Information injection-pump assembly
ZEXEL
101602-0370
1016020370
ISUZU
5156010493
5156010493
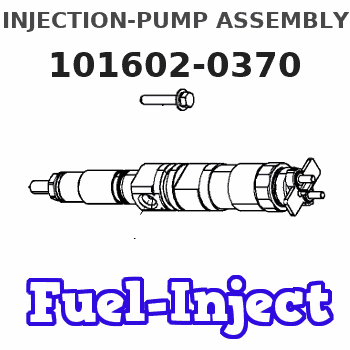
Rating:
Cross reference number
ZEXEL
101602-0370
1016020370
ISUZU
5156010493
5156010493
Zexel num
Bosch num
Firm num
Name
Calibration Data:
Adjustment conditions
Test oil
1404 Test oil ISO4113 or {SAEJ967d}
1404 Test oil ISO4113 or {SAEJ967d}
Test oil temperature
degC
40
40
45
Nozzle and nozzle holder
105780-8140
Bosch type code
EF8511/9A
Nozzle
105780-0000
Bosch type code
DN12SD12T
Nozzle holder
105780-2080
Bosch type code
EF8511/9
Opening pressure
MPa
17.2
Opening pressure
kgf/cm2
175
Injection pipe
Outer diameter - inner diameter - length (mm) mm 6-2-600
Outer diameter - inner diameter - length (mm) mm 6-2-600
Tester oil delivery pressure
kPa
157
157
157
Tester oil delivery pressure
kgf/cm2
1.6
1.6
1.6
Direction of rotation (viewed from drive side)
Right R
Right R
Injection timing adjustment
Direction of rotation (viewed from drive side)
Right R
Right R
Injection order
1-5-3-6-
2-4
Pre-stroke
mm
3.6
3.55
3.65
Beginning of injection position
Drive side NO.1
Drive side NO.1
Difference between angles 1
Cal 1-5 deg. 60 59.5 60.5
Cal 1-5 deg. 60 59.5 60.5
Difference between angles 2
Cal 1-3 deg. 120 119.5 120.5
Cal 1-3 deg. 120 119.5 120.5
Difference between angles 3
Cal 1-6 deg. 180 179.5 180.5
Cal 1-6 deg. 180 179.5 180.5
Difference between angles 4
Cyl.1-2 deg. 240 239.5 240.5
Cyl.1-2 deg. 240 239.5 240.5
Difference between angles 5
Cal 1-4 deg. 300 299.5 300.5
Cal 1-4 deg. 300 299.5 300.5
Injection quantity adjustment
Adjusting point
A
Rack position
8.4
Pump speed
r/min
750
750
750
Average injection quantity
mm3/st.
49.1
47.6
50.6
Max. variation between cylinders
%
0
-2
2
Basic
*
Fixing the rack
*
Injection quantity adjustment_02
Adjusting point
B
Rack position
9.1
Pump speed
r/min
725
725
725
Average injection quantity
mm3/st.
61.6
59.6
63.6
Max. variation between cylinders
%
0
-4
4
Fixing the lever
*
Injection quantity adjustment_03
Adjusting point
C
Rack position
6.7+-0.5
Pump speed
r/min
325
325
325
Average injection quantity
mm3/st.
9.4
8.1
10.7
Max. variation between cylinders
%
0
-14
14
Fixing the rack
*
Remarks
Adjust only variation between cylinders; adjust governor according to governor specifications.
Adjust only variation between cylinders; adjust governor according to governor specifications.
Test data Ex:
Governor adjustment

N:Pump speed
R:Rack position (mm)
(1)Target notch: K
----------
K=10
----------
----------
K=10
----------
Speed control lever angle
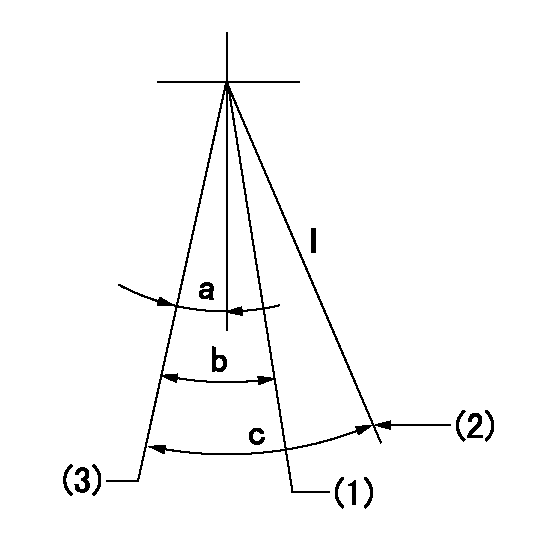
I:Idle
(1)Set the pump speed at aa
(2)Stopper bolt setting
(3)Set speed at bb (setting at shipping).
