Information injection-pump assembly
BOSCH
F 019 Z10 347
f019z10347
ZEXEL
101601-5702
1016015702
HINO
220006742A
220006742a
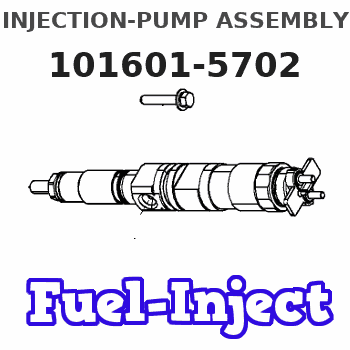
Rating:
Service parts 101601-5702 INJECTION-PUMP ASSEMBLY:
1.
_
7.
COUPLING PLATE
8.
_
9.
_
11.
Nozzle and Holder
23600-2133
12.
Open Pre:MPa(Kqf/cm2)
19.6{200}
15.
NOZZLE SET
Cross reference number
BOSCH
F 019 Z10 347
f019z10347
ZEXEL
101601-5702
1016015702
HINO
220006742A
220006742a
Zexel num
Bosch num
Firm num
Name
Calibration Data:
Adjustment conditions
Test oil
1404 Test oil ISO4113 or {SAEJ967d}
1404 Test oil ISO4113 or {SAEJ967d}
Test oil temperature
degC
40
40
45
Nozzle and nozzle holder
105780-8210
Nozzle
105780-0070
Nozzle holder
105780-2080
Bosch type code
EF8511/9
Opening pressure
MPa
17.2
Opening pressure
kgf/cm2
175
Injection pipe
Outer diameter - inner diameter - length (mm) mm 6-2-600
Outer diameter - inner diameter - length (mm) mm 6-2-600
Overflow valve
134424-0920
Overflow valve opening pressure
kPa
162
147
177
Overflow valve opening pressure
kgf/cm2
1.65
1.5
1.8
Tester oil delivery pressure
kPa
157
157
157
Tester oil delivery pressure
kgf/cm2
1.6
1.6
1.6
Direction of rotation (viewed from drive side)
Right R
Right R
Injection timing adjustment
Direction of rotation (viewed from drive side)
Right R
Right R
Injection order
1-4-2-6-
3-5
Pre-stroke
mm
3.8
3.77
3.83
Beginning of injection position
Drive side NO.1
Drive side NO.1
Difference between angles 1
Cal 1-4 deg. 60 59.75 60.25
Cal 1-4 deg. 60 59.75 60.25
Difference between angles 2
Cyl.1-2 deg. 120 119.75 120.25
Cyl.1-2 deg. 120 119.75 120.25
Difference between angles 3
Cal 1-6 deg. 180 179.75 180.25
Cal 1-6 deg. 180 179.75 180.25
Difference between angles 4
Cal 1-3 deg. 240 239.75 240.25
Cal 1-3 deg. 240 239.75 240.25
Difference between angles 5
Cal 1-5 deg. 300 299.75 300.25
Cal 1-5 deg. 300 299.75 300.25
Injection quantity adjustment
Adjusting point
-
Rack position
11.5
Pump speed
r/min
850
850
850
Average injection quantity
mm3/st.
77.6
76
79.2
Max. variation between cylinders
%
0
-3.5
3.5
Basic
*
Fixing the rack
*
Standard for adjustment of the maximum variation between cylinders
*
Injection quantity adjustment_02
Adjusting point
H
Rack position
9+-0.5
Pump speed
r/min
250
250
250
Each cylinder's injection qty
mm3/st.
16.9
15.9
17.9
Fixing the rack
*
Standard for adjustment of the maximum variation between cylinders
*
Injection quantity adjustment_03
Adjusting point
A
Rack position
R1(11.5)
Pump speed
r/min
850
850
850
Average injection quantity
mm3/st.
77.6
76.6
78.6
Basic
*
Fixing the lever
*
Injection quantity adjustment_04
Adjusting point
B
Rack position
R1+0.5
Pump speed
r/min
1450
1450
1450
Average injection quantity
mm3/st.
88.9
84.9
92.9
Fixing the lever
*
Injection quantity adjustment_05
Adjusting point
C
Rack position
R1-0.3
Pump speed
r/min
600
600
600
Average injection quantity
mm3/st.
64.2
60.2
68.2
Fixing the lever
*
Injection quantity adjustment_06
Adjusting point
D
Rack position
R1+0.5
Pump speed
r/min
1150
1150
1150
Average injection quantity
mm3/st.
