Information injection-pump assembly
BOSCH
9 400 614 738
9400614738
ZEXEL
101602-1434
1016021434
MITSUBISHI
ME088910
me088910
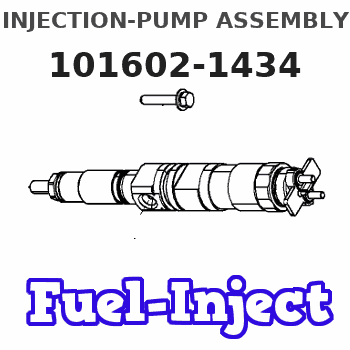
Rating:
Service parts 101602-1434 INJECTION-PUMP ASSEMBLY:
1.
_
5.
AUTOM. ADVANCE MECHANIS
6.
COUPLING PLATE
8.
_
9.
_
11.
Nozzle and Holder
12.
Open Pre:MPa(Kqf/cm2)
21.6(220)
15.
NOZZLE SET
Include in #1:
101602-1434
as INJECTION-PUMP ASSEMBLY
Include in #2:
105856-5230
as _
Cross reference number
BOSCH
9 400 614 738
9400614738
ZEXEL
101602-1434
1016021434
MITSUBISHI
ME088910
me088910
Zexel num
Bosch num
Firm num
Name
101602-1434
9 400 614 738
ME088910 MITSUBISHI
INJECTION-PUMP ASSEMBLY
6D34T K 14BF INJECTION PUMP ASSY PE6AD PE
6D34T K 14BF INJECTION PUMP ASSY PE6AD PE
Calibration Data:
Adjustment conditions
Test oil
1404 Test oil ISO4113 or {SAEJ967d}
1404 Test oil ISO4113 or {SAEJ967d}
Test oil temperature
degC
40
40
45
Nozzle and nozzle holder
105780-8140
Bosch type code
EF8511/9A
Nozzle
105780-0000
Bosch type code
DN12SD12T
Nozzle holder
105780-2080
Bosch type code
EF8511/9
Opening pressure
MPa
17.2
Opening pressure
kgf/cm2
175
Injection pipe
Outer diameter - inner diameter - length (mm) mm 6-2-600
Outer diameter - inner diameter - length (mm) mm 6-2-600
Overflow valve
131424-5520
Overflow valve opening pressure
kPa
255
221
289
Overflow valve opening pressure
kgf/cm2
2.6
2.25
2.95
Tester oil delivery pressure
kPa
157
157
157
Tester oil delivery pressure
kgf/cm2
1.6
1.6
1.6
Direction of rotation (viewed from drive side)
Right R
Right R
Injection timing adjustment
Direction of rotation (viewed from drive side)
Right R
Right R
Injection order
1-5-3-6-
2-4
Pre-stroke
mm
3.5
3.45
3.55
Beginning of injection position
Drive side NO.1
Drive side NO.1
Difference between angles 1
Cal 1-5 deg. 60 59.5 60.5
Cal 1-5 deg. 60 59.5 60.5
Difference between angles 2
Cal 1-3 deg. 120 119.5 120.5
Cal 1-3 deg. 120 119.5 120.5
Difference between angles 3
Cal 1-6 deg. 180 179.5 180.5
Cal 1-6 deg. 180 179.5 180.5
Difference between angles 4
Cyl.1-2 deg. 240 239.5 240.5
Cyl.1-2 deg. 240 239.5 240.5
Difference between angles 5
Cal 1-4 deg. 300 299.5 300.5
Cal 1-4 deg. 300 299.5 300.5
Injection quantity adjustment
Adjusting point
A
Rack position
9.8
Pump speed
r/min
850
850
850
Average injection quantity
mm3/st.
71.5
70.5
72.5
Max. variation between cylinders
%
0
-2.5
2.5
Basic
*
Fixing the lever
*
Injection quantity adjustment_02
Adjusting point
-
Rack position
7.4+-0.5
Pump speed
r/min
450
450
450
Average injection quantity
mm3/st.
8
6.7
9.3
Max. variation between cylinders
%
0
-14
14
Fixing the rack
*
Remarks
Adjust only variation between cylinders; adjust governor according to governor specifications.
Adjust only variation between cylinders; adjust governor according to governor specifications.
Injection quantity adjustment_03
Adjusting point
D
Rack position
10++
Pump speed
r/min
100
100
100
Average injection quantity
mm3/st.
