Information injection-pump assembly
BOSCH
9 400 610 293
9400610293
ZEXEL
101601-9922
1016019922
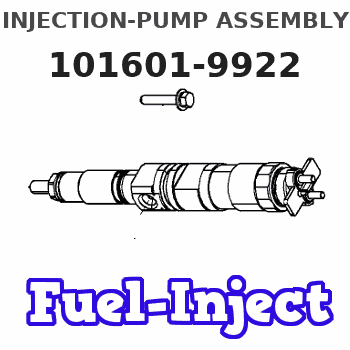
Rating:
Service parts 101601-9922 INJECTION-PUMP ASSEMBLY:
1.
_
6.
COUPLING PLATE
7.
COUPLING PLATE
8.
_
9.
_
11.
Nozzle and Holder
12.
Open Pre:MPa(Kqf/cm2)
21.6{220}
15.
NOZZLE SET
Cross reference number
BOSCH
9 400 610 293
9400610293
ZEXEL
101601-9922
1016019922
Zexel num
Bosch num
Firm num
Name
Calibration Data:
Adjustment conditions
Test oil
1404 Test oil ISO4113 or {SAEJ967d}
1404 Test oil ISO4113 or {SAEJ967d}
Test oil temperature
degC
40
40
45
Nozzle and nozzle holder
105780-8140
Bosch type code
EF8511/9A
Nozzle
105780-0000
Bosch type code
DN12SD12T
Nozzle holder
105780-2080
Bosch type code
EF8511/9
Opening pressure
MPa
17.2
Opening pressure
kgf/cm2
175
Injection pipe
Outer diameter - inner diameter - length (mm) mm 6-2-600
Outer diameter - inner diameter - length (mm) mm 6-2-600
Overflow valve
131424-1520
Overflow valve opening pressure
kPa
157
123
191
Overflow valve opening pressure
kgf/cm2
1.6
1.25
1.95
Tester oil delivery pressure
kPa
157
157
157
Tester oil delivery pressure
kgf/cm2
1.6
1.6
1.6
Direction of rotation (viewed from drive side)
Left L
Left L
Injection timing adjustment
Direction of rotation (viewed from drive side)
Left L
Left L
Injection order
1-5-3-6-
2-4
Pre-stroke
mm
3.3
3.25
3.35
Beginning of injection position
Drive side NO.1
Drive side NO.1
Difference between angles 1
Cal 1-5 deg. 60 59.5 60.5
Cal 1-5 deg. 60 59.5 60.5
Difference between angles 2
Cal 1-3 deg. 120 119.5 120.5
Cal 1-3 deg. 120 119.5 120.5
Difference between angles 3
Cal 1-6 deg. 180 179.5 180.5
Cal 1-6 deg. 180 179.5 180.5
Difference between angles 4
Cyl.1-2 deg. 240 239.5 240.5
Cyl.1-2 deg. 240 239.5 240.5
Difference between angles 5
Cal 1-4 deg. 300 299.5 300.5
Cal 1-4 deg. 300 299.5 300.5
Injection quantity adjustment
Adjusting point
A
Rack position
11.9
Pump speed
r/min
1450
1450
1450
Average injection quantity
mm3/st.
73.5
71.5
75.5
Max. variation between cylinders
%
0
-3
3
Basic
*
Fixing the lever
*
Injection quantity adjustment_02
Adjusting point
C
Rack position
9.9+-0.5
Pump speed
r/min
250
250
250
Average injection quantity
mm3/st.
10.5
9
12
Max. variation between cylinders
%
0
-15
15
Fixing the rack
*
Injection quantity adjustment_03
Adjusting point
D
Rack position
-
Pump speed
r/min
100
100
100
Average injection quantity
mm3/st.
74.5
74.5
Fixing the lever
*
Remarks
After startup boost setting
After startup boost setting
Timer adjustment
Pump speed
r/min
550--
Advance angle
deg.
0
0
0
Remarks
Start
Start
Timer adjustment_02
Pump speed
r/min
500
Advance angle
deg.
0.5
Timer adjustment_03
Pump speed
r/min
1000
Advance angle
deg.
3.2
2.7
3.7
Timer adjustment_04
Pump speed
r/min
1500
Advance angle
deg.
6.5
6
7
Remarks
Finish
Finish
Test data Ex:
Governor adjustment
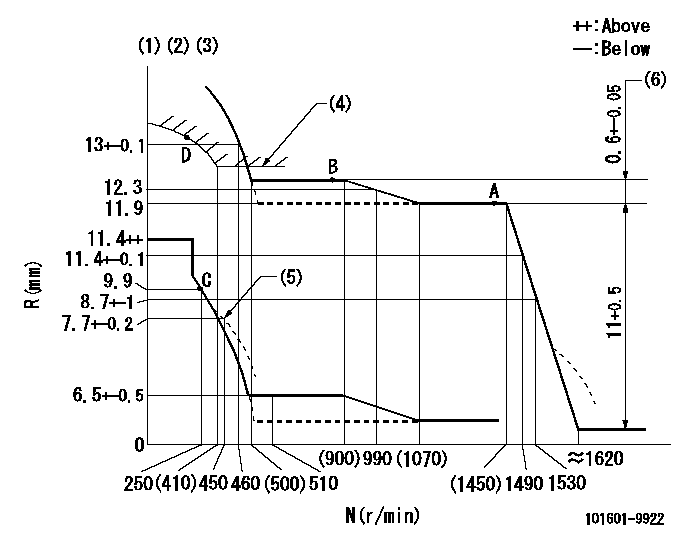
N:Pump speed
R:Rack position (mm)
(1)Lever ratio: RT
(2)Target shim dimension: TH
(3)Tolerance for racks not indicated: +-0.05mm.
(4)Excess fuel setting for starting: SXL (N = N1)
(5)Damper spring setting
(6)Rack difference between N = N2 and N = N3
----------
RT=1 TH=2.4mm SXL=12.6+0.2mm N1=450r/min N2=1450r/min N3=900r/min
----------
----------
RT=1 TH=2.4mm SXL=12.6+0.2mm N1=450r/min N2=1450r/min N3=900r/min
----------
Speed control lever angle

