Information injection-pump assembly
ZEXEL
101602-2322
1016022322
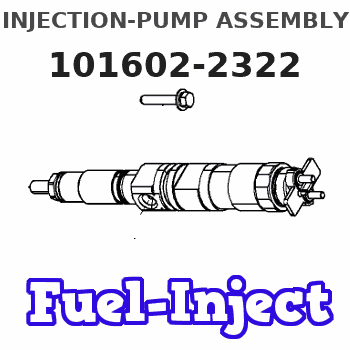
Rating:
Service parts 101602-2322 INJECTION-PUMP ASSEMBLY:
1.
_
5.
AUTOM. ADVANCE MECHANIS
7.
COUPLING PLATE
8.
_
9.
_
11.
Nozzle and Holder
23600-1830A
12.
Open Pre:MPa(Kqf/cm2)
19.6{200}
15.
NOZZLE SET
Cross reference number
ZEXEL
101602-2322
1016022322
Zexel num
Bosch num
Firm num
Name
101602-2322
INJECTION-PUMP ASSEMBLY
Calibration Data:
Adjustment conditions
Test oil
1404 Test oil ISO4113 or {SAEJ967d}
1404 Test oil ISO4113 or {SAEJ967d}
Test oil temperature
degC
40
40
45
Nozzle and nozzle holder
105780-8140
Bosch type code
EF8511/9A
Nozzle
105780-0000
Bosch type code
DN12SD12T
Nozzle holder
105780-2080
Bosch type code
EF8511/9
Opening pressure
MPa
17.2
Opening pressure
kgf/cm2
175
Injection pipe
Outer diameter - inner diameter - length (mm) mm 6-2-600
Outer diameter - inner diameter - length (mm) mm 6-2-600
Overflow valve
134424-0920
Overflow valve opening pressure
kPa
162
147
177
Overflow valve opening pressure
kgf/cm2
1.65
1.5
1.8
Tester oil delivery pressure
kPa
157
157
157
Tester oil delivery pressure
kgf/cm2
1.6
1.6
1.6
Direction of rotation (viewed from drive side)
Right R
Right R
Injection timing adjustment
Direction of rotation (viewed from drive side)
Right R
Right R
Injection order
1-4-2-6-
3-5
Pre-stroke
mm
4
3.95
4.05
Beginning of injection position
Drive side NO.1
Drive side NO.1
Difference between angles 1
Cal 1-4 deg. 60 59.5 60.5
Cal 1-4 deg. 60 59.5 60.5
Difference between angles 2
Cyl.1-2 deg. 120 119.5 120.5
Cyl.1-2 deg. 120 119.5 120.5
Difference between angles 3
Cal 1-6 deg. 180 179.5 180.5
Cal 1-6 deg. 180 179.5 180.5
Difference between angles 4
Cal 1-3 deg. 240 239.5 240.5
Cal 1-3 deg. 240 239.5 240.5
Difference between angles 5
Cal 1-5 deg. 300 299.5 300.5
Cal 1-5 deg. 300 299.5 300.5
Injection quantity adjustment
Adjusting point
A
Rack position
9.3
Pump speed
r/min
1000
1000
1000
Average injection quantity
mm3/st.
86.5
85.5
87.5
Max. variation between cylinders
%
0
-3.5
3.5
Basic
*
Fixing the lever
*
Injection quantity adjustment_02
Adjusting point
-
Rack position
6+-0.5
Pump speed
r/min
410
410
410
Average injection quantity
mm3/st.
10
9
11
Max. variation between cylinders
%
0
-10
10
Fixing the rack
*
Remarks
Adjust only variation between cylinders; adjust governor according to governor specifications.
Adjust only variation between cylinders; adjust governor according to governor specifications.
Injection quantity adjustment_03
Adjusting point
C
Rack position
-
Pump speed
r/min
100
100
100
Average injection quantity
mm3/st.
