Information injection-pump assembly
ZEXEL
101601-5202
1016015202
HINO
220005240A
220005240a

Rating:
Service parts 101601-5202 INJECTION-PUMP ASSEMBLY:
1.
_
6.
COUPLING PLATE
7.
COUPLING PLATE
8.
_
9.
_
11.
Nozzle and Holder
12.
Open Pre:MPa(Kqf/cm2)
21.6(220)
15.
NOZZLE SET
Cross reference number
ZEXEL
101601-5202
1016015202
HINO
220005240A
220005240a
Zexel num
Bosch num
Firm num
Name
101601-5202
220005240A HINO
INJECTION-PUMP ASSEMBLY
W06E * K
W06E * K
Calibration Data:
Adjustment conditions
Test oil
1404 Test oil ISO4113 or {SAEJ967d}
1404 Test oil ISO4113 or {SAEJ967d}
Test oil temperature
degC
40
40
45
Nozzle and nozzle holder
105780-8140
Bosch type code
EF8511/9A
Nozzle
105780-0000
Bosch type code
DN12SD12T
Nozzle holder
105780-2080
Bosch type code
EF8511/9
Opening pressure
MPa
17.2
Opening pressure
kgf/cm2
175
Injection pipe
Outer diameter - inner diameter - length (mm) mm 6-2-600
Outer diameter - inner diameter - length (mm) mm 6-2-600
Overflow valve
131424-5720
Overflow valve opening pressure
kPa
255
221
289
Overflow valve opening pressure
kgf/cm2
2.6
2.25
2.95
Tester oil delivery pressure
kPa
157
157
157
Tester oil delivery pressure
kgf/cm2
1.6
1.6
1.6
Direction of rotation (viewed from drive side)
Right R
Right R
Injection timing adjustment
Direction of rotation (viewed from drive side)
Right R
Right R
Injection order
1-4-2-6-
3-5
Pre-stroke
mm
3.1
3.07
3.13
Beginning of injection position
Drive side NO.1
Drive side NO.1
Difference between angles 1
Cal 1-4 deg. 60 59.75 60.25
Cal 1-4 deg. 60 59.75 60.25
Difference between angles 2
Cyl.1-2 deg. 120 119.75 120.25
Cyl.1-2 deg. 120 119.75 120.25
Difference between angles 3
Cal 1-6 deg. 180 179.75 180.25
Cal 1-6 deg. 180 179.75 180.25
Difference between angles 4
Cal 1-3 deg. 240 239.75 240.25
Cal 1-3 deg. 240 239.75 240.25
Difference between angles 5
Cal 1-5 deg. 300 299.75 300.25
Cal 1-5 deg. 300 299.75 300.25
Injection quantity adjustment
Adjusting point
-
Rack position
9.2
Pump speed
r/min
900
900
900
Average injection quantity
mm3/st.
52.4
50.4
54.4
Max. variation between cylinders
%
0
-3.5
3.5
Basic
*
Fixing the rack
*
Standard for adjustment of the maximum variation between cylinders
*
Injection quantity adjustment_02
Adjusting point
H
Rack position
8+-0.5
Pump speed
r/min
250
250
250
Average injection quantity
mm3/st.
6.8
5.3
8.3
Max. variation between cylinders
%
0
-10
10
Fixing the rack
*
Standard for adjustment of the maximum variation between cylinders
*
Injection quantity adjustment_03
Adjusting point
A
Rack position
R1(9.2)
Pump speed
r/min
900
900
900
Average injection quantity
mm3/st.
52.4
51.4
53.4
Basic
*
Fixing the lever
*
Injection quantity adjustment_04
Adjusting point
B
Rack position
R1-0.35
Pump speed
r/min
1600
1600
1600
Average injection quantity
mm3/st.
50.2
46.2
54.2
Fixing the lever
*
Injection quantity adjustment_05
Adjusting point
C
Rack position
R1-0.35
Pump speed
r/min
600
600
600
Average injection quantity
mm3/st.
36.5
32.5
40.5
Fixing the lever
*
Injection quantity adjustment_06
Adjusting point
D
Rack position
R1-0.1
Pump speed
r/min
1200
1200
1200
Average injection quantity
mm3/st.
53.1
49.1
57.1
Fixing the lever
*
Injection quantity adjustment_07
Adjusting point
E
Rack position
R1+0.2
Pump speed
r/min
400
400
400
Average injection quantity
mm3/st.
29.2
25.2
33.2
Fixing the lever
*
Injection quantity adjustment_08
Adjusting point
I
Rack position
-
Pump speed
r/min
100
100
100
Average injection quantity
mm3/st.
99
99
109
Fixing the lever
*
Rack limit
*
Timer adjustment
Pump speed
r/min
1050--
Advance angle
deg.
