Information injection-pump assembly
ZEXEL
101601-8530
1016018530
ISUZU
1156016911
1156016911
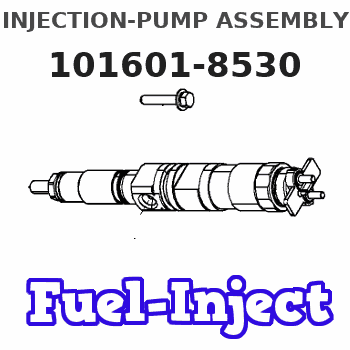
Rating:
Cross reference number
ZEXEL
101601-8530
1016018530
ISUZU
1156016911
1156016911
Zexel num
Bosch num
Firm num
Name
Calibration Data:
Adjustment conditions
Test oil
1404 Test oil ISO4113 or {SAEJ967d}
1404 Test oil ISO4113 or {SAEJ967d}
Test oil temperature
degC
40
40
45
Nozzle and nozzle holder
105780-8140
Bosch type code
EF8511/9A
Nozzle
105780-0000
Bosch type code
DN12SD12T
Nozzle holder
105780-2080
Bosch type code
EF8511/9
Opening pressure
MPa
17.2
Opening pressure
kgf/cm2
175
Injection pipe
Outer diameter - inner diameter - length (mm) mm 6-2-600
Outer diameter - inner diameter - length (mm) mm 6-2-600
Overflow valve
132424-0620
Overflow valve opening pressure
kPa
157
123
191
Overflow valve opening pressure
kgf/cm2
1.6
1.25
1.95
Tester oil delivery pressure
kPa
157
157
157
Tester oil delivery pressure
kgf/cm2
1.6
1.6
1.6
Direction of rotation (viewed from drive side)
Right R
Right R
Injection timing adjustment
Direction of rotation (viewed from drive side)
Right R
Right R
Injection order
1-5-3-6-
2-4
Pre-stroke
mm
3.6
3.55
3.65
Beginning of injection position
Drive side NO.1
Drive side NO.1
Difference between angles 1
Cal 1-5 deg. 60 59.5 60.5
Cal 1-5 deg. 60 59.5 60.5
Difference between angles 2
Cal 1-3 deg. 120 119.5 120.5
Cal 1-3 deg. 120 119.5 120.5
Difference between angles 3
Cal 1-6 deg. 180 179.5 180.5
Cal 1-6 deg. 180 179.5 180.5
Difference between angles 4
Cyl.1-2 deg. 240 239.5 240.5
Cyl.1-2 deg. 240 239.5 240.5
Difference between angles 5
Cal 1-4 deg. 300 299.5 300.5
Cal 1-4 deg. 300 299.5 300.5
Injection quantity adjustment
Adjusting point
-
Rack position
12.7
Pump speed
r/min
1000
1000
1000
Average injection quantity
mm3/st.
78
76.4
79.6
Max. variation between cylinders
%
0
-2.5
2.5
Basic
*
Fixing the rack
*
Standard for adjustment of the maximum variation between cylinders
*
Injection quantity adjustment_02
Adjusting point
H
Rack position
9.5+-0.5
Pump speed
r/min
260
260
260
Average injection quantity
mm3/st.
8.1
6.8
9.4
Max. variation between cylinders
%
0
-14
14
Fixing the rack
*
Standard for adjustment of the maximum variation between cylinders
*
Injection quantity adjustment_03
Adjusting point
A
Rack position
R1(12.7)
Pump speed
r/min
1000
1000
1000
Average injection quantity
mm3/st.
78
77
79
Basic
*
Fixing the lever
*
Injection quantity adjustment_04
Adjusting point
I
Rack position
15+-0.5
Pump speed
r/min
150
150
150
Average injection quantity
mm3/st.
