Information injection-pump assembly
ZEXEL
101601-5656
1016015656
HINO
220006343B
220006343b
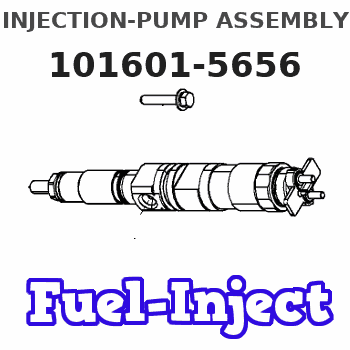
Rating:
Service parts 101601-5656 INJECTION-PUMP ASSEMBLY:
1.
_
7.
COUPLING PLATE
8.
_
9.
_
11.
Nozzle and Holder
23600-2133A
12.
Open Pre:MPa(Kqf/cm2)
19.6{200}
15.
NOZZLE SET
Cross reference number
ZEXEL
101601-5656
1016015656
HINO
220006343B
220006343b
Zexel num
Bosch num
Firm num
Name
Calibration Data:
Adjustment conditions
Test oil
1404 Test oil ISO4113 or {SAEJ967d}
1404 Test oil ISO4113 or {SAEJ967d}
Test oil temperature
degC
40
40
45
Nozzle and nozzle holder
105780-8140
Bosch type code
EF8511/9A
Nozzle
105780-0000
Bosch type code
DN12SD12T
Nozzle holder
105780-2080
Bosch type code
EF8511/9
Opening pressure
MPa
17.2
Opening pressure
kgf/cm2
175
Injection pipe
Outer diameter - inner diameter - length (mm) mm 6-2-600
Outer diameter - inner diameter - length (mm) mm 6-2-600
Overflow valve
131424-8320
Overflow valve opening pressure
kPa
108
88
128
Overflow valve opening pressure
kgf/cm2
1.1
0.9
1.3
Tester oil delivery pressure
kPa
157
157
157
Tester oil delivery pressure
kgf/cm2
1.6
1.6
1.6
Direction of rotation (viewed from drive side)
Right R
Right R
Injection timing adjustment
Direction of rotation (viewed from drive side)
Right R
Right R
Injection order
1-4-2-6-
3-5
Pre-stroke
mm
3.8
3.77
3.83
Beginning of injection position
Drive side NO.1
Drive side NO.1
Difference between angles 1
Cal 1-4 deg. 60 59.75 60.25
Cal 1-4 deg. 60 59.75 60.25
Difference between angles 2
Cyl.1-2 deg. 120 119.75 120.25
Cyl.1-2 deg. 120 119.75 120.25
Difference between angles 3
Cal 1-6 deg. 180 179.75 180.25
Cal 1-6 deg. 180 179.75 180.25
Difference between angles 4
Cal 1-3 deg. 240 239.75 240.25
Cal 1-3 deg. 240 239.75 240.25
Difference between angles 5
Cal 1-5 deg. 300 299.75 300.25
Cal 1-5 deg. 300 299.75 300.25
Injection quantity adjustment
Adjusting point
-
Rack position
12
Pump speed
r/min
850
850
850
Average injection quantity
mm3/st.
76.1
74.5
77.7
Max. variation between cylinders
%
0
-3.5
3.5
Basic
*
Fixing the rack
*
Standard for adjustment of the maximum variation between cylinders
*
Injection quantity adjustment_02
Adjusting point
H
Rack position
9.5+-0.5
Pump speed
r/min
250
250
250
Each cylinder's injection qty
mm3/st.
15
14
16
Fixing the rack
*
Standard for adjustment of the maximum variation between cylinders
*
Injection quantity adjustment_03
Adjusting point
A
Rack position
R1(12)
Pump speed
r/min
850
850
850
Average injection quantity
mm3/st.
76.1
75.1
77.1
Basic
*
Fixing the lever
*
Injection quantity adjustment_04
Adjusting point
B
Rack position
R1+0.45
Pump speed
r/min
1450
1450
1450
Average injection quantity
mm3/st.
86.8
82.8
90.8
Fixing the lever
*
Injection quantity adjustment_05
Adjusting point
C
Rack position
R1-0.25
Pump speed
r/min
580
580
580
Average injection quantity
mm3/st.
62.8
58.8
66.8
Fixing the lever
*
Injection quantity adjustment_06
Adjusting point
D
Rack position
R1+0.45
Pump speed
r/min
1150
1150
1150
Average injection quantity
mm3/st.
85.4
81.4
89.4
Fixing the lever
*
Injection quantity adjustment_07
Adjusting point
I
Rack position
-
Pump speed
r/min
100
100
100
Average injection quantity
mm3/st.
140
140
150
Fixing the lever
*
Rack limit
*
Timer adjustment
Pump speed
r/min
925--
Advance angle
deg.
