Information injection-pump assembly
ZEXEL
101601-7792
1016017792
ISUZU
1156012821
1156012821
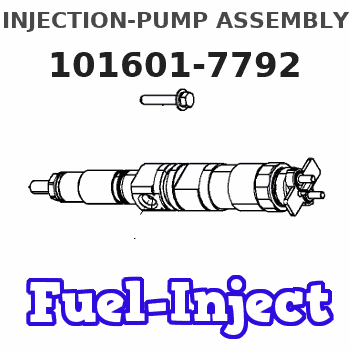
Rating:
Service parts 101601-7792 INJECTION-PUMP ASSEMBLY:
1.
_
3.
GOVERNOR
7.
COUPLING PLATE
8.
_
9.
_
11.
Nozzle and Holder
1-15300-104-2
12.
Open Pre:MPa(Kqf/cm2)
18.1{185}
15.
NOZZLE SET
Cross reference number
ZEXEL
101601-7792
1016017792
ISUZU
1156012821
1156012821
Zexel num
Bosch num
Firm num
Name
Calibration Data:
Adjustment conditions
Test oil
1404 Test oil ISO4113 or {SAEJ967d}
1404 Test oil ISO4113 or {SAEJ967d}
Test oil temperature
degC
40
40
45
Nozzle and nozzle holder
105780-8140
Bosch type code
EF8511/9A
Nozzle
105780-0000
Bosch type code
DN12SD12T
Nozzle holder
105780-2080
Bosch type code
EF8511/9
Opening pressure
MPa
17.2
Opening pressure
kgf/cm2
175
Injection pipe
Outer diameter - inner diameter - length (mm) mm 6-2-600
Outer diameter - inner diameter - length (mm) mm 6-2-600
Overflow valve
132424-0620
Overflow valve opening pressure
kPa
157
123
191
Overflow valve opening pressure
kgf/cm2
1.6
1.25
1.95
Tester oil delivery pressure
kPa
157
157
157
Tester oil delivery pressure
kgf/cm2
1.6
1.6
1.6
Direction of rotation (viewed from drive side)
Right R
Right R
Injection timing adjustment
Direction of rotation (viewed from drive side)
Right R
Right R
Injection order
1-5-3-6-
2-4
Pre-stroke
mm
3.6
3.55
3.65
Beginning of injection position
Drive side NO.1
Drive side NO.1
Difference between angles 1
Cal 1-5 deg. 60 59.5 60.5
Cal 1-5 deg. 60 59.5 60.5
Difference between angles 2
Cal 1-3 deg. 120 119.5 120.5
Cal 1-3 deg. 120 119.5 120.5
Difference between angles 3
Cal 1-6 deg. 180 179.5 180.5
Cal 1-6 deg. 180 179.5 180.5
Difference between angles 4
Cyl.1-2 deg. 240 239.5 240.5
Cyl.1-2 deg. 240 239.5 240.5
Difference between angles 5
Cal 1-4 deg. 300 299.5 300.5
Cal 1-4 deg. 300 299.5 300.5
Injection quantity adjustment
Adjusting point
-
Rack position
11.4
Pump speed
r/min
900
900
900
Average injection quantity
mm3/st.
70.7
69.2
72.2
Max. variation between cylinders
%
0
-2.5
2.5
Basic
*
Fixing the rack
*
Standard for adjustment of the maximum variation between cylinders
*
Injection quantity adjustment_02
Adjusting point
H
Rack position
9.6+-0.5
Pump speed
r/min
260
260
260
Average injection quantity
mm3/st.
9.4
8.1
10.7
Max. variation between cylinders
%
0
-14
14
Fixing the rack
*
Standard for adjustment of the maximum variation between cylinders
*
Remarks
Adjust only variation between cylinders; adjust governor according to governor specifications.
Adjust only variation between cylinders; adjust governor according to governor specifications.
Injection quantity adjustment_03
Adjusting point
A
Rack position
R1(11.4)
Pump speed
r/min
900
900
900
Average injection quantity
mm3/st.
70.7
69.7
71.7
Basic
*
Fixing the lever
*
Injection quantity adjustment_04
Adjusting point
B
Rack position
R1-0.1
Pump speed
r/min
1500
1500
1500
Average injection quantity
mm3/st.
81
77.8
84.2
Fixing the lever
*
Injection quantity adjustment_05
Adjusting point
I
Rack position
-
Pump speed
r/min
150
150
150
Average injection quantity
mm3/st.
86
86
96
Fixing the lever
*
Rack limit
*
Timer adjustment
Pump speed
r/min
1200--
Advance angle
deg.
0
0
0
Remarks
Start
Start
Timer adjustment_02
Pump speed
r/min
1150
Advance angle
deg.
0.5
Timer adjustment_03
Pump speed
r/min
1300
Advance angle
deg.
2
1.5
2.5
Timer adjustment_04
Pump speed
r/min
1500
Advance angle
deg.
