Information injection-pump assembly
BOSCH
9 400 614 602
9400614602
ZEXEL
101601-5174
1016015174
HINO
220005191A
220005191a
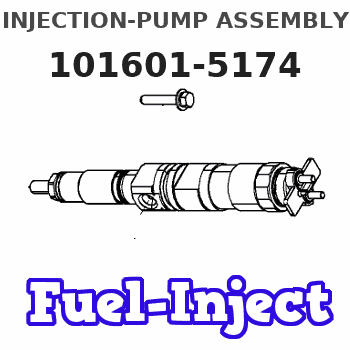
Rating:
Service parts 101601-5174 INJECTION-PUMP ASSEMBLY:
1.
_
7.
COUPLING PLATE
8.
_
9.
_
11.
Nozzle and Holder
12.
Open Pre:MPa(Kqf/cm2)
14.2(145)/19.6(200)
14.
NOZZLE
Cross reference number
BOSCH
9 400 614 602
9400614602
ZEXEL
101601-5174
1016015174
HINO
220005191A
220005191a
Zexel num
Bosch num
Firm num
Name
9 400 614 602
220005191A HINO
INJECTION-PUMP ASSEMBLY
H07C * K 14BE INJECTION PUMP ASSY PE6A PE
H07C * K 14BE INJECTION PUMP ASSY PE6A PE
Calibration Data:
Adjustment conditions
Test oil
1404 Test oil ISO4113 or {SAEJ967d}
1404 Test oil ISO4113 or {SAEJ967d}
Test oil temperature
degC
40
40
45
Nozzle and nozzle holder
105780-8140
Bosch type code
EF8511/9A
Nozzle
105780-0000
Bosch type code
DN12SD12T
Nozzle holder
105780-2080
Bosch type code
EF8511/9
Opening pressure
MPa
17.2
Opening pressure
kgf/cm2
175
Injection pipe
Outer diameter - inner diameter - length (mm) mm 6-2-600
Outer diameter - inner diameter - length (mm) mm 6-2-600
Overflow valve
134424-0920
Overflow valve opening pressure
kPa
162
147
177
Overflow valve opening pressure
kgf/cm2
1.65
1.5
1.8
Tester oil delivery pressure
kPa
157
157
157
Tester oil delivery pressure
kgf/cm2
1.6
1.6
1.6
Direction of rotation (viewed from drive side)
Right R
Right R
Injection timing adjustment
Direction of rotation (viewed from drive side)
Right R
Right R
Injection order
1-4-2-6-
3-5
Pre-stroke
mm
3.1
3.07
3.13
Beginning of injection position
Drive side NO.1
Drive side NO.1
Difference between angles 1
Cal 1-4 deg. 60 59.75 60.25
Cal 1-4 deg. 60 59.75 60.25
Difference between angles 2
Cyl.1-2 deg. 120 119.75 120.25
Cyl.1-2 deg. 120 119.75 120.25
Difference between angles 3
Cal 1-6 deg. 180 179.75 180.25
Cal 1-6 deg. 180 179.75 180.25
Difference between angles 4
Cal 1-3 deg. 240 239.75 240.25
Cal 1-3 deg. 240 239.75 240.25
Difference between angles 5
Cal 1-5 deg. 300 299.75 300.25
Cal 1-5 deg. 300 299.75 300.25
Injection quantity adjustment
Adjusting point
-
Rack position
9.4
Pump speed
r/min
900
900
900
Average injection quantity
mm3/st.
70
69
71
Max. variation between cylinders
%
0
-3.5
3.5
Basic
*
Fixing the rack
*
Standard for adjustment of the maximum variation between cylinders
*
Injection quantity adjustment_02
Adjusting point
H
Rack position
7+-0.1
Pump speed
r/min
275
275
275
Average injection quantity
mm3/st.
8
7
9
Max. variation between cylinders
%
0
-10
10
Fixing the rack
*
Standard for adjustment of the maximum variation between cylinders
*
Remarks
Adjust only variation between cylinders; adjust governor according to governor specifications.
Adjust only variation between cylinders; adjust governor according to governor specifications.
Injection quantity adjustment_03
Adjusting point
A
Rack position
R1(9.4)
Pump speed
r/min
900
900
900
Average injection quantity
mm3/st.
70
69
71
Basic
*
Fixing the lever
*
Injection quantity adjustment_04
Adjusting point
I
Rack position
-
Pump speed
r/min
100
100
100
Average injection quantity
mm3/st.
140
140
150
Fixing the lever
*
Rack limit
*
Timer adjustment
Pump speed
r/min
1250--
Advance angle
deg.
0
0
0
Load
3/4
Remarks
Start
Start
Timer adjustment_02
Pump speed
r/min
1200
Advance angle
deg.
0.3
Load
3/4
Timer adjustment_03
Pump speed
r/min
1450
Advance angle
deg.
