Information injection-pump assembly
ZEXEL
101602-0670
1016020670
ISUZU
1156008771
1156008771
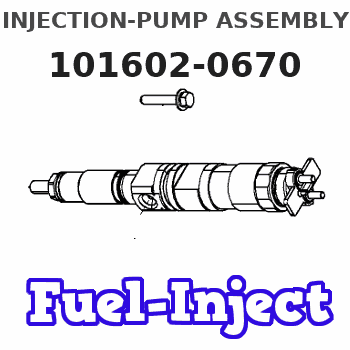
Rating:
Cross reference number
ZEXEL
101602-0670
1016020670
ISUZU
1156008771
1156008771
Zexel num
Bosch num
Firm num
Name
Calibration Data:
Adjustment conditions
Test oil
1404 Test oil ISO4113 or {SEAJ967d}
1404 Test oil ISO4113 or {SEAJ967d}
Test oil temperature
degC
40
40
45
Nozzle and nozzle holder
105780-8140
Bosch type code
EF8511/9A
Nozzle
105780-0000
Bosch type code
DN12SD12T
Nozzle holder
105780-2080
Bosch type code
EF8511/9
Opening pressure
MPa
17.2
Opening pressure
kgf/cm2
175
Injection pipe
Outer diameter - inner diameter - length (mm) mm 6-2-600
Outer diameter - inner diameter - length (mm) mm 6-2-600
Overflow valve
132424-0620
Overflow valve opening pressure
kPa
157
123
191
Overflow valve opening pressure
kgf/cm2
1.6
1.25
1.95
Tester oil delivery pressure
kPa
157
157
157
Tester oil delivery pressure
kgf/cm2
1.6
1.6
1.6
Direction of rotation (viewed from drive side)
Right R
Right R
Injection timing adjustment
Direction of rotation (viewed from drive side)
Right R
Right R
Injection order
1-5-3-6-
2-4
Pre-stroke
mm
3.2
3.15
3.25
Beginning of injection position
Drive side NO.1
Drive side NO.1
Difference between angles 1
Cal 1-5 deg. 60 59.5 60.5
Cal 1-5 deg. 60 59.5 60.5
Difference between angles 2
Cal 1-3 deg. 120 119.5 120.5
Cal 1-3 deg. 120 119.5 120.5
Difference between angles 3
Cal 1-6 deg. 180 179.5 180.5
Cal 1-6 deg. 180 179.5 180.5
Difference between angles 4
Cyl.1-2 deg. 240 239.5 240.5
Cyl.1-2 deg. 240 239.5 240.5
Difference between angles 5
Cal 1-4 deg. 300 299.5 300.5
Cal 1-4 deg. 300 299.5 300.5
Injection quantity adjustment
Adjusting point
A
Rack position
8.6
Pump speed
r/min
900
900
900
Average injection quantity
mm3/st.
66.5
65
68
Max. variation between cylinders
%
0
-2.5
2.5
Basic
*
Fixing the rack
*
Injection quantity adjustment_02
Adjusting point
B
Rack position
5.6+-0.5
Pump speed
r/min
325
325
325
Average injection quantity
mm3/st.
10.2
8.9
11.5
Max. variation between cylinders
%
0
-14
14
Fixing the rack
*
Test data Ex:
Governor adjustment
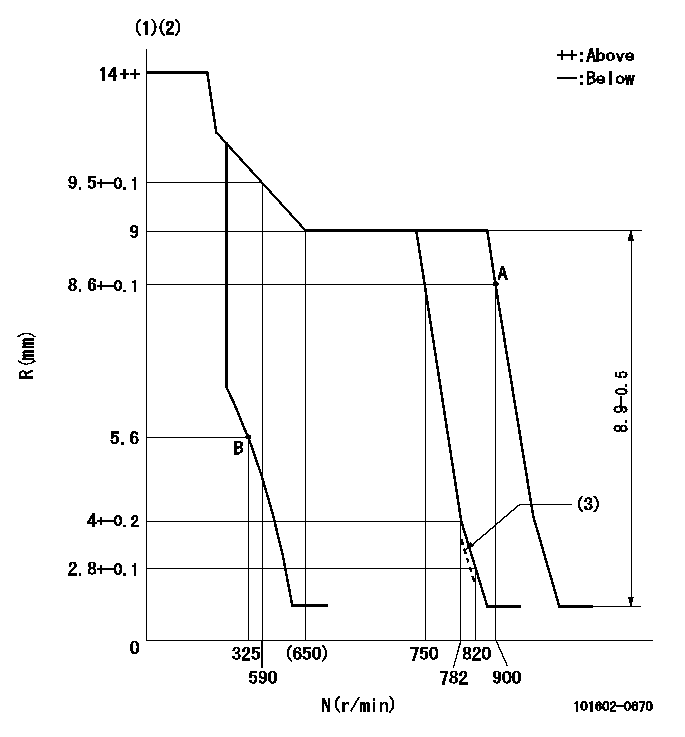
N:Pump speed
R:Rack position (mm)
(1)Target notch: K
(2)Tolerance for racks not indicated: +-0.05mm.