0
0
0
Remarks
Start
Start
Timer adjustment_02
Pump speed
r/min
1000
Advance angle
deg.
0.3
Timer adjustment_03
Pump speed
r/min
1500
Advance angle
deg.
4.5
4.2
4.8
Remarks
Finish
Finish
Test data Ex:
Governor adjustment
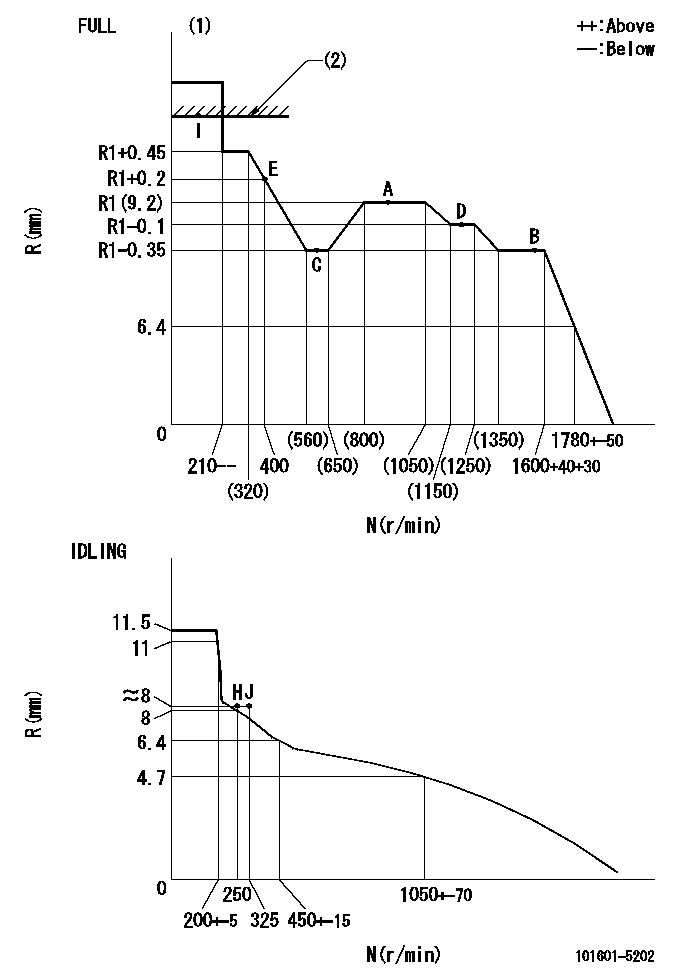
N:Pump speed
R:Rack position (mm)
(1)Torque cam stamping: T1
(2)RACK LIMIT
----------
T1=C09
----------
----------
T1=C09
----------
Speed control lever angle

F:Full speed
I:Idle
(1)Stopper bolt set position 'H'
----------
----------
a=34deg+-5deg b=35deg+-3deg
----------
----------
a=34deg+-5deg b=35deg+-3deg
Stop lever angle

N:Engine normal (pump normal)
S:Engine stop
(1)Set the stopper screw.
(2)(Apply red paint after setting.)
----------
----------
a=20deg+-5deg b=(28deg)+-5deg
----------
----------
a=20deg+-5deg b=(28deg)+-5deg
0000001501 LEVER
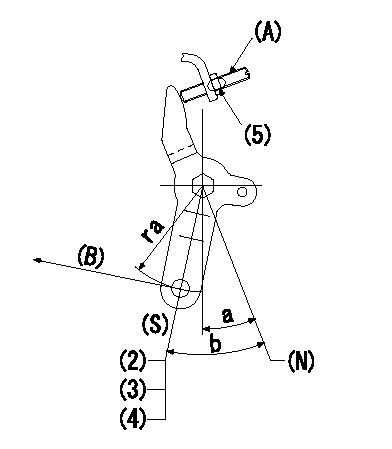
(N) Engine normal (pump normal)
(S) Engine stop
(A) stopper screw
(B) Stop direction (perpendicular)
Stop lever adjusting procedure
(1)After completing adjustment, confirm that the engine's normal lever angle (pump's normal lever) is within the specifications in the figure above.
(2)With the speed lever at Full and the pump speed at Na (specified speed), temporarily set the stopper screw (A) at the rack position Ra.
(3)Turn the stopper screw (A) Rb in the stop direction (Nb turns) and set it. Measure the rack position. (Rack position = approx. Rc)
(4)After setting, confirm non-injection with the speed lever at idle and pump speed at Nc.
(5)After adjustment, apply red paint.
