Information injection-pump assembly
BOSCH
9 400 614 698
9400614698
ZEXEL
101601-9970
1016019970
NISSAN-DIESEL
1670095069
1670095069
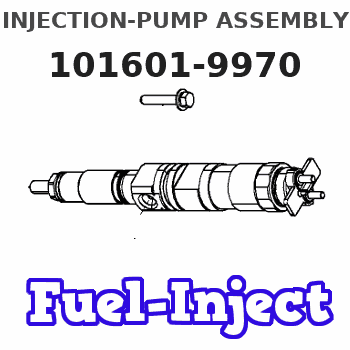
Rating:
Service parts 101601-9970 INJECTION-PUMP ASSEMBLY:
1.
_
7.
COUPLING PLATE
8.
_
9.
_
11.
Nozzle and Holder
16600-95013
12.
Open Pre:MPa(Kqf/cm2)
19.6{200}
15.
NOZZLE SET
Cross reference number
BOSCH
9 400 614 698
9400614698
ZEXEL
101601-9970
1016019970
NISSAN-DIESEL
1670095069
1670095069
Zexel num
Bosch num
Firm num
Name
101601-9970
9 400 614 698
1670095069 NISSAN-DIESEL
INJECTION-PUMP ASSEMBLY
NE6 K 14BE INJECTION PUMP ASSY PE6A PE
NE6 K 14BE INJECTION PUMP ASSY PE6A PE
Calibration Data:
Adjustment conditions
Test oil
1404 Test oil ISO4113 or {SAEJ967d}
1404 Test oil ISO4113 or {SAEJ967d}
Test oil temperature
degC
40
40
45
Nozzle and nozzle holder
105780-8140
Bosch type code
EF8511/9A
Nozzle
105780-0000
Bosch type code
DN12SD12T
Nozzle holder
105780-2080
Bosch type code
EF8511/9
Opening pressure
MPa
17.2
Opening pressure
kgf/cm2
175
Injection pipe
Outer diameter - inner diameter - length (mm) mm 6-2-600
Outer diameter - inner diameter - length (mm) mm 6-2-600
Overflow valve
132424-0620
Overflow valve opening pressure
kPa
157
123
191
Overflow valve opening pressure
kgf/cm2
1.6
1.25
1.95
Tester oil delivery pressure
kPa
157
157
157
Tester oil delivery pressure
kgf/cm2
1.6
1.6
1.6
Direction of rotation (viewed from drive side)
Right R
Right R
Injection timing adjustment
Direction of rotation (viewed from drive side)
Right R
Right R
Injection order
1-4-2-6-
3-5
Pre-stroke
mm
3
2.95
3.05
Beginning of injection position
Drive side NO.1
Drive side NO.1
Difference between angles 1
Cal 1-4 deg. 60 59.5 60.5
Cal 1-4 deg. 60 59.5 60.5
Difference between angles 2
Cyl.1-2 deg. 120 119.5 120.5
Cyl.1-2 deg. 120 119.5 120.5
Difference between angles 3
Cal 1-6 deg. 180 179.5 180.5
Cal 1-6 deg. 180 179.5 180.5
Difference between angles 4
Cal 1-3 deg. 240 239.5 240.5
Cal 1-3 deg. 240 239.5 240.5
Difference between angles 5
Cal 1-5 deg. 300 299.5 300.5
Cal 1-5 deg. 300 299.5 300.5
Injection quantity adjustment
Adjusting point
A
Rack position
8.8
Pump speed
r/min
1400
1400
1400
Average injection quantity
mm3/st.
79.4
78.4
80.4
Max. variation between cylinders
%
0
-3.5
3.5
Basic
*
Fixing the lever
*
Injection quantity adjustment_02
Adjusting point
B
Rack position
9.2
Pump speed
r/min
600
600
600
Average injection quantity
mm3/st.
68.3
66.3
70.3
Max. variation between cylinders
%
0
-5
5
Fixing the lever
*
Injection quantity adjustment_03
Adjusting point
C
Rack position
7.2+-0.5
Pump speed
r/min
285
285
285
Average injection quantity
mm3/st.
9
7.2
10.8
Max. variation between cylinders
%
0
-10
10
Fixing the rack
*
Injection quantity adjustment_04
Adjusting point
D
Rack position
13.2+-0.
5
Pump speed
r/min
150
150
150
Average injection quantity
mm3/st.
115
115
Fixing the lever
*
Remarks
After startup boost setting
After startup boost setting
Timer adjustment
Pump speed
r/min
550--
Advance angle
deg.
0
0
0
Remarks
Start
Start
Timer adjustment_02
Pump speed
r/min
500
Advance angle
deg.
0.5
Timer adjustment_03
Pump speed
r/min
800
Advance angle
deg.
1.5
1
2
Timer adjustment_04
Pump speed
r/min
1200
Advance angle
deg.
