Information injection-pump assembly
ZEXEL
101601-5723
1016015723
HINO
220006982A
220006982a
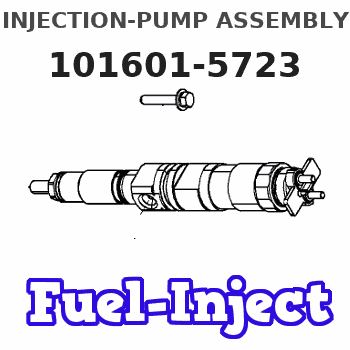
Rating:
Service parts 101601-5723 INJECTION-PUMP ASSEMBLY:
1.
_
7.
COUPLING PLATE
8.
_
9.
_
11.
Nozzle and Holder
23600-2133
12.
Open Pre:MPa(Kqf/cm2)
19.6{200}
15.
NOZZLE SET
Cross reference number
ZEXEL
101601-5723
1016015723
HINO
220006982A
220006982a
Zexel num
Bosch num
Firm num
Name
Calibration Data:
Adjustment conditions
Test oil
1404 Test oil ISO4113 or {SAEJ967d}
1404 Test oil ISO4113 or {SAEJ967d}
Test oil temperature
degC
40
40
45
Nozzle and nozzle holder
105780-8140
Bosch type code
EF8511/9A
Nozzle
105780-0000
Bosch type code
DN12SD12T
Nozzle holder
105780-2080
Bosch type code
EF8511/9
Opening pressure
MPa
17.2
Opening pressure
kgf/cm2
175
Injection pipe
Outer diameter - inner diameter - length (mm) mm 6-2-600
Outer diameter - inner diameter - length (mm) mm 6-2-600
Overflow valve
131424-8320
Overflow valve opening pressure
kPa
108
88
128
Overflow valve opening pressure
kgf/cm2
1.1
0.9
1.3
Tester oil delivery pressure
kPa
157
157
157
Tester oil delivery pressure
kgf/cm2
1.6
1.6
1.6
Direction of rotation (viewed from drive side)
Right R
Right R
Injection timing adjustment
Direction of rotation (viewed from drive side)
Right R
Right R
Injection order
1-4-2-6-
3-5
Pre-stroke
mm
3.8
3.77
3.83
Beginning of injection position
Drive side NO.1
Drive side NO.1
Difference between angles 1
Cal 1-4 deg. 60 59.75 60.25
Cal 1-4 deg. 60 59.75 60.25
Difference between angles 2
Cyl.1-2 deg. 120 119.75 120.25
Cyl.1-2 deg. 120 119.75 120.25
Difference between angles 3
Cal 1-6 deg. 180 179.75 180.25
Cal 1-6 deg. 180 179.75 180.25
Difference between angles 4
Cal 1-3 deg. 240 239.75 240.25
Cal 1-3 deg. 240 239.75 240.25
Difference between angles 5
Cal 1-5 deg. 300 299.75 300.25
Cal 1-5 deg. 300 299.75 300.25
Injection quantity adjustment
Adjusting point
-
Rack position
11.5
Pump speed
r/min
850
850
850
Average injection quantity
mm3/st.
76.1
74.5
77.7
Max. variation between cylinders
%
0
-3.5
3.5
Basic
*
Fixing the rack
*
Standard for adjustment of the maximum variation between cylinders
*
Injection quantity adjustment_02
Adjusting point
H
Rack position
9+-0.5
Pump speed
r/min
250
250
250
Each cylinder's injection qty
mm3/st.
15
14
16
Fixing the rack
*
Standard for adjustment of the maximum variation between cylinders
*
Injection quantity adjustment_03
Adjusting point
A
Rack position
R1(11.5)
Pump speed
r/min
850
850
850
Average injection quantity
mm3/st.
76.1
75.1
77.1
Basic
*
Fixing the lever
*
Injection quantity adjustment_04
Adjusting point
B
Rack position
R1+0.45
Pump speed
r/min
1450
1450
1450
Average injection quantity
mm3/st.
86.8
82.8
90.8
Fixing the lever
*
Injection quantity adjustment_05
Adjusting point
C
Rack position
R1-0.25
Pump speed
r/min
580
580
580
Average injection quantity
mm3/st.
62.8
58.8
66.8
Fixing the lever
*
Injection quantity adjustment_06
Adjusting point
D
Rack position
R1+0.45
Pump speed
r/min
1150
1150
1150
Average injection quantity
mm3/st.
85.4
81.4
89.4
Fixing the lever
*
Injection quantity adjustment_07
Adjusting point
I
Rack position
-
Pump speed
r/min
100
100
100
Average injection quantity
mm3/st.
