Information injection-pump assembly
BOSCH
F 019 Z10 341
f019z10341
ZEXEL
101601-5693
1016015693
HINO
220006542A
220006542a
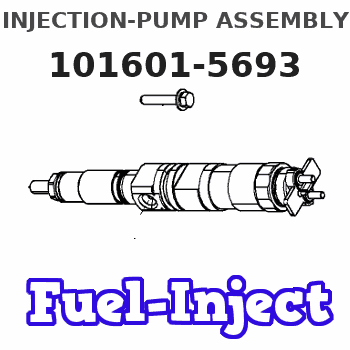
Rating:
Service parts 101601-5693 INJECTION-PUMP ASSEMBLY:
1.
_
7.
COUPLING PLATE
8.
_
9.
_
11.
Nozzle and Holder
23600-2133
12.
Open Pre:MPa(Kqf/cm2)
19.6{200}
15.
NOZZLE SET
Include in #1:
101601-5693
as INJECTION-PUMP ASSEMBLY
Include in #2:
104205-3030
as _
Cross reference number
BOSCH
F 019 Z10 341
f019z10341
ZEXEL
101601-5693
1016015693
HINO
220006542A
220006542a
Zexel num
Bosch num
Firm num
Name
Calibration Data:
Adjustment conditions
Test oil
1404 Test oil ISO4113 or {SAEJ967d}
1404 Test oil ISO4113 or {SAEJ967d}
Test oil temperature
degC
40
40
45
Nozzle and nozzle holder
105780-8210
Nozzle
105780-0070
Nozzle holder
105780-2080
Bosch type code
EF8511/9
Opening pressure
MPa
17.2
Opening pressure
kgf/cm2
175
Injection pipe
Outer diameter - inner diameter - length (mm) mm 6-2-600
Outer diameter - inner diameter - length (mm) mm 6-2-600
Overflow valve
134424-0920
Overflow valve opening pressure
kPa
162
147
177
Overflow valve opening pressure
kgf/cm2
1.65
1.5
1.8
Tester oil delivery pressure
kPa
157
157
157
Tester oil delivery pressure
kgf/cm2
1.6
1.6
1.6
Direction of rotation (viewed from drive side)
Right R
Right R
Injection timing adjustment
Direction of rotation (viewed from drive side)
Right R
Right R
Injection order
1-4-2-6-
3-5
Pre-stroke
mm
3.8
3.77
3.83
Beginning of injection position
Drive side NO.1
Drive side NO.1
Difference between angles 1
Cal 1-4 deg. 60 59.75 60.25
Cal 1-4 deg. 60 59.75 60.25
Difference between angles 2
Cyl.1-2 deg. 120 119.75 120.25
Cyl.1-2 deg. 120 119.75 120.25
Difference between angles 3
Cal 1-6 deg. 180 179.75 180.25
Cal 1-6 deg. 180 179.75 180.25
Difference between angles 4
Cal 1-3 deg. 240 239.75 240.25
Cal 1-3 deg. 240 239.75 240.25
Difference between angles 5
Cal 1-5 deg. 300 299.75 300.25
Cal 1-5 deg. 300 299.75 300.25
Injection quantity adjustment
Adjusting point
-
Rack position
11.5
Pump speed
r/min
850
850
850
Average injection quantity
mm3/st.
77.6
76
79.2
Max. variation between cylinders
%
0
-3.5
3.5
Basic
*
Fixing the rack
*
Standard for adjustment of the maximum variation between cylinders
*
Injection quantity adjustment_02
Adjusting point
H
Rack position
9+-0.5
Pump speed
r/min
250
250
250
Each cylinder's injection qty
mm3/st.
16.9
15.9
17.9
Fixing the rack
*
Standard for adjustment of the maximum variation between cylinders
*
Injection quantity adjustment_03
Adjusting point
A
Rack position
R1(11.5)
Pump speed
r/min
850
850
850
Average injection quantity
mm3/st.
77.6
76.6
78.6
Basic
*
Fixing the lever
*
Injection quantity adjustment_04
Adjusting point
B
Rack position
R1+0.5
Pump speed
r/min
1450
1450
1450
Average injection quantity
mm3/st.
88.9
84.9
92.9
Fixing the lever
*
Injection quantity adjustment_05
Adjusting point
C
Rack position
R1-0.3
Pump speed
r/min
600
600
600
Average injection quantity
mm3/st.
64.2
60.2
68.2
Fixing the lever
*
Injection quantity adjustment_06
Adjusting point
D
Rack position
R1+0.5
Pump speed
r/min
1150
1150
1150
Average injection quantity
mm3/st.