92
92
100
Fixing the lever
*
Rack limit
*
Test data Ex:
Governor adjustment
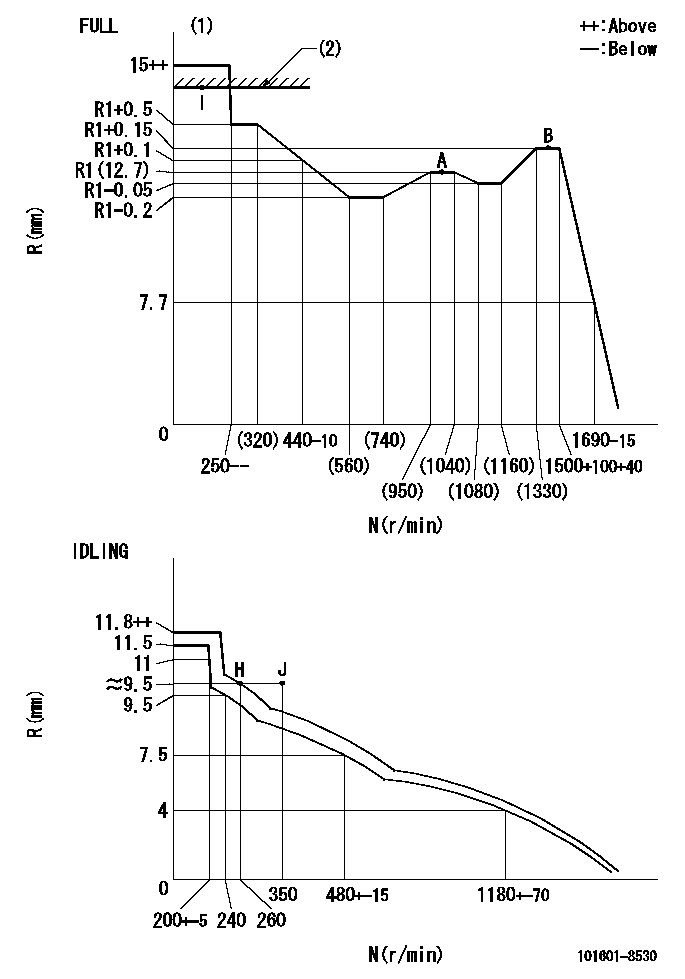
N:Pump speed
R:Rack position (mm)
(1)Torque cam stamping: T1
(2)RACK LIMIT
----------
T1=78
----------
----------
T1=78
----------
Timer adjustment

(1)Adjusting range
(2)Step response time
(N): Speed of the pump
(L): Load
(theta) Advance angle
(Srd1) Step response time 1
(Srd2) Step response time 2
1. Adjusting conditions for the variable timer
(1)Adjust the clearance between the pickup and the protrusion to L.
----------
L=1.5+-0.2mm N3=800r/min C3=(6.4deg) t1=2--sec. t2=2--sec.
----------
N1=1200++r/min N2=1500r/min P1=0kPa(0kgf/cm2) P2=392kPa(4kgf/cm2) C1=1.5--deg C2=6.4+-0.3deg R01=0/4load R02=4/4load
----------
L=1.5+-0.2mm N3=800r/min C3=(6.4deg) t1=2--sec. t2=2--sec.
----------
N1=1200++r/min N2=1500r/min P1=0kPa(0kgf/cm2) P2=392kPa(4kgf/cm2) C1=1.5--deg C2=6.4+-0.3deg R01=0/4load R02=4/4load
Speed control lever angle
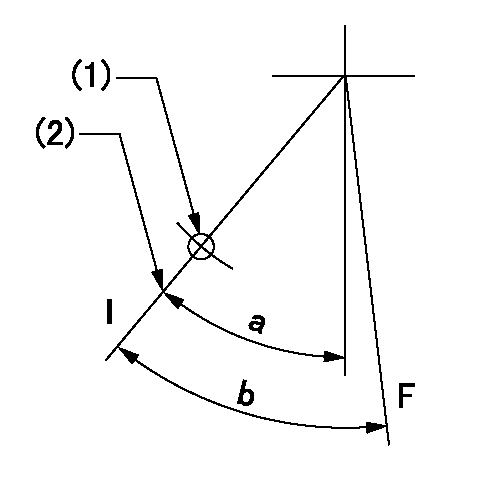
F:Full speed
I:Idle
(1)Use the hole at R = aa
(2)Stopper bolt setting
----------
aa=35mm
----------
a=42deg+-5deg b=(45deg)+-3deg
----------
aa=35mm
----------
a=42deg+-5deg b=(45deg)+-3deg
Stop lever angle

N:Pump normal
S:Stop the pump.