4
3.5
4.5
Load
4/4
Remarks
Finish
Finish
Test data Ex:
Governor adjustment
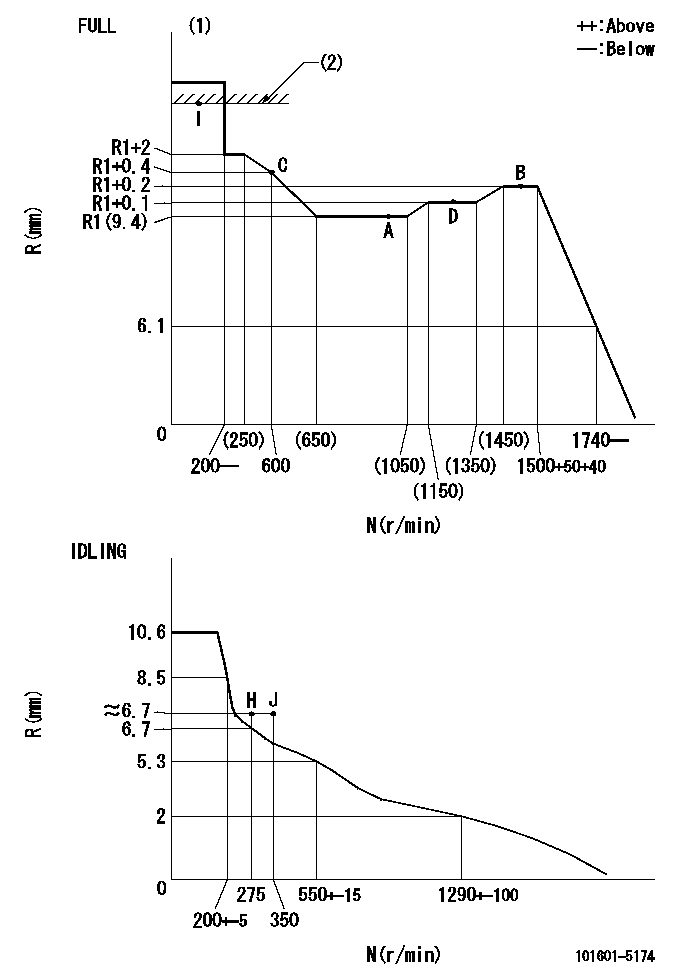
N:Pump speed
R:Rack position (mm)
(1)Torque cam stamping: T1
(2)RACK LIMIT
----------
T1=B94
----------
----------
T1=B94
----------
Speed control lever angle
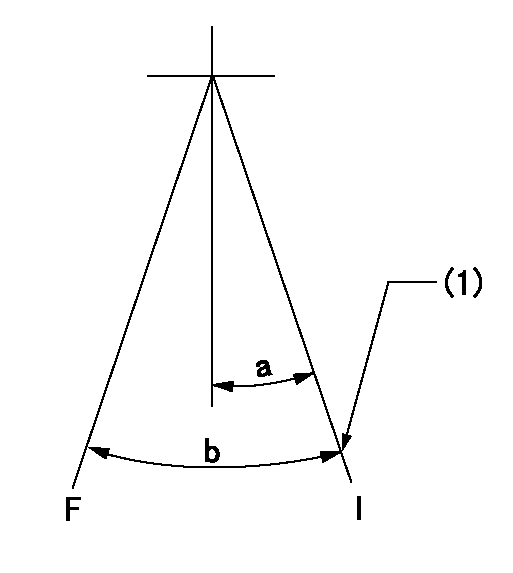
F:Full speed
I:Idle
(1)Stopper bolt set position 'H'
----------
----------
a=33deg+-5deg b=(45deg)+-3deg
----------
----------
a=33deg+-5deg b=(45deg)+-3deg
Stop lever angle
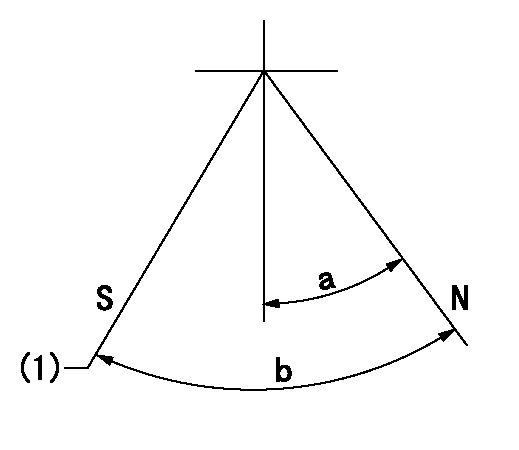
N:Engine normal (pump normal)
S:Engine stop
(1)Set the stopper screw. (After setting, apply red paint.)