(3)Set idle sub-spring
----------
K=10
----------
----------
K=10
----------
Speed control lever angle
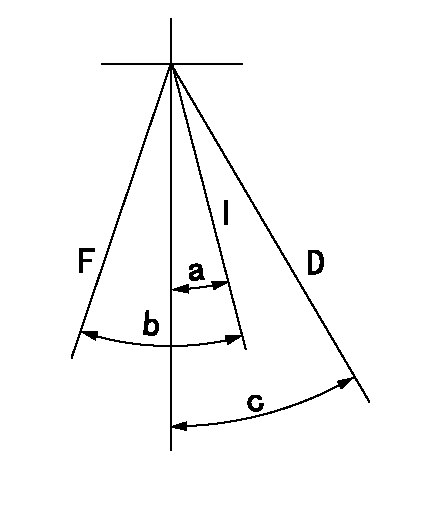
F:Full speed
I:Idle
D:Dead point
----------
----------
a=18deg+-1deg b=27deg+-5deg c=20deg+-3deg
----------
----------
a=18deg+-1deg b=27deg+-5deg c=20deg+-3deg
Stop lever angle

N:Pump normal
S:Stop the pump.
(1)Normal
----------
----------
a=2.5deg+-5deg b=46deg+-5deg
----------
----------
a=2.5deg+-5deg b=46deg+-5deg
0000001501 LEVER
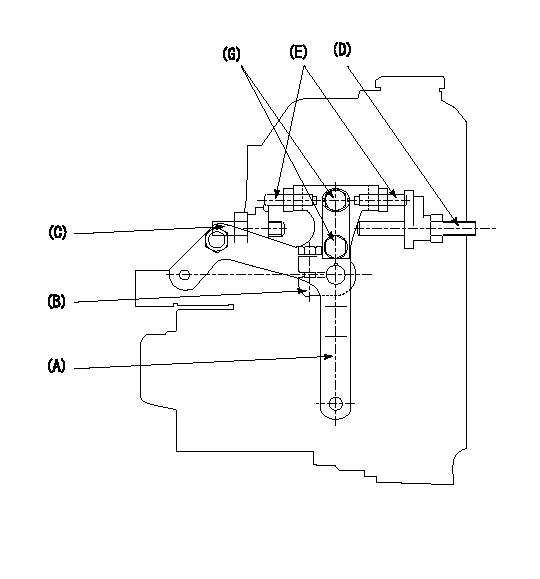
1. Variable lever adjustment
(1)Fix lever (B) in the beginning of speed increase position using bolts (C) and (D).
(2)Temporarily fix the lever (A) at the dead point and measure the lever angle .
(3)Fix the lever (A) at the idle lever angle position using the bolt (E).
(4)Lock using bolt (G).
(5)After completing idle adjustment, loosen the full side stopper bolt (D).
(6)Move the lever (A) in the full speed direction.
(7)Fix bolt (D) at full speed position.
(8)Finally, measure the lever angle and set the idle stopper bolt (C) stop position.
----------
----------
----------
----------
Timing setting

(1)Pump vertical direction
(2)Position of gear mark 'CC' at No 1 cylinder's beginning of injection
(3)B.T.D.C.: aa
(4)-
----------
aa=16deg
----------
a=(100deg)
----------
aa=16deg
----------
a=(100deg)
Information:
Test Procedure
System Operation
A thermocouple is a temperature sensor. The thermocouple consists of two different metals. The metals are joined together at one end. A small voltage is produced when the junction is heated. The change in voltage is interpreted by an electronic device in order to determine a change in temperature. The MMS uses K type thermocouples. The K type thermocouples have ranges from -200 °C (-328 °F)to 1260 °C (2300 °F). This temperature range corresponds to a voltage range of negative 5.9 mV to 51.0 mV.The signal is used in order to trigger alarms and the signal is used in order to display the parameter.
Illustration 1 g00563634
Diagram of the thermocouple
Illustration 2 g00563637
Schematic of the thermocoupleFunctional Test
Check the electrical connectors and check the wiring.
Bodily contact with electrical potential can cause bodily injury or death.To avoid the possibility of injury or death, ensure that the main power supply has been disconnected before performing any maintenance or removing any modules.
Disconnect the power supply.
Check the electrical connectors and check the wiring for damage or bad connections.
Verify that all modules are properly seated.
Verify the status of the LED on the SLC 5/04.The results of the preceding procedure are in the following list:
All of the components are fully installed. All of the components are free of corrosion. All of the components are free of damage. All of the modules are properly seated. Stop.
The components are not fully installed. The components are not free of corrosion. The components are damaged. All of the modules are not properly seated. Repair the component. Verify that the repair resolves the problem. STOP.
System Operation
A thermocouple is a temperature sensor. The thermocouple consists of two different metals. The metals are joined together at one end. A small voltage is produced when the junction is heated. The change in voltage is interpreted by an electronic device in order to determine a change in temperature. The MMS uses K type thermocouples. The K type thermocouples have ranges from -200 °C (-328 °F)to 1260 °C (2300 °F). This temperature range corresponds to a voltage range of negative 5.9 mV to 51.0 mV.The signal is used in order to trigger alarms and the signal is used in order to display the parameter.
Illustration 1 g00563634
Diagram of the thermocouple
Illustration 2 g00563637
Schematic of the thermocoupleFunctional Test
Check the electrical connectors and check the wiring.
Bodily contact with electrical potential can cause bodily injury or death.To avoid the possibility of injury or death, ensure that the main power supply has been disconnected before performing any maintenance or removing any modules.
Disconnect the power supply.
Check the electrical connectors and check the wiring for damage or bad connections.
Verify that all modules are properly seated.
Verify the status of the LED on the SLC 5/04.The results of the preceding procedure are in the following list:
All of the components are fully installed. All of the components are free of corrosion. All of the components are free of damage. All of the modules are properly seated. Stop.
The components are not fully installed. The components are not free of corrosion. The components are damaged. All of the modules are not properly seated. Repair the component. Verify that the repair resolves the problem. STOP.