Information injection-pump assembly
BOSCH
9 400 614 622
9400614622
ZEXEL
101601-5632
1016015632
HINO
220006323A
220006323a
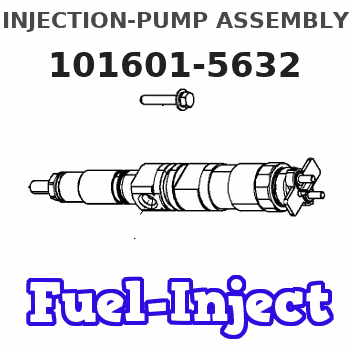
Rating:
Service parts 101601-5632 INJECTION-PUMP ASSEMBLY:
1.
_
7.
COUPLING PLATE
8.
_
9.
_
11.
Nozzle and Holder
23600-2133A
12.
Open Pre:MPa(Kqf/cm2)
19.6{200}
15.
NOZZLE SET
Cross reference number
BOSCH
9 400 614 622
9400614622
ZEXEL
101601-5632
1016015632
HINO
220006323A
220006323a
Zexel num
Bosch num
Firm num
Name
101601-5632
9 400 614 622
220006323A HINO
INJECTION-PUMP ASSEMBLY
H07D-A * K 14BF INJECTION PUMP ASSY PE6AD PE
H07D-A * K 14BF INJECTION PUMP ASSY PE6AD PE
Calibration Data:
Adjustment conditions
Test oil
1404 Test oil ISO4113 or {SAEJ967d}
1404 Test oil ISO4113 or {SAEJ967d}
Test oil temperature
degC
40
40
45
Nozzle and nozzle holder
105780-8210
Nozzle
105780-0070
Bosch type code
DN12SD12T-1
Nozzle holder
105780-2080
Bosch type code
EF8511/9
Opening pressure
MPa
17.2
Opening pressure
kgf/cm2
175
Injection pipe
Outer diameter - inner diameter - length (mm) mm 6-2-600
Outer diameter - inner diameter - length (mm) mm 6-2-600
Overflow valve
134424-0920
Overflow valve opening pressure
kPa
162
147
177
Overflow valve opening pressure
kgf/cm2
1.65
1.5
1.8
Tester oil delivery pressure
kPa
157
157
157
Tester oil delivery pressure
kgf/cm2
1.6
1.6
1.6
Direction of rotation (viewed from drive side)
Right R
Right R
Injection timing adjustment
Direction of rotation (viewed from drive side)
Right R
Right R
Injection order
1-4-2-6-
3-5
Pre-stroke
mm
3.8
3.77
3.83
Beginning of injection position
Drive side NO.1
Drive side NO.1
Difference between angles 1
Cal 1-4 deg. 60 59.75 60.25
Cal 1-4 deg. 60 59.75 60.25
Difference between angles 2
Cyl.1-2 deg. 120 119.75 120.25
Cyl.1-2 deg. 120 119.75 120.25
Difference between angles 3
Cal 1-6 deg. 180 179.75 180.25
Cal 1-6 deg. 180 179.75 180.25
Difference between angles 4
Cal 1-3 deg. 240 239.75 240.25
Cal 1-3 deg. 240 239.75 240.25
Difference between angles 5
Cal 1-5 deg. 300 299.75 300.25
Cal 1-5 deg. 300 299.75 300.25
Injection quantity adjustment
Adjusting point
-
Rack position
11.5
Pump speed
r/min
850
850
850
Average injection quantity
mm3/st.
77.6
76
79.2
Max. variation between cylinders
%
0
-3.5
3.5
Basic
*
Fixing the rack
*
Standard for adjustment of the maximum variation between cylinders
*
Injection quantity adjustment_02
Adjusting point
H
Rack position
9+-0.5
Pump speed
r/min
250
250
250
Each cylinder's injection qty
mm3/st.
16.9
15.9
17.9
Fixing the rack
*
Standard for adjustment of the maximum variation between cylinders
*
Injection quantity adjustment_03
Adjusting point
A
Rack position
R1(11.5)
Pump speed
r/min
850
850
850
Average injection quantity
mm3/st.
77.6
76.6
78.6
Basic
*
Fixing the lever
*
Injection quantity adjustment_04
Adjusting point
B
Rack position
R1+0.5
Pump speed
r/min
1450
1450
1450
Average injection quantity
mm3/st.