87.4
83.4
91.4
Fixing the lever
*
Injection quantity adjustment_07
Adjusting point
I
Rack position
-
Pump speed
r/min
100
100
100
Average injection quantity
mm3/st.
140
140
150
Fixing the lever
*
Rack limit
*
Timer adjustment
Pump speed
r/min
925--
Advance angle
deg.
0
0
0
Load
1/4
Remarks
Start
Start
Timer adjustment_02
Pump speed
r/min
875
Advance angle
deg.
0.3
Load
1/4
Timer adjustment_03
Pump speed
r/min
(920--)
Advance angle
deg.
1
0.7
1.3
Load
4/4
Remarks
Measure the actual speed.
Measure the actual speed.
Timer adjustment_04
Pump speed
r/min
1175+50
Advance angle
deg.
1
0.7
1.3
Load
3/4
Timer adjustment_05
Pump speed
r/min
1400+50
Advance angle
deg.
5.5
5.2
5.8
Load
4/4
Remarks
Finish
Finish
Test data Ex:
Governor adjustment
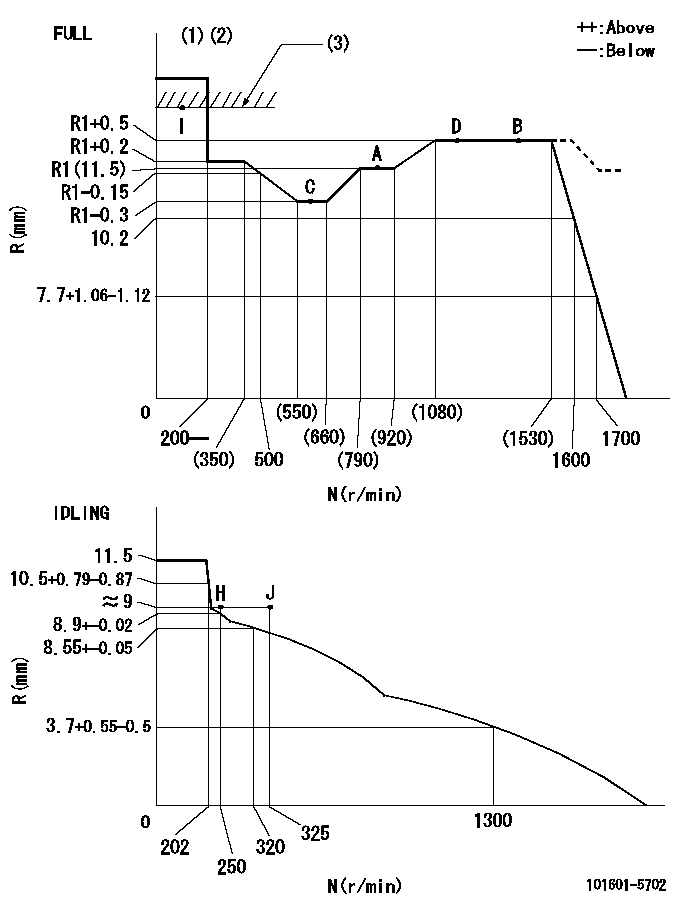
N:Pump speed
R:Rack position (mm)
(1)Torque cam stamping: T1
(2)Tolerance for racks not indicated: +-0.05mm.
(3)RACK LIMIT
----------
T1=F80
----------
----------
T1=F80
----------
Speed control lever angle
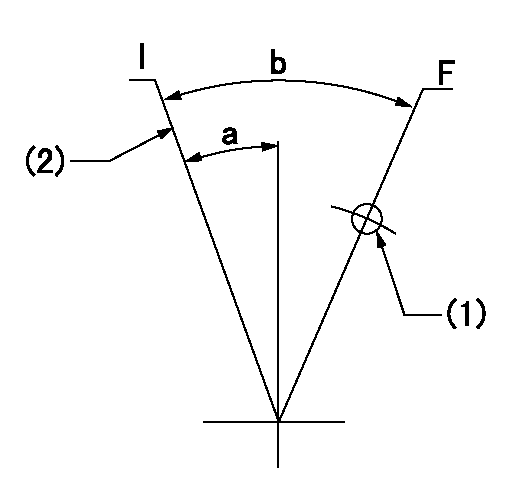
F:Full speed
I:Idle
(1)Use the hole at R = aa
(2)Stopper bolt set position 'H'
----------
aa=25.5mm
----------
a=20deg+-5deg b=37deg+-3deg
----------
aa=25.5mm
----------
a=20deg+-5deg b=37deg+-3deg
Stop lever angle

N:Pump normal
S:Stop the pump.