87.4
83.4
91.4
Fixing the lever
*
Injection quantity adjustment_07
Adjusting point
I
Rack position
-
Pump speed
r/min
100
100
100
Average injection quantity
mm3/st.
140
140
150
Fixing the lever
*
Rack limit
*
Timer adjustment
Pump speed
r/min
925--
Advance angle
deg.
0
0
0
Load
1/4
Remarks
Start
Start
Timer adjustment_02
Pump speed
r/min
875
Advance angle
deg.
0.3
Load
1/4
Timer adjustment_03
Pump speed
r/min
(920--)
Advance angle
deg.
1
0.7
1.3
Load
4/4
Remarks
Measure the actual speed.
Measure the actual speed.
Timer adjustment_04
Pump speed
r/min
1175+50
Advance angle
deg.
1
0.7
1.3
Load
3/4
Timer adjustment_05
Pump speed
r/min
1400+50
Advance angle
deg.
5.5
5.2
5.8
Load
4/4
Remarks
Finish
Finish
Test data Ex:
Governor adjustment
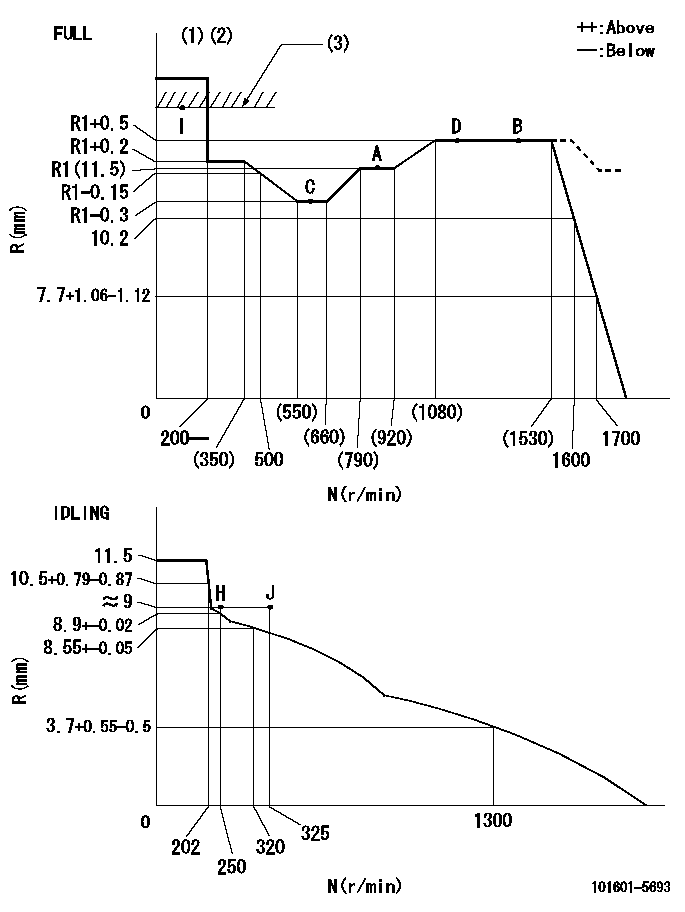
N:Pump speed
R:Rack position (mm)
(1)Torque cam stamping: T1
(2)Tolerance for racks not indicated: +-0.05mm.
(3)RACK LIMIT
----------
T1=F80
----------
----------
T1=F80
----------
Speed control lever angle
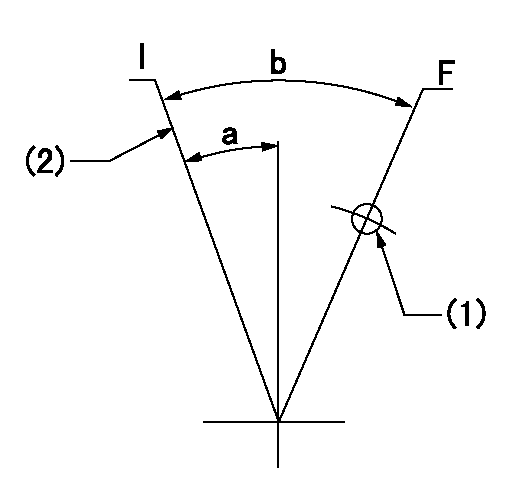
F:Full speed
I:Idle
(1)Use the hole at R = aa
(2)Stopper bolt set position 'H'
----------
aa=25.5mm
----------
a=20deg+-5deg b=37deg+-3deg
----------
aa=25.5mm
----------
a=20deg+-5deg b=37deg+-3deg
Stop lever angle

N:Pump normal
S:Stop the pump.