88.9
84.9
92.9
Fixing the lever
*
Injection quantity adjustment_05
Adjusting point
C
Rack position
R1-0.3
Pump speed
r/min
600
600
600
Average injection quantity
mm3/st.
64.2
60.2
68.2
Fixing the lever
*
Injection quantity adjustment_06
Adjusting point
D
Rack position
R1+0.5
Pump speed
r/min
1150
1150
1150
Average injection quantity
mm3/st.
87.4
83.4
91.4
Fixing the lever
*
Injection quantity adjustment_07
Adjusting point
I
Rack position
-
Pump speed
r/min
100
100
100
Average injection quantity
mm3/st.
140
140
150
Fixing the lever
*
Rack limit
*
Timer adjustment
Pump speed
r/min
925--
Advance angle
deg.
0
0
0
Load
1/4
Remarks
Start
Start
Timer adjustment_02
Pump speed
r/min
875
Advance angle
deg.
0.3
Load
1/4
Timer adjustment_03
Pump speed
r/min
(920--)
Advance angle
deg.
1
0.7
1.3
Load
4/4
Timer adjustment_04
Pump speed
r/min
1175+50
Advance angle
deg.
1
0.7
1.3
Load
3/4
Timer adjustment_05
Pump speed
r/min
1400+50
Advance angle
deg.
5.5
5.2
5.8
Load
4/4
Remarks
Finish
Finish
Test data Ex:
Governor adjustment
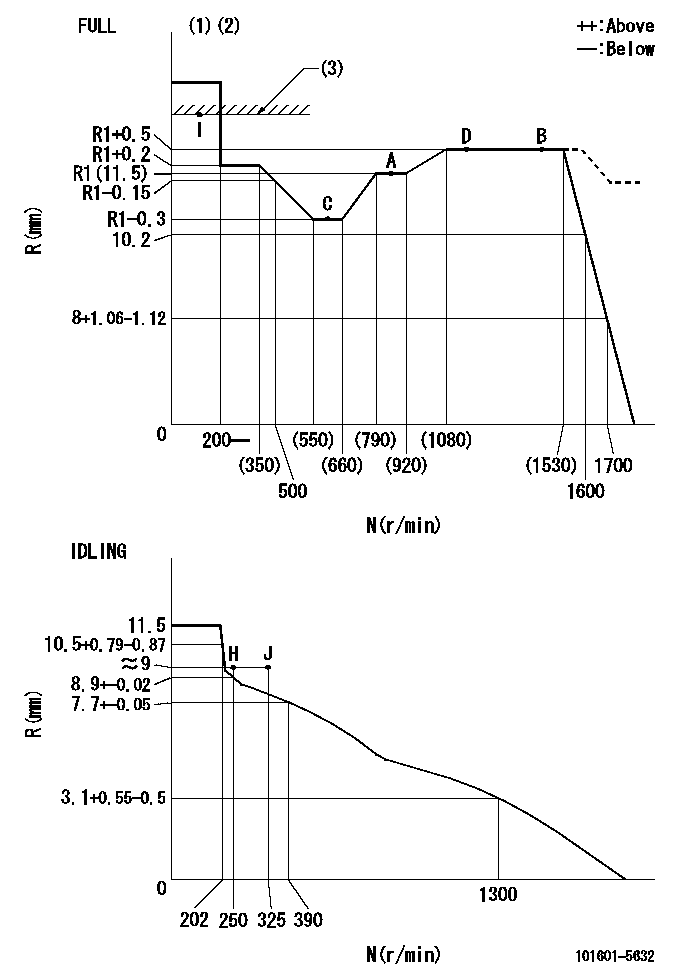
N:Pump speed
R:Rack position (mm)
(1)Torque cam stamping: T1
(2)Tolerance for racks not indicated: +-0.05mm.