----------
aa=750r/min bb=900r/min
----------
a=3deg+-5deg b=6deg+-5deg c=24deg+-5deg
----------
aa=750r/min bb=900r/min
----------
a=3deg+-5deg b=6deg+-5deg c=24deg+-5deg
Stop lever angle
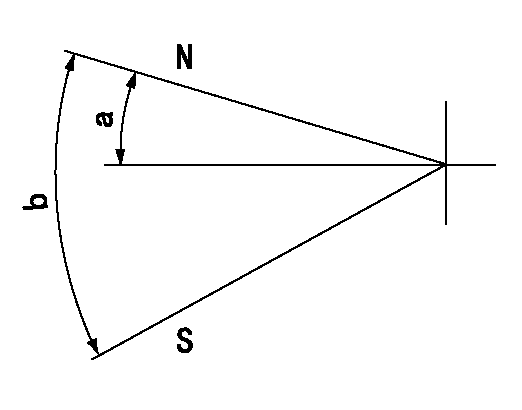
N:Pump normal
S:Stop the pump.
----------
----------
a=12deg+-5deg b=46deg+-5deg
----------
----------
a=12deg+-5deg b=46deg+-5deg
Timing setting

(1)Pump vertical direction
(2)Position of gear mark 'CC' at No 1 cylinder's beginning of injection
(3)B.T.D.C.: aa
(4)-
----------
aa=20deg
----------
a=(90deg)
----------
aa=20deg
----------
a=(90deg)
Information:
Illustration 1 g00564355
7W-2743 Electronic Speed Switch (ESS)
(1) Push button for Overspeed Verification
(2) Reset button
(3) Overspeed indicator lamp
(4) Seal screw plug for adjusting the engine overspeed
(5) Seal screw plug for adjusting the crank terminate speed
(6) Seal screw plug for adjusting the oil step pressure speed setting The procedure for the magnetic pickup test will determine if the operation of the magnetic pickup is correct.
Connect a 6V-7070 Digital Multimeter to the "COM" terminal and the "SIG" terminal. The terminals are (ESS-3)and (ESS-4) of the ESS. Set the meter voltage scale to a scale that is greater than 1.5 VAC. Start the engine. Run the engine at low idle or 600 rpm. Choose the one that is larger. If the voltage that is measured is 1.5 VAC or more, the operation of the magnetic pickup is correct. If the voltage is less than 1.5 VAC, go to Step 2.
Stop the engine. Disconnect the wiring for the magnetic pickup at the plug-in connector. Connect the voltmeter to the connector terminals of the magnetic pickup. Start the engine. Run the engine at low idle or 600 rpm. Choose the one that is larger. If the voltage that is measured is 1.5 VAC or more, repair the wiring that is between the magnetic pickup and the ESS. If the voltage is less than 1.5 VAC, go to Step 3.
Illustration 2 g00564913
Magnetic pickup
(1) Clearance
(2) Magnetic pickup
(3) Wires to the connector
(4) Locknut
(5) Flywheel housing
(6) Ring gear
Loosen locknut (4) and turn magnetic pickup (2) in the counterclockwise direction in order to remove magnetic pickup (2) from flywheel housing (5). Turn the flywheel until a gear tooth of ring gear (6) is directly in the center of the threaded hole for magnetic pickup (2). Install magnetic pickup (2) in flywheel housing (5).
Turn magnetic pickup (2) in the clockwise direction until the end of magnetic pickup (2) slightly touches the gear tooth. Turn the magnetic pickup for one-half turn in the counterclockwise direction in order to set correct clearance (1). Tighten locknut (4) to a torque of 45 7 N m (33 5 lb ft). Note: Do not allow the magnetic pickup to turn while the locknut is tightened.
Repeat Step 2. If the voltage is still less than 1.5 VAC, replace the magnetic pickup.