(1)Use the hole at R = aa
----------
aa=35mm
----------
a=14.5deg+-5deg b=40deg+-5deg
----------
aa=35mm
----------
a=14.5deg+-5deg b=40deg+-5deg
0000001501 AIR CYLINDER
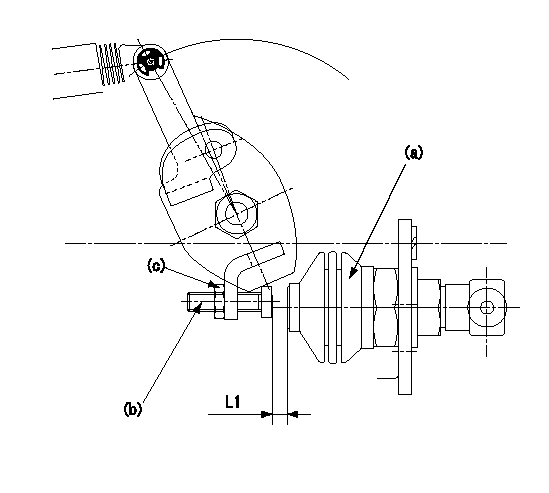
Adjustment of the air cylinder
1. Set the speed lever at the idling position.
2. Set the gap between the air cylinder (a) and the set bolt (b) to L1.
3. Set the speed at N1, apply positive pressure P1 to the air cylinder (a) and read the rack position.
4. Push set bolt (b) out and tighten nut (c) at N1 when the rack position is R1.
5. Apply positive pressure several times and confirm that the lever returns to the idle position at positive pressure P2.
6. Confirm that the rack position is R1 at positive pressure P1.
----------
L1=(8)mm R1=8.8+-0.1mm N1=475r/min P1=392+98kPa(4+1kgf/cm2) P2=0kPa(0kgf/cm2)
----------
----------
L1=(8)mm R1=8.8+-0.1mm N1=475r/min P1=392+98kPa(4+1kgf/cm2) P2=0kPa(0kgf/cm2)
----------
Timing setting
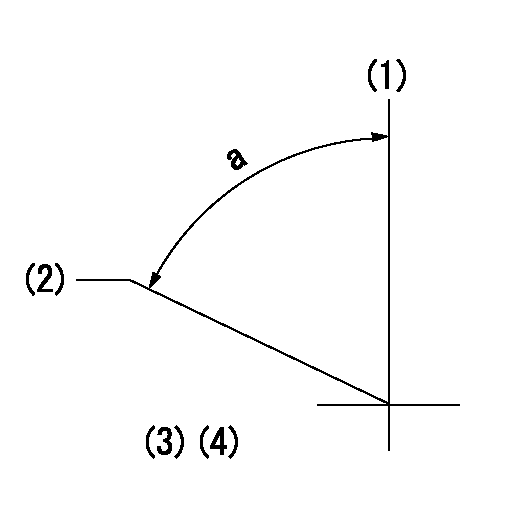
(1)Pump vertical direction
(2)Coupling's key groove position at No 1 cylinder's beginning of injection
(3)-
(4)-
----------
----------
a=(50deg)
----------
----------
a=(50deg)
Information:
To Remove Injection Nozzles
Special tooling is required. See the Service Manual for this engine or your Caterpillar dealer.Turbocharger, Jacket Water Pump and Raw Water Pump
Operation of the engine until the turbocharger fails, can cause severe damage to the turbocharger's compressor wheel and/or the engine. For example, damage to the turbocharger compressor wheel could cause parts from the compressor wheel to enter the engine cylinder and cause additional damage to the piston, valve and cylinder head.A failed water pump might cause severe engine overheating problems that could result in cracks in the cylinder head, a piston seizure or other potential damage to the engine.Inspect/Rebuild or Exchange Turbocharger
Turbocharger bearing failures can cause large quantities of oil to enter the air intake and exhaust systems. Loss of engine lubricant can result in serious engine damage.Minor leakage of a turbocharger housing under extended low idle operation will not cause problems as long as no turbocharger bearing failure occurred.When a turbocharger bearing failure is accompanied by a significant engine performance loss (exhaust smoke or engine speed up at no load), DO NOT continue engine operation until the turbocharger is repaired or replaced.