4
3.5
4.5
Remarks
Finish
Finish
Test data Ex:
Governor adjustment
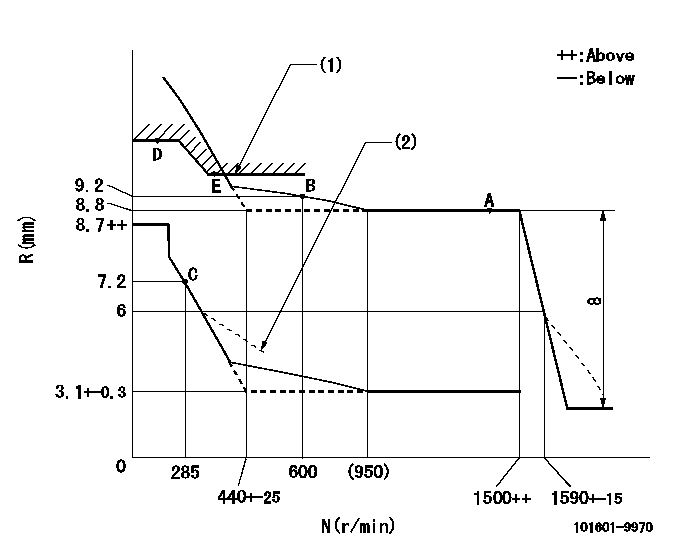
N:Pump speed
R:Rack position (mm)
(1)Excess fuel setting for starting: SXL
(2)Damper spring setting: DL
----------
SXL=10+0.2mm DL=6-0.2mm
----------
----------
SXL=10+0.2mm DL=6-0.2mm
----------
0000000901

F:Full load
I:Idle
(1)Stopper bolt setting
----------
----------
a=16.5deg+-5deg b=21deg+-3deg
----------
----------
a=16.5deg+-5deg b=21deg+-3deg
Stop lever angle

N:Pump normal
S:Stop the pump.
(1)Use the pin at R = aa
----------
aa=20mm
----------
a=71deg+-5deg b=40deg+-5deg
----------
aa=20mm
----------
a=71deg+-5deg b=40deg+-5deg
Timing setting
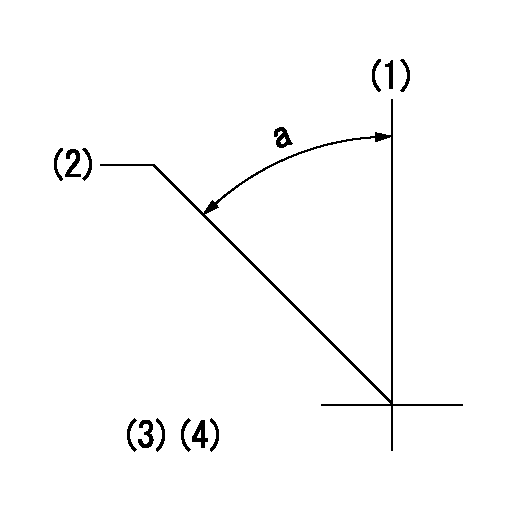
(1)Pump vertical direction
(2)Coupling's key groove position at No 1 cylinder's beginning of injection
(3)-
(4)-
----------
----------
a=(35deg)
----------
----------
a=(35deg)
Information:
ACTION REQUIRED
Do not order the 601-8546 and 601-8547 Hoses. The new hoses have been direct shipped to the dealership prior to the release of this Service Letter program.
If you have not received the parts, the parts received are damaged, or if you have any questions you will need to work with your Dealer TC to submit the information or question through CPI Feedback within the Service Information Management System (SIMSi).
Give the information to your Dealer Technical Communicator (TC) along with this service letter program number and CPI number 472555.
Request the Dealer TC to submit the CPI Feedback.
Refer to the attached Rework Procedure.
OWNER NOTIFICATION
Owners in the following countries will receive the attached Owner Notification:
US
Canada
SERVICE CLAIM ALLOWANCES
Caterpillar Dealer Suggested Customer Suggested
Parts % Labor Hrs% Parts % Labor Hrs% Parts % Labor Hrs%
100% 100% 0% 0% 0% 0%
This is a 1.5-hour job
Note: $60 US Dollars are allowed for 10 Liters of coolant.
PARTS DISPOSITION
Handle the parts in accordance with your Warranty Bulletin on warranty parts handling.
MAKE EVERY EFFORT TO COMPLETE THIS PROGRAM AS SOON AS POSSIBLE.
EXAMPLE COPY OF OWNER NOTIFICATION
XYZ Corporation
3240 Arrow Drive
Anywhere, YZ 99999
PRIORITY - PRODUCT IMPROVEMENT PROGRAM FOR REPLACING THE DEF INJECTOR COOLANT HOSES
MODELS INVOLVED - CERTAIN 313 AND 315 NGH EXCAVATORS
Dear Cat Product Owner:
The existing coolant hoses need to be replaced on the products listed below. The existing hoses can leak water and/or burst. You will not be charged for the service performed.
Contact your local Cat dealer immediately to schedule this service. The dealer will advise you of the time required to complete this service.
If you are no longer the owner of this product(s), please contact your local Cat dealer so that our records can be updated. Please refer the dealer to their Service Letter dated 01Jul2020 when scheduling this service.
We regret the inconvenience this may cause you, and urge you to have this service performed as soon as possible to prevent unscheduled downtime.
Caterpillar Inc.
Identification #(s)
Attached to 01Jul2020 Service Letter
Rework Procedure
1. Confirm the machine/engine components/coolant are cooled down for safety.
2. Drain coolant (approximately 10L) to avoid spilling out from hoses during replacement.
3. Removed the strap on hose. Refer to Image1.3.1.
Image1.3.1
4. Loosen the clamps and remove the hoses (both inlet and outlet). Refer to Image1.4.1.
Image1.4.1
5. Install new parts. Refer to Images1.5.1 and 1.5.2.
Image1.5.1
Image1.5.2
6. Fill the coolant and check for leakage from the hoses.
Have questions with 101601-9970?
Group cross 101601-9970 ZEXEL
China
Nissan-Diesel
Dpico
Nissan-Diesel
101601-9970
9 400 614 698
1670095069
INJECTION-PUMP ASSEMBLY
NE6
NE6