5.5
5
6
Remarks
Finish
Finish
Test data Ex:
Governor adjustment
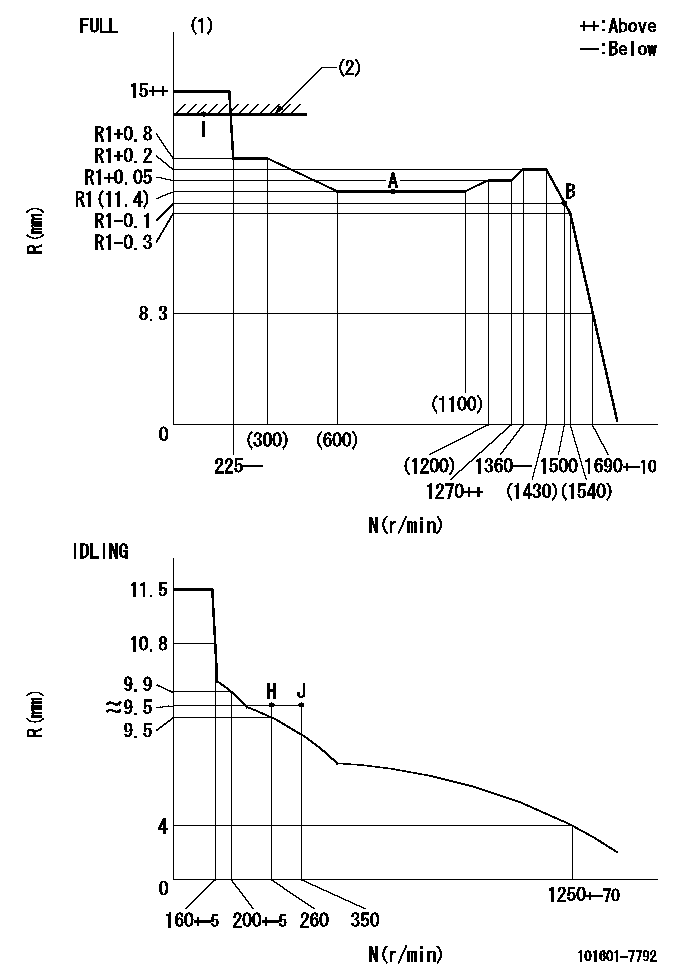
N:Pump speed
R:Rack position (mm)
(1)Torque cam stamping: T1
(2)RACK LIMIT
----------
T1=A38
----------
----------
T1=A38
----------
Speed control lever angle
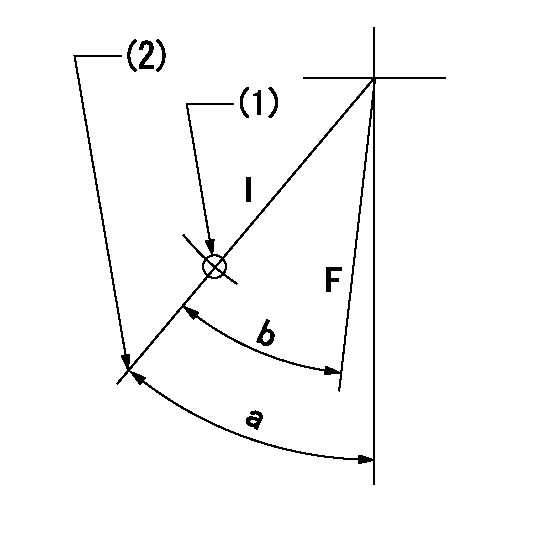
F:Full speed
I:Idle
(1)Use the hole at R = aa
(2)Stopper bolt setting
----------
aa=35mm
----------
a=42deg+-5deg b=35deg+-3deg
----------
aa=35mm
----------
a=42deg+-5deg b=35deg+-3deg
Stop lever angle

N:Pump normal
S:Stop the pump.
----------
----------
a=25deg+-5deg b=40deg+-5deg
----------
----------
a=25deg+-5deg b=40deg+-5deg
Timing setting
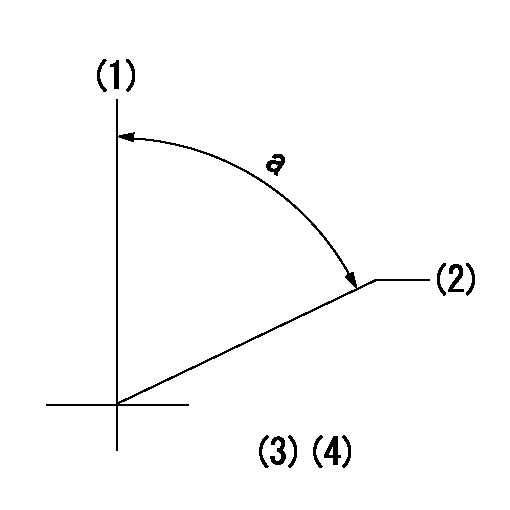
(1)Pump vertical direction
(2)Position of timer's threaded hole at No 1 cylinder's beginning of injection
(3)-
(4)-
----------
----------
a=(60deg)
----------
----------
a=(60deg)
Information:
17. Add coolant mixture if necessary to bring the coolant to within 13 mm (1/2 inch) below the bottom of the fill tube or the correct level on the sight glass, if equipped. Upon initial fill the sight gauge can indicate an incorrect coolant level. Be sure the coolant is to the bottom of the fill tube. Recheck the coolant level and fill the cooling system to the bottom of the fill tube if the system was low.