1. Remove the exhaust outlet piping and inlet piping from the turbocharger. Visually check for oil leaks.2. Turn the turbine and compressor wheel by hand.3. The assembly should turn freely.4. Inspect the turbine wheel and compressor wheel for contact with the turbocharger housing.5. There should NOT be any visible signs of contact between the turbine or compressor wheel and the turbocharger housing.Check the compressor wheel for cleanliness. If only the blade side of the wheel is dirty, dirt and/or moisture is passing through the air filtering system.If oil is found only on the back side of the wheel, it indicates a turbo oil seal leak. The leak may be the result of extended engine operation at low idle or an intake air line restriction (plugged filters).Maintain the compressor wheel/turbo housing by cleaning with standard shop solvents and a soft bristle brush.6. Check the end play and bearing clearance on the turbine wheel and shaft with a dial indicator. Attach the indicator and position the pointer on the end of turbocharger shaft. Push and pull on the other end of the shaft observing the dial indicator for total reading. End play should read between 0.076 to 0.203 mm (.003 to .008 inch). If indicator reading exceeds this tolerance, the turbocharger should be rebuilt or replaced. If indicator reading is less than 0.076 mm (.003 inch), it may be an indication of carbon build-up on the turbine wheel. The turbocharger should be disassembled, cleaned and inspected.If the measurements are not within specifications, the turbocharger must be repaired or replaced.7. When installing or replacing V-band clamps, position the gap (tightening screw) down if possible so any accumulation of moisture will drain away.Turbocharger components require precision clearances and balancing due to operation at high rotational (torsional) speeds. Severe Service Applications can accelerate component wear and may suggest the need to Inspect/Repair/Replace the cartridge at reduced intervals
Special tooling is required. See the Service Manual for this engine or your Caterpillar dealer.Turbocharger, Jacket Water Pump and Raw Water Pump
Operation of the engine until the turbocharger fails, can cause severe damage to the turbocharger's compressor wheel and/or the engine. For example, damage to the turbocharger compressor wheel could cause parts from the compressor wheel to enter the engine cylinder and cause additional damage to the piston, valve and cylinder head.A failed water pump might cause severe engine overheating problems that could result in cracks in the cylinder head, a piston seizure or other potential damage to the engine.Inspect/Rebuild or Exchange Turbocharger
Turbocharger bearing failures can cause large quantities of oil to enter the air intake and exhaust systems. Loss of engine lubricant can result in serious engine damage.Minor leakage of a turbocharger housing under extended low idle operation will not cause problems as long as no turbocharger bearing failure occurred.When a turbocharger bearing failure is accompanied by a significant engine performance loss (exhaust smoke or engine speed up at no load), DO NOT continue engine operation until the turbocharger is repaired or replaced.
1. Remove the exhaust outlet piping and inlet piping from the turbocharger. Visually check for oil leaks.2. Turn the turbine and compressor wheel by hand.3. The assembly should turn freely.4. Inspect the turbine wheel and compressor wheel for contact with the turbocharger housing.5. There should NOT be any visible signs of contact between the turbine or compressor wheel and the turbocharger housing.Check the compressor wheel for cleanliness. If only the blade side of the wheel is dirty, dirt and/or moisture is passing through the air filtering system.If oil is found only on the back side of the wheel, it indicates a turbo oil seal leak. The leak may be the result of extended engine operation at low idle or an intake air line restriction (plugged filters).Maintain the compressor wheel/turbo housing by cleaning with standard shop solvents and a soft bristle brush.6. Check the end play and bearing clearance on the turbine wheel and shaft with a dial indicator. Attach the indicator and position the pointer on the end of turbocharger shaft. Push and pull on the other end of the shaft observing the dial indicator for total reading. End play should read between 0.076 to 0.203 mm (.003 to .008 inch). If indicator reading exceeds this tolerance, the turbocharger should be rebuilt or replaced. If indicator reading is less than 0.076 mm (.003 inch), it may be an indication of carbon build-up on the turbine wheel. The turbocharger should be disassembled, cleaned and inspected.If the measurements are not within specifications, the turbocharger must be repaired or replaced.7. When installing or replacing V-band clamps, position the gap (tightening screw) down if possible so any accumulation of moisture will drain away.Turbocharger components require precision clearances and balancing due to operation at high rotational (torsional) speeds. Severe Service Applications can accelerate component wear and may suggest the need to Inspect/Repair/Replace the cartridge at reduced intervals