Information injection-pump assembly
ZEXEL
101602-2290
1016022290
HINO
220203000A
220203000a
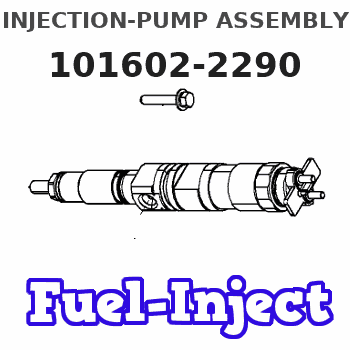
Rating:
Cross reference number
ZEXEL
101602-2290
1016022290
HINO
220203000A
220203000a
Zexel num
Bosch num
Firm num
Name
Calibration Data:
Adjustment conditions
Test oil
1404 Test oil ISO4113 or {SAEJ967d}
1404 Test oil ISO4113 or {SAEJ967d}
Test oil temperature
degC
40
40
45
Nozzle and nozzle holder
105780-8140
Bosch type code
EF8511/9A
Nozzle
105780-0000
Bosch type code
DN12SD12T
Nozzle holder
105780-2080
Bosch type code
EF8511/9
Opening pressure
MPa
17.2
Opening pressure
kgf/cm2
175
Injection pipe
Outer diameter - inner diameter - length (mm) mm 6-2-600
Outer diameter - inner diameter - length (mm) mm 6-2-600
Overflow valve
134424-0920
Overflow valve opening pressure
kPa
162
147
177
Overflow valve opening pressure
kgf/cm2
1.65
1.5
1.8
Tester oil delivery pressure
kPa
157
157
157
Tester oil delivery pressure
kgf/cm2
1.6
1.6
1.6
Direction of rotation (viewed from drive side)
Right R
Right R
Injection timing adjustment
Direction of rotation (viewed from drive side)
Right R
Right R
Injection order
1-4-2-6-
3-5
Pre-stroke
mm
4.8
4.77
4.83
Beginning of injection position
Drive side NO.1
Drive side NO.1
Difference between angles 1
Cal 1-4 deg. 60 59.75 60.25
Cal 1-4 deg. 60 59.75 60.25
Difference between angles 2
Cyl.1-2 deg. 120 119.75 120.25
Cyl.1-2 deg. 120 119.75 120.25
Difference between angles 3
Cal 1-6 deg. 180 179.75 180.25
Cal 1-6 deg. 180 179.75 180.25
Difference between angles 4
Cal 1-3 deg. 240 239.75 240.25
Cal 1-3 deg. 240 239.75 240.25
Difference between angles 5
Cal 1-5 deg. 300 299.75 300.25
Cal 1-5 deg. 300 299.75 300.25
Injection quantity adjustment
Adjusting point
A
Rack position
9.1
Pump speed
r/min
1050
1050
1050
Average injection quantity
mm3/st.
99.2
98.2
100.2
Max. variation between cylinders
%
0
-3.5
3.5
Basic
*
Fixing the lever
*
Injection quantity adjustment_02
Adjusting point
-
Rack position
5.6+-0.5
Pump speed
r/min
410
410
410
Average injection quantity
mm3/st.
10
9
11
Max. variation between cylinders
%
0
-10
10
Fixing the rack
*
Remarks
Adjust only variation between cylinders; adjust governor according to governor specifications.
Adjust only variation between cylinders; adjust governor according to governor specifications.
Injection quantity adjustment_03
Adjusting point
C
Rack position
-
Pump speed
r/min
100
100
100
Average injection quantity
mm3/st.
133
133
143
Fixing the lever
*
Rack limit
*
Test data Ex:
Governor adjustment
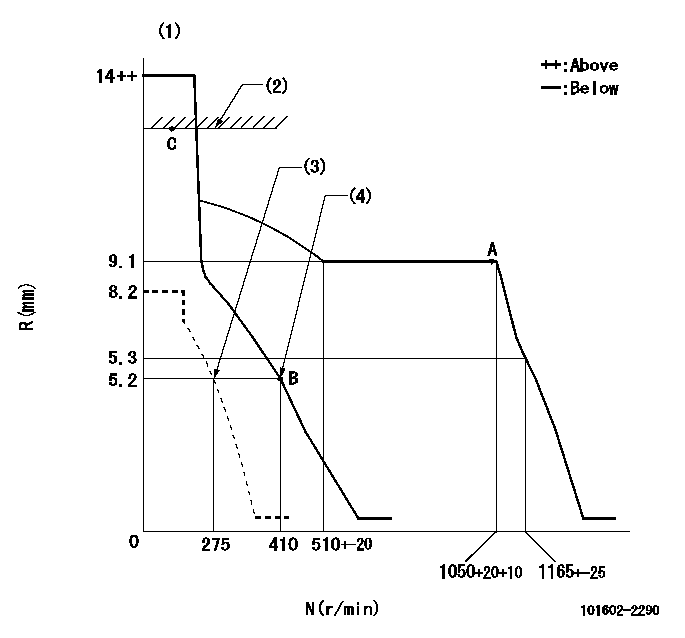
N:Pump speed
R:Rack position (mm)
(1)Target notch: K
(2)RACK LIMIT
(3)Set idle sub-spring
(4)Main spring setting
----------
K=10
----------
----------
K=10
----------
Speed control lever angle
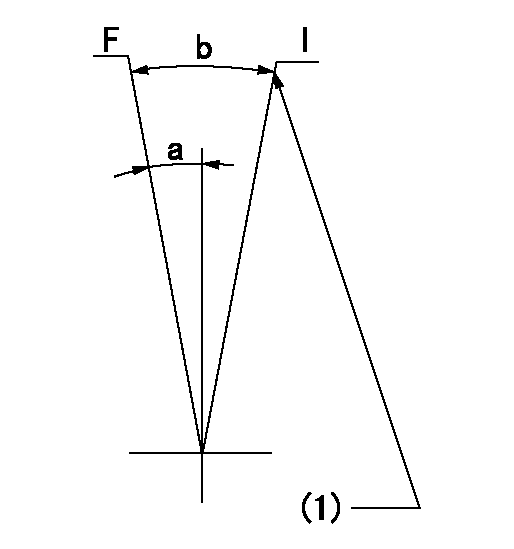
F:Full speed
I:Idle
(1)Stopper bolt setting
----------
----------
a=6deg+-5deg b=18deg+-5deg
----------
----------
a=6deg+-5deg b=18deg+-5deg
Stop lever angle

N:Pump normal
S:Stop the pump.
