Information injection-pump assembly
BOSCH
F 019 Z10 823
f019z10823
ZEXEL
101602-1320
1016021320
MITSUBISHI
ME157337
me157337
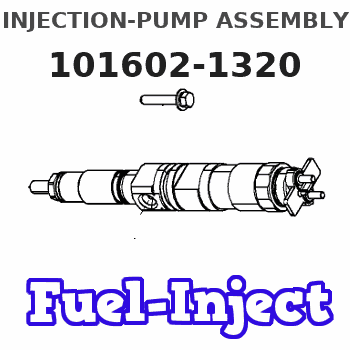
Rating:
Service parts 101602-1320 INJECTION-PUMP ASSEMBLY:
1.
_
5.
AUTOM. ADVANCE MECHANIS
7.
COUPLING PLATE
8.
_
9.
_
11.
Nozzle and Holder
12.
Open Pre:MPa(Kqf/cm2)
21.6(220)
15.
NOZZLE SET
Cross reference number
BOSCH
F 019 Z10 823
f019z10823
ZEXEL
101602-1320
1016021320
MITSUBISHI
ME157337
me157337
Zexel num
Bosch num
Firm num
Name
101602-1320
F 019 Z10 823
ME157337 MITSUBISHI
INJECTION-PUMP ASSEMBLY
6D22 * K
6D22 * K
Calibration Data:
Adjustment conditions
Test oil
1404 Test oil ISO4113 or {SAEJ967d}
1404 Test oil ISO4113 or {SAEJ967d}
Test oil temperature
degC
40
40
45
Nozzle and nozzle holder
105780-8140
Bosch type code
EF8511/9A
Nozzle
105780-0000
Bosch type code
DN12SD12T
Nozzle holder
105780-2080
Bosch type code
EF8511/9
Opening pressure
MPa
17.2
Opening pressure
kgf/cm2
175
Injection pipe
Outer diameter - inner diameter - length (mm) mm 6-2-600
Outer diameter - inner diameter - length (mm) mm 6-2-600
Overflow valve
131424-4620
Overflow valve opening pressure
kPa
255
221
289
Overflow valve opening pressure
kgf/cm2
2.6
2.25
2.95
Tester oil delivery pressure
kPa
157
157
157
Tester oil delivery pressure
kgf/cm2
1.6
1.6
1.6
Direction of rotation (viewed from drive side)
Right R
Right R
Injection timing adjustment
Direction of rotation (viewed from drive side)
Right R
Right R
Injection order
1-5-3-6-
2-4
Pre-stroke
mm
4.5
4.45
4.55
Beginning of injection position
Governor side NO.1
Governor side NO.1
Difference between angles 1
Cal 1-5 deg. 60 59.5 60.5
Cal 1-5 deg. 60 59.5 60.5
Difference between angles 2
Cal 1-3 deg. 120 119.5 120.5
Cal 1-3 deg. 120 119.5 120.5
Difference between angles 3
Cal 1-6 deg. 180 179.5 180.5
Cal 1-6 deg. 180 179.5 180.5
Difference between angles 4
Cyl.1-2 deg. 240 239.5 240.5
Cyl.1-2 deg. 240 239.5 240.5
Difference between angles 5
Cal 1-4 deg. 300 299.5 300.5
Cal 1-4 deg. 300 299.5 300.5
Injection quantity adjustment
Adjusting point
A
Rack position
9.3
Pump speed
r/min
750
750
750
Average injection quantity
mm3/st.
114.3
111.3
117.3
Max. variation between cylinders
%
0
-3
3
Basic
*
Fixing the lever
*
Injection quantity adjustment_02
Adjusting point
B
Rack position
9
Pump speed
r/min
750
750
750
Average injection quantity
mm3/st.
106.5
100.5
112.5
Fixing the rack
*
Injection quantity adjustment_03
Adjusting point
C
Rack position
6.9+-0.5
Pump speed
r/min
250
250
250
Average injection quantity
mm3/st.
14.6
12
17.2
Max. variation between cylinders
%
0
-15
15
Fixing the rack
*
Injection quantity adjustment_04
Adjusting point
D
Rack position
13+1
Pump speed
r/min
100
100
100
Average injection quantity
mm3/st.
155
155
175
Fixing the lever
*
Rack limit
*
Test data Ex:
Governor adjustment

N:Pump speed
R:Rack position (mm)
(1)Target notch: K
(2)RACK LIMIT: RAL
(3)Idle sub spring setting: L1.
(4)Setting at shipping
(5)Rack difference between N = N1 and N = N2
----------
K=8 RAL=13+1mm L1=5+-0.1mm N1=750r/min N2=250r/min
----------
----------
K=8 RAL=13+1mm L1=5+-0.1mm N1=750r/min N2=250r/min
----------
Speed control lever angle

F:Full speed
I:Idle
(1)Stopper bolt setting
(2)At shipping
(3)Set the pump speed at aa
(4)Set the pump speed at bb.
----------
aa=750r/min bb=900r/min
----------
a=24deg+-5deg b=(2deg) c=1deg+-5deg d=5deg+-5deg
----------
aa=750r/min bb=900r/min
----------
a=24deg+-5deg b=(2deg) c=1deg+-5deg d=5deg+-5deg
Stop lever angle

N:Pump normal
S:Stop the pump.
----------
----------
a=19deg+-5deg b=53deg+-5deg
----------
----------
a=19deg+-5deg b=53deg+-5deg
Timing setting