In cold weather, frequently check the specific gravity of the coolant solution to ensure adequate protection.If the engine is to be stored in, or shipped to an area with freezing temperatures, the cooling system must be either protected to the lowest expected outside temperature or drained completely to prevent damage. Always check your cooling system before operating your engine. Depending on load, failure to operate with thermostats could result in either an overheating or an excessive cooling condition.
18. Check the condition of the filler cap gasket (if equipped). If the gasket is damaged, discard the old filler cap and install a new filler cap. 19. Stop the engine and check the coolant to ensure it is at the proper level. Every 10,000 Hour Cleaning Procedure-Oil Cooler and Aftercooler Core
Caterpillar recommends that the oil cooler and aftercooler cores be removed, cleaned and pressure tested at Every 10,000 Hour overhaul time, or if a turbocharger failure has occurred, or if at any time the turbocharger develops an oil leak.1. Remove the core. Turn the core upside down to remove debris from the inlet.
Do not use caustic cleaners to clean the core. Caustic cleaners will attack the internal metals of the core and cause leakage.
2. Back flush internally with a solvent to loosen foreign substances and to remove oil. Caterpillar recommends the use of Caterpillar Hydrosolv 4165 or Hydrosolv 100 Liquid Cleaners. 3. Shake the core vigorously to eliminate any trapped debris. 4. Wash the core with hot, soapy water. Rinse thoroughly with clean water. 5. Dry the core with compressed air. Blow air in reverse direction of normal flow. Use all necessary safety equipment while using compressed air. 6. Inspect the system to ensure cleanliness and install the core. SR4 Generator
Make sure residual voltage in the rotor, stator and the generator is discharged.If this generator is to be connected to a utility electrical distribution system, it must be isolated from the distribution system by means of:a. Opening the main switch in the case of the generator temporarily connected to the system or,b. A double throw (transfer) switch in the case of a permanent connection to the system.Failure to do so could result in personal injury or death due to electrical shock. This warning does not apply when a generator and utility distribution system are designed and approved by the utility to run in parallel.
Before working inside the generator, make sure that the starting motor can not be activated by any automatic or manual signal.Electronic components in the regulator can be damaged during generator
In cold weather, frequently check the specific gravity of the coolant solution to ensure adequate protection.If the engine is to be stored in, or shipped to an area with freezing temperatures, the cooling system must be either protected to the lowest expected outside temperature or drained completely to prevent damage. Always check your cooling system before operating your engine. Depending on load, failure to operate with thermostats could result in either an overheating or an excessive cooling condition.
18. Check the condition of the filler cap gasket (if equipped). If the gasket is damaged, discard the old filler cap and install a new filler cap. 19. Stop the engine and check the coolant to ensure it is at the proper level. Every 10,000 Hour Cleaning Procedure-Oil Cooler and Aftercooler Core
Caterpillar recommends that the oil cooler and aftercooler cores be removed, cleaned and pressure tested at Every 10,000 Hour overhaul time, or if a turbocharger failure has occurred, or if at any time the turbocharger develops an oil leak.1. Remove the core. Turn the core upside down to remove debris from the inlet.
Do not use caustic cleaners to clean the core. Caustic cleaners will attack the internal metals of the core and cause leakage.
2. Back flush internally with a solvent to loosen foreign substances and to remove oil. Caterpillar recommends the use of Caterpillar Hydrosolv 4165 or Hydrosolv 100 Liquid Cleaners. 3. Shake the core vigorously to eliminate any trapped debris. 4. Wash the core with hot, soapy water. Rinse thoroughly with clean water. 5. Dry the core with compressed air. Blow air in reverse direction of normal flow. Use all necessary safety equipment while using compressed air. 6. Inspect the system to ensure cleanliness and install the core. SR4 Generator
Make sure residual voltage in the rotor, stator and the generator is discharged.If this generator is to be connected to a utility electrical distribution system, it must be isolated from the distribution system by means of:a. Opening the main switch in the case of the generator temporarily connected to the system or,b. A double throw (transfer) switch in the case of a permanent connection to the system.Failure to do so could result in personal injury or death due to electrical shock. This warning does not apply when a generator and utility distribution system are designed and approved by the utility to run in parallel.
Before working inside the generator, make sure that the starting motor can not be activated by any automatic or manual signal.Electronic components in the regulator can be damaged during generator