130
130
140
Fixing the lever
*
Rack limit
*
Test data Ex:
Governor adjustment
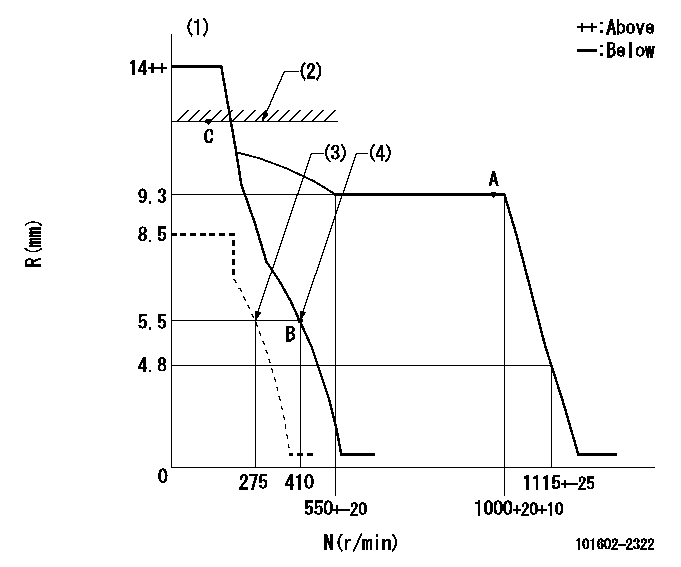
N:Pump speed
R:Rack position (mm)
(1)Target notch: K
(2)RACK LIMIT
(3)Set idle sub-spring
(4)Main spring setting
----------
K=6
----------
----------
K=6
----------
Speed control lever angle
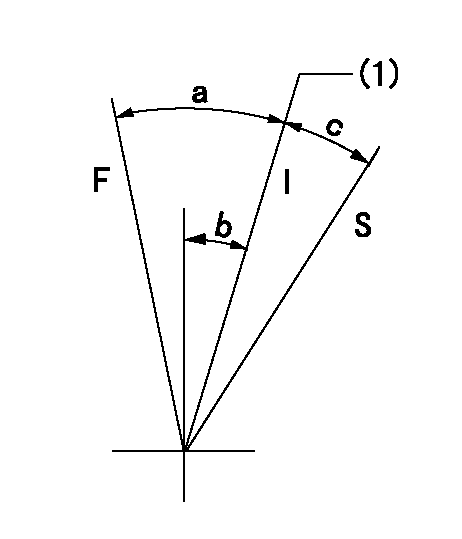
F:Full speed
I:Idle
S:Stop
(1)Set the stopper bolt at delivery
----------
----------
a=(16deg)+-5deg b=(16deg)+-5deg c=(16deg)+-5deg
----------
----------
a=(16deg)+-5deg b=(16deg)+-5deg c=(16deg)+-5deg
Stop lever angle

N:Pump normal
S:Stop the pump.
(1)Normal
(2)Rack position aa or less, pump speed bb
----------
aa=5mm bb=0r/min
----------
a=27deg+-5deg b=53deg+-5deg
----------
aa=5mm bb=0r/min
----------
a=27deg+-5deg b=53deg+-5deg
Timing setting
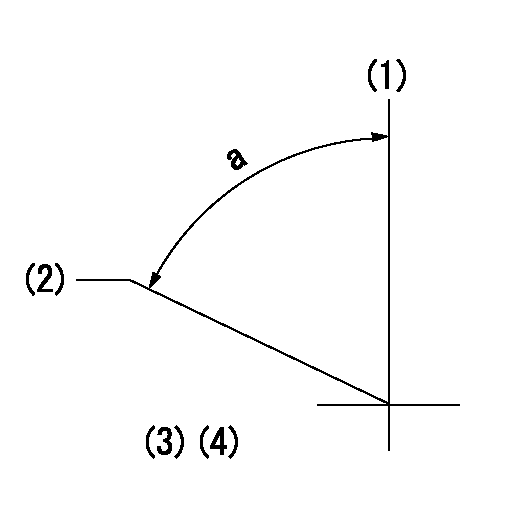
(1)Pump vertical direction
(2)Coupling's key groove position at No 1 cylinder's beginning of injection
(3)-
(4)-
----------
----------
a=(60deg)
----------
----------
a=(60deg)
Information:
In the New Systems, Refilled Systems, and converted systemsEvery year: add to it hours: ever year or every 2000 hours, whichever comes first.When referring to the Service Life in table 1, use the interval that occurs first. These coolant change intervals are only achievable with annual S O S Services Level 2 coolant sampling analysis.Refer to the engine Operation and Maintenance Manual for the correct interval for replacement of the cooling system water temperature regulator.Note: For engines that require a maximum of 20% glycol, make sure that the amount of additive in the final mix is appropriate. Example of mixing a 20% glycol solution is given in Table 3.