(1)Use the hole at R = aa
----------
aa=35mm
----------
a=14.5deg+-5deg b=40deg+-5deg
----------
aa=35mm
----------
a=14.5deg+-5deg b=40deg+-5deg
Timing setting
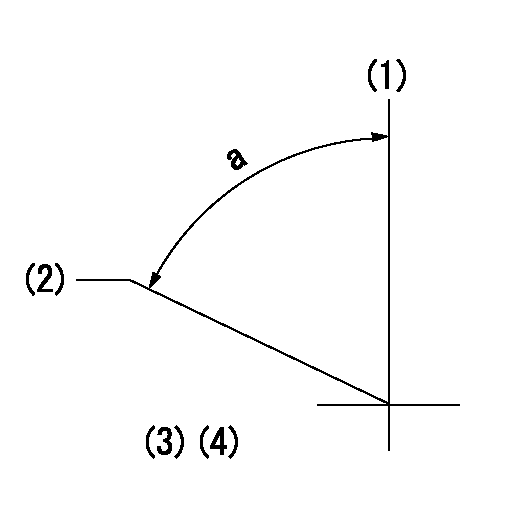
(1)Pump vertical direction
(2)Coupling's key groove position at No 1 cylinder's beginning of injection
(3)-
(4)-
----------
----------
a=(50deg)
----------
----------
a=(50deg)
Information:
USE FUEL CONSUMPTION, SERVICE HOURS OR TIME INTERVAL, WHICHEVER OCCURS FIRST.Daily
Walk-Around Inspection - Inspect engine for leaks and loose connections Engine Crankcase - Check oil level Cooling System - Check coolant level Marine Gear - Check oil level Air Starting Motor (If Equipped) - Check motor oiler level Air Cleaner Indicator - Check Clutch Shift Collar (If Equipped) - Lubricate Raw Water Pump - Check strainer and primeEvery 1900 L (500 gal) of Fuel or 50 Hours*
Zinc Rods - Inspect/Replace Marine Gear Oil and Filter - Change on new or rebuilt marine gears at first 50 hours ONLY, then at Every 2000 Hours thereafter) Air Tank - Drain water/sedimentEvery 4750 L (1250 gal) of Fuel or 125 Hours*
Clutch Shift Collar and Bearing and Shift Lever - 1 Lubricate/Check/AdjustEvery 9500 L (2500 gal) of Fuel or 250 Hours*
Scheduled Oil Sampling (S O S)** - Obtain Engine Oil and Filters** - Replace Fuel System - Drain water & sediment from tank; Replace final filter/Clean primary filter Cooling System - Test for coolant additive concentration; Add liquid coolant additive or replace coolant additive maintenance element (if equipped) Crankcase Breather - Clean Batteries - Clean/Inspect and check electrolyte level Belts, Hoses and Clamps - Inspect/Check Engine Air Cleaners - Clean Valve Lash** (At First Oil Change Only) - Check/Adjust**The oil change interval is based on fuel consumption. Use fuel consumption as the best indicator of oil change interval. The sump capacity also determines oil change interval. Standard sump at 250 Hours, Deep Sump at 500 Hours. Confirm the interval with Scheduled Oil Sampling (S O S) or contact your Caterpillar dealer.Every 38 000 L (10,000 gal) of Fuel or 1000 Hours*
Marine Gear - Replace oil and filter, Clean strainer/breather, Lubricate output shaft seal Governor - Inspect/Lubricate linkage; Check/Adjust fuel ratio control and low idle - Engine Protective Devices - Inspect/CheckEvery 114 000 L (30,000 gal) of Fuel or 3000 Hours*
Engine Valve Lash - Check/Adjust, Inspect valve rotators Cooling System - Clean/Flush/Change coolant and replace thermostat Engine Mounts and Crankshaft Vibration Damper - Inspect/Check PAR Analysis - ObtainEvery 190 000 L (50,000 gal) of Fuel or 5000 Hours*
Fuel Injection Nozzles - Test/Exchange Turbocharger, Jacket Water Pump and Raw Water Pump - Inspect/Rebuild or Exchange Alternator, Air Compressor and Starting Motors - Inspect/Rebuild or Exchange if necessary Rod Bearings1 - Inspect/Replace1Replace if fuel consumption exceeds 45.5 liter (12 U.S. gallon) per hour.OVERHAUL Every 380 000 L (100,000 gal) of Fuel or 10,000 Hours*
Cylinder Head, Connecting Rods, Pistons, Cylinder Liners, Turbocharger, Oil Pump, Spacer Plate, Fuel Ratio Control, Cam Followers, Fuel Transfer Pump and Timing Advance - Inspect/Rebuild or Exchange Piston Rings, Main Bearings, Rod Bearings, Valve Rotators and Crankshaft Seals - Replace Fuel Injection Nozzles - Test Fuel Injection Pump - Test Crankshaft, Camshaft, Cam Bearings, Damper, Governor, Fuel Pump Camshaft and Fuel Rack - Inspect Oil Cooler - Clean/Test Aftercooler Core - Clean/Test Coolant Analysis - Obtain*First Perform Previous Service Hour Items
