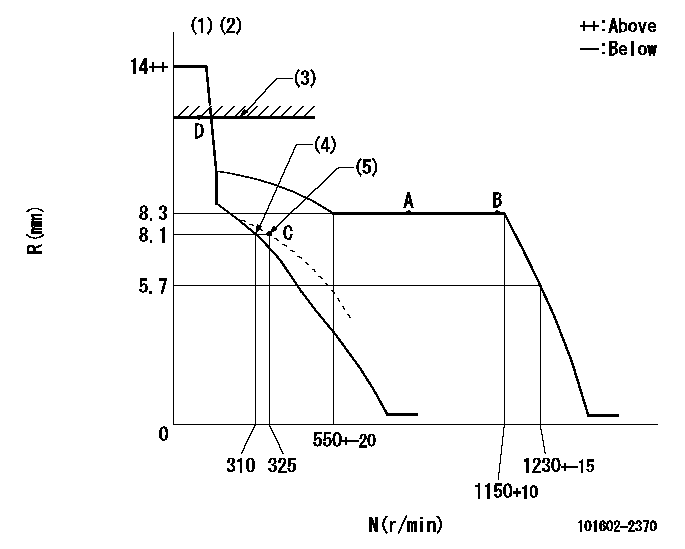
N:Pump speed
R:Rack position (mm)
(1)Target notch: K
(2)Torque spring does not operate.
(3)RACK LIMIT
(4)Main spring setting
(5)Set idle sub-spring
----------
K=9
----------
----------
K=9
----------
Speed control lever angle

F:Full speed
I:Idle
(1)Stopper bolt setting
----------
----------
a=7deg+-5deg b=20deg+-5deg
----------
----------
a=7deg+-5deg b=20deg+-5deg
Stop lever angle

N:Pump normal
S:Stop the pump.
----------
----------
a=27deg+-5deg b=53deg+-5deg
----------
----------
a=27deg+-5deg b=53deg+-5deg
Timing setting
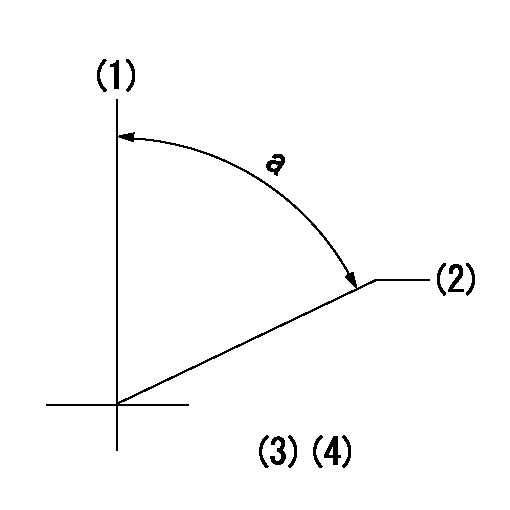
(1)Pump vertical direction
(2)Position of gear's standard threaded hole at No 1 cylinder's beginning of injection
(3)-
(4)-
----------
----------
a=(70deg)
----------
----------
a=(70deg)
Information:
Illustration 1 g01046024
Engine with two turbochargers (1) Inlet valves (2) Exhaust valves (3) Inlet manifold (4) Exhaust manifold (5) Water inlet for the aftercooler (6) Water outlet for the aftercooler (7) Aftercooler (8) Air inlet (9) Exhaust outlet (10) Compressor (11) TurbineThe components of the air inlet and exhaust system control the quality of air and the amount of air that is available for combustion. The components of the air inlet and exhaust system are the following components:
Air cleaner
Turbocharger
Aftercooler
Cylinder head
Valves and valve system components
Piston and cylinder
Inlet manifold
Exhaust manifoldNote: The following description of the operation of the air inlet and exhaust system assumes that the engine is developing boost pressure. Inlet air passes through the air cleaner into the air inlet (8) of the turbocharger compressor wheel (10). The turbocharger will supply more volume of air into the engine. This compressing of the air is referred to as boost. The compressing of air causes the air temperature to rise to about 204 °C (400 °F). As the air flows through the aftercooler (7) the temperature of the compressed air lowers to about 46 °C (115 °F). Cooling of the inlet air causes the air to become more dense. This increases combustion efficiency and this increases horsepower output.From the aftercooler, air enters the inlet manifold (3). Air flow from the inlet manifold (3) into the cylinders is controlled by inlet valves (1). There are two inlet valves and two exhaust valves (2) for each cylinder. The inlet valves open at the top center position before the piston moves toward the bottom center position. This is called the inlet stroke. When the inlet valves open, cooled compressed air from the inlet port enters the cylinder. The inlet valves close as the piston reaches the bottom center position. The piston begins to travel back to the top center position on the compression stroke. The air in the cylinder is compressed to a very high temperature. When the piston is near the end of the compression stroke, fuel is injected into the cylinder and mixes with the air. This causes combustion to start in the cylinder. Once combustion starts, the combustion force pushes the piston toward the bottom center position. This is called the power stroke. The exhaust valves open when the piston moves toward the bottom center position and the exhaust gases are pushed through the exhaust port into exhaust manifold (4) as the piston travels toward top center on the exhaust stroke. The exhaust valves close and the cycle starts again. The complete cycle consists of four strokes:
Inlet
Compression
Power
ExhaustExhaust gases from the exhaust manifold (4) enter the turbine side of the turbocharger. The exhaust gas temperature causes the turbine wheel (11) in the turbocharger to turn. The turbine wheel is connected to the shaft that drives the compressor wheel. Exhaust gases from the turbine wheel exit the turbocharger (9) .Turbocharger
Illustration 2 g01361124
Water cooled turbocharger (8) Air inlet (9) Exhaust outlet (11) Exhaust inlet (12) Compressor housing (13) Compressor wheel (14) Bearing (15) Oil Inlet