(1)Pump vertical direction
(2)Coupling's key groove position at No 1 cylinder's beginning of injection
(3)-
(4)-
----------
----------
a=(7deg)
----------
----------
a=(7deg)
Information:
The current API categories represent the minimum requirements for diesel engine oils. These categories are developed in collaboration of OEMs and the Oil and Chemical industries.The current licensed oils are:
API CK-4, released December 2016
API CJ-4, released 2006
API CI-4, API CI-4PLUS released 2002
API CH-4, released 1998Each API category is technically more advanced and of higher performance than the prior one.Refer to API 1509 document and/or ASTM D4485 for details of the API tests requirements and limits.Note: Obsolete API oil categories are not licensed by the API and hence are of uncontrolled quality. These oils are technically inferior to current oils and can result in reduced engine performance and life. These obsolete oil categories are not allowed in Cat engines.API FA-4 is NOT recommended for Caterpillar engines. API FA oil is designed with low High Temperature High Shear (HTHS) viscosity oil for use in certain 2017 On-Highway truck engines that have to meet certain on-road emissions regulations. This category is not backwards compatible.In order to help protect your engine, and in order to help optimize oil drain intervals for engine applications and duty cycles, use Cat S O S Services oil analysis. Refer to the section below and to the section on Cat S O S Services given later in the Special Publication.
Depending on application severity and localized environmental conditions, and also depending on maintenance practices, operating Direct Injection (DI) diesel engines and operating PC (Precombustion Chamber) diesel engines on fuel with sulfur levels over 0.1 percent (1000 ppm) may require significantly shortened oil change intervals in order to help maintain adequate wear protection. Refer to this Special Publication, "Fuel Specifications" section, “Diesel Fuel Sulfur” topic for additional information.
Fuel Sulfur Impact on Engine Oil
The use of Cat S O S Services oil analysis is recommended for determining oil life.For Caterpillar machines operating under emissions regulations such as US EPA Tier4, EU Stage V or other emission regulations controls, the maximum fuel sulfur level permitted by regulations in the US is 0.0015% or 15 ppm. Maximum permitted fuel sulfur levels in other emissions regulated countries may vary from .0015% or 15 ppm slightly and must be followed.In order to help protect your engine and optimize oil drain intervals for engine applications and duty cycles, it is important to use SOS Services oil analysis to determine if the sulfur has degraded the oil. Use Cat S O S Services oil analysis per the following general guidelines:
Recommended normally
For fuel sulfur level up to 0.05 percent (500 ppm), no additional sampling is required. Follow the recommended oil sampling in the machine OMM
For fuel sulfur level of > 0.05 percent to 0.5 percent (500 ppm to 5000 ppm), SOS services oil analysis is strongly recommended to determine oil drain intervals. Sample the oil every 250 hours until a trend is established,
API CK-4, released December 2016
API CJ-4, released 2006
API CI-4, API CI-4PLUS released 2002
API CH-4, released 1998Each API category is technically more advanced and of higher performance than the prior one.Refer to API 1509 document and/or ASTM D4485 for details of the API tests requirements and limits.Note: Obsolete API oil categories are not licensed by the API and hence are of uncontrolled quality. These oils are technically inferior to current oils and can result in reduced engine performance and life. These obsolete oil categories are not allowed in Cat engines.API FA-4 is NOT recommended for Caterpillar engines. API FA oil is designed with low High Temperature High Shear (HTHS) viscosity oil for use in certain 2017 On-Highway truck engines that have to meet certain on-road emissions regulations. This category is not backwards compatible.In order to help protect your engine, and in order to help optimize oil drain intervals for engine applications and duty cycles, use Cat S O S Services oil analysis. Refer to the section below and to the section on Cat S O S Services given later in the Special Publication.
Depending on application severity and localized environmental conditions, and also depending on maintenance practices, operating Direct Injection (DI) diesel engines and operating PC (Precombustion Chamber) diesel engines on fuel with sulfur levels over 0.1 percent (1000 ppm) may require significantly shortened oil change intervals in order to help maintain adequate wear protection. Refer to this Special Publication, "Fuel Specifications" section, “Diesel Fuel Sulfur” topic for additional information.
Fuel Sulfur Impact on Engine Oil
The use of Cat S O S Services oil analysis is recommended for determining oil life.For Caterpillar machines operating under emissions regulations such as US EPA Tier4, EU Stage V or other emission regulations controls, the maximum fuel sulfur level permitted by regulations in the US is 0.0015% or 15 ppm. Maximum permitted fuel sulfur levels in other emissions regulated countries may vary from .0015% or 15 ppm slightly and must be followed.In order to help protect your engine and optimize oil drain intervals for engine applications and duty cycles, it is important to use SOS Services oil analysis to determine if the sulfur has degraded the oil. Use Cat S O S Services oil analysis per the following general guidelines:
Recommended normally
For fuel sulfur level up to 0.05 percent (500 ppm), no additional sampling is required. Follow the recommended oil sampling in the machine OMM
For fuel sulfur level of > 0.05 percent to 0.5 percent (500 ppm to 5000 ppm), SOS services oil analysis is strongly recommended to determine oil drain intervals. Sample the oil every 250 hours until a trend is established,
Have questions with 101602-1320?
Group cross 101602-1320 ZEXEL
Mitsubishi
101602-1320
F 019 Z10 823
ME157337
INJECTION-PUMP ASSEMBLY
6D22
6D22