F:Full speed
----------
----------
a=10deg+-5deg
----------
----------
a=10deg+-5deg
0000000901

F:Full load
I:Idle
(1)Use the hole at R = aa
(2)Stopper bolt setting
----------
aa=55mm
----------
a=5.5deg+-5deg b=22deg+-3deg
----------
aa=55mm
----------
a=5.5deg+-5deg b=22deg+-3deg
Stop lever angle
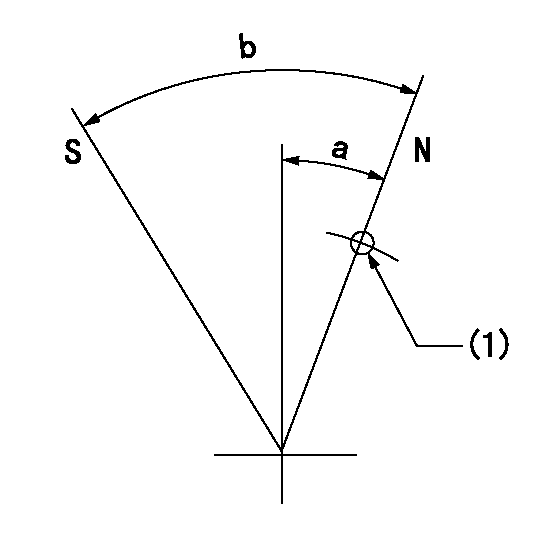
N:Pump normal
S:Stop the pump.
(1)Use the pin at R = aa
----------
aa=30mm
----------
a=35deg+-5deg b=71deg+-5deg
----------
aa=30mm
----------
a=35deg+-5deg b=71deg+-5deg
Timing setting

(1)Pump vertical direction
(2)Coupling's key groove position for the No. 6 cylinder's beginning of injection
(3)-
(4)-
----------
----------
a=(30deg)
----------
----------
a=(30deg)
Information:
TECHNICAL INFORMATION BULLETIN June 16, 2004
Truck Engines
C7 (KAL)
C9 (9DG)
C-9 (MTB)
Component Code: 1290SUBJECT: Injector Misfire due to Low/No Fuel Condition
PROBLEM:
Analysis of injectors returned from the field indicates that running the engine out of fuel, excessive air in the fuel, or high fuel inlet restriction may cause an internal injector failure. Multiple injectors failing the Cylinder Cutout Test in Caterpillar Electronic Technician (Cat ET) may indicate this mode of failure. If this occurs, debris from the internal injector failure may collect in the fuel return pressure regulator or fuel return screen (if equipped). See Figure 1.
SOLUTION:
If the Cylinder Cutout Test in Cat ET indicates that multiple injectors have failed, or if the engine has a recent history of injector failures, the fuel return pressure regulator and the fuel return screen need to be inspected for debris. See Figure 1.
Clean the fuel return screen (if equipped). If the engine is equipped with a fuel regulator that has a 90-degree elbow on the cylinder head, then there is a screen inside of the elbow. Remove the 90-degree elbow from the cylinder head and pressure regulator assembly. See Figure 1. Reverse flush any debris out of the elbow screen. If all of the debris cannot be removed from the elbow screen, then replace the 196-6838 90-degree elbow.
Clean/Replace the fuel return pressure regulator assembly as required. If the engine is equipped with a 90-degree elbow screen (see Step 2), the debris should have been caught by the screen. Only replace the 229-8870 pressure regulator if debris is visible on the inlet side of the pressure regulator. Replace failed injectors as indicated by the Cat ET Cylinder Cutout Test.
If the engine did not run out of fuel, make sure that the fuel inlet restriction measured at the fuel transfer pump inlet is within specification (max inlet restriction 4.1 in Hg or 14 kPa). Also, make sure that there is not excessive air in the fuel system by using a sight gauge on the fuel inlet and fuel outlet of the cylinder head. Make sure the fuel tank vent or cap is venting properly.
Note: There have been documented cases of pinched/restricted Original Equipment Manufacturer (OEM) fuel lines and air entry on OEM primary fuel filters.
If the fuel return pressure regulator or the elbow are replaced, return them to the Caterpillar claims room at the address below.
Caterpillar Service Claims Room 8201 N. University Peoria, IL 61615 USA Attn: Geoff Monari / Anant Kasture
Please share this information with your TEPS dealers.
Figure 1
COPYRIGHT 2004 CATERPILLAR
ALL RIGHTS RESERVED