Table 3
Example of Mixing Up a 20% Glycol Coolant (1)
Total Volume of the Cooling System Add the Following:
ELC Concentrate ELI Concentrate Water
10 Gallons 2 Gallons 0.5 Gallons 7.5 Gallons
(1) Volumes can also be in liters as long as all the volume units are consistentExtended life coolants require the one time maintenance addition of an extender at coolant service mid-life. For commercial coolants, do NOT use an extender with a coolant unless the extender has been approved by the coolant manufacturer for use with the coolant. The coolant manufacturer is responsible to ensure compatibility and acceptable performance. Failure to follow these recommendations can result in shortened cooling system component life.Conventional coolants require the maintenance addition of SCA throughout the expected life. For commercial coolants, do NOT use an SCA unless approved by the coolant supplier for use with the coolant. The coolant manufacturer is responsible to ensure compatibility and acceptable performance."ASTM D6210" require coolants that are properly dosed with SCA and that are in a properly maintained cooling system in normal service to be suitable for use for a maximum of 2 years. The suitability for use requirement is the direct responsibility of the coolant manufacturer and SCA manufacturer. Consult with the coolant and/or SCA manufacturer concerning the suitability of the products for use in a given application.Cat DEAC is fully formulated and does not require a treatment with an SCA at the initial fill.A commercial heavy-duty coolant/antifreeze that meets the "ASTM D6210"specification does not require a treatment with an SCA at the initial fill.Commercial Heavy Duty coolants that meet only "ASTM D4985" specification are not recommended for Caterpillar applications. These coolants may not provide the performance characteristics needed for heavy duty applications. Cat coolants and the coolants detailed in Table 1 and in this Chapter are formulated to offer the required performance in Cat engines. Refer to Table 1 for Cat coolants recommendations.Cat ELC, Cat ELI, Cat DEAC, Cat Extender, and Cat SCA are available in several container sizes. The availability of part numbers will vary by the region. Consult your Cat dealer.In stationary and marine engine applications that do not require protection from boiling or freezing, except as noted in Table 2, Cat ELI in water or SCA and water are acceptable.
Table 3
Example of Mixing Up a 20% Glycol Coolant (1)
Total Volume of the Cooling System Add the Following:
ELC Concentrate ELI Concentrate Water
10 Gallons 2 Gallons 0.5 Gallons 7.5 Gallons
(1) Volumes can also be in liters as long as all the volume units are consistentExtended life coolants require the one time maintenance addition of an extender at coolant service mid-life. For commercial coolants, do NOT use an extender with a coolant unless the extender has been approved by the coolant manufacturer for use with the coolant. The coolant manufacturer is responsible to ensure compatibility and acceptable performance. Failure to follow these recommendations can result in shortened cooling system component life.Conventional coolants require the maintenance addition of SCA throughout the expected life. For commercial coolants, do NOT use an SCA unless approved by the coolant supplier for use with the coolant. The coolant manufacturer is responsible to ensure compatibility and acceptable performance."ASTM D6210" require coolants that are properly dosed with SCA and that are in a properly maintained cooling system in normal service to be suitable for use for a maximum of 2 years. The suitability for use requirement is the direct responsibility of the coolant manufacturer and SCA manufacturer. Consult with the coolant and/or SCA manufacturer concerning the suitability of the products for use in a given application.Cat DEAC is fully formulated and does not require a treatment with an SCA at the initial fill.A commercial heavy-duty coolant/antifreeze that meets the "ASTM D6210"specification does not require a treatment with an SCA at the initial fill.Commercial Heavy Duty coolants that meet only "ASTM D4985" specification are not recommended for Caterpillar applications. These coolants may not provide the performance characteristics needed for heavy duty applications. Cat coolants and the coolants detailed in Table 1 and in this Chapter are formulated to offer the required performance in Cat engines. Refer to Table 1 for Cat coolants recommendations.Cat ELC, Cat ELI, Cat DEAC, Cat Extender, and Cat SCA are available in several container sizes. The availability of part numbers will vary by the region. Consult your Cat dealer.In stationary and marine engine applications that do not require protection from boiling or freezing, except as noted in Table 2, Cat ELI in water or SCA and water are acceptable.
Have questions with 101602-2322?
Group cross 101602-2322 ZEXEL
Hino
101602-2322
INJECTION-PUMP ASSEMBLY