140
140
150
Fixing the lever
*
Rack limit
*
Timer adjustment
Pump speed
r/min
925--
Advance angle
deg.
0
0
0
Load
1/4
Remarks
Start
Start
Timer adjustment_02
Pump speed
r/min
875
Advance angle
deg.
0.3
Load
1/4
Timer adjustment_03
Pump speed
r/min
(920--)
Advance angle
deg.
1
0.7
1.3
Load
4/4
Timer adjustment_04
Pump speed
r/min
1175+50
Advance angle
deg.
1
0.7
1.3
Load
3/4
Timer adjustment_05
Pump speed
r/min
1400+50
Advance angle
deg.
5.5
5.2
5.8
Load
4/4
Remarks
Finish
Finish
Test data Ex:
Governor adjustment
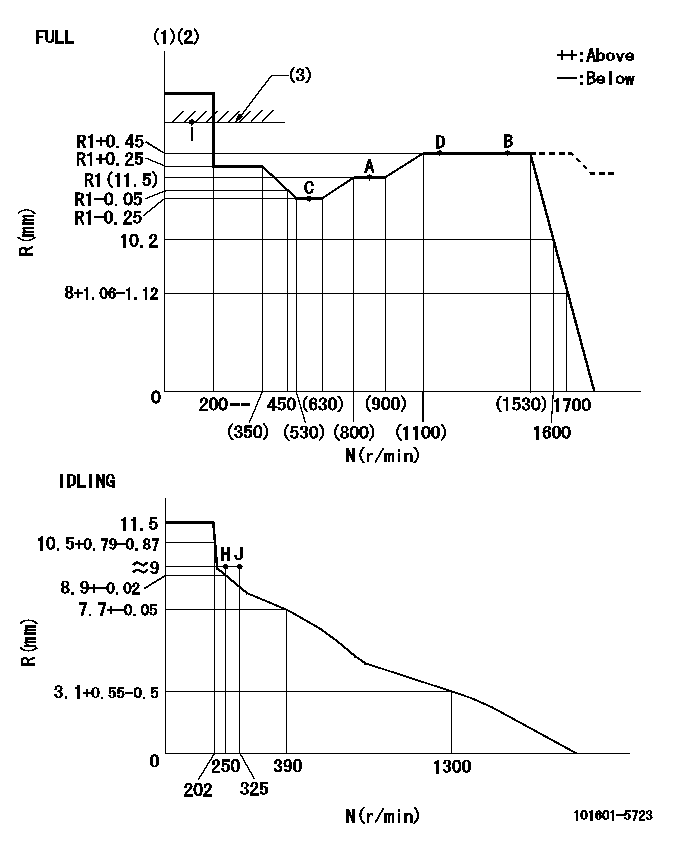
N:Pump speed
R:Rack position (mm)
(1)Torque cam stamping: T1
(2)Tolerance for racks not indicated: +-0.05mm.
(3)RACK LIMIT
----------
T1=H16
----------
----------
T1=H16
----------
Speed control lever angle
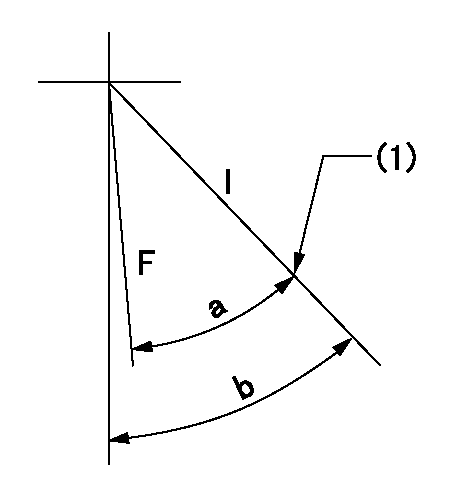
F:Full speed
I:Idle
(1)Stopper bolt set position 'H'
----------
----------
a=(40deg)+-3deg b=44deg+-5deg
----------
----------
a=(40deg)+-3deg b=44deg+-5deg
Stop lever angle
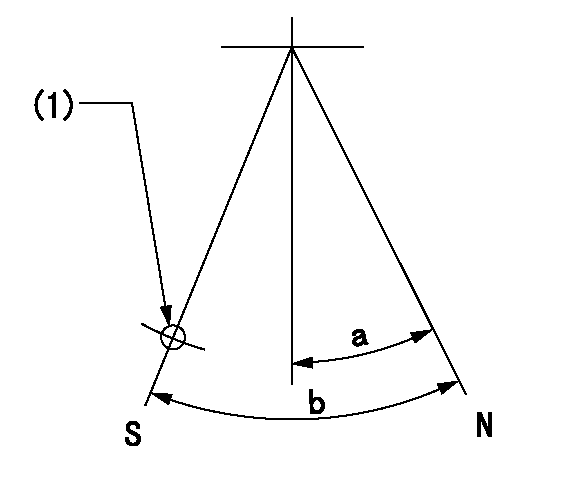
N:Pump normal
S:Stop the pump.
