Information injection-pump assembly
BOSCH
9 400 611 746
9400611746
ZEXEL
101602-1150
1016021150
MITSUBISHI
ME070757
me070757
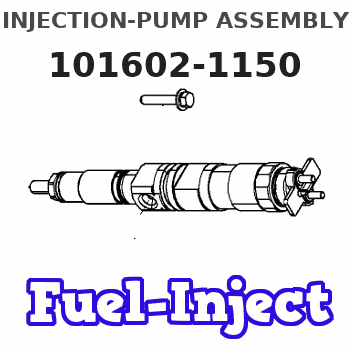
Rating:
Service parts 101602-1150 INJECTION-PUMP ASSEMBLY:
1.
_
5.
AUTOM. ADVANCE MECHANIS
6.
COUPLING PLATE
8.
_
9.
_
11.
Nozzle and Holder
ME070516
12.
Open Pre:MPa(Kqf/cm2)
17.7{180}
15.
NOZZLE SET
Cross reference number
BOSCH
9 400 611 746
9400611746
ZEXEL
101602-1150
1016021150
MITSUBISHI
ME070757
me070757
Zexel num
Bosch num
Firm num
Name
101602-1150
9 400 611 746
ME070757 MITSUBISHI
INJECTION-PUMP ASSEMBLY
6D14T K 14BF INJECTION PUMP ASSY PE6AD PE
6D14T K 14BF INJECTION PUMP ASSY PE6AD PE
Calibration Data:
Adjustment conditions
Test oil
1404 Test oil ISO4113 or {SAEJ967d}
1404 Test oil ISO4113 or {SAEJ967d}
Test oil temperature
degC
40
40
45
Nozzle and nozzle holder
105780-8140
Bosch type code
EF8511/9A
Nozzle
105780-0000
Bosch type code
DN12SD12T
Nozzle holder
105780-2080
Bosch type code
EF8511/9
Opening pressure
MPa
17.2
Opening pressure
kgf/cm2
175
Injection pipe
Outer diameter - inner diameter - length (mm) mm 6-2-600
Outer diameter - inner diameter - length (mm) mm 6-2-600
Overflow valve
131424-4620
Overflow valve opening pressure
kPa
255
221
289
Overflow valve opening pressure
kgf/cm2
2.6
2.25
2.95
Tester oil delivery pressure
kPa
157
157
157
Tester oil delivery pressure
kgf/cm2
1.6
1.6
1.6
Direction of rotation (viewed from drive side)
Left L
Left L
Injection timing adjustment
Direction of rotation (viewed from drive side)
Left L
Left L
Injection order
1-5-3-6-
2-4
Pre-stroke
mm
3.3
3.25
3.35
Beginning of injection position
Governor side NO.1
Governor side NO.1
Difference between angles 1
Cal 1-5 deg. 60 59.5 60.5
Cal 1-5 deg. 60 59.5 60.5
Difference between angles 2
Cal 1-3 deg. 120 119.5 120.5
Cal 1-3 deg. 120 119.5 120.5
Difference between angles 3
Cal 1-6 deg. 180 179.5 180.5
Cal 1-6 deg. 180 179.5 180.5
Difference between angles 4
Cyl.1-2 deg. 240 239.5 240.5
Cyl.1-2 deg. 240 239.5 240.5
Difference between angles 5
Cal 1-4 deg. 300 299.5 300.5
Cal 1-4 deg. 300 299.5 300.5
Injection quantity adjustment
Adjusting point
A
Rack position
11.4
Pump speed
r/min
850
850
850
Average injection quantity
mm3/st.
98.6
97.6
99.6
Max. variation between cylinders
%
0
-2.5
2.5
Basic
*
Fixing the lever
*
Injection quantity adjustment_02
Adjusting point
-
Rack position
7+-0.5
Pump speed
r/min
350
350
350
Average injection quantity
mm3/st.
15
12.4
17.6
Max. variation between cylinders
%
0
-15
15
Fixing the rack
*
Remarks
Adjust only variation between cylinders; adjust governor according to governor specifications.
Adjust only variation between cylinders; adjust governor according to governor specifications.
Test data Ex:
Governor adjustment
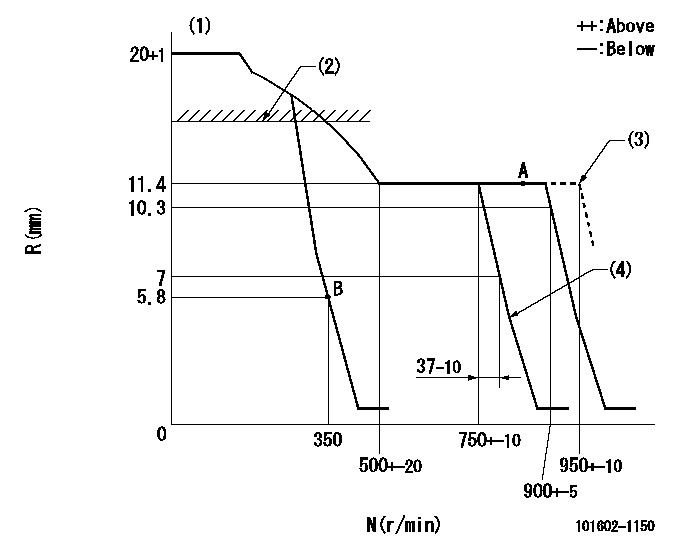
N:Pump speed
R:Rack position (mm)
(1)Target notch: K
(2)RACK CAP: R1
(3)At shipping
(4)Idle sub spring setting: L1.
----------
K=10 R1=(17.5)mm L1=4-0.5mm
----------
----------
K=10 R1=(17.5)mm L1=4-0.5mm
----------
Speed control lever angle