----------
Na=1600r/min Ra=5.1mm Rb=1.5mm Nb=1.5 Rc=3.1mm Nc=250r/min
----------
ra=37mm a=20deg+-5deg b=(28deg)+-5deg
----------
Na=1600r/min Ra=5.1mm Rb=1.5mm Nb=1.5 Rc=3.1mm Nc=250r/min
----------
ra=37mm a=20deg+-5deg b=(28deg)+-5deg
Timing setting
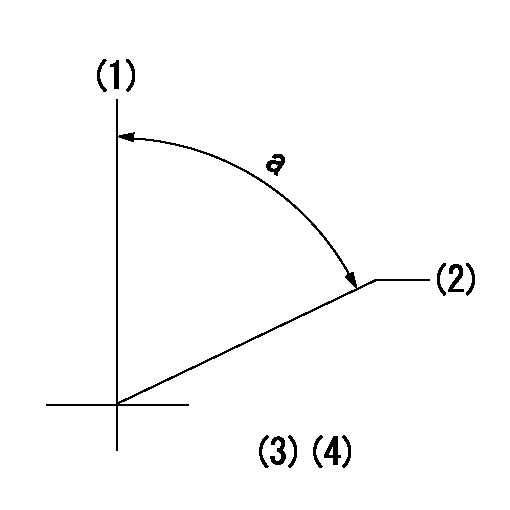
(1)Pump vertical direction
(2)Position of gear's standard threaded hole at No 1 cylinder's beginning of injection
(3)-
(4)-
----------
----------
a=(70deg)
----------
----------
a=(70deg)
Information:
Start By:
Keep all parts clean from contaminants. Contaminants put into the system may cause rapid wear and shortened component life.
a. remove crankshaft rear seal and wear sleeve1. Loosen the bolts that hold the oil pan and oil plan plate to the cylinder block. Remove the bolts that hold the oil pan plate to the flywheel housing.2. Install spacers between the oil pan plate and the cylinder block to hold the oil pan plate away from the flywheel housing. 3. Remove turbocharger oil drain tube (1).4. Remove the bolt to clip (3).5. Install tool (A) and fasten a hoist as shown. Remove bolts (4) and remove flywheel housing (2). The weight of the flywheel housing is 39 kg (85 lb.). The following steps are for the installation of the flywheel housing.6. Clean the old gasket from the surfaces of the cylinder block and flywheel housing that make contact with each other. Install a new gasket on the cylinder block.7. Install two 1/2" - 13 NC guide bolts in the cylinder block. Install tool (A) on the flywheel housing. Fasten a hoist and put the flywheel housing in position on the guide bolts. Install all but two bolts in the flywheel housing. Remove tool (A) and the guide bolts. Install the other two bolts. Tighten the flywheel housing bolts in the sequence as shown. 8. Cut the bottom of the gasket even with the flywheel housing and cylinder block. Put 5H2471 Gasket Cement on the bottom of the gasket where the gasket makes contact with the gasket for the oil pan plate. Remove shims from each side of the engine. Tighten all of the oil pan bolts. Install the bolts that hold the oil pan plate to the flywheel housing.9. Install the bolt to clip (3). Install turbocharger oil drain tube (1).End By:a. install crankshaft rear seal and wear sleeve
Keep all parts clean from contaminants. Contaminants put into the system may cause rapid wear and shortened component life.
a. remove crankshaft rear seal and wear sleeve1. Loosen the bolts that hold the oil pan and oil plan plate to the cylinder block. Remove the bolts that hold the oil pan plate to the flywheel housing.2. Install spacers between the oil pan plate and the cylinder block to hold the oil pan plate away from the flywheel housing. 3. Remove turbocharger oil drain tube (1).4. Remove the bolt to clip (3).5. Install tool (A) and fasten a hoist as shown. Remove bolts (4) and remove flywheel housing (2). The weight of the flywheel housing is 39 kg (85 lb.). The following steps are for the installation of the flywheel housing.6. Clean the old gasket from the surfaces of the cylinder block and flywheel housing that make contact with each other. Install a new gasket on the cylinder block.7. Install two 1/2" - 13 NC guide bolts in the cylinder block. Install tool (A) on the flywheel housing. Fasten a hoist and put the flywheel housing in position on the guide bolts. Install all but two bolts in the flywheel housing. Remove tool (A) and the guide bolts. Install the other two bolts. Tighten the flywheel housing bolts in the sequence as shown. 8. Cut the bottom of the gasket even with the flywheel housing and cylinder block. Put 5H2471 Gasket Cement on the bottom of the gasket where the gasket makes contact with the gasket for the oil pan plate. Remove shims from each side of the engine. Tighten all of the oil pan bolts. Install the bolts that hold the oil pan plate to the flywheel housing.9. Install the bolt to clip (3). Install turbocharger oil drain tube (1).End By:a. install crankshaft rear seal and wear sleeve
Have questions with 101601-5202?
Group cross 101601-5202 ZEXEL
Hino
Hino
101601-5202
220005240A
INJECTION-PUMP ASSEMBLY
W06E
W06E