Information injection-pump assembly
ZEXEL
101602-1501
1016021501
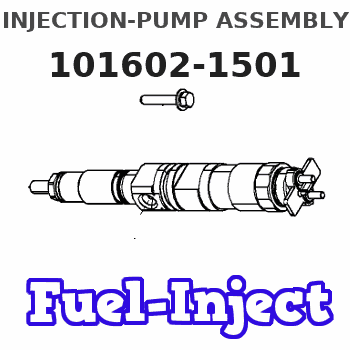
Rating:
Service parts 101602-1501 INJECTION-PUMP ASSEMBLY:
1.
_
5.
AUTOM. ADVANCE MECHANIS
6.
COUPLING PLATE
8.
_
9.
_
11.
Nozzle and Holder
ME016655
12.
Open Pre:MPa(Kqf/cm2)
21.6{220}
15.
NOZZLE SET
Include in #1:
101602-1501
as INJECTION-PUMP ASSEMBLY
Include in #2:
104057-3280
as _
Cross reference number
ZEXEL
101602-1501
1016021501
Zexel num
Bosch num
Firm num
Name
101602-1501
INJECTION-PUMP ASSEMBLY
14BE PE6A PE
14BE PE6A PE
Calibration Data:
Adjustment conditions
Test oil
1404 Test oil ISO4113 or {SAEJ967d}
1404 Test oil ISO4113 or {SAEJ967d}
Test oil temperature
degC
40
40
45
Nozzle and nozzle holder
105780-8140
Bosch type code
EF8511/9A
Nozzle
105780-0000
Bosch type code
DN12SD12T
Nozzle holder
105780-2080
Bosch type code
EF8511/9
Opening pressure
MPa
17.2
Opening pressure
kgf/cm2
175
Injection pipe
Outer diameter - inner diameter - length (mm) mm 6-2-600
Outer diameter - inner diameter - length (mm) mm 6-2-600
Overflow valve
131424-5520
Overflow valve opening pressure
kPa
255
221
289
Overflow valve opening pressure
kgf/cm2
2.6
2.25
2.95
Tester oil delivery pressure
kPa
157
157
157
Tester oil delivery pressure
kgf/cm2
1.6
1.6
1.6
Direction of rotation (viewed from drive side)
Right R
Right R
Injection timing adjustment
Direction of rotation (viewed from drive side)
Right R
Right R
Injection order
1-5-3-6-
2-4
Pre-stroke
mm
3.5
3.45
3.55
Beginning of injection position
Drive side NO.1
Drive side NO.1
Difference between angles 1
Cal 1-5 deg. 60 59.5 60.5
Cal 1-5 deg. 60 59.5 60.5
Difference between angles 2
Cal 1-3 deg. 120 119.5 120.5
Cal 1-3 deg. 120 119.5 120.5
Difference between angles 3
Cal 1-6 deg. 180 179.5 180.5
Cal 1-6 deg. 180 179.5 180.5
Difference between angles 4
Cyl.1-2 deg. 240 239.5 240.5
Cyl.1-2 deg. 240 239.5 240.5
Difference between angles 5
Cal 1-4 deg. 300 299.5 300.5
Cal 1-4 deg. 300 299.5 300.5
Injection quantity adjustment
Adjusting point
A
Rack position
9.7
Pump speed
r/min
850
850
850
Average injection quantity
mm3/st.
68
67
69
Max. variation between cylinders
%
0
-2.5
2.5
Basic
*
Fixing the lever
*
Injection quantity adjustment_02
Adjusting point
-
Rack position
7.8+-0.5
Pump speed
r/min
440
440
440
Average injection quantity
mm3/st.
7.5
6.2
8.8
Max. variation between cylinders
%
0
-14
14
Fixing the rack
*
Remarks
Adjust only variation between cylinders; adjust governor according to governor specifications.
Adjust only variation between cylinders; adjust governor according to governor specifications.
Injection quantity adjustment_03
Adjusting point
D
Rack position
-
Pump speed
r/min
100
100
100
Average injection quantity
mm3/st.
65
65
70
Fixing the lever
*
Rack limit
*
Test data Ex:
Governor adjustment
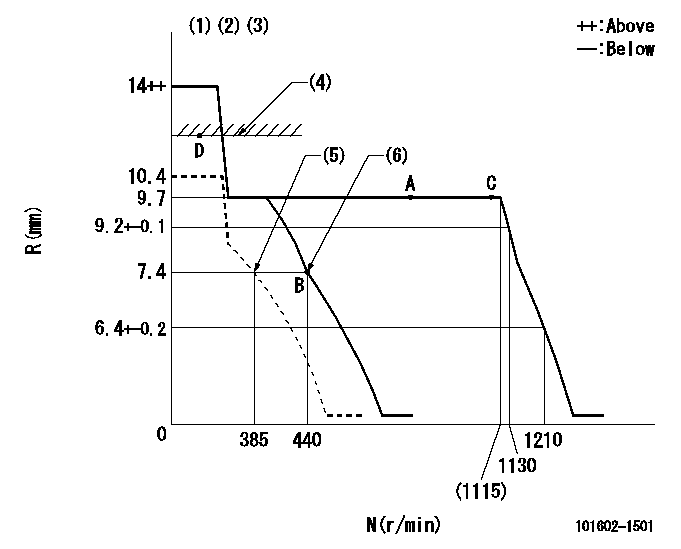
N:Pump speed
R:Rack position (mm)
(1)Target notch: K
(2)Tolerance for racks not indicated: +-0.05mm.