----------
----------
a=27deg+-5deg b=53deg+-5deg
----------
----------
a=27deg+-5deg b=53deg+-5deg
Timing setting
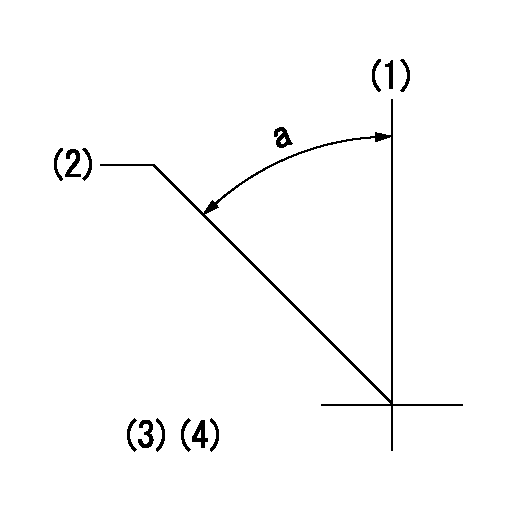
(1)Pump vertical direction
(2)Coupling's key groove position at No 1 cylinder's beginning of injection
(3)-
(4)-
----------
----------
a=(50deg)
----------
----------
a=(50deg)
Information:
Illustration 2 g01681836
(3) CGI flex pipe
Inspect the CGI flex pipe that is installed on all Kenworth and Peterbilt chassis. Check for a previous update to the CGI flex pipe under either a Peterbilt or Kenworth Technical Information BulletinThis work should be charged to your local OEM dealer with instructions that are provided with the service letter.
Peterbilt -Field Repair Notice 408-1 or newer Clean Gas Induction (CGI) and Main Exhaust Pipe Couplings
Kenworth – Technical Information Bulletin Number 43-12 or newer
Drain and save the coolant. The saved coolant can then be reused. Draining the coolant is necessary in order to replace the ARD combustion head.
Illustration 3 g01678253
(4) CGI coolant hose and clamps that are replaced on S/N:SDP1-17026
Inspect the CGI coolant hose and clamps and replace the CGI coolant hose and clamps if it is necessary on S/N:SDP1-17026.
Only replace the hose if the hose has not already been updated. Only black colored hoses should be replaced. The replacement hose is blue or green in color. The blue or green hose does not need to be replaced.Note: There will be some coolant that is left in the line after draining.
Illustration 4 g01678273
(5) Location of fuel control valves
Replace the Pilot and Main Fuel Control Valves. The fuel control valve must not be overtorqued.Torque for the two solenoid valve groups ... 50 5 N m (37 4 lb ft)Final installation torque for the two solenoid nuts ... 20 3 N m (15 2 lb ft)
Replace the ARD combustion head and the components of the ARD utilizing the Disassembly and Assembly Manual, RENR9706 for the proper procedure.Note: Do not install the fuel lines to the ARD Combustion head at this time. These lines will be installed after flushing the fuel system. Leave the protective shipping caps in the fuel ports of the ARD combustion head.
Illustration 5 g01681795
(8) ARD flame detection temperature sensor
In addition to the replacement of the ARD combustion head, install a new ARD flame detection temperature sensor. Refer to Special Instruction, REHS3794 for proper wire routing. If a stainless steel zip tie is removed a newstainless steel zip tie should be used.
Illustration 6 g01681813
(9) CGI temperature sensor
Replace the CGI temperature sensor. Refer to the Disassembly and Assembly Manual, RENR9706 and Disassembly and Assembly Manual, RENR9705 for the proper procedures. Proper wire routing should be followed. If a stainless steel zip tie is removed a new stainless steel zip tie should be used.
Refill the cooling system with the coolant that was saved in Step 8.
Flush the ARD fuel system. Refer to Special Instruction, REHS3848 for the correct procedure.
Flash the engine with the latest software. The release date of the software must be November 2008 or a newer date.Tables that are used in order to look up software and the process for obtaining the software are provided below.
Perform a verification test of the air system and save the file.Note: Refer to Troubleshooting Guide, RENR9343, "Air System Verification Test" that is located on the Service Information System for the pass or fail criteria.
Perform a stationary regeneration. Check