Walk-Around Inspection - Inspect engine for leaks and loose connections Engine Crankcase - Check oil level Cooling System - Check coolant level Marine Gear - Check oil level Air Starting Motor (If Equipped) - Check motor oiler level Air Cleaner Indicator - Check Clutch Shift Collar (If Equipped) - Lubricate Raw Water Pump - Check strainer and primeEvery 1900 L (500 gal) of Fuel or 50 Hours*
Zinc Rods - Inspect/Replace Marine Gear Oil and Filter - Change on new or rebuilt marine gears at first 50 hours ONLY, then at Every 2000 Hours thereafter) Air Tank - Drain water/sedimentEvery 4750 L (1250 gal) of Fuel or 125 Hours*
Clutch Shift Collar and Bearing and Shift Lever - 1 Lubricate/Check/AdjustEvery 9500 L (2500 gal) of Fuel or 250 Hours*
Scheduled Oil Sampling (S O S)** - Obtain Engine Oil and Filters** - Replace Fuel System - Drain water & sediment from tank; Replace final filter/Clean primary filter Cooling System - Test for coolant additive concentration; Add liquid coolant additive or replace coolant additive maintenance element (if equipped) Crankcase Breather - Clean Batteries - Clean/Inspect and check electrolyte level Belts, Hoses and Clamps - Inspect/Check Engine Air Cleaners - Clean Valve Lash** (At First Oil Change Only) - Check/Adjust**The oil change interval is based on fuel consumption. Use fuel consumption as the best indicator of oil change interval. The sump capacity also determines oil change interval. Standard sump at 250 Hours, Deep Sump at 500 Hours. Confirm the interval with Scheduled Oil Sampling (S O S) or contact your Caterpillar dealer.Every 38 000 L (10,000 gal) of Fuel or 1000 Hours*
Marine Gear - Replace oil and filter, Clean strainer/breather, Lubricate output shaft seal Governor - Inspect/Lubricate linkage; Check/Adjust fuel ratio control and low idle - Engine Protective Devices - Inspect/CheckEvery 114 000 L (30,000 gal) of Fuel or 3000 Hours*
Engine Valve Lash - Check/Adjust, Inspect valve rotators Cooling System - Clean/Flush/Change coolant and replace thermostat Engine Mounts and Crankshaft Vibration Damper - Inspect/Check PAR Analysis - ObtainEvery 190 000 L (50,000 gal) of Fuel or 5000 Hours*
Fuel Injection Nozzles - Test/Exchange Turbocharger, Jacket Water Pump and Raw Water Pump - Inspect/Rebuild or Exchange Alternator, Air Compressor and Starting Motors - Inspect/Rebuild or Exchange if necessary Rod Bearings1 - Inspect/Replace1Replace if fuel consumption exceeds 45.5 liter (12 U.S. gallon) per hour.OVERHAUL Every 380 000 L (100,000 gal) of Fuel or 10,000 Hours*
Cylinder Head, Connecting Rods, Pistons, Cylinder Liners, Turbocharger, Oil Pump, Spacer Plate, Fuel Ratio Control, Cam Followers, Fuel Transfer Pump and Timing Advance - Inspect/Rebuild or Exchange Piston Rings, Main Bearings, Rod Bearings, Valve Rotators and Crankshaft Seals - Replace Fuel Injection Nozzles - Test Fuel Injection Pump - Test Crankshaft, Camshaft, Cam Bearings, Damper, Governor, Fuel Pump Camshaft and Fuel Rack - Inspect Oil Cooler - Clean/Test Aftercooler Core - Clean/Test Coolant Analysis - Obtain*First Perform Previous Service Hour Items