----------
----------
a=0deg+-5deg b=(31deg)+-5deg
----------
----------
a=0deg+-5deg b=(31deg)+-5deg
Timing setting
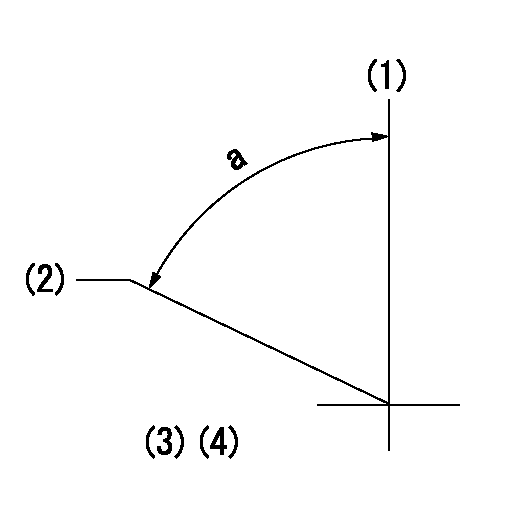
(1)Pump vertical direction
(2)Coupling's key groove position at No 1 cylinder's beginning of injection
(3)-
(4)-
----------
----------
a=(60deg)
----------
----------
a=(60deg)
Information:
Start By:a. remove radiator
Keep all parts clean from contaminants. Contaminants put into the system may cause rapid wear and shortened component life.
1. Loosen bolt (4), bolt (5), and bolt (6). Remove belts (3).2. Remove bolts (2) and fan (1). 3. Remove bolt (7) and washer (8). Put enough spacers (10) on bolt (7) to get approximately 3.18 mm (.125 in) of clearance between washer (8) and vibration damper and pulley assembly (9). Install bolt (7), washer (8), and spacers (10).
If spacers (10) are not used, damage to the bolt and/or crankshaft can result when the vibration damper and pulley are removed from the crankshaft.
4. Install tool (A) as shown, and loosen vibration damper and pulley assembly (9).5. Remove tool (A), bolt (7), washer (8), spacers (10), and vibration damper and pulley assembly (9). 6. If necessary, remove bolts (11) and vibration damper (12). The following steps are to install the crankshaft vibration damper and pulley. Inspect the vibration damper housing for leakage or dents (damage housing). If either condition exists, a replacement of the vibration damper must be made.7. Install vibration damper (12) on pulley (13). Install bolts (11).8. Install vibration damper and pulley assembly (9) and install bolt (7), spacers (10) and washer (8).
The flat side of washer (8) must be installed toward vibration damper and pulley assembly (9).
9. Tighten bolt (7) to a torque of 284 to 340 N m (210 to 250 lb ft). Hit bolt (7) with a hammer and retighten to a torque of 284 to 340 N m (210 to 250 lb ft).10. Position belts (3). Tighten bolts (4), (5), and (6). Use a belt tension gauge and make an adjustment of the belts. Measure the belt farthest from the engine. Tighten new belts until the gauge indication is 534 22 N (120 5 lb ft). Operate the engine at high idle for a minimum of 30 minutes after installing radiator and guards. Make another adjustment of the belt tension. The correct gauge indication for a used belt is 400 44 N (90 10 lb.). Tighten bolt (4), bolt (5), and bolt (6).11. Install fan (1) and bolt (2).End By:a. install radiator
Keep all parts clean from contaminants. Contaminants put into the system may cause rapid wear and shortened component life.
1. Loosen bolt (4), bolt (5), and bolt (6). Remove belts (3).2. Remove bolts (2) and fan (1). 3. Remove bolt (7) and washer (8). Put enough spacers (10) on bolt (7) to get approximately 3.18 mm (.125 in) of clearance between washer (8) and vibration damper and pulley assembly (9). Install bolt (7), washer (8), and spacers (10).
If spacers (10) are not used, damage to the bolt and/or crankshaft can result when the vibration damper and pulley are removed from the crankshaft.
4. Install tool (A) as shown, and loosen vibration damper and pulley assembly (9).5. Remove tool (A), bolt (7), washer (8), spacers (10), and vibration damper and pulley assembly (9). 6. If necessary, remove bolts (11) and vibration damper (12). The following steps are to install the crankshaft vibration damper and pulley. Inspect the vibration damper housing for leakage or dents (damage housing). If either condition exists, a replacement of the vibration damper must be made.7. Install vibration damper (12) on pulley (13). Install bolts (11).8. Install vibration damper and pulley assembly (9) and install bolt (7), spacers (10) and washer (8).
The flat side of washer (8) must be installed toward vibration damper and pulley assembly (9).
9. Tighten bolt (7) to a torque of 284 to 340 N m (210 to 250 lb ft). Hit bolt (7) with a hammer and retighten to a torque of 284 to 340 N m (210 to 250 lb ft).10. Position belts (3). Tighten bolts (4), (5), and (6). Use a belt tension gauge and make an adjustment of the belts. Measure the belt farthest from the engine. Tighten new belts until the gauge indication is 534 22 N (120 5 lb ft). Operate the engine at high idle for a minimum of 30 minutes after installing radiator and guards. Make another adjustment of the belt tension. The correct gauge indication for a used belt is 400 44 N (90 10 lb.). Tighten bolt (4), bolt (5), and bolt (6).11. Install fan (1) and bolt (2).End By:a. install radiator