----------
----------
a=25deg+-5deg b=40deg+-5deg
----------
----------
a=25deg+-5deg b=40deg+-5deg
0000001501 RACK SENSOR
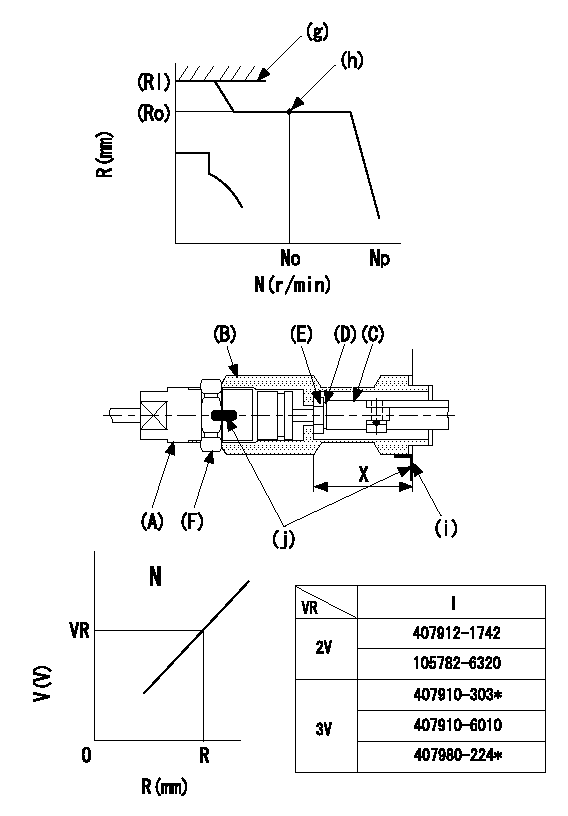
(g) rack limit
(h) Standard point
(i) pump end face
(j) Apply red paint.
Rack sensor adjustment (154610-0420)
1. Rack limit adjustment
(1)Fix the rack at the rack limit position Rl.
(2)Attach shim (D) [shim thickness standard (17.5 - R1] to rod (C) and tighten nut (E).
(3)Measure the distance X between the end face of the pump and the nut (E), and select a shim (D) so that X = 33-0.2mm.
(4)Release the rack, mount the joint (B) and fix.
(5)At this time, confirm that the shim (D) does not interfere with the joint (B).
2. Rack limit adjustment (amp-equipped type)
(1)Screw in the bobbin (A) until it contacts the joint (B).
(2)Fix the speed control lever at the full side and set the pump speed at No r/min.
(3)Adjust the depth that the bobbin (A) is screwed in so that the control unit's rack sensor output voltage is VR (V), then tighten the nut (F). (If equipped with a boost compensator, perform with boost pressure applied.)
(4)Apply red paint to both the joint (B) and the nut (F) join, and the joint (B) and the pump join.