F:Full speed
I:Idle
(1)Stopper bolt setting
(2)At shipping
(3)Pump speed = aa
(4)Pump speed = bb
----------
aa=750r/min bb=900r/min
----------
a=27deg+-5deg b=(2deg) c=2deg+-5deg d=6deg+-5deg
----------
aa=750r/min bb=900r/min
----------
a=27deg+-5deg b=(2deg) c=2deg+-5deg d=6deg+-5deg
Stop lever angle

N:Pump normal
S:Stop the pump.
(1)At delivery
----------
----------
a=26deg+-5deg b=53deg+-5deg
----------
----------
a=26deg+-5deg b=53deg+-5deg
Timing setting

(1)Pump vertical direction
(2)Position of coupling's tooth at No 1 cylinder's beginning of injection
(3)B.T.D.C.: aa
(4)-
----------
aa=14deg
----------
a=(0deg)
----------
aa=14deg
----------
a=(0deg)
Information:
Disconnect all electrical power from the monitor before removing components. Failure to disconnect the power could result in severe electrical shock or damage to the monitor. An electrical shock can cause severe personal injury or death.
Components that are inside of the monitor may be damaged by Electrostatic Discharge (ESD). Make sure that you wear a grounding strap whenever you handle the following components: circuit boards, memory modules and other internal components.
Wear a well grounded wrist strap and perform work in a static free environment. Electrostatic discharge can damage the monitor and components.
In order to remove the back cover or the top cover, perform the following procedure:
Disconnect the power from the monitor.
Illustration 1 g00858068
(1) 4 Screws (2) 8 Screws
Loosen the 8 screws (2) that secure the back cover in place. Remove the screws in order to access the power supply, the hard drive, and the floppy disk drive.
Loosen the 4 screws (1) that secure the top cover. Remove the screws in order to access the add-in cards and the memory modules.
In order to reinstall the back cover, position the back cover over the chassis and tighten the 8 screws (2). Align the two pins on the inside of the back cover that secure the hard drive bay.Note: Be careful not to push the vibration dampers (grommets) on the drive out of the sheet metal.
In order to reinstall the top cover, position the top cover over the chassis and tighten the 4 screws (1) .
Have questions with 101602-1150?
Group cross 101602-1150 ZEXEL
Mitsubishi
101602-1150
9 400 611 746
ME070757
INJECTION-PUMP ASSEMBLY
6D14T
6D14T