(3)Supplied with torque spring not set.
(4)RACK LIMIT
(5)Set idle sub-spring
(6)Main spring setting
----------
K=12
----------
----------
K=12
----------
Speed control lever angle
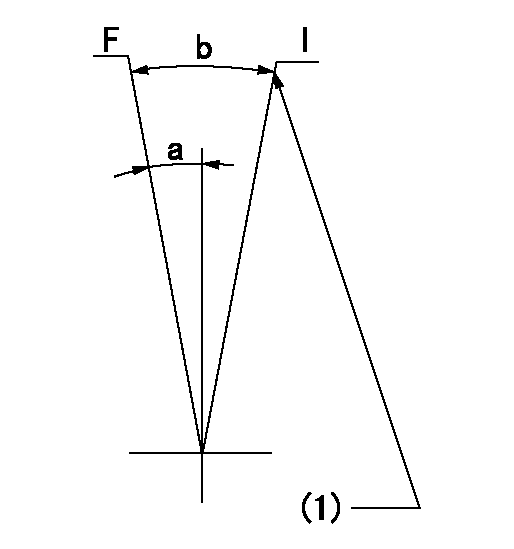
F:Full speed
I:Idle
(1)Stopper bolt setting
----------
----------
a=9deg+-5deg b=24deg+-5deg
----------
----------
a=9deg+-5deg b=24deg+-5deg
Stop lever angle

N:Pump normal
S:Stop the pump.
----------
----------
a=26.5deg+-5deg b=53deg+-5deg
----------
----------
a=26.5deg+-5deg b=53deg+-5deg
Timing setting

(1)Pump vertical direction
(2)Position of gear mark '3' at No 1 cylinder's beginning of injection
(3)B.T.D.C.: aa
(4)-
----------
aa=12.5deg
----------
a=(130deg)
----------
aa=12.5deg
----------
a=(130deg)
Information:
Rework Procedure
This procedure is only required when utilizing the 444-2472 Bracket As or 444-2473 Bracket As, the former 222-6953 Valve Cover Bases, and the new stamped steel valve covers. Disregard if using 442-5727 Valve Cover Base.The preferred method to correct this issue is to remove the former 222-6953 Valve Cover Base and install the current 442-5727 Valve Cover Base. This valve cover base removes the need for the 444-2472 Bracket As and 444-2473 Bracket As.The alternative method is to modify the 444-2472 Bracket As or 444-2473 Bracket As to be used with the 222-6953 Valve Mechanism Cover Base and stamped steel valve cover.Note:
Illustration 1 g06088172
Bracket assemblies view
(1) 444-2472 Bracket As
(2) 444-2473 Bracket As
Illustration 2 g06088191
Side view of the bracket.
(3) Button portion
(4) Weld stud
Illustration 3 g06088192
Top view of the bracket.
The illustration above shows the location of the material that will need to be removed from the button of the bracket assemblies.
Illustration 4 g06088194
Side view of the bracket.
Illustration 5 g06088195
View of the bracket after modification.
Remove 4 mm (0.16 in) from the button on the bracket as shown in Illustration 4.
Once the additional material has been removed from the modified bracket, fit the valve cover to ensure that proper clearance has been created allowing sealing of valve cover PIP seal. Install and torque the valve cover using the appropriate procedure from the Disassembly and Assembly manual.
Illustration 6 g06088196
Impression made by bracket assemblies that contact the valve cover.
Remove the valve cover and inspect the mating surface to see if any contact marks are present as shown in Illustration 6. If contact marks are present, extra material of the button will need to be removed for clearance.
This procedure is only required when utilizing the 444-2472 Bracket As or 444-2473 Bracket As, the former 222-6953 Valve Cover Bases, and the new stamped steel valve covers. Disregard if using 442-5727 Valve Cover Base.The preferred method to correct this issue is to remove the former 222-6953 Valve Cover Base and install the current 442-5727 Valve Cover Base. This valve cover base removes the need for the 444-2472 Bracket As and 444-2473 Bracket As.The alternative method is to modify the 444-2472 Bracket As or 444-2473 Bracket As to be used with the 222-6953 Valve Mechanism Cover Base and stamped steel valve cover.Note:
Illustration 1 g06088172
Bracket assemblies view
(1) 444-2472 Bracket As
(2) 444-2473 Bracket As
Illustration 2 g06088191
Side view of the bracket.
(3) Button portion
(4) Weld stud
Illustration 3 g06088192
Top view of the bracket.
The illustration above shows the location of the material that will need to be removed from the button of the bracket assemblies.
Illustration 4 g06088194
Side view of the bracket.
Illustration 5 g06088195
View of the bracket after modification.
Remove 4 mm (0.16 in) from the button on the bracket as shown in Illustration 4.
Once the additional material has been removed from the modified bracket, fit the valve cover to ensure that proper clearance has been created allowing sealing of valve cover PIP seal. Install and torque the valve cover using the appropriate procedure from the Disassembly and Assembly manual.
Illustration 6 g06088196
Impression made by bracket assemblies that contact the valve cover.
Remove the valve cover and inspect the mating surface to see if any contact marks are present as shown in Illustration 6. If contact marks are present, extra material of the button will need to be removed for clearance.
Have questions with 101602-1501?
Group cross 101602-1501 ZEXEL
101602-1501
INJECTION-PUMP ASSEMBLY