----------
N=- R=R1(12.7)mm VR=2+-0.01V
----------
----------
N=- R=R1(12.7)mm VR=2+-0.01V
----------
Timing setting
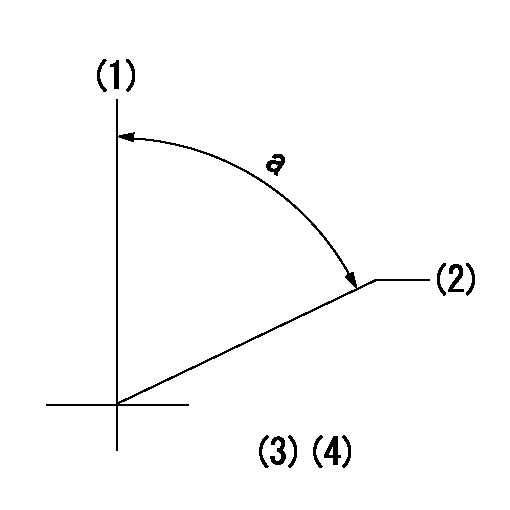
(1)Pump vertical direction
(2)Positions of coupling's threaded installation holes at No 1 cylinder's beginning of injection
(3)-
(4)-
----------
----------
a=(60deg)
----------
----------
a=(60deg)
Information:
1. Loosen two bolts (2) and two nuts (3). Remove bolt (1), and remove fan drive belts (4).2. Remove the nuts and bolts that hold the fan drive in place. Remove fan drive (5). The following steps are for installation of the fan drive.3. Put fan drive (5) in position on the timing gear cover.4. Install bolts (2) and nuts (3) loosely. Make a replacement of the belts as a set only.5. Install fan belts (4). Install bolt (1). Make an adjustment to the belt tension with tool (A). Measure the belt farthest away from the engine. Tighten new belts to a gauge indication of 120 5. After the engine is operated at high idle for a minimum of 30 minutes, make another adjustment to the belt tension. The correct tension for used belts is a gauge indication of 90 10.6. Tighten bolts (2) and nuts (3) that hold the fan drive in place.Disassemble Fan Drive
Start By:a. remove fan drive This is a typical later model fan drive. 1. Remove two bolts (2) that hold the fan adapter to the pulley.2. Remove fan adapter (1) from the pulley 3. Remove bolts (3) and washer (4). Remove seal (5). 4. Remove pulley (8) from bracket (6).5. Remove bearing (10) and spacer (9) from the pulley. Remove spacer (7), seal (11) and bearing (12) from the pulley.Assemble Fan Drive
1. Install bearing (12) in the rear of pulley (8). 2. Install lip-type seal (11) with tooling (A). The lip of the seal must be away from the bearing. Put 5P960 Multipurpose Grease on the lip of the seal.3. Install spacer (7) so the end with the taper is toward the inside of pulley (8).4. Install spacer (9) and bearing (4) in the front of the pulley. 5. Put seal (5) on the front of the pulley. Install the pulley on bracket (6). 6. Install washer (4) and bolts (3) that hold the pulley in position.7. Install the fan drive adapter on the pulley.8. Fill the fan drive with 5P960 Multipurpose Grease.End By:a. install fan drive
Start By:a. remove fan drive This is a typical later model fan drive. 1. Remove two bolts (2) that hold the fan adapter to the pulley.2. Remove fan adapter (1) from the pulley 3. Remove bolts (3) and washer (4). Remove seal (5). 4. Remove pulley (8) from bracket (6).5. Remove bearing (10) and spacer (9) from the pulley. Remove spacer (7), seal (11) and bearing (12) from the pulley.Assemble Fan Drive
1. Install bearing (12) in the rear of pulley (8). 2. Install lip-type seal (11) with tooling (A). The lip of the seal must be away from the bearing. Put 5P960 Multipurpose Grease on the lip of the seal.3. Install spacer (7) so the end with the taper is toward the inside of pulley (8).4. Install spacer (9) and bearing (4) in the front of the pulley. 5. Put seal (5) on the front of the pulley. Install the pulley on bracket (6). 6. Install washer (4) and bolts (3) that hold the pulley in position.7. Install the fan drive adapter on the pulley.8. Fill the fan drive with 5P960 Multipurpose Grease.End By:a. install fan drive