(3)RACK LIMIT
----------
T1=F03
----------
----------
T1=F03
----------
Speed control lever angle

F:Full speed
I:Idle
(1)Use the hole at R = aa
(2)Stopper bolt set position 'H'
----------
aa=46mm
----------
a=30deg+-5deg b=(40deg)+-3deg
----------
aa=46mm
----------
a=30deg+-5deg b=(40deg)+-3deg
Stop lever angle
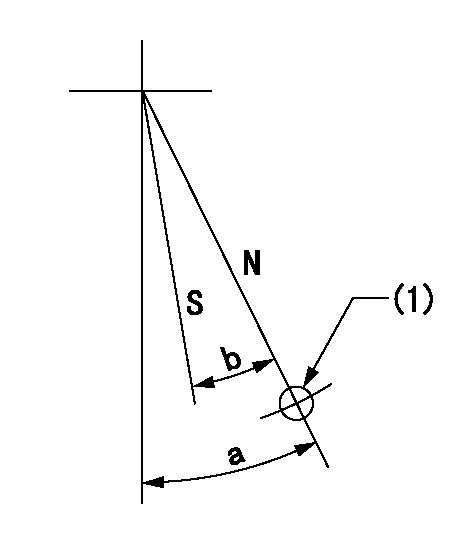
N:Pump normal
S:Stop the pump.
(1)Use the hole at R = aa
----------
aa=35mm
----------
a=40deg+-5deg b=40deg+-5deg
----------
aa=35mm
----------
a=40deg+-5deg b=40deg+-5deg
Timing setting
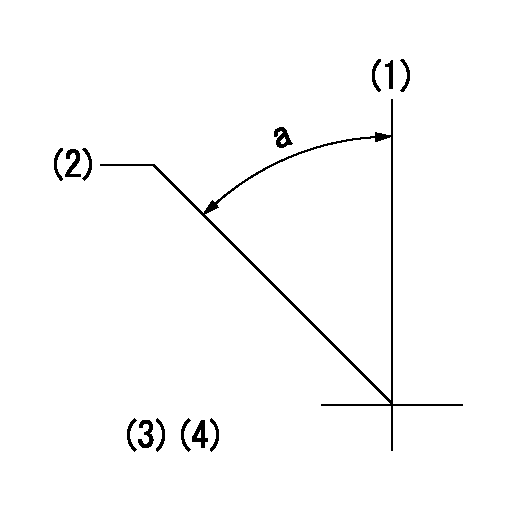
(1)Pump vertical direction
(2)Coupling's key groove position at No 1 cylinder's beginning of injection
(3)-
(4)-
----------
----------
a=(50deg)
----------
----------
a=(50deg)
Information:
Introduction
The problem that is identified below does not have a permanent solution. Until a permanent solution is known, use the solution that is listed below.Problem
A significant amount of HEUI pumps and injectors have been returned, but no cause of failure can be determined.Solution
Diagnostic procedures have been updated and have been incorporated into the following publications:
Special Instruction, REHS3819, "Procedure for Troubleshooting and Cleaning the Oil Rail System for the Hydraulic Electronic Unit Injector (HEUI)"
Troubleshooting, "Injection Actuation Pressure - Test"Note: These publications have been translated into Mandarin and Spanish.In addition, a new troubleshooting checklist is included with all service repair for HUEI pumps and HEUI injectors. The checklist is a summary of the diagnostic procedure steps to be confirmed before a suspect component is replaced. The checklist must be completed and returned with the suspect components in order to aid engineering to determine the cause of failure.Following the instructions step-by-step is critical in order to diagnose the failed component correctly. Do not skip steps in the procedures. Skipping steps in the procedure will lead to incorrect diagnosis of the problem.
The problem that is identified below does not have a permanent solution. Until a permanent solution is known, use the solution that is listed below.Problem
A significant amount of HEUI pumps and injectors have been returned, but no cause of failure can be determined.Solution
Diagnostic procedures have been updated and have been incorporated into the following publications:
Special Instruction, REHS3819, "Procedure for Troubleshooting and Cleaning the Oil Rail System for the Hydraulic Electronic Unit Injector (HEUI)"
Troubleshooting, "Injection Actuation Pressure - Test"Note: These publications have been translated into Mandarin and Spanish.In addition, a new troubleshooting checklist is included with all service repair for HUEI pumps and HEUI injectors. The checklist is a summary of the diagnostic procedure steps to be confirmed before a suspect component is replaced. The checklist must be completed and returned with the suspect components in order to aid engineering to determine the cause of failure.Following the instructions step-by-step is critical in order to diagnose the failed component correctly. Do not skip steps in the procedures. Skipping steps in the procedure will lead to incorrect diagnosis of the problem.
Have questions with 101601-5632?
Group cross 101601-5632 ZEXEL
Hino
101601-5632
9 400 614 622
220006323A
INJECTION-PUMP ASSEMBLY
H07D-A
H07D-A