0
0
0
Load
1/4
Remarks
Start
Start
Timer adjustment_02
Pump speed
r/min
875
Advance angle
deg.
0.3
Load
1/4
Timer adjustment_03
Pump speed
r/min
(920--)
Advance angle
deg.
1
0.7
1.3
Load
4/4
Timer adjustment_04
Pump speed
r/min
1175+50
Advance angle
deg.
1
0.7
1.3
Load
3/4
Timer adjustment_05
Pump speed
r/min
1400+50
Advance angle
deg.
5.5
5.2
5.8
Load
4/4
Remarks
Finish
Finish
Test data Ex:
Governor adjustment
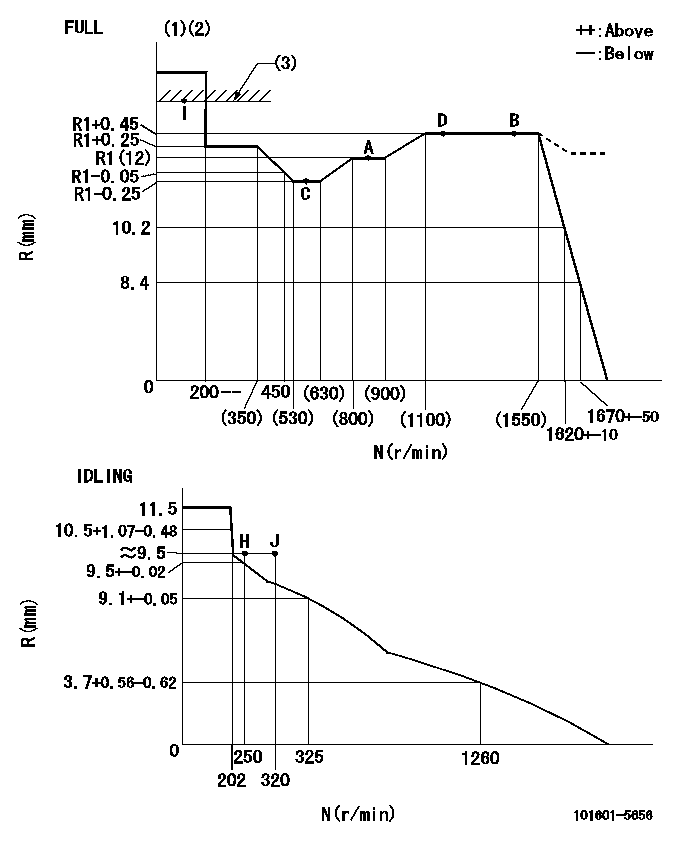
N:Pump speed
R:Rack position (mm)
(1)Torque cam stamping: T1
(2)Tolerance for racks not indicated: +-0.05mm.
(3)RACK LIMIT
----------
T1=H17
----------
----------
T1=H17
----------
Speed control lever angle

F:Full speed
I:Idle
(1)Use the hole at R = aa
(2)Stopper bolt set position 'H'
----------
aa=44mm
----------
a=33deg+-5deg b=(46deg)+-3deg
----------
aa=44mm
----------
a=33deg+-5deg b=(46deg)+-3deg
Stop lever angle
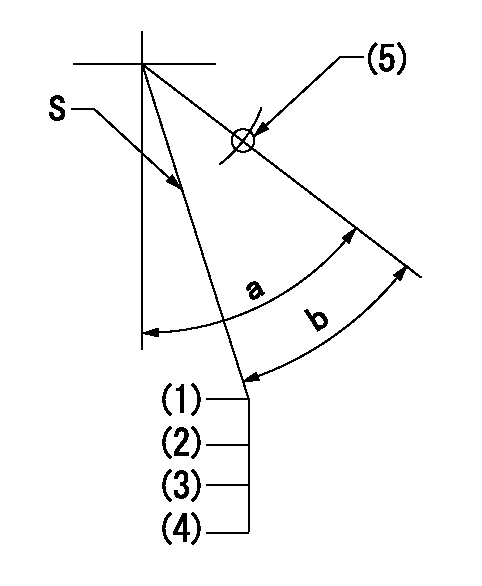
S:Engine stop
(1)With the speed lever in the full position at speed = aa, set the stop screw so that the rack position = bb (non-injection rack position).
(2)Confirm non-injection with the speed lever in the idle position at speed = cc.
(3)With the speed lever in the idle position at speed = dd, operate the stop lever 2 or 3 times and confirm that the rack does not stick. After adjustment apply red paint.
(4)After adjustment, apply red paint.