65
65
70
Fixing the lever
*
Rack limit
*
Test data Ex:
Governor adjustment
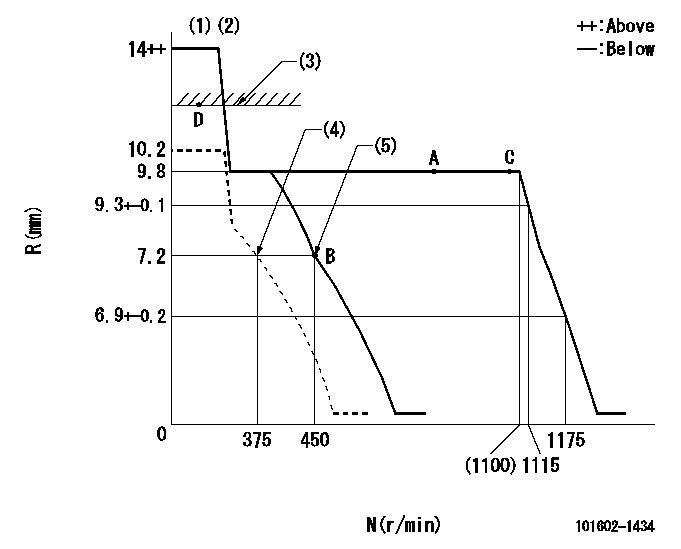
N:Pump speed
R:Rack position (mm)
(1)Target notch: K
(2)Tolerance for racks not indicated: +-0.05mm.
(3)RACK LIMIT
(4)Set idle sub-spring
(5)Main spring setting
----------
K=11
----------
----------
K=11
----------
Speed control lever angle
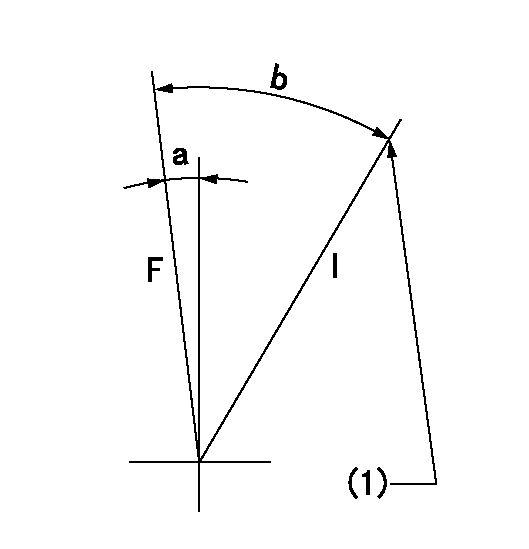
F:Full speed
I:Idle
(1)Stopper bolt setting
----------
----------
a=6deg+-5deg b=22deg+-5deg
----------
----------
a=6deg+-5deg b=22deg+-5deg
Stop lever angle

N:Pump normal
S:Stop the pump.
(1)Normal
----------
----------
a=26.5deg+-5deg b=53deg+-5deg
----------
----------
a=26.5deg+-5deg b=53deg+-5deg
Timing setting

(1)Pump vertical direction
(2)Position of gear mark '3' at No 1 cylinder's beginning of injection
(3)B.T.D.C.: aa
(4)-
----------
aa=12.5deg
----------
a=(130deg)
----------
aa=12.5deg
----------
a=(130deg)
Information:
Introduction
This Special Instruction contains the strap torquing procedure for the straps on the DEF tank.Read the entire Special Instruction. Understand the information before you perform any procedures. Strap Torquing Procedure
Illustration 1 g03354750
(1) Strap (2) Nut
Install strap (1) and torque nut (2) .Torque for nut (2) ... 11 1 N m (97 9 lb in)Note: If the strap has a hook or other non-adjustable fastener on one end, only the adjustment end is torqued during installation.Note: If both ends of the strap have adjustable fasteners, both ends should be torqued only once. Do not go back and forth when applying assembly torque. Torque the first side to specification, then ensure that the torque on the second side is at specifications. Do not go back and retorque the first side.
This Special Instruction contains the strap torquing procedure for the straps on the DEF tank.Read the entire Special Instruction. Understand the information before you perform any procedures. Strap Torquing Procedure
Illustration 1 g03354750
(1) Strap (2) Nut
Install strap (1) and torque nut (2) .Torque for nut (2) ... 11 1 N m (97 9 lb in)Note: If the strap has a hook or other non-adjustable fastener on one end, only the adjustment end is torqued during installation.Note: If both ends of the strap have adjustable fasteners, both ends should be torqued only once. Do not go back and forth when applying assembly torque. Torque the first side to specification, then ensure that the torque on the second side is at specifications. Do not go back and retorque the first side.
Have questions with 101602-1434?
Group cross 101602-1434 ZEXEL
Mitsubishi
101602-1434
9 400 614 738
ME088910
INJECTION-PUMP ASSEMBLY
6D34T
6D34T