(1)Use the hole at R = aa
----------
aa=35mm
----------
a=14.5deg+-5deg b=40deg+-5deg
----------
aa=35mm
----------
a=14.5deg+-5deg b=40deg+-5deg
Timing setting
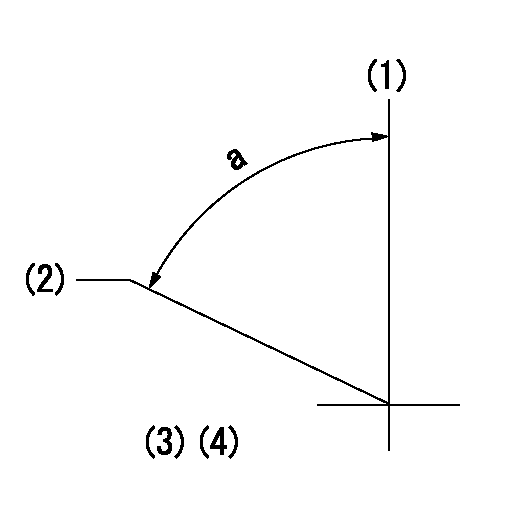
(1)Pump vertical direction
(2)Coupling's key groove position at No 1 cylinder's beginning of injection
(3)-
(4)-
----------
----------
a=(50deg)
----------
----------
a=(50deg)
Information:
The engine is turbocharged and air-to-air aftercooled (ATAAC) with direct fuel injection.The 3176 is an electronically controlled, mechanically actuated unit injector diesel engine. Timing advance is achieved by precise control of injector firing. Engine speed is controlled by adjusting the firing duration. A pulse wheel provides information to the fuel cooled ECM (Electronic Control Module) for detection of cylinder position and engine speed.The 3176 electronic engine control system was designed to provide electronic governing, automatic air fuel ratio control, torque rise shaping, injection timing control and system diagnostics. Additional benefits such as cruise control, vehicle speed limiting, low and high gears engine speed limiting (progressive shift engine speed control), PTO governor, data link and multi-torque ratings provide for additional engine fuel economy, driver comfort and serviceability.The fuel system is a mechanically actuated, electronically controlled unit injector combining the pumping, electronic fuel metering and injecting elements in a single unit to produce higher injection pressures (22,000 psi [151 600 kPa]). High injection pressures help to reduce fuel consumption and particulate emissions.The use of this type of unit injector provides total electronic control of injection timing. The injection timing is varied as a function of engine operating conditions. This optimizes the engine's performance for starting, emissions, noise, fuel consumption and driveability.A full range electronic governor is utilized and controls the fuel injection output to maintain the engine speed desired by the 3176 system. The governor functions like the Caterpillar mechanical governor in the mid-range, but includes additional features. These include programmable isochronous low idle and 20 rpm governor overrun.The 3176 has built-in diagnostics to assure that all components are functioning and operating properly. In the event of a system component deviation from programmed limits, the operator will be alerted to the condition by a dashboard mounted "Check Engine" light.A Caterpillar service tool may be used to read the numerical code of the faulty component. Intermittent faults are logged and stored in the system memory. Refer to Engine Diagnostics section of this publication for alternative methods.The cooling system consists of a gear driven pump, with one thermostat which regulates the engine coolant temperature, a plate type oil cooler and a radiator incorporating a shunt system.The 3176 does not have a cylinder block water cooling system. Instead, the cast water manifold in the spacer deck distributes 65% of the coolant volume to each of the cylinder liners and the remaining 35% flows directly to the cylinder head.The engine lubricating oil, which is both cooled and filtered, is supplied by a gear-type pump. Bypass valves provide unrestricted flow of lubrication oil to the engine parts when oil viscosity is high, or if either the oil cooler or the oil filter elements (paper cartridge) should become plugged.Multi-Torque Rating (if equipped)
This feature provides higher torque levels and better fuel economy while in top gear only. The 3176 electronics are able to determine when the vehicle is in top gear by calculating the engine rpm/vehicle speed ratio. A ratio of less than 26.6 will provide higher
This feature provides higher torque levels and better fuel economy while in top gear only. The 3176 electronics are able to determine when the vehicle is in top gear by calculating the engine rpm/vehicle speed ratio. A ratio of less than 26.6 will provide higher