(5)Use the hole above R = ee
----------
aa=1450r/min bb=6.3-0.5mm cc=250r/min dd=0r/min ee=35mm
----------
a=40deg+-5deg b=(26deg)+-5deg
----------
aa=1450r/min bb=6.3-0.5mm cc=250r/min dd=0r/min ee=35mm
----------
a=40deg+-5deg b=(26deg)+-5deg
Timing setting
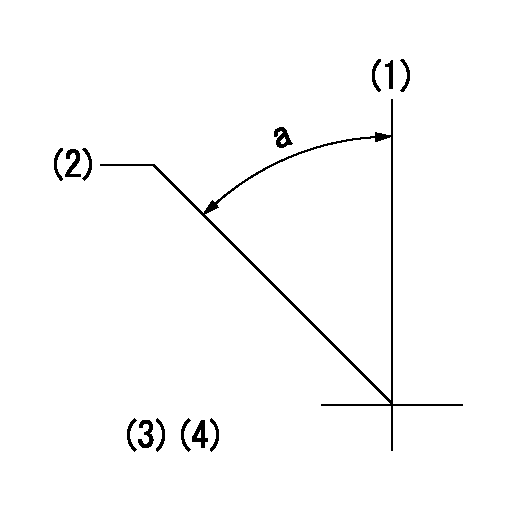
(1)Pump vertical direction
(2)Coupling's key groove position at No 1 cylinder's beginning of injection
(3)-
(4)-
----------
----------
a=(50deg)
----------
----------
a=(50deg)
Information:
4. Start the engine. After starting, travel with caution, at minimum speed.5. To stop the vessel, stop the engine. Remove the bolts engaging the clutch when the engine is stopped. Disassemble and inspect the clutch plates for warping and cracking. Damage can occur by having the clutch plates mechanically engaged. Under severe operating conditions, the marine gear should be disassembled and all bearings inspected closely.Engine Jacket Water Pump Failure
If the engine jacket water pump should fail, fresh water can be supplied to the engine jacket using the emergency water system.
Tee Connector (1), Shut Off Valve (2), Emergency Jacket Water Pump (3), Tee Connector (4) & Shut Off Valve (5).1. Stop the engine. If the water pump bearing has failed, the water pump does NOT need to be removed.2. Open valve (2) between the emergency pump and oil cooler connection. 3. Place the diverter valve handle in the EMERGENCY position.4. Start and prime the emergency jacket water pump (3). Allow air to escape from the emergency cooling system lines.5. Check coolant level in the expansion tank. Add coolant if required.6. Start the engine. Always start the engine according to the required Engine Starting procedure described in this manual. Engage marine gear and operate vessel at normal speed. If the engine jacket water coolant is lost (i.e. water line rupture or leak) and an insufficient supply of fresh water is available to replenish the system, raw water may be pumped through the engine.a. Stop the engine and make the necessary water pump and lines connections to pump raw water into the jacket water system and back to the source.b. Remove the temperature regulating thermostats from the regulator housing and install housing cover.c. Start and prime the emergency pump.d. Start the engine and allow to idle at low idle. Always start the engine according to the required Engine Starting procedure described in this manual. Engage the marine gear forward clutch. Operate the engine at the lowest speed for the existing weather conditions.e. Maintain engine temperatures as low as possible to minimize deposits in the engine and corrosion of components. Have the engine jacket water system completely disassembled, cleaned and inspected after reaching port. Replace all parts which are corroded or damaged.Engine Raw Water Pump Failure
The
If the engine jacket water pump should fail, fresh water can be supplied to the engine jacket using the emergency water system.
Tee Connector (1), Shut Off Valve (2), Emergency Jacket Water Pump (3), Tee Connector (4) & Shut Off Valve (5).1. Stop the engine. If the water pump bearing has failed, the water pump does NOT need to be removed.2. Open valve (2) between the emergency pump and oil cooler connection. 3. Place the diverter valve handle in the EMERGENCY position.4. Start and prime the emergency jacket water pump (3). Allow air to escape from the emergency cooling system lines.5. Check coolant level in the expansion tank. Add coolant if required.6. Start the engine. Always start the engine according to the required Engine Starting procedure described in this manual. Engage marine gear and operate vessel at normal speed. If the engine jacket water coolant is lost (i.e. water line rupture or leak) and an insufficient supply of fresh water is available to replenish the system, raw water may be pumped through the engine.a. Stop the engine and make the necessary water pump and lines connections to pump raw water into the jacket water system and back to the source.b. Remove the temperature regulating thermostats from the regulator housing and install housing cover.c. Start and prime the emergency pump.d. Start the engine and allow to idle at low idle. Always start the engine according to the required Engine Starting procedure described in this manual. Engage the marine gear forward clutch. Operate the engine at the lowest speed for the existing weather conditions.e. Maintain engine temperatures as low as possible to minimize deposits in the engine and corrosion of components. Have the engine jacket water system completely disassembled, cleaned and inspected after reaching port. Replace all parts which are corroded or damaged.